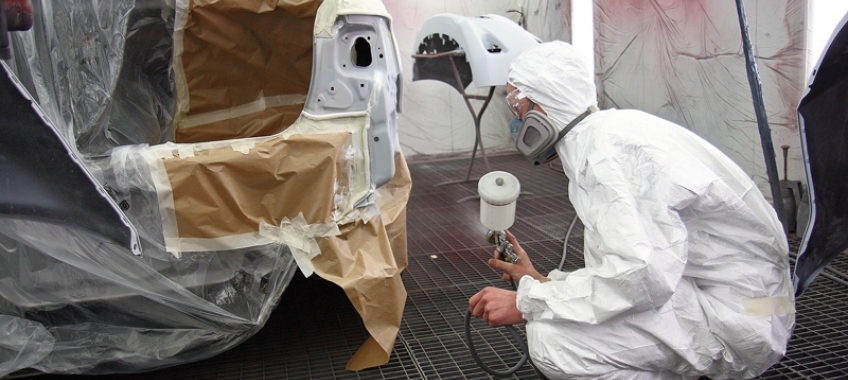
Komercyjny debiut tych produktów na terenie Polski nastąpił wiosną 1997 roku w ASO Opel w Łodzi. Od 2000 roku można już było mówić o rozwoju tej technologii na terenie kraju, ponieważ z każdym miesiącem przybywało nowych lakierni ASO wyposażanych w mieszalnie z systemem wodorozcieńczalnym, oferowanym przez coraz większą ilość dostawców. W tle tych zmian technologicznych głośno mówiono także o wymogach formalno-prawnych i spodziewanym zmierzchu technologii konwencjonalnej, opartej o rozcieńczalniki organiczne. Rynek usługodawców zaczął się dzielić na zwolenników nowego materiału (lakiernie ASO oraz duże warsztaty rzemieślnicze) oraz na zdeklarowanych przeciwników tego systemu (małe lakiernie i warsztaty samochodowe). Wydawało się, że przepisy prawa zmuszą wszystkich do daleko idących zmian technicznych w lakierniach samochodowych, jak i do przyjęcia efektów rewolucji technologicznej, w której spoiwo lakieru modyfikowane wodą stanowiło najważniejszy czynnik wprowadzanych zmian.
Wyposażenie lakierni z materiałami wodorozcieńczalnymi
„Początek nowego” to także chwila, gdy na braku rzetelnych i wyczerpujących informacji rodzą się plotki i niedomówienia, w tym przypadku niedomówienia technologiczne. W bezpośredni sposób zmiana systemu lakierów wymuszała tylko zmianę pistoletów lakierniczych i to w niektórych tylko lakierniach (czasami wymiany lub zakupu drugiej myjni tych aparatów z dodatkową komorą do mycia wodą). Najwięcej kontrowersji pod względem kosztów inwestycji wzbudzała jednak sygnalizowana powszechnie konieczność wymiany komory lakierniczo-suszarniczej. Urządzenie to do chwili pojawienia się informacji o obowiązkowym i powszechnym stosowaniu lakierów wodnych przy naprawach i renowacji pojazdów dostępne było w bardzo prostych konfiguracjach i słabych osiągach technicznych. Wiele kabin z końca XX wieku i pierwszych lat wieku XXI nie posiadało turbiny wyciągowej, a jedynie sam nadmuch ogrzanego powietrza. Sporo urządzeń wyposażonych nawet w turbinę wyciągową nie posiadało funkcji recyrkulacji w fazie suszenia, tzn. że ogrzane na wymienniku ciepła powietrze było jednak powoli usuwane na zewnątrz, podnosząc koszty fazy suszenia. Wiele kabin lakierniczo-suszarniczych funkcję recyrkulacji zachowywało na mało wydajnym poziomie 70/30%, co oznaczało, że aż 30% ogrzewanego powietrza w fazie suszenia kierowane jest nadal na zewnątrz. Nowe urządzenia ze zintegrowanymi jednostkami termowentylacyjnymi (tzw. monoblokiem) wykazywały nieco większą skuteczność na poziomie 80/20%. Wydajność przesyłowa wentylatorów w urządzeniach kabino-suszarek powszechnie obecnych w lakierniach samochodowych tamtego okresu zamykała się w