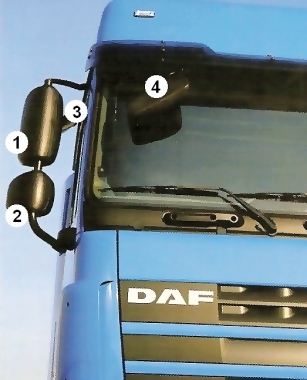
Lusterka zewnętrzne
Lusterka zewnętrzne w pojazdach mają duży wpływ na bezpieczeństwo czynne. Analiza przyczyn kolizji i wypadków, szczególnie z udziałem samochodów ciężarowych, wykazała ograniczoną widoczność pośrednią jako ich istotną przyczynę. Uznano, że niezbędne jest powiększenie obszarów wokół pojazdu, które kierujący mógłby obserwować. Mając powyższe na uwadze, zmieniono dotychczasowe przepisy dotyczące zewnętrznego pola widzenia z boku, do przodu i do tyłu. Przedstawioną problematykę obecnie regulują między innymi następujące dyrektywy Parlamentu Europejskiego i Rady:
- dyrektywa 2003/97/WE z dnia 10 listopada 2003 roku w sprawie zbliżenia ustawodawstw państw członkowskich w odniesieniu do homologacji typu urządzeń służących do pośredniego widzenia oraz pojazdów wyposażonych w te urządzenia (zmieniająca dyrektywę 70/156/EWG i uchylająca dyrektywę 71/127/EWG),
- dyrektywa 2007/38/WE z dnia 11 lipca 2007 roku w sprawie doposażenia samochodów ciężarowych zarejestrowanych we Wspólnocie w lusterka samochodowe.
Wprowadzone zmiany zostały spowodowane koniecznością dostosowania przepisów do obecnego stanu wiedzy i postępu technicznego. Pierwsza z wyżej wymienionych dyrektyw dotyczy pojazdów nowych. Ponieważ należało również poprawić widoczność pośrednią w dotychczas eksploatowanych pojazdach, zdecydowano się na wydanie drugiej dyrektywy w sprawie doposażenia samochodów ciężarowych w lusterka. Dyrektywa 2007/38/WE dotyczy pojazdów:
- kategorii N2 (pojazdy samochodowe ciężarowe o dmc większej niż 3,5 t, ale nie przekraczającej 12 t),
- kategorii N3 (pojazdy samochodowe ciężarowe o dmc ponad 12 t).
Wyżej wymienione samochody ciężarowe, zarejestrowane po raz pierwszy po dniu 1 stycznia 2000 r., powinny zostać doposażone w lusterka (fot.1): klasy IV (szerokokątne) i klasy V (bliskiego zasięgu). W większości przypadków było to technicznie wykonalne. Jeżeli byłoby to technicznie niemożliwe do realizacji lub ekonomicznie nieuzasadnione, to dyrektywa dopuszcza możliwość odstępstw od jej wymagań (takie pojazdy powinny być wyposażone w lusterka lub inne urządzenia o parametrach zbliżonych do tych, o których mowa w przepisach). Dostosowanie polskiego prawa do wymagań wspólnotowych nastąpiło po wydaniu rozporządzenia Ministra Infrastruktury z dnia 4 maja 2009 r. zmieniającego rozporządzenie w sprawie warunków technicznych pojazdów oraz zakresu ich niezbędnego wyposażenia (Dz.U. nr 75 z 2009 r.), w którym jest mowa m.in. o lusterkach szerokokątnych i bliskiego zasięgu. Również w nowym rozporządzeniu Ministra Infrastruktury z dnia 18 września 2009 r. w sprawie zakresu i sposobu przeprowadzania badań technicznych pojazdów oraz wzorów dokumentów stosowanych przy tych badaniach wprowadzono zapisy zobowiązujące diagnostę do sprawdzenia, czy pojazdy ciężarowe kategorii N2 i N3, zarejestrowane po 1 stycznia 2000 r., posiadają lusterka klasy IV i V.
Oznakowanie odblaskowe konturowe pojazdu
Wśród przyczyn wypadków drogowych z udziałem samochodów ciężarowych, do których dochodzi w godzinach nocnych i o zmierzchu, występują: zbyt późne zauważenie takiego pojazdu na drodze, niewłaściwa ocena jego wielkości i prędkości jazdy. Z badań wykonanych w Instytucie Transportu Samochodowego wynika, że w ostatnich latach około 30% wypadków z udziałem samochodów ciężarowych wydarzyło się po zapadnięciu zmroku. Najwięcej z nich stanowiły zderzenia boczne, a w dalszej kolejności były to potrącenia pieszych, zderzenia czołowe i zderzenia tylne. Dostępne wyniki badań wskazują, że zastosowanie konturowego oznakowania odblaskowego może realnie zmniejszyć liczbę zderzeń bocznych i tylnych, które stanowiły dotąd 12% wypadków z udziałem pojazdów ciężkich.
Konieczność stosowania odblaskowego oznakowania konturowego wynika z ratyfikowanych przez Polskę regulaminów EKG ONZ (regulamin nr 48). Zgodnie z rozporządzeniem Ministra Infrastruktury z dnia 4 maja 2009 r. zmieniającym rozporządzenie w sprawie warunków technicznych pojazdów oraz zakresu ich niezbędnego wyposażenia (Dz.U. nr 75 z 2009 r.), wprowadzono obowiązek takiego oznakowania dla pojazdów rejestrowanych po raz pierwszy w kraju po 10 października 2009 r. Zgodnie z tymi przepisami odblaskowe oznakowanie konturowe powinno się obowiązkowo umieścić z tyłu i z boku niżej wymienionych pojazdów (z wyjątkiem podwozia samochodu ciężarowego z kabiną i ciągnika siodłowego):
- kategorii N2 – pojazdy, których dmc przekracza 7,5 t i nie przekracza 12 t, długość jest większa od 6 m, a szerokość jest większa od 2,1 m,
- kategorii N3 – pojazdy, których dmc przekracza 12 t, długość jest większa od 6 m, a szerokość jest większa od 2,1 m,
- kategorii O3 – przyczepy i naczepy, których dmc jest większa niż 3,5 t i nie przekracza 10 t,
- kategorii O4 – przyczepy i naczepy, których dmc przekracza 10 t.
Niedozwolone jest umieszczanie odblaskowego oznakowania konturowego na pojazdach kategorii M1 (samochody osobowe) i O1 (przyczepy o dmc mniejszej niż 0,75 t). Z kolei na wszystkich pojazdach innych kategorii (także podwoziu samochodu ciężarowego z kabiną i ciągniku siodłowym) oznakowanie odblaskowe konturowe jest opcjonalnie dopuszczone do stosowania. Nadwozie wymienne nie podlega obowiązkowi oznakowania konturowego, choć byłoby to łatwe do wykonania. Należy jednak podkreślić, że jest taka potrzeba, ponieważ identycznie jak kontener nie jest wyposażone w urządzenia oświetleniowe, przez co jest słabo widoczne w nocy. Natomiast na samochodach przeznaczonych do przewozu nadwozi wymiennych, prawidłowe umieszczenie oznakowania konturowego (obowiązkowego) jest najczęściej niemożliwe.
Zgodnie z regulaminem nr 48 EKG ONZ dopuszczalne są następujące kolory oznakowania odblaskowego konturowego: dla konturu bocznego – kolor żółty lub biały, a dla konturu tylnego – kolor żółty lub czerwony. Natomiast w omawianym rozporządzeniu dopuszczono oznakowanie konturowe odblaskowe barwy białej na tylnej ścianie pojazdu, co jest niezgodne z wymogami przepisów międzynarodowych.
Niżej przedstawiono minimalne wymagania dotyczące oznakowania konturowego pojazdu:
- oznakowanie powinno stanowić minimum 80% skumulowanej długości pojazdu (jeżeli nie jest to możliwe, to 60%),
- oznakowanie konturu tylnego powinno być pełne,
- oznakowanie boczne powinno być co najmniej w postaci linii dolnej i górnych rogów,
- nie zaleca się kombinacji pojazdu i naczepy, w której tylko jedno z nich jest oznakowane,
- zastosowana taśma odblaskowa musi mieć minimum 5 cm szerokości (bardziej szczegółowe informacje zawarte są w załącznikach regulaminu).
Na fot. 2 przedstawiono przykłady rozmieszczenia oznakowania konturowego dla różnych rodzajów pojazdów samochodowych (ciągnik siodłowy z naczepą, samochód ciężarowy z przyczepą).
Diagnozowanie nadwozia
Zakres diagnozowania nadwozia pojazdu obejmuje najczęściej: określenie stopnia zużycia, sprawdzenie szczelności, określenie geometrii nadwozia oraz pomiar współczynnika przepuszczalności światła szyb samochodowych. Obecnie, ze względu na stosowane wyposażenie, podstawowymi badaniami stanu technicznego nadwozia/ramy w stacjach kontroli pojazdów w Polsce są badania organoleptyczne. Podstawą oceny stopnia zużycia nadwozia stosowaną podczas przeglądów technicznych jest ocena stopnia jego skorodowania. Badanie wykonuje się organoleptycznie, wynik kontroli jest w znacznym stopniu subiektywny i może być miarodajny tylko w pewnym zakresie, w dużym stopniu zależnym od fachowości diagnosty. Miejsca skorodowane można odszukać przez obserwację z bliska powierzchni poszczególnych elementów nośnych i poszycia nadwozia. Jeżeli uszkodzeń korozyjnych nie widać gołym okiem, to w celu ich odszukania można ostukać blachy na przykład młotkiem lub trzonkiem wkrętaka. Blachy skorodowane wydają po uderzeniu dźwięk przytłumiony i głuchy oraz nie sprężynują. Należy przeprowadzić oględziny głównych węzłów nadwozia lub elementów ramy pojazdu ustawionego na kanale lub na podnośniku. Wynik kontroli należy uznać za negatywny, jeśli stwierdzono zły stan techniczny (np. nadmierną korozję), wadliwy montaż, naprawę głównych węzłów nadwozia lub elementów ramy, zwłaszcza stanowiących bazę do mocowania innych układów oraz zespołów i mechanizmów sterowania pojazdem (mechanizm kierowniczy, pompa hamulcowa itd.). Diagnosta wykonuje oględziny pojazdu na stanowisku kontrolnym stacji i tylko w uzasadnionych przypadkach przeprowadza pomiary za pomocą przymiarów liniowych lub sprawdzianów. Na tej podstawie powinien stwierdzić, czy nie występuje istotna niezgodność podstawowych wymiarów nadwozia/ramy (jako bazy do mocowania innych układów) z wymaganiami wytwórcy pojazdu, a szczególnie: rozstawu kół i osi oraz zwisów przedniego i tylnego. Wykaz czynności kontrolnych oraz metod i kryteriów oceny stanu nadwozia (kabiny kierowcy, skrzyni ładunkowej) zawarto w obowiązujących przepisach – rozporządzenie w sprawie zakresu i sposobu przeprowadzania badań technicznych pojazdów oraz wzorów dokumentów stosowanych przy tych badaniach (Dz.U. nr 155 z 2009 r.). W uzasadnionych przypadkach w stacjach kontroli pojazdów należy wykonywać pomiar współczynnika przepuszczalności światła szyb samochodowych. W związku z tym stacje kontroli pojazdów są wyposażone w odpowiedni przyrząd. Przyrząd do badania przepuszczalności światła szyb zbudowany jest z dwóch zasadniczych zespołów: oświetlacza i urządzenia pomiarowego. Oświetlacz składa się ze źródła światła (lampa halogenowa) oraz systemu optycznego (do formowania równoległej wiązki światła). Urządzenie pomiarowe wyposażone jest w detektor promieniowania z systemem optycznym (do rozpraszania strumienia światła), układ pomiarowy i wyświetlacz.
Współczynnik przepuszczalności światła szyb samochodowych należy obliczyć z zależności:
gdzie:
p – współczynnik przepuszczalności światła szyby,
Ф1 – strumień światła wychodzący z powierzchni wyjściowej szyby,
Ф – strumień światła pochodzący od tła,
Ф2 – strumień światła padający na powierzchnię wejściową szyby.
Badanie przepuszczalności światła szyb samochodowych wykonuje się następująco:
- do pomiaru wybrać najbardziej płaską część szyby (szyba czysta i sucha),
- przyrząd należy wyregulować w taki sposób, aby wyświetlacz pokazywał 0% (gdy na detektor nie pada żadne światło) oraz 100% (detektor oświetlony bezpośrednio przez oświetlacz – strumień światła Ф2),
- oświetlacz i detektor należy zamocować po obu stronach szyby w taki sposób, aby ich osie optyczne pokrywały się,
- zmierzyć strumień światła Ф pochodzący od tła,
- włączyć lampę oświetlacza i po odczekaniu około 1 minuty zmierzyć strumień światła Ф1 na powierzchni wyjściowej (wewnętrznej) szyby,
- do kolejnego pomiaru można przystąpić dopiero po zgaszeniu lampy oświetlacza i odczekaniu około 1 minuty (ostygnięcie jej żarnika).
Przepuszczalność światła szyb samochodowych należy uznać za wystarczającą, gdy wynosi nie mniej niż: 75% dla szyb przednich lub 70% dla szyb bocznych przednich. Na rynku dostępne są przyrządy do pomiaru przepuszczalności światła szyb samochodowych różnych wytwórców, np. AMX 710 firmy Automex (fot. 3). Można je stosować do sprawdzania szyb samochodowych podczas okresowych badań technicznych oraz kontroli drogowych.
Pełna kontrola stanu technicznego nadwozia (ramy) pojazdu może być obecnie profesjonalnie wykonana tylko w odpowiednio wyposażonych stacjach obsługi oraz warsztatach samochodowych. Niżej opisano, w sposób bardziej szczegółowy, metody i urządzenia stosowane do kontroli geometrii nadwozia pojazdu. Ocenę stopnia zużycia nadwozia (głównie nasilenia korozji) i sprawdzanie jego szczelności wykonuje się najczęściej organoleptycznie. Do pomiaru grubości powłoki lakierowej stosuje się warstwomierze (fot. 4) wykorzystujące zjawiska indukcji magnetycznej lub prądów wirowych.
Stopień odkształcenia nadwozia z reguły określa się takimi metodami, jak:
- oględziny zewnętrzne,
- kontrola geometrii układu jezdnego (ustawienia kół i osi),
- pomiary po przekątnej,
- pomiary kontrolne na zgodność wymiarów,
- pomiary kontrolne przestrzenne.
Oględziny zewnętrzne pozwalają na wstępną ocenę stopnia deformacji elementów nadwozia (ramy). Kontrola geometrii układu jezdnego na ogół dotyczy sprawdzenia ustawienia kół oraz równoległości osi i przesunięcia osi. Pomiary po przekątnej polegają na sprawdzeniu i porównaniu odległości między charakterystycznymi punktami płyty podłogowej, ramy lub szkieletu nadwozia (kabiny). Korzysta się przy tym z faktu, że przekątne mają jednakową długość. Metoda nie zapewnia odpowiedniej dokładności podczas ustalania odkształceń pionowych płyty podłogowej. Pomiary kontrolne na zgodność wymiarów obejmują sprawdzenie odległości między punktami kontrolnymi nadwozia i porównanie wyników z wartościami podanymi w dokumentacji technicznej pojazdu (karta pomiarowa, schemat płyty podłogowej lub bryły nadwozia z zaznaczonymi wymiarami). Do takiej kontroli wykorzystuje się na ogół przyrządy miernicze mechaniczne (przymiary, drążki teleskopowe i cyrkle blacharskie). Są to najtańsze przyrządy umożliwiające wykonanie pomiarów geometrii nadwozia, ale mogą być stosowane tylko przy niewielkich uszkodzeniach. Pomiar geometrii całego nadwozia byłby mało dokładny i trudny do przeprowadzenia. Przykładami takich przyrządów są teleskop pomiarowy firmy Wieländer+Schill (fot. 5) i przymiar blacharski firmy Herkules.
Obecnie na rynku dostępne są również cyrkle elektroniczne, takie jak: Intelli-Tape firmy Chief lub EzCalipre firmy Autorobot. Są to urządzenia przenośne i bardzo poręczne. Mieszczą się w jednym futerale, można je przewozić w samochodzie i są szczególnie przydatne dla rzeczoznawców samochodowych. Niżej przedstawiono przykładowo elektroniczny cyrkiel blacharski EzCalipre. Jest to zaawansowany technicznie przyrząd do dokładnych dwu- i trójwymiarowych pomiarów nadwozia i podwozia pojazdu oraz do dokumentowania wyników badań. Przeznaczony jest do wykonywania pomiarów w samochodach osobowych, dostawczych i terenowych. Zasilanie bateryjne zapewnia mobilność i możliwość stosowania w różnych miejscach i warunkach. Podstawowe zespoły tego przyrządu przedstawiono na fot. 6, a sposób wykonywania pomiaru na fot. 7.
Cyrkiel został wyposażony w wyświetlacz, na którym można obserwować położenie danego punktu kontrolnego. Zmierzone dane są przesyłane (połączenie bezprzewodowe) do programu sterującego w komputerze i na ekranie monitora można porównać aktualne oraz wymagane przez wytwórców położenie punktów kontrolnych. Podawane są również różnice pomiędzy obiema wartościami. Wyniki pomiarów zapisane w pamięci komputera mogą być wydrukowane w raporcie z badań. Przyrząd jest dostarczany razem z potrzebną dokumentacją techniczną. Baza danych zawiera około 60 punktów pomiarowych dla jednego modelu samochodu. Umożliwia to sprawdzenie stanu całej bryły pojazdu. Za pomocą urządzenia można zmierzyć długość i szerokość (pomiary symetryczne, pomiary po przekątnej) oraz odczytać różnice wysokości położenia punktów kontrolnych. Zarówno kalibrację systemu, jak i pomiary można wykonać dla pojazdu ustawionego na stanowisku kanałowym, na podnośniku lub na płaskiej posadzce.
Do sprawdzania kształtu geometrycznego nadwozia za pomocą pomiarów kontrolnych przestrzennych stosuje się: sprawdziany, szablony lub systemy pomiarowe ram do naprawy nadwozi. Sprawdziany odwzorowują (za pomocą uchwytów bazowych) położenie charakterystycznych punktów płyty podłogowej. Szablony pozwalają na sprawdzanie bryły nadwozia (odwzorowują kształt otworów i pokryw w nadwoziu). Ramy kontrolno-pomiarowe są elementem wyposażenia urządzeń do prostowania nadwozi podczas naprawy.
W przypadku, gdy struktura nadwozia ulegnie odkształceniom (niewłaściwa eksploatacja, kolizja, wypadek), przywrócenie właściwego kształtu i wytrzymałości bryle nadwozia wymaga zastosowania odpowiednich stanowisk naprawczych. Takie stanowiska wyposaża się w specjalne urządzenia naprawcze oraz w przyrządy kontrolno-pomiarowe, które są w stanie określić prawidłowość geometrii bryły nadwozia (zgodność z wymaganiami ustalonymi przez wytwórcę). Określenie faktycznego stanu przestrzennej bryły nadwozia jest możliwe po wykonaniu pomiarów charakterystycznych punktów nadwozia, których rozmieszczenie podawane jest w specjalistycznych danych technicznych pojazdu (karty pomiarowe, schematyczne rysunki płyty podłogowej lub bryły nadwozia). Wyniki dokonanych pomiarów porównuje się z danymi technicznymi pojazdu, aby ustalić miejsca i wielkość ewentualnych odkształceń bryły nadwozia. Punktami pomiarowymi nadwozia są najczęściej otwory konstrukcyjne lub technologiczne, śruby mocujące oraz nakrętki.
Układem odniesienia jest opisany na nadwoziu abstrakcyjny prostopadłościan, którego podstawa przebiega równolegle do podłogi pojazdu, a dłuższe ściany biegną równolegle do wzdłużnej płaszczyzny symetrii. W stosunku do tak wyznaczonej bazy (trzech wymiarów) można prowadzić pomiar różnymi systemami pomiarowymi. Do dokładnych pomiarów geometrii nadwozia stosuje się mechaniczne systemy pomiarowe lub elektroniczne (komputerowe) systemy pomiarowe.
Urządzenia mechaniczne umożliwiają pomiar długości, szerokości i wysokości na jakiej usytuowane są punkty kontrolne. W trakcie wykonywania pomiarów powinno się porównywać rzeczywiste położenie punktów z informacjami zawartymi w kartach pomiarowych. Mechaniczne systemy pomiarowe wytwarzane są przez różnych producentów i mają podobną budowę. Podstawowymi elementami tych urządzeń są (fot. 8):
- prowadnica ze skalą, która służy do wykonania pomiarów równolegle do wzdłużnej osi symetrii płyty podłogowej,
- poprzeczne suporty (przesuwane), dzięki którym można dokonywać pomiarów poprzecznych płyty podłogowej,
- komplet wymiennych trzpieni do pomiarów wysokości płyty podłogowej,
- bramka pomiarowa (składana), która jest używana podczas pomiarów górnych części nadwozia.
Urządzenia z mechanicznymi systemami pomiarowymi produkowane są między innymi przez takie firmy, jak: Autorobot (mechaniczne trójwymiarowe urządzenie pomiarowe), Blackhawk (P-188 mk2), Car-O-Liner (Car-O-Mech), Celette (Metro 2000), Herkules (Compact).
Najczęściej spotykane elektroniczne (komputerowe) systemy pomiarowe różnią od mechanicznych następujące możliwości: automatyczne porównywanie zmierzonych wartości z danymi zawartymi w programie komputerowym, wykonywanie analizy wyników oraz możliwość wydruku dokumentacji (protokołu z badań). Urządzenia komputerowe składają się z części mechanicznej (o konstrukcji podobnej do mechanicznych urządzeń pomiarowych) i części elektronicznej, służącej do zamiany wartości przemieszczeń czujników pomiarowych na sygnały elektryczne. Impulsy elektryczne przesyłane są do komputera, który je przetwarza i wyświetla na monitorze w postaci przestrzennych parametrów zmierzonych punktów kontrolnych. Wyniki pomiarów są następnie odpowiednio zestawiane oraz porównywane z danymi nominalnymi określonymi przez producenta. Urządzenia elektroniczne (komputerowe) dzieli się na dwie grupy: wielopunktowe oraz jednopunktowe. Podczas pomiarów systemami wielopunktowymi, na przykład Shark firmy Blackhawk lub Genesis 2 (wersja Velocity i Vector) firmy Chief, można śledzić jednocześnie położenie kilku lub kilkunastu punktów kontrolnych, co jest bardzo przydatne podczas naprawy blacharskiej nadwozia. Natomiast w systemach jednopunktowych można w danym momencie obserwować położenie tylko jednego punktu pomiarowego. Jednopunktowe systemy pomiarowe oferowane są między innymi przez takie firmy, jak: Autorobot (Calipre), Car Bench (Contact), Car-O-Liner (Car-O-Tronic), Celette (Naja), Spanesi (Touch). Ze względu na zastosowaną metodę pomiarową urządzenia elektroniczne (komputerowe) można podzielić na:
- mechaniczno-elektroniczne,
- laserowo-elektroniczne,
- ultradźwiękowo-elektroniczne.
Urządzenia z systemem pomiarowym mechaniczno-elektronicznym są łatwe w użyciu, a nakład pracy podczas ich montażu i demontażu jest stosunkowo niewielki. Taki system pomiarowy charakteryzuje się znaczną odpornością na zakłócenia zewnętrzne, stosunkowo prostą konstrukcją oraz nadaje się do prowadzenia pomiarów diagnostycznych również bez ramy naprawczej. Tę metodę pomiarową zastosowano między innymi w urządzeniach: Calipre firmy Autorobot, Car-O-Tronic firmy Car-O-Liner, Naja firmy Celette oraz Master Liner 2 firmy Herkules. Interesującym rozwiązaniem jest urządzenie Calipre (fot. 9) wytwarzane przez Autorobot. Oprócz płyty podłogowej pozwala na precyzyjny pomiar górnych części nadwozia pojazdu i przestrzeni pasażerskiej. Wykorzystuje się do tego przesuwną bramkę pomiarową, która jest sprzęgnięta elektronicznie z wysięgnikami pomiarowymi. Urządzenie Calipre jest także wyposażone w głowicę pomiarową służącą do pomiarów punktów kontrolnych płyty podłogowej. Niżej przedstawiono, na przykładzie urządzenia Car-O-Tronic (fot. 10), budowę oraz zasadę działania takich systemów pomiarowych. Istotnym elementem urządzenia jest ramię pomiarowe przeznaczone do pomiarów (w układzie trzech współrzędnych) kątów pomiędzy przegubowo połączonymi segmentami tego ramienia. Konieczne wymiary obliczane są z trygonometrycznych funkcji cosinusów tych kątów przez odpowiednie oprogramowanie komputera. Podstawę ramienia pomiarowego można przesuwać wzdłuż pojazdu po prowadnicach. Ponadto, ramię może wykonywać ruchy obrotowe, a trzpień pomiarowy można przemieszczać w pionie i w poziomie. Z głowicy pomiarowej sygnały informacyjne są przesyłane (za pomocą fal radiowych lub promieniowania podczerwonego) do komputera. Odpowiedni program wykonuje niezbędne obliczenia, pokazuje wyniki pomiarów na ekranie monitora i zapisuje w formie elektronicznej. Należy dodać, że urządzenia mechaniczno-elektroniczne nie wymagają wykonywania czynności związanych z tradycyjną kalibracją. Po wykonaniu pomiaru trzech nieodkształconych punktów kontrolnych następuje samokalibracja systemu względem mierzonego nadwozia.
