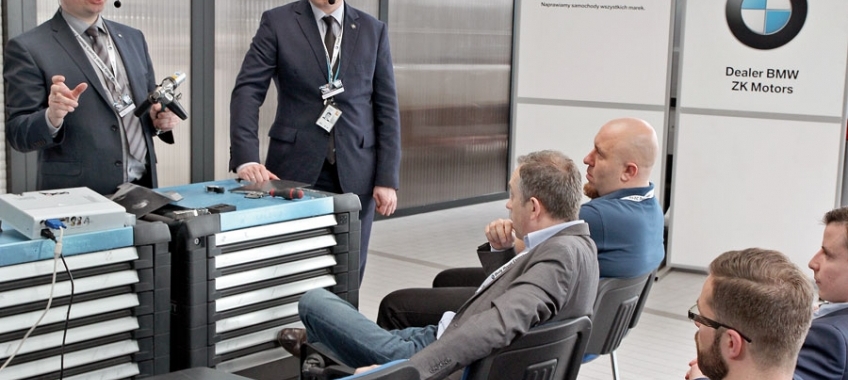
Dwudniowe szkolenie (14-15 kwietnia, Kielce) z inicjatywy Działu Aftersales BMW Group zorganizowano dla punktów dilerskich marki oraz firm ubezpieczeniowych w Polsce. Prezentowana tematyka okazała się na tyle uniwersalna, że wnioski z dyskusji wydają się ciekawe także dla tych, którym przyjdzie zmierzyć się z naprawami tychże samochodów np. w roli podwykonawców.
Miejscem spotkania był nowoczesny obiekt BMW ZK Motors – pierwszy w Kielcach i województwie świętokrzyskim autoryzowany salon koncernu BMW. Wybór to nieprzypadkowy. Najnowszy punkt sieci dilerskiej BMW Group uzyskał prestiżowy certyfikat BMW „Green Building” poświadczający zastosowanie najnowszych technologii z zakresu budownictwa przyjaznego dla środowiska.
Agenda spotkania liczyła kilkanaście bloków tematycznych. Zamysłem organizatorów było poruszenie tematów, które decydują o wysokich standardach napraw powypadkowych. Nic dziwnego. W szkoleniu z inicjatywy działu aftersales BMW Group uczestniczyli także reprezentanci rynku ubezpieczeń z firm Allianz, Warta, PZU, eksperci z firmy Dekra, co niewątpliwie podniosło merytoryczną wartość szkolenia.
Wiele pytań uczestników dotyczyło rzeczywistych czasów napraw. Prowadzący zapewnili, że tworzeniem jednostek czasowych zajmują się specjalne działy BMW. Zanim powstanie dokumentacja dla konkretnego modelu, na warsztat trafia czasem kilkadziesiąt pojazdów, a każdy jest wielokrotnie demontowany i naprawiany. Dopiero uśredniony czas staje się obowiązującym w instrukcjach naprawczych producenta.
– Dokumentacja naprawcza musi być dostępna dla podwykonawców, o ile punkt autoryzowany współpracuje w dziedzinie odbudowy karoserii z warsztatem niezależnym, które ze wskazania dealera także podlegają naszej opiece i audytom – podkreślił Jerzy Pająk, Aftersales Project Manager BMW Group Polska. – To o tyle istotne, że nawet nity używane do łączenia dwóch elementów konstrukcyjnych dostarczane są w dwóch specyfikacjach, a gwarancja takiego połączenia w niemałej mierze zależy od rodzaju użytych wierteł. Naprawa niewłaściwa będzie miała miejsce wtedy, gdy użyto spawania jako metody zastępczej, pomimo wyraźnego wskazania, że konieczne było nitowanie lub klejenie.
Przedstawiciele koncernu BMW podkreślali, jak ważne są wstępne oględziny, demontaż uszkodzonych elementów i pomiar punktów bazowych. Co ciekawe, miejsca wycięcia elementów uszkodzonych – tu oczywiście korzystamy z dokumentacji technicznej – powinny być od razu zabezpieczane antykorozyjnie (np. podłużnice). Według standardów BMW obowiązek taki nie leży więc w gestii lakiernika. Za naganne uznali użycie metod udarowych – zwłaszcza przyrządu do prostowania podłużnic.
Nieco o konsekwencjach
O konsekwencjach niestosowania się do wytycznych producenta pojazdu wspomniano, przywołując co bardziej ryzykowne pokusy napraw. Sporo miejsca poświecono też weryfikacji jakości prac – w końcowym etapie za pomocą szczelinomierza i pomiarów ściśle według tolerancji producenta. Skądinąd potrzebę wnikliwszej inspekcji wizualnej przywołano kolejny raz, bo przy okazji prezentacji zaawansowanych technologicznie materiałów. Mowa była o komponentach z włókien węglowych. Konstrukcję i ocenę uszkodzeń elementów karbonowych omawiano na przykładzie BMWi. Wspomnijmy, że zdecydowanie tylko do wymiany kwalifikuje się komponent, jeśli uszkodzenie objawia się wystającymi (postrzępionymi) włóknami. Podobnie będzie w przypadku rozwarstwienia osnowy włókien. Zawsze też należy dokonać kolejnej weryfikacji, analizując kąt uszkodzenia.
