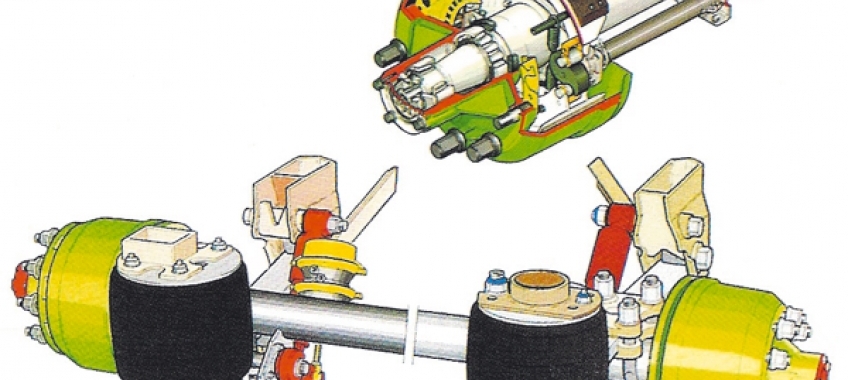
Układ hamulcowy samochodu powinien wytworzyć na osiach kół jezdnych momenty hamujące, umożliwiające w sposób kontrolowany przez kierowcę zmniejszenie prędkości jazdy, a także unieruchomienie pojazdu na postoju. Każdy układ hamulcowy, niezależnie od jego przeznaczenia i rozwiązania konstrukcyjnego, można podzielić na mechanizmy hamulcowe i mechanizmy sterujące (uruchamiające) hamulcami. Cierne mechanizmy hamulcowe wytwarzają momenty hamujące wskutek tarcia odpowiednich powierzchni współpracujących elementów, z których jedne są związane kinematycznie z kołami jezdnymi, a drugie z nieruchomymi obrotowo elementami podwozia. Zadaniem mechanizmu sterