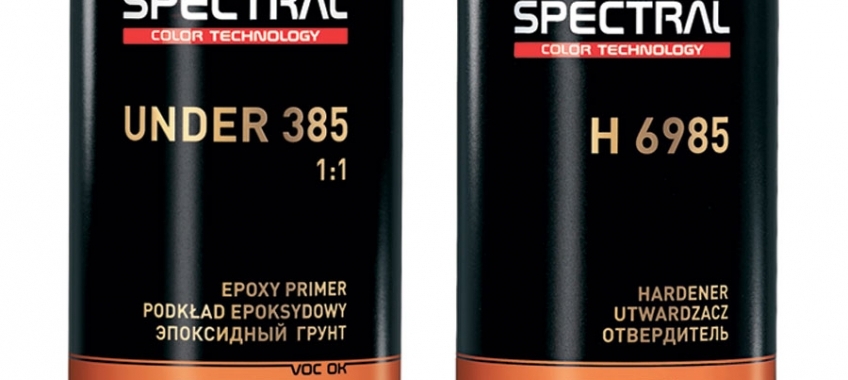
Seria krótkich artykułów pod zbiorczym tytułem „Akademia Spectral – wady lakiernicze” opisuje poszczególne etapy procesu lakierowania i potencjalne błędy, jakie mogą wystąpić w trakcie ich realizacji. W poprzednim numerze opisaliśmy proces zabezpieczenia fabrycznego nowego samochodu. Tym razem zajmiemy się zabezpieczeniem antykorozyjnym w czasie typowej naprawy lakierniczej.
Zasadniczo, patrząc na podejście niektórych serwisów lakierniczych do kwestii zabezpieczenia antykorozyjnego, można by w tym momencie zakończyć pisanie artykułu. Najczęściej klient nie pyta o gwarancję, bo co niby mogłoby być nie w porządku z polakierowanym elementem? Pomijając ewidentne wpadki lakiernika związane z niepasującym kolorem, wtrąceniami, nadlewkami na krawędziach, zgazowaniem powłoki czy niewłaściwym spolerowaniem lakieru, klient w zasadzie się „nie czepia”. Jest tak szczęśliwy, że ma polakierowane auto, iż zazwyczaj pobieżna wizualna ocena wystarcza mu do akceptacji naprawy. Stąd lakiernicy pod nosem prześmiewczo odpowiadają, że „gwarancja do bramy”.
Podsumowując, klient serwisu lakierniczego ma rzeczywiście znikome możliwości oceny poprawności technologicznej przebiegu naprawy. Oprócz wizualnej oceny powłoki, jeśli posiada miernik do pomiaru grubości powłoki, może ewentualnie ocenić zbyt dużą całkowitą jej grubość. Pomiar grubości całkowitej nie daje niestety informacji o grubości poszczególnych warstw (w tym zabezpieczenia antykorozyjnego). Fakt ten powszechnie wykorzystują serwisy lakiernicze, idąc na „skróty technologiczne”, na zasadzie: czego oko nie widzi – tego sercu nie żal.
Formalnie jednak, zgodnie z prawem konsumenckim, klient ma 2 lata na dochodzenie swoich roszczeń, więc w momencie wydania faktury lub rachunku serwis automatycznie przez taki okres ponosi odpowiedzialność gwarancyjną za naprawę lakierniczą. W przypadku wymiany elementu na nowy, oryginalny i zabezpieczony fabrycznie kataforezą zagwarantowanie 2-letniego okresu gwarancji nie stanowi większego problemu, natomiast w przypadku elementów naprawianych warto zadbać o odpowiednie zabezpieczenie antykorozyjne.
Pytanie brzmi: dlaczego serwisy lakiernicze stosują skróty technologiczne? Jeden powód już znamy (niemożność dokładnego sprawdzenia przez klienta), drugim jest chęć skrócenia czasu naprawy i zmniejszenie zużycia materiałów.
Z obserwacji praktyk warsztatowych wynika, że najczęstsze zaniechania w zakresie zabezpieczenia antykorozyjnego w naprawie lakierniczej to:
- brak podkładu antykorozyjnego przed nałożeniem szpachlówki poliestrowej,
- brak zabezpieczenia antykorozyjnego lub zbyt słaba izolacja miejsc przeszlifowanych na podkładzie i bezpośrednie nakładanie koloru bazowego.
Dlaczego te zaniechania są niebezpieczne i jakie możliwości zabezpieczenia antykorozyjnego mają lakiernicy we wspomnianych przypadkach?
Zabezpieczenie antykorozyjne przed szpachlówką poliestrową
Powszechne szpachlowanie na „gołą blachę” to standard napraw lakierniczych. Na czym więc polega problem? Higroskopijne wypełniacze – talki, baryty, dolomity – i higroskopijna z natury żywica poliestrowa używana najczęściej w szpachlówkach powodują, że trudno oczekiwać od niej właściwości antykorozyjnych.
Żywica poliestrowa zapewnia z reguły bardzo dobrą przyczepność do wszystkich podłoży, nie znaczy to jednak, że bezpośrednie nakładanie, w szczególności na niezabezpieczone, podatne na korozję (stal) podłoże jest optymalnym wyborem. W praktyce najczęstszym zabezpieczeniem antykorozyjnym stosowanym przed nałożeniem szpachlówki poliestrowej jest podkład epoksydowy 2K. Żywica epoksydowa ma świetne właściwości barierowe (izoluje znacznie lepiej niż żywice akrylowe czy poliuretanowe), przez co użyta w podkładzie i wsparta dodatkami antykorozyjnymi doskonale zabezpiecza przed korozją. Nowoczesne rozwiązania producentów materiałów lakierniczych, mam tu na myśli podkład epoksydowy UNDER 385, znacząco ułatwiają przebieg procesu technologicznego. Jest to możliwe dzięki temu, że przy lepkości
14-15 s (DIN 4/20°) aplikujemy jedną cienką warstwę pistoletem lakierniczym z dyszą Ø 1.3, co umożliwia uzyskanie grubości warstwy podkładu epoksydowego na poziomie 15-20 µm. Taka grubość warstwy podkładu epoksydowego jest wystarczająca, żeby:
- odizolować podłoże przed nałożeniem szpachlówki,
- zapewnić właściwą przyczepność szpachlówki do podłoża,
- eliminować efekt „kontur mapy” w miejscu nałożenia szpachlówki (odznaczania się strefy brzegowej pomiędzy szpachlówką a podłożem).
Jeżeli nawet potrzeba zabezpieczenia antykorozyjnego i lepszej przyczepności nie przekonuje lakiernika do używania podkładu epoksydowego, to już wada lakiernicza w postaci mapowania szpachlówki (widocznej po naprawie) powinna go przekonać w 100%. Powstawanie „kontur mapy” wynika z tego, że wypełniacze w typowych szpachlówkach mają poziom 50-60 µm, przez co praktycznie niemożliwe jest uzyskanie gładkiego przejścia na starej powłoce lakierowej/metalu.
Dzięki nakładaniu szpachlówki poliestrowej na podkład epoksydowy, w którym wielkość wypełniacza wynosi 5-10 µm (w strefie przejścia następuje połączenie dużych wypełniaczy ze szpachlówki i małych wypełniaczy z podkładu), jesteśmy w stanie uzyskać bardzo gładkie przejście, co w praktyce eliminuje ryzyko pojawienia się „kontur mapy”.
Jeżeli do tego dodamy informacje, że nakładanie szpachlówki poliestrowej na podkład epoksydowy SPECTRAL UNDER 385, zaaplikowany w jednej cienkiej warstwie, jest możliwe po 30 min/20°C i dodatkowo nie musimy go szlifować przed jej nałożeniem, to mamy przyjazne lakiernikowi rozwiązanie technologiczne.
Brak zabezpieczenia antykorozyjnego/słaba izolacja miejsc przeszlifowanych
Jednym z czynników, który decyduje o stopniu zabezpieczenia antykorozyjnego, jest grubość nakładanej warstwy. Ma to szczególne znaczenie w przypadku powłok, które działają na zasadzie barierowej (np. podkłady epoksydowe). Wiadomo że nawet najlepsza żywica w podkładzie i najgrubsza warstwa nie chronią na wieczność. Jeżeli jednak mamy do wyboru podkład epoksydowy i akrylowy, np. do izolacji miejsc przeszlifowanych, to zdecydowanie lepszy dla ochrony będzie podkład epoksydowy, gdyż przy takiej samej grubości zapewni lepszą ochronę.
Korozja najszybciej pojawia się w miejscach, gdzie czynniki zewnętrzne (woda, sól) będą miały najdłuższy czas do penetracji powłoki (progi, listwy ozdobne, fartuchy). Zbyt mała grubość powłoki antykorozyjnej lub jej całkowity brak w tych miejscach to prędzej czy później ryzyko pojawienia się korozji. W przypadku miejsc szczególnie narażonych na korozję (np. progi, dolne partie drzwi) najbezpieczniej sięgnąć po podkład epoksydowy 2K – SPECTRAL UNDER 385.
Na „przeszlifki” podkładu do gołego metalu w miejscach mniej narażonych na korozję możemy użyć podkładu epoksydowego w aerozolu SPECTRAL UNDER 395 Spray dla zapewnienia minimalnego okresu gwarancyjnego. Pamiętajmy jednak, że jest on przeznaczony do napraw punktowych. Dzięki szybkiemu schnięciu znacznie przyspiesza przebieg lakierowania. O ile aplikacja bazy rozcieńczalnikowej na „przeszlifki” podkładu do gołej blachy zazwyczaj uchodziła lakiernikowi bezkarnie, to już w przypadku baz wodorozcieńczalnych znacząco przyspiesza korozję lub nawet uniemożliwia ich aplikację w tych miejscach. Łatwość użycia podkładu epoksydowego w aerozolu SPECTRAL UNDER 395 Spray praktycznie wyeliminowała świetny w działaniu podkład reaktywny SPECTRAL UNDER 345.
W zasadzie, mówiąc o ochronie antykorozyjnej, powinniśmy rozpocząć od podkładu reaktywnego. Sposób jego działania jest odmienny niż powłok barierowych. W tym przypadku nie działa grubość powłoki, tylko chemia komponentów. Nie przypadkowo utwardzacz do produktu jest zamknięty w opakowaniu z tworzywa sztucznego, zawiera on kawas ortofosforowy. Połączenie żywicy poliwinylowej z komponentu A, pigmentów antykorozyjnych i wspomnianego kwasu ortofosforowego daje (w wyniku reakcji chemicznej – pasywacji) świetne zabezpieczenie antykorozyjne.
Dlaczego lakiernicy tak rzadko sięgają po podkład reaktywny? Powodów tego stanu jest kilka, m.in.:
- na podkład reaktywny nie można nakładać bezpośrednio szpachlówki (wymagana jest wcześniejsza izolacja za pomocą podkładu akrylowego) – co wymaga czasu,
- na podkład reaktywny nie można nakładać podkładu epoksydowego,
- popełniane błędy technologiczne (zbyt duża dysza, zbyt grube warstwy, nakładanie za pomocą pędzla, zacieki itp.).
Zabarwienie podkładu reaktywnego nie służy do uzyskania siły krycia – ma informować lakiernika, czy równomiernie go zaaplikował w cienkiej warstwie. Grubsza warstwa to niekoniecznie lepsza ochrona, a gwarantowany problem z doschnięciem – podkład w zacieku lub nałożony w bardzo grubej warstwie pędzlem nie dosycha nawet w ciągu 0,5 roku i jest cały czas „gumowaty”. Zbyt grubą warstwę lub zaciek z podkładu reaktywnego należy usunąć przed aplikacją podkładu akrylowego. Natomiast, dla doświadczonego lakiernika podkład reaktywny stosowany na „gołą blachę” w cienkiej warstwie 4-5 µm na sucho, a następnie pokrywany podkładem akrylowym, w szczególności w wariantach „mokro na mokro”, to świetne rozwiązanie zapewniające ochronę antykorozyjną przy niewielkim zużyciu materiału. Podkład reaktywny świetnie sprawdzi się w szczególności w miejscach, w których wcześniej rozpoczęły się procesy korozyjne (korozja nalotowa).
Tomasz Tomczyk
wicedyrektor, Dział Szkoleń NOVOL
Komentarze (0)