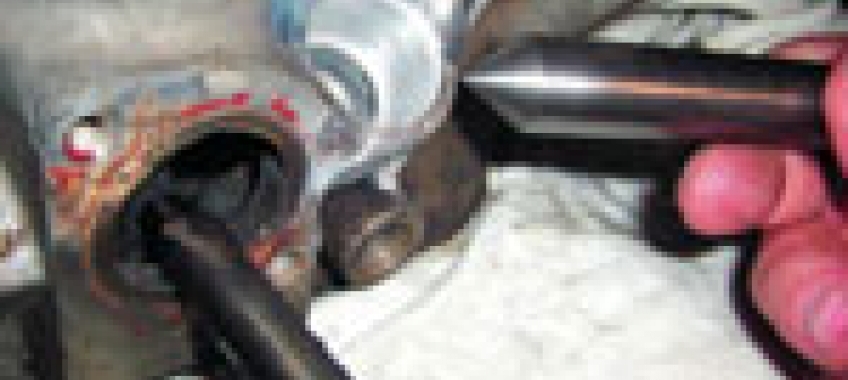
Postęp technologiczny sprawia, że swą budową współczesne głowice silnikowe przypominają... ser szwajcarski. Ażurowej konstrukcji odlewy z coraz bliżej sąsiadującymi otworami (na gniazda zaworów, świece, tłoki itd.) trudniej wykonać i coraz łatwiej zepsuć. W pogoni za osiągami i obniżeniem masy, czyli na skutek przyrostu ilości gniazd zaworów i malejącej grubości ścianek, konstrukcje głowic jednostek napędowych są coraz finezyjniej i wymyślniej odlewane, co oczywiście nie pozostaje bez wpływu na ryzyko pojawienia się fabrycznych i eksploatacyjnych uszkodzeń w postaci mikropęknięć.
Coraz częściej uszkodzeniu ulegają nie bloki silników, a właśnie głowice, choć te pierwsze powszechniej wykonuje się z aluminium, a nie z żeliwa. Głowice pracują też w dużo trudniejszych warunkach. Zmianie uległy parametry ich pracy. Na ich skróconą żywotność wpływa podwyższone ciśnienie pracy i wyższa temperatura, ponieważ bardzo często dąży się do zwiększenia czasu otwarcia zaworów oraz występują układy o zmiennych fazach rozrządu. Na wyższe temperatury pracy jednostki napędowej, wbrew pozorom, wpływa też uboższa mieszanka paliwa. Ta ostatnia wymuszona jest oczywiście chęcią budowy oszczędniejszych silników. Generalnie w benzynowych jednostkach dużo rzadziej pękają głowice. Jednostki wysokoprężne pracują w trudniejszych warunkach, bo wysiłki konstruktorów zmierzają do osiągnięcia jak największej mocy z jak najmniejszej pojemności skokowej silnika przy jednoczesnym ograniczeniu zużycia paliwa.
Miejscowe spawanie pękniętej głowicy.
- Pamiętajmy jednak, że głowica często nie jest przyczyną usterek jednostki napędowej czy nawet osprzętu silnika, co po prostu skutkiem innych usterek – zauważa inż. Arkadiusz Ignacy. - Z tych i innych powodów prawidłowa diagnoza niepokojących objawów towarzyszących pracy silnika, a dokonana przez typowy warsztat samochodowy, ma decydujące znaczenie podczas wielu czynności diagnostycznych i potem naprawczych, a dokonywanych przez wyspecjalizowane firmy, które zajmują się regeneracją głowic. Po prostu usługi te są kosztowne i z tej racji powinny być dokonywane dopiero po wykluczenia pewnych objawów. Te da się zaobserwować podczas codziennej eksploatacji pojazdu, którego jednostkę napędową podejrzewamy o uszkodzenie (pęknięcie) głowicy.
Głowica spawana od strony wałka.
Oto jakie objawy warto odnotować w poszukiwaniu usterek trapiących głowicę silnika:
- czy ubywa cieczy chłodzącej;
- czy są przedmuchy do płaszcza wodnego (po wykręceniu korka zbiorniczka wyrównującego płyn chłodzący “bulgocze”);
- czy dostaje się płyn chłodzący do układu smarowania silnika lub odwrotnie - czy to olej dostaje się do układu chłodzenia (tzw. mleko w układzie chłodzenia);
- czy puchną węże układu chłodzenia (efekt zapowietrzenia).
Najczęstsze przyczyny uszkodzenia głowic
Bardzo często głowica pęka na skutek uszkodzenia układu rozrządu. Użytkowanie pojazdu, w którym pasek rozrządu nie został na czas wymieniony, pękając lub “przeskakując” potrafi spowodować poważną usterkę kwalifikującą głowicę do kosztownej regeneracji (np. na skutek uderzenia zaworu w tłok).