Temat jakości i weryfikacji prac naprawczych przywołano jeszcze kilkukrotnie podczas prezentacji metod napraw poszycia. W BMW dopuszczalne przypadki naprawy poszycia nadwozia warunkują przypadki, gdy: brak uszkodzeń wzmocnień pod poszyciem; połączenia spawane i klejone nie są rozerwane; brak pęknięć/rozerwań poszycia. Zakres alternatywnych napraw elementów plastikowych szerzej omówiono w aspekcie zderzaków przednich i tylnych. Pokusę napraw ogranicza wielkość uszkodzenia (do Ø 25 mm) bez przejść do krawędzi elementu. Dlaczego tak?
– Jakkolwiek procedury spawania tworzyw sztucznych są dopuszczalne, ponieważ są one opłacalne, to w przypadku naprawy zderzaków wyposażonych w czujniki systemów aktywnego bezpieczeństwa i ochrony pieszych, klamry lub inne elementy metalowe nie mogą być używane. Nawet grubość nowej powłoki lakierniczej czy szpachli użytych podczas prac lakierniczych może zakłócać działanie systemów antykolizyjnych – podkreślił J. Pająk.
Realizacja takich prac musi uwzględniać fakt, że czujnik działa poprawnie, gdy pole pomiaru fali ultradźwiękowej nie jest zakłócone.
Przestrzegając przed konsekwencjami daleko posuniętych napraw zderzaków, organizatorzy zaprezentowali film, który dowodził, jak bardzo pęd powietrza wzbudza taki w rezonans, co skutkuje nie tylko pogorszeniem komfortu jazdy (propagacja hałasu), ale także błędami w odczycie kamer czy pęknięciami w naprawianych miejscach. Wniosek był nader oczywisty. Podczas odbudowy pojazdu coraz częściej przyjdzie nam wykazać się wiedzą wykraczającą poza tradycyjnie pojmowane rzemiosło blacharza czy lakiernika samochodowego. Kodowanie kamer stanowi oczywiście osobny temat tak realizowanych napraw.
Czujnik deszczu – jak wymieniać?
Kolejny punkt programu dotyczył reżimu prac polegających na wymianie szyb samochodowych. Prezentacji towarzyszył wstęp, podczas którego uczestnicy spotkań dokonali analizy szyb czołowych pochodzących od różnych dostawców. Na pozór identyczne produkty różniły się wagą, transparentnością i jakością wykonania.
Przednia szyba samochodowa stanowi również istotny element systemu AIRBAG. Podczas zderzenia poduszka powietrzna napełnia się gazem, znajdując jeden ze swoich punktów podparcia właśnie na szybie. Jeśli szyba nie wytrzyma tego naprężenia, pęknie lub wypadnie, uniemożliwi poduszce właściwe napełnienie, przez co nie będzie ona skuteczna w razie kolizji, więc nie ochroni od obrażeń. Skoro przeszklenie karoserii pełni niebagatelną rolę w dziedzinie zachowania sztywności nadwozia, prowadzący uczulali na aspekt weryfikacji produktów, jakość (klejenia) montażu i pasowania.
Szczególną uwagę poświęcono wymianie czujnika deszczu – mowa o operacji przełożenia nieuszkodzonego elementu do wklejonej (nowej) szyby. Fabrycznie montowane są w tej chwili dwa rodzaje czujników – różniące się na pierwszy rzut oka gabarytami (35 mm i 55 mm). Okazuje się, że ten mniejszy, nowszy technologicznie przysparza sporo problemu podczas wymiany szyby czołowej. Praktyka dowodzi, że nierzadko próby odklejenia go z uszkodzonej szyby kończą się zniszczeniem. O ile trudności nie sprawia uwolnienie metalowych zacisków obudowy sensora, to po poluzowaniu blokady trzeba odczekać ok. 30 minut, by w określonych warunkach (temperatura 20°C na powierzchni silikonu) warstwa silikonu się zrelaksowała i dopiero potem należy delikatnie oderwać płytkę sensora od szyby. Jeśli warstwa silikonu nie schodzi równomiernie, należy zrobić to jeszcze wolniej.
Wniosek? Uczestnicy – zarówno przedstawiciele punktów dilerskich, jak i TU – zaapelowali do przedstawicieli działu aftermarket BMW, by w kosztorysie napraw precyzyjniej dookreślić owo ryzyko uszkodzenia czujnika.
Reżim układu kierowniczego
Długo jeszcze w kuluarach uczestnicy szkolenia rozwodzili się nad wywołanym przez organizatora tematem, związanym z odpowiedzialnością prawną ASO i TU, gdy poniechać wymiany przekładni kierowniczej na skutek uszkodzeń w wyniku wypadku.
Jak wiadomo, podczas wypadku lub podobnych zdarzeń na skutek nagłych obciążeń układu kierowniczego może dojść do różnych uszkodzeń przekładni kierowniczej. W przypadku przekładni wykrycie wewnętrznych usterek jest bardzo trudne i żmudne, niemożliwe w warunkach warsztatowych. Usterki te stanowią niedopuszczalne ryzyko dla pojazdu, ponieważ mogą spowodować uszkodzenie całego układu kierowniczego.
– Całościowa kontrola wszystkich elementów przekładni kierowniczej z reguły jest nieopłacalna ze względu na nieproporcjonalnie duży nakład pracy, dlatego uwzględnia się wtedy stan innych powiązanych elementów, których kontrola jest łatwiejsza. Potrzeba dogłębnych badań, aby zagwarantować integralność strukturalną przekładni kierowniczej po wypadku, a igranie z ludzkim życiem w imię redukcji kosztów jest karygodne – przybliżył wykładnię producenta J. Pająk. – Jeżeli wymiana przekładni kierowniczej, wymagana ze względów bezpieczeństwa, zostanie odrzucona przez klienta lub ubezpieczyciela ze względu na koszty, należy sporządzić notkę do akt, którą musi podpisać strona ponosząca koszt naprawy powypadkowej. Uwaga! Elementy bezpieczeństwa, których poprawne funkcjonowanie nie może już zostać zagwarantowane, mogą spowodować cofnięcie dopuszczenia pojazdu do ruchu. Jeśli więc naprawa zostanie odrzucona przez klienta ze względu na koszty, to należy sporządzić stosowną dokumentację.
Pomijając dyskusję, przybliżmy procedurę wypracowaną przez koncern BMW. Otóż należy wymienić przekładnię kierowniczą wraz z drążkami kierowniczymi z prawej i lewej strony, jeżeli spełniony jest przynajmniej jeden z poniższych punktów: widoczne lub w inny sposób wykrywalne uszkodzenia przekładni kierowniczej; niedopuszczalny wzrost momentu obrotowego potrzebnego do obracania kierownicą oraz zacieranie przekładni kierowniczej podczas obracania kierownicą pomiędzy skrajnymi położeniami (bez hydraulicznego układu wspomagania kierownicy); przekroczenie dopuszczalnych wartości tolerancji podczas pomiaru geometrii kół; szkody na skutek pożaru. Determinuje nas też trwałe odkształcenie lub pęknięcie obręczy kół, jeżeli wynik kontroli geometrii kół jest negatywny, a także uszkodzenie: kolumny zawieszenia, amortyzatorów, zwrotnic i mocowań kół, wahaczy poprzecznych, drążków reakcyjnych, wahaczy wleczonych lub stabilizatorów o takiej samej funkcji, złącz śrubowych elementów ustalających koło w nadwoziu, korpusu osi przedniej, ramion kierowniczych, drążków kierowniczych, mocowań przekładni kierowniczej, a także oczywiście samej kolumny kierownicy.
No dobrze, a co się dzieje z wymontowanymi przekładniami według owej procedury? Podlegają zwrotowi do fabryki, gdzie są złomowane. Części te nie mogą wrócić na rynek.
W naszej relacji pominęliśmy inne, nie mniej ciekawe punkty dwudniowego spotkania. Obszerny blok szkoleniowy dotyczył np. technologii lakierowania i drobnych napraw, sporo miejsca poświęcono uszkodzeniom felg i opon. Ciekawy zapis w instrukcjach BMW dotyczy też bieżnika kół. Akceptowalna różnica głębokości bieżnika to do 2 mm. Ten wymóg ma bowiem zasadnicze znaczenie dla poprawności działania systemów wspomagających kierowcę (np. DSC). Co ciekawe, koncern nie przewiduje montażu opon naprawianych – obojętnie jak bardzo zaawansowane są metody producenta ogumienia.
Po dwóch dniach owocnych dyskusji i sporów uczestnicy doszli do wspólnego wniosku, iż producent konstruując auto, równolegle opracowuje technologię naprawczą popartą szeregiem badań i testów. Odejście od niej przy naprawie powypadkowej może stanowić nawet śmiertelne zagrożenie dla uczestników ruchu drogowego. Pracownicy serwisów blacharsko-lakierniczych BMW przechodzą szereg szkoleń technicznych w ramach ścieżki szkoleniowej, podczas której poznają metody naprawcze opracowane przez inżynierów BMW. Należy zdawać sobie sprawę, iż to właśnie producent wyznacza metody naprawcze swoich pojazdów, nie firma ubezpieczeniowa czy dystrybutorzy rozmaitych narzędzi dla serwisów blacharskich.
Rafał Dobrowolski
Fot. R. Dobrowolski i materiały szkoleniowe Aftersales BMW Group
Komentarze (0)