Jednym z urządzeń służących do pomiarów geometrii nadwozia jest laserowo- -elektroniczny system Genesis 2 firmy Chief (fot. 11). W celu przeprowadzenia pomiaru w odpowiednich punktach płyty podłogowej należy umieścić sondy pomiarowe z naniesionym kodem kreskowym. Natomiast pod płytą podłogową, w środkowej jej części, ustawia się skaner z dwiema głowicami emitujący promieniowanie laserowe wokół stanowiska pomiarowego. W trakcie pomiaru skaner identyfikuje poszczególne punkty kontrolne i określa ich dokładne położenie. Innym przykładem komputerowego urządzenia służącego do pomiarów geometrii nadwozia jest ultradźwiękowo-elektroniczny system Shark (fot. 12) wytwarzany przez firmę Blackhawk. To urządzenie wykorzystuje ultradźwięki, które są wysyłane przez sondy, a odbierane przez mikrofony usytuowane w głównej belce pomiarowej połączonej z komputerem. Mierzony jest czas przesyłania sygnału między sondą a belką. Wyniki pomiarów po przetworzeniu na impulsy elektryczne przesyłane są do komputera, który je porównuje z danymi technicznymi badanego pojazdu. Na ekranie monitora pokazywane są dane o stanie geometrii nadwozia. Możliwa jest jednoczesna obserwacja i kontrola położenia kilkunastu punktów pomiarowych. Niektórzy wytwórcy sprzętu pomiarowego oferują połączone systemy pomiarowe do kontroli odkształcenia płyty podłogowej nadwozia (ramy) oraz badania geometrii układu jezdnego (kątów ustawienia kół i osi) zarówno samochodów osobowych, jak i ciężarowych. Takie urządzenia są szczególnie przydatne dla stacji diagnostycznych (do kontroli pojazdu po wypadku i przed dopuszczeniem do ruchu).
Określenie stopnia deformacji ramy (w samochodach ciężarowych) jest możliwe po wykonaniu pomiarów charakterystycznych punktów kontrolnych. Każda rama ma oznaczone przez producenta typowe punkty charakterystyczne (otwory konstrukcyjne, otwory technologiczne i inne), których rozmieszczenie podawane jest w specjalistycznych danych technicznych pojazdu, np. kartach pomiarowych. Wyniki dokonanych pomiarów porównuje się z danymi technicznymi pojazdu, co pozwala ustalić miejsca i stopień ewentualnych odkształceń ramy. Układem odniesienia jest najczęściej płaszczyzna symetrii ramy, do której przyporządkowane są wymiary w płaszczyźnie poziomej. Po wykonaniu pomiarów w tej płaszczyźnie określa się pozostałe wymiary kontrolne. Bazą jest również abstrakcyjny prostopadłościan, którego podstawa jest równoległa do płaszczyzny ramy, a dłuższe ściany są równoległe do wzdłużnej płaszczyzny symetrii. Pomiar odnoszony do tak wyznaczonej bazy (w układzie trzech współrzędnych) można prowadzić różnymi przyrządami (systemami pomiarowymi).
Znanymi producentami urządzeń do pomiaru i naprawy ram są między innymi szwedzka firma Josam i wymieniona wcześniej firma Blackhawk.
dr inż. Kazimierz Sitek
Komentarze (2)