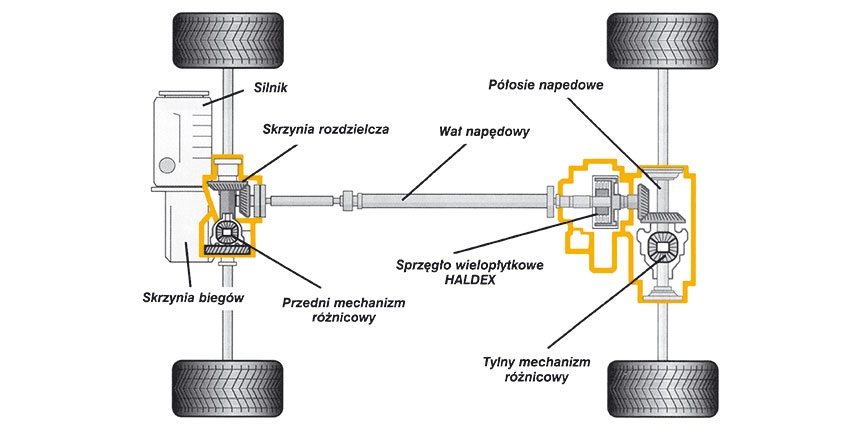
Rys. 1. Przykład układu napędowego pojazdu z nierozłączalnym napędem na wszystkie koła (źródło: Haldex).
1. Pomiar wartości luzów osiowych i kątowych
Stan techniczny układu napędowego ocenia się na podstawie wyników pomiarów: luzu kątowego całego układu napędowego, wybranych grup zespołów, poszczególnych zespołów, skoku jałowego i skoku roboczego pedału sprzęgła, luzu osiowego wałka atakującego przekładni głównej, luzów w przegubach i połączeniach wielowypustowych wałów napędowych itp. Istotną trudnością w praktycznym zastosowaniu tej metody diagnostycznej jest brak kryteriów oceny stanu technicznego układu napędowego za pomocą luzu kątowego. Dopiero przypisanie konkretnemu elementowi, na przykład przekładni głównej, odpowiedniej wartości luzu kątowego pozwala na praktyczne zastosowanie opisanej metody. Przykładowo zależność między sumarycznym luzem kątowym w układzie napędowym i przebiegiem pojazdu samochodowego można wyrazić równaniem:
L = a · x + b
gdzie:
L – sumaryczny luz kątowy [0],
b – początkowy luz kątowy [0],
a – średnia intensywność wzrostu sumarycznego luzu kątowego [0/1000 km],
x – przebieg samochodu [tys. km].
Znajomość tego modelu daje możliwość oceny luzu kątowego, jak również prognozowania jego zmian w czasie eksploatacji samochodu. Na przykład dla samochodu ciężarowego średniej ładowności po wykonaniu badań ustalono, że zmianę luzów kątowych całego układu napędowego, skrzyni biegów oraz przekładni głównej mostu można przedstawić równaniami linii prostej [2]:
LUN = 0,06 x + 8,5 [o]
LSB = 0,004 x + 1,6 [o]
LMN = 0,06 x + 6,1 [o]
Stwierdzono, że przekładnia główna wraz z mechanizmem różnicowym wywiera największy wpływ na wartości luzu kątowego układu napędowego rozpatrywanego pojazdu w procesie użytkowania. Ustalono dwie graniczne wartości luzu kątowego dla tylnego mostu tego samochodu. Dolna granica luzu (2,5÷5o) pozwala ocenić poprawność montażu tylnego mostu, górna granica (18o) odpowiada osiągnięciu przez główne elementy przekładni tylnego mostu granicznych wartości zużycia powierzchni współpracujących. Ustalono również, że przekładnię główną należy regulować po stwierdzeniu wartości luzów kątowych w zakresie 12-140. Pomiar luzu kątowego należy do czynności kontrolnych w ramach obsługiwania technicznego. Umożliwia to bieżącą kontrolę stanu technicznego przekładni głównej i przeprowadzenie regulacji luzu w chwili najbardziej odpowiedniej.
Przedstawiona analiza wyników badań luzów kątowych w układach napędowych rozpatrywanych pojazdów ciężarowych średniej ładowności pozwala stwierdzić, że opisana metoda pomiaru jest przydatna do oceny stanu technicznego układu napędowego samochodu.
Schemat pomiarowy luzów w układzie napędowym pojazdu samochodowego [2].
2. Diagnozowanie wibroakustyczne
Diagnostyka wibroakustyczna jest procesem diagnostycznym wykorzystującym do opracowania diagnozy obiektu sygnały wibroakustyczne, to jest drgania i hałas towarzyszące funkcjonowaniu obiektów technicznych podczas pracy.
Informacje o stanie technicznym zespołów układu napędowego zawierają również wytwarzane podczas ich pracy sygnały wibroakustyczne. Podczas pracy obiektów technicznych, w wyniku zachodzących w nich procesów roboczych, wzbudzają się drgania, dla których ośrodkiem przenoszenia się są elementy samego obiektu i otaczające go środowisko. Efektem zewnętrznym drgań w pierwszym przypadku są wibracje, a w drugim hałas. Drgania stanowią odzwierciedlenie najistotniejszych procesów fizycznych zachodzących w obiekcie (zespole, mechanizmie). Parametry drgań charakteryzują zarówno ogólne właściwości obiektu, jak i właściwości poszczególnych jego elementów. Źródłami drgań w samochodach są na przykład procesy gazodynamiczne, regularne zderzenia części w skojarzeniach na skutek luzów i niewyrównoważenia mas, drgania wywołane procesami tarcia między współpracującymi elementami. Drgania te, choć z reguły niekorzystne dla pracy obiektu, są cennym symptomem diagnostycznym, ponieważ wyróżniają się dużą pojemnością informacyjną. Charakteryzujące je wielkości (amplituda, częstotliwość i inne) są bardzo wrażliwe na zmiany wywołujących je procesów oraz na zmiany parametrów struktury, determinujących sposób rozchodzenia się drgań.
Drgania elementów pojazdu są możliwe do zmierzenia w normalnych warunkach pracy i cechuje je szerokie widmo umożliwiające dokładną analizę rejestrowanych sygnałów. Diagnostykę wibroakustyczną wykorzystuje się przede wszystkim do oceny stanu technicznego silnika, zespołów układu przeniesienia napędu (zwłaszcza przekładni zębatych i ułożyskowań wałów), elementów zawieszenia samochodu itp.
Wibroakustyczny sygnał diagnostyczny może być rejestrowany za pomocą czujnika umieszczonego bezpośrednio na obiekcie badań lub za pomocą mikrofonu umieszczonego w pobliżu badanego obiektu (zespołu). W pierwszym przypadku sygnał diagnostyczny jest opisywany za pomocą wielkości charakteryzujących ruch drgający (np. przemieszczenie, prędkość, przyspieszenie), w drugim za pomocą wielkości charakteryzujących zjawiska akustyczne (ciśnienie akustyczne, natężenie dźwięku, moc akustyczna itp.). Miarami tych wielkości są najczęściej: amplituda, poziom (w odniesieniu do wielkości akustycznych), częstotliwość, a także charakterystyki częstotliwościowe, charakterystyki statystyczne oraz ich estymatory.
Sygnał wibroakustyczny jest jednak najczęściej sygnałem złożonym, pochodzącym z wielu źródeł, a bogactwo niesionych przez niego informacji stwarza poważne trudności z właściwą ich interpretacją. Dlatego najważniejszym problemem diagnostyki wibroakustycznej jest znalezienie sposobu na rozdzielenie sygnału na takie składowe lub wyznaczenie takich charakterystyk, które można by było jednoznacznie przyporządkować określonym źródłom i które umożliwiłyby dokonanie jakościowej i ilościowej oceny zmiany określonych parametrów struktury obiektu. Służą do tego specjalnie opracowane metody analizy sygnałów, wykorzystujące analizatory oraz metody komputerowe.
Najczęściej stosuje się następujące rodzaje analizatorów: urządzenia do analizy statystycznej, urządzenia do analizy korelacyjnej oraz urządzenia do analizy widmowej. Analizatory mogą być instalowane na końcu toru pomiarowego zamiast rejestratora lub równolegle do niego. Wówczas analiza sygnałów odbywa się w sposób ciągły. Innym rozwiązaniem jest na przykład nagrywanie sygnałów pomiarowych na taśmie (płycie) rejestratora magnetycznego i następnie odtwarzanie ich w warunkach laboratoryjnych, co umożliwia ich obróbkę za pomocą analizatora.
Podstawową wyjściową charakterystyką odbieranego od obiektu technicznego sygnału wibroakustycznego jest jego realizacja czasowa, to znaczy zmiana wartości amplitudy dowolnego parametru sygnału (przemieszczenia, przyspieszenia, ciśnienia akustycznego itp.) w funkcji czasu. Jest to funkcja losowa i jej bezpośrednie wykorzystanie do diagnozowania stanu technicznego obiektów jest ograniczone. Celem maksymalnego wytłumienia zakłóceń oraz uściślenia obserwacji sygnał wibroakustyczny jest rejestrowany w możliwie wąskim paśmie częstotliwości charakterystycznym dla danego skojarzenia.
Najczęściej jednak realizacja czasowa sygnału jest przetwarzana na inną charakterystykę (np. postać widmową, funkcję korelacyjną itd.). Jednym ze sposobów jest analiza spektralna drgań polegająca na pogrupowaniu składowych sygnału według częstotliwości. Uzyskane w ten sposób widmo amplitudowo-częstotliwościowe umożliwia uwypuklenie zmian zachodzących w składowych sygnału, pochodzących od poszczególnych par części. Wyznaczenie funkcji korelacyjnej umożliwia zaobserwowanie zmian zachodzących w mechanizmie przez porównanie jej z wzorcami charakterystycznymi dla poszczególnych stanów bądź przez wydzielenie z sygnału składowych okresowych.
Schemat funkcjonalny podstawowego systemu pomiaru i analizy procesów wibroakustycznych [3].
Wibroakustyczne metody badań stanu technicznego zespołów układu przeniesienia napędu (skrzyń biegów, skrzyń rozdzielczych, przekładni głównych mostów napędowych) mają na celu diagnozowanie stopnia zużycia elementów, wykruszeń zębów kół zębatych, pęknięć, uszkodzeń łożysk, nadmiernych luzów itp. na podstawie zmian w widmie badanego sygnału diagnostycznego. Sygnałami takimi mogą być na przykład przyspieszenia mierzone w wybranych punktach obudowy zespołu, poziom ciśnienia akustycznego mierzony za pomocą mikrofonów ustawionych w pobliżu badanego zespołu itp. Z uwagi na złożoność zjawisk składających się na ostateczną postać sygnału wyjściowego wnioskowanie takie jest bardzo trudne i praktycznie nie ma uniwersalnych metod umożliwiających szybkie sformułowanie diagnozy dla dowolnego zespołu. Pozytywne rezultaty uzyskuje się dla konkretnych, rozpoznanych obiektów, w wyniku zastosowania często złożonych metod analizy sygnału (metod korelacyjnych, analizy widmowej) w celu wydzielenia z rejestrowanych sygnałów tych jego składowych, które są nośnikami poszukiwanych informacji.
Metody stanowiskowe
Najbardziej przydatnym sposobem oceny stanu technicznego układu napędowego za pomocą parametrów efektywności pracy są badania stanowiskowe, wykonywane na rolkowych hamowniach podwoziowych. Podstawowymi wielkościami mierzonymi na hamowni podwoziowej są moc na kołach napędowych (NK) oraz kontrolne zużycie paliwa (QK). W celu określenia mocy na kołach przyjmuje się zazwyczaj warunki ustalone, to znaczy prędkość jazdy V = constans, kąt wzniesienia α= 0, przyspieszenie a = 0 m/s2. Na hamowni odwzorowuje się opory powietrza i toczenia. Badania mogą być wykonywane również w warunkach ruchu nieustalonego (V ≠ constans, a ≠ 0). Na hamowni należy wówczas odwzorować opory toczenia, powietrza oraz bezwładności. Badania w ruchu nieustalonym pozwalają określić efektywność pracy układu napędowego za pomocą rozpędzania oraz próby wybiegu. W przypadku próby wybiegu mierzoną wielkością jest droga wybiegu (Sw). Wartość tego parametru świadczy o stratach w zespołach układu napędowego i jezdnego.
Badania stanu technicznego pojazdu samochodowego na hamowni podwoziowej obejmują sprawdzenia wstępne i zasadnicze (pomiarowe).
Do sprawdzeń wstępnych (przygotowawczych) są zaliczane:
- oględziny zewnętrzne, których celem jest ocena szczelności, stopnia skompletowania oraz prawidłowości mocowania poszczególnych zespołów układu napędowego,
- ocena ilości płynu chłodzącego w układzie chłodzenia i oleju w układzie smarowania,
- określenie ciśnienia powietrza w oponach i stanu ogumienia kół,
- próba funkcjonowania silnika i zespołów układu przeniesienia napędu przy różnych prędkościach obrotowych i obciążeniach.
Przykładowe układy do pomiarów procesów wibroakustycznych [1]: a – układ najprostszy (przetwornik wejściowy i miernik), b – układ do analizy i rejestracji widma sygnału, c – układ do wyznaczania i rejestracji funkcji korelacji, P – przetwornik wejściowy, UD – układ dopasowujący, OSC – oscyloskop, M – miernik, AW – analizator, K – korelator, R – rejestrator.
Komentarze (0)