- Czasem zamontowanie wątpliwej jakości napinacza paska rozrządu wystarczy, by zniszczyć napęd. Słabsza zwykle jakość łożysk nieoryginalnego napinacza skutkować może zwiększonym ryzykiem uszkodzenia całego silnika – podkreśla inż. A. Ignacy.
Czasem regeneracja głowicy sprowadza się także do wykrycia i usunięcia luzów czy śladów korozji gazowej.
Oczywiście, sama technika i kultura jazdy ma duże znaczenie dla żywotności odlewu silnikowego. W przegrzanych jednostkach napędowych mogą pojawić się wtórne odkształcenia płaszczyzny głowicy lub bloku silnika. Bardzo często dochodzi wtedy do pęknięć tych elementów. Ryzykowna jest nawet maniera dolewania płynu (najczęściej, niestety, wody) do układu chłodzenia. Nie gwarantuje to prawidłowej pracy silnika, a w ekstremalnym momencie, kiedy po prostu zabraknie tego płynu, dochodzi do przegrzania jednostki. Takie ryzyko spowodowane jest miejscowym przegrzaniem odlewu. Przegrzanie następuje, gdy powstaje “poduszka powietrzna”, która nie odprowadza ciepła z jednostki napędowej.
Proces technologiczny impregnacji detali aluminiowych.
Często też czy to na skutek niewłaściwej metody pracy, czy po prostu na skutek zapieczenia gwintów (świec czy gniazd zaworów) powstają dodatkowe uszkodzenia głowicy. Uszkodzenia mechaniczne skutkować mogą np. zerwaniem gwintu. Źle przyłożone narzędzie, które działa momentem odginającym (np. na świecę zapłonową czy żarową) na ukośnie wykonany w odlewie gwint skutkuje jego zerwaniem. Zbagatelizowanie przez mechanika konieczności wymiany uszczelek (np. pod głowicą) przy każdorazowym demontażu jednostki napędowej sprawia, że rośnie ryzyko wystąpienia niekorzystnego efektu “przedmuchu” z komory spalania do płaszcza wodnego. Przegrzaniu i uszkodzenia ulega wtedy często korpus i głowica silnika. Nawet taki wydawałoby się drobiazg jak nieszczelność korka zbiornika wyrównawczego lub chłodnicy zwiększa ryzyko wystąpienia miejscowego przegrzania odlewów i pojawienia się naprężeń skutkujących pękaniem materiału.
Diagnoza odlewów
Etapy napraw głowic polegają na: wstępnym umyciu głowicy; rozbiórce i weryfikacji jej stanu i całej jednostki napędowej (wykrycie luzów, śladów zużycia czy korozji gazowej – wypalone grzybki, pęknięcia); kontroli “płaskości”, czyli płaszczyzny przylegania do bloku cylindrów (kontrola szczelinomierzami lub snopem światła w celu wykrycia prześwitów); sprawdzeniu szczelności korpusu głowicy; regeneracji (np. spawaniu pęknięć).
Nawiercanie otworów poddanych regeneracji.
- Choć benzynowe jednostki napędowe rzadziej trapią defekty materiałów budujących korpus silnika, to np. bardzo często przychodzi nam naprawiać 2-litrowe silniki Forda modeli Transit czy Sierra – wyjaśnia inż. A. Ignacy. - Zwykle wiemy też przed diagnozą, w okolicy którego zaworu należy szukać pęknięć. Każdorazowo też, jeśli sprawdzamy głowicę na szczelność i wykluczamy objawy osłabienia konstrukcji, to i tak przy drugiej diagnozie nawet przegrzewamy korpus w poszukiwaniu najdrobniejszych pęknięć i szczelin. To że głowica jest szczelna nie gwarantuje, że nie ma w niej uszkodzeń. Diagnoza odbywa się po prostu w danym momencie i nie można wykluczyć, że pęknięcie nastąpi np. za miesiąc, bo proces naruszenia konstrukcji postępuje “od wewnątrz” w sposób niewidoczny gołym okiem i w sposób prawie niemożliwy do zdiagnozowania.
Frezarka SERDI umożliwia także wytaczanie nowych gniazd zaworowych w regenerowanej głowicy.
Sprawdzanie ciśnieniowe szczelności korpusu jest nieodłącznym elementem prawidłowej naprawy głowicy. Bardzo często po prostu pęknięcia są trudne do wykrycia “gołym okiem”. Dopiero po stworzeniu warunków zbliżonych do panujących podczas pracy silnika jest możliwe zdiagnozowanie drobnych pęknięć. Tak jak w przypadku kontroli szczelności instalacji gazowej, którą poddaje się próbie 3-4-krotnie większego ciśnienia roboczego, tak ciśnienie to musi być wyższe, więc prostym acz skutecznym sposobem jest zanurzenie odlewu w wannie z wodą i obserwacja miejsc, z których uchodzą bąbelki powietrza.
Prócz tej metody są jeszcze dwie, wymagające jednak specjalistycznych urządzeń: rentgenowskie prześwietlenia i sprawdzanie magnesem. Ta ostatnia polega na obserwacji opiłków metalu, które inaczej zachowują się w okolicach pęknięć (podobną metodę wykorzystuje się w kryminalistyce, gdzie służy ona do weryfikacji procederu przebijania numerów silnika). Czasem przed kontrolą ciśnieniową dobrze jest podgrzać głowicę do temperatury zbliżonej do wartości osiąganych w czasie normalnej pracy silnika (np. 70-80 stopni C).
- Większość pęknięć korpusów głowic jest spawalna, jeśli tylko jest dobry dostęp umożliwiający pracownikowi wykonanie tej czynności – zapewnia inż. A. Ignacy. - Pęknięcia wewnątrz (w środku) korpusu najtrudniej spawać; czasem nie pozostaje nic innego jak wyfrezowanie (lub wycięcie fragmentu odlewu) sobie dogodnego dostępu do miejsca uszkodzenia. Psujemy coś”, żeby naprawić miejsce niedostępne dla palnika spawacza. Taka ingerencja wbrew pozorom nie osłabia konstrukcji odlewu, jeśli fachowiec wie, gdzie wykonać nacięcie, które po całej operacji należy przywrócić do stanu poprzedniego. Spawanie musi odbywać się przy użyciu materiałów szczegółowo dobranych do konstrukcji danego korpusu, czyli np. druty spawalnicze muszą być zbliżonego składu co spawany materiał. Ma znaczenie też dobór prądu spawania – ten zależy w dużej mierze od grubości spawanego materiału; temperatura a nawet gaz spawania. Pracownik zaznacza precyzyjnie miejsce pęknięcia, następnie nawierca je by “dojść” do samego dołu pęknięcia i by otwór ten nabrał regularnych kształtów. Potem ukosuje się taki otwór, a czasem nawet przewierca się głowicę na wskroś, by zaspawać uszkodzenie możliwie najmocniej, czyli z obu stron głowicy. W końcu czyścimy miejsce spawania, bo też eliminacja wtrąceń czy wręcz zanieczyszczeń korzystnie wpływa na efektywność dokonanej naprawy. Dopiero po wstępnym obrobieniu naprawianego elementu nadchodzi czas na wykonanie kontroli szczelności. Na samym końcu montuje się gniazda zaworowe (po planowaniu płaszczyzny) po sprawdzeniu ich współosiowości z prowadnicami zaworowym poprzez przefrezowanie gniazd (dociera się zawory i całość montuje).
Impregnacja odlewów
Wielu producentów silników spalinowych stosuje już technologię zapożyczoną z Formuły 1, a polegającą na impregnacji odlewów. Proces ten podyktowany jest wspomnianym stopniem skomplikowania “ażurowej” konstrukcji odlewów głowic i korpusów. Impregnacja odlewów oparta jest na wypełnianiu mikroporów, które ujawniają się w procesie produkcji. Te nie byłyby oczywiście przyczyną dużych przecieków, ale jak wiadomo nawet niewielkie przenikanie czynnika, np. rozgrzanego oleju do płaszcza wodnego, prowadzi czasem do najmniej oczekiwanych defektów konstrukcji.
- W naszej firmie stosujemy wiele urządzeń światowej klasy, które służą impregnacji takich odlewów przy okazji procesu regeneracji – mówi inż. A. Ignacy. - Jednym z takich urządzeń jest linia do impregnacji próżniowej odlewów żywicami światowego lidera tej technologii – firmy MALDANER. Drugim takim urządzeniem jest frezarka do gniazd zaworowych marki SERDI. Umożliwia ona zarówno wytaczanie fabrycznych gniazd zaworowych, jak i tych nowo wykonanych przez naszych pracowników. Trzecim urządzeniem pomocnym przy regeneracji głowic i korpusów silników jest urządzenie firmy NEWAN. Służy do podciśnieniowego sprawdzania szczelności zaworów.
Opracowano na podstawie specjalnego wykładu wygłoszonego przez pana Arkadiusza Ignacego z firmy AUTOTECHN – Mariola B Plinta IGNACY dla redakcji “Nowoczesnego Warsztatu”.
Notował: Rafał Dobrowolski
Zdjęcia: AUTOTECHN i R. Dobrowolski
Komentarze (0)