granicach 16-25.000 m3/h, gwarantując prędkość opadu powietrza na poziomie 0,17-0,26 m/s. Dopiero od 2005 roku dostępna była powszechnie norma PN-EN 13355:2004 określająca zasady bezpieczeństwa dla zintegrowanych komór malarskich. Norma ta zharmonizowana jest dyrektywą maszynową, co oznacza, że urządzenia produkowane po 2005 roku, wykonane zgodnie ze wskazaniami dobrowolnie wykorzystywanej normy, bez problemów ocechowane były przez producenta znakiem CE i wydawaną dla tego znaku Deklaracją Zgodności WE. Norma ta sugerowała producentom komór lakierniczych projektowanie ich w taki sposób, aby średnia prędkość opadu powietrza w fazie lakierowania wynosiła 0,3 m/s. Technicy koncernów lakierniczych i osoby związane z branża lakierniczą sugerowały często właścicielom nowo projektowanych obiektów, że kabina lakiernicza przystosowana do aplikacji lakierów wodorozcieńczalnych musi mieć prędkość opadu na poziomie 0,26 m/s, a przepływ powietrza przez wnętrze tego urządzenia wynosić powinien minimum 26.000 m3/h. Generalnie nie wiadomo do dziś, skąd czerpane były takie dane. Wskazana w normie prędkość opadu 0,3 m/s wynikała z symulacji i obliczenia potencjalnego zagrożenia wybuchem i to akurat dla materiałów zawierających spore ilości palnych substancji lotnych. W normie nie ma nigdzie mowy o konieczności dostosowania urządzenia czy jego części składowych do współpracy z materiałem wodorozcieńczalnym. Tym bardziej nie ma tu żadnych parametrów, które mogłyby taką kabinę zaklasyfikować jako gotową do pracy z tymi materiałami.
Plotka powtórzona kilkaset razy stała się więc obowiązujący standardem. Zaczęło się tu zakorzeniać nowe sformułowanie techniczne: „kabina do lakierów wodnych”. Nikt nie wiedział, czym faktycznie ma być taka kabina, ale wielu osobom wydawało się, że to taka z prędkością opadu 0,26 m/s, z przepływem 26.000 m3/h, długa na 7, szeroka na 4 i wysoka na 2,8, maks. 3 metry.
W dalszej modyfikacji mitów o specjalistycznych kabinach do wody okazywało się, że urządzenie to posiadać powinno także dysze/zwężki Venturiego. Urządzenia takie pojawiły się w dwóch wersjach: montowanych na stałe w górnej części obudowy kabiny, zasilane przez odrębne silniki i wentylatory oraz w formie pojedynczych dysz montowanych w kabinie lub tylko do nich wnoszonych. W tej wersji dysze zasilane były sprężonym powietrzem. Silny podmuch wytwarzany przez to urządzenie miał pomagać w szybkim suszeniu baz wodorozcieńczalnych. Znany powszechnie fakt bardzo długiego czasu schnięcia baz wodorozcieńczalnych stanowił też największy problem organizacyjny wielu lakierni. Lakierowany samochód blokował komorę lakierniczą na dłuższy okres niż przy używaniu starego systemu baz konwencjonalnych.
Duże, nominalne przepływy powietrza w komorach lakierniczych wymagały stosowania silników o większych mocach. Więcej zassanego, zimnego powietrza z zewnątrz to także większa ilość paliwa do jego ogrzania i wyższy koszt każdego cyklu pracy urządzenia. Sam materiał bazowy był droższy w zakupie od swoich konwencjonalnych odpowiedników. Koszty wprowadzania nowej technologii rosły. W ramach dalszego szerzenia mitów pojawiać się zaczęły pierwsze informacje technologiczne o bezbarwnych lakierach wodorozcieńczalnych i ich długim, bo ponadgodzinnym czasie suszenia w temperaturze 60OC. Każdą lakiernię, która zdecydowała się przejść na system baz wodorozcieńczalnych, czekała też wymiana pistoletów natryskowych, a w zasadzie zakup odrębnych do aplikacji bazy i lakierów bezbarwnych. Do tej pory robiono to jednym aparatem natryskowym i jednym zestawem głowic. Materiał wodorozcieńczalny pokrywany jest jednak akrylowym, chemoutwardzalnym lakierem bezbarwnym. Do aplikacji bazy wodnej stosowane były aparaty klasy HVLP, wykonane z stopów odpornych na działanie wody. Lakiery bezbarwne aplikowane były jeszcze przez chwilę standardowymi pistoletami klasy HP, a gdy te wychodziły już z użytku, zastępowano je pistoletami nowszej generacji. Od tego czasu standardem było już posiadanie w lakierni odrębnych aparatów natryskowych do baz kolorystycznych i odrębnych do lakieru bezbarwnego. Nie dość, że nowe koszty wynikły z konieczności zakupu nowych pistoletów do bazy wodnej, to jeszcze drugiego zestawu do lakierów bezbarwnych.
Gdy nowe produkty zadomowiły się już na krajowym rynku i mity o nich ustępować zaczęły faktom, okazywało się coraz częściej, że to, co nowoczesne, nie jest wcale lepsze od starego, a wiele nakładów inwestycyjnych dotyczących lakierni było po prostu zbędnych. Materiał wodorozcieńczalny nie chciał schnąć tak szybko, jak zakładano – w nowych komorach z dużym nominalnym przepływem powietrza i po fazie aplikacji bazy często uruchamiana była suszarka w celu szybkiego wysuszenia tego produktu. Ci, którzy zmienili komory na nowsze i wydajniejsze, płacili teraz więcej za paliwo niż ich koledzy w lakierniach posiadających stare, proste kabiny. Czas suszenia bazy wodnej był w tych urządzenia bardzo zbliżony. Szeroko rekomendowane dysze Venturiego ujawniły swoje wady, gdy silny przepływ powietrza powodował podrywanie pyłów w kabinie, odrywanie maskowania i łopotanie końcówek folii ochronnych. Systemu tego używano coraz rzadziej, a w wielu lakierniach szybko z niego zrezygnowano. Nowe aparaty natryskowe klasy HVLP wymagały innego prowadzenia i sposobu natrysku, ponieważ nie rozpylały one tak dokładnie lakieru jak starsze wersje pistoletów pracujących na wysokim ciśnieniu. Powodowało to, że lakiernicy mieli kłopoty z pracą z lakierami bazowymi i cieniowaniem elementów sąsiadujących. Mimo to powoli zwiększała się ilość lakierni wyposażanych w mieszalnie z system wodorozcieńczalnym. Z dzisiejszego punktu widzenia można by stwierdzić, że wprowadzenie lakierów wodorozcieńczalnych do lakierni samochodowych w Polsce trafiło w idealny moment. Pomimo chwilowych mikrotąpnięć lata 1997-2005 to okres stałego rozwoju branży naprawczej. W tym okresie powstawały nowe stacje ASO z nowoczesnymi lakierniami, główny odbiorca technologii lakierów wodorozcieńczalnych. Duże warsztaty samochodowe zawierały korzystne umowy o współpracy z salonami sprzedaży samochodów dopiero formującymi swoje obiekty. Te warsztaty także korzystać zaczęły z technologii lakierów wodorozcieńczalnych. W 2008 roku wyglądało na to, że sprawa jest już przesądzona. Lakiery konwencjonalne zostaną wycofane lada moment, a kto się nie przestawił na nową technologię, musi się wycofać. Duże warsztaty i stacje ASO czekały na okres swojego triumfu. Szopy, nory czy stodoły to pojęcia, które krążyły w branży jako złośliwe określenie małych, jednoosobowych punktów usługowych, działających bez pozwoleń, zgłoszeń, wbrew zasadom środowiskowym i wielu wytycznym technologicznym obowiązującym w tej branży. Jednak nadejście dnia, w którym szara strefa i małe zakłady usługowe degradujące rynek niskimi cenami zakończą swoją działalność z braku dostępu do taniego i prostego w aplikacji materiału konwencjonalnego, wydawało się nieuniknione.
Duzi kontra mali. Podział rynku usługodawców
Minął rok, a potem kolejny. Zakończyły się wszystkie formalne okresy przejściowe. Skończył się czas tolerancji technologicznej i formalnoprawnej. W ostatniej chwili nieliczne już średnie zakłady lakiernicze nieposiadające jeszcze mieszalni z materiałami wodorozcieńczalnymi przestawiały się błyskawicznie na nową technologię. Tu rzadziej popełniano już błędy „pionierów” i nie dokonywano kompletnej przebudowy zakładu. Po prostu system lakierów konwencjonalnych w zakładzie zastąpiły nowe lakiery wodorozcieńczalne. Większa i szeroko dostępna wiedza o tej technologii oraz powszechne już programy szkoleniowe przyczyniły się do tego, że nie było problemów ze znalezieniem pracowników znających technologię nowych produktów. Czas mijał. W 2010 roku zdecydowanie widać było, że rynek branży napraw lakierniczych podzielił się na dwa przeciwstawne obozy – lakiernie, które miały nowoczesne wyposażenie i mieszalnie z materiałami wodorozcieńczalnymi oraz te, gdzie brakowało nowoczesnego, a często nawet podstawowego wyposażenia i gdzie nadal prowadzono naprawy materiałami konwencjonalnymi. W obiektach tych rzadko znaleźć można było samodzielne mieszalniki. W większości przypadków korzystały one z usług mieszalni sklepowych. Gdzieś pomiędzy tym, co nowoczesne, a tym, co już przestarzałe, znajdowała się grupa „maruderów” – lakierni działających legalnie i wyposażonych w podstawowy sprzęt dla tego typu obiektu, jednak nadal, tak jak te małe zakłady, funkcjonujących w oparciu o materiały konwencjonalne.
Gdyby zebrać się na podsumowanie tego okresu, od pionierskich działań stacji serwisowej Opla w Łodzi do dnia, w którym przepisy prawa zabroniły rzekomo używania do napraw pojazdów osobowych materiałów z dużą zawartością LZO, stwierdzić można, że operacja wymiany technologii materiałowej w legalnych lakierniach przebiegła nad wyraz sprawnie. Bez wątpienia w obecnej sytuacji, w jakiej znajduje się branża napraw powypadkowych, mało kto chciałby rozmawiać o inwestycjach i kosztownych zmianach technologicznych. Faktem jest, że wiele nakładów modernizacyjnych wymuszanych na lakierniach okazało się po czasie zbędnych i wynikało jedynie z nieznajomości tego, co nadchodzi. Jednak technologia lakierów wodorozcieńczalnych była i jest kilkakrotnie droższa od tanich produktów konwencjonalnych. Tam, gdzie rozwojem kieruje ekonomia, nie ma mowy o tym, aby nowa technologia bezproblemowo wypierała starą, gdy działania takie zamiast ewidentnych korzyści i zysków przynoszą kłopoty i straty. W takiej sytuacji nie pomagają nawet nakazy formalnoprawne i prowadzone kontrole. Wiele osób prowadzących od lat małe warsztaty blacharsko-lakiernicze, widząc niekorzystny rozwój gospodarczy, przeprowadziło analizę potencjalnych zysków i wszystkich kosztów wprowadzenia nowej technologii, rezygnując z dalszego prowadzenia firmy.
Sytuacja gospodarcza ostatnich lat nie sprzyjała nikomu w branży lakierniczej, a szczególnie legalnym usługodawcom. Lakiernicy tracili pracę w zamykanych zakładach. Znaleźć nie mogli jej też młodzi ludzie innych profesji. Na obrzeżach dużych metropolii, peryferiach większych miast i na terenach małych miejscowości, w garażach i budynkach gospodarczych powstawać zaczęły jednoosobowe, całkowicie nielegalne lakiernie samochodowe. Tu nikomu nie przychodziło nawet do głowy sięganie po produkty wodorozcieńczalne. Te małe obiekty wymuszały na mieszalniach sklepowych dysponowanie tanimi produktami. Produktami, które przecież zgodnie z obowiązującymi przepisami nie powinny być sprzedawane i używane do napraw powypadkowych i renowacji samochodów. Tanie usługi dostępne na obrzeżach każdego miasta i w wielu małych miejscowościach „ścisnęły” rynek napraw samochodowych, a szczególnie zachwiały cenami tych usług. Brak obciążeń podatkowych i formalnoprawnych, opłat środowiskowych, kosztownego sprzętu i oparcie usług o tanie produkty konwencjonalne pozwalało tym małym, niedoinwestowanym garażom wykonywać naprawy lakiernicze za 30% stawki dyktowanej przez ASO czy inne renomowane zakłady. Często krytykowana, fatalna jakość wykonywanych napraw nie znajdowała stuprocentowego pokrycia w rzeczywistości. Pamiętać tu należy, że do „szarej strefy” trafili także dobrej klasy fachowcy, osoby szkolone przez koncerny lakiernicze. Oczywiście większość takich napraw faktycznie reprezentowała fatalny poziom jakościowy. Kłopot z oceną tego rynku jest jednak taki, że wpadki jakościowe zdarzały się zarówno renomowanym obiektom z autoryzacją koncernu samochodowego, jak i tym fatalnie wyposażonym, nielegalnym malarniom. Rynek zleceniodawców usług lakierniczych szybko podzielił się na zwolenników napraw w renomowanych obiektach i zagorzałych przeciwników takich serwisów. Konflikt interesów przechodzi powoli w otwartą wojnę dwóch środowisk jednej branży. Nigdy jeszcze szara strefa napraw samochodów, szczególnie w branży lakierniczej, nie była tak rozbudowana i wszechobecna.
Gdy małe i średnie, legalnie działające lakiernie samochodowe zorientowały się, że wejście w systemy materiałów wodorozcieńczalny było zbyt pochopne, zaczęły poszukiwać podstaw prawnych i przepisów, o których wszyscy mówili, ale niewiele osób je wcześniej analizowało. Trend ten wziął się stąd, że malutkie, jednoosobowe punkty lakiernicze i ich główne źródło zaopatrzenia, czyli mieszalnie sklepowe, nadal sprzedawały, a lakiernie korzystały z materiałów konwencjonalnych. Przytaczane wcześniej zakazy i ograniczenia oraz wróżby wycofania ze sprzedaży tych materiałów okazały się jednak fikcją. Skala tego – jak się wydawało – nielegalnego procederu okazała się na tyle duża, że nikomu nie mieściło się w głowie to, żeby z takim rozmachem i tak jawnie łamane były obowiązujące przepisy prawa. Coraz częściej stawiano publicznie proste pytanie, jak to w końcu jest z tą wodą? Bezwzględny wymóg formalnoprawny czy swoboda w wyborze produktów z nadal legalnych systemów konwencjonalnych?
Analiza przepisów oraz praktyka w ich stosowaniu zaowocowały sporym zaskoczeniem dla tych, którzy przyjęli za fakt, że systemy baz wodorozcieńczalnych to jedyne dopuszczone produkty do realizacji napraw w lakierniach samochodowych. Gdzie znajdowało się niedomówienie formalne i dlaczego dziś wiele lakierni samochodowych nadal legalnie korzysta z tanich produktów konwencjonalnych, dowiecie się Państwo po lekturze ostatniej, trzeciej części publikacji.
Robert Grzywaczewski
projekter@projekter.pl
Komentarze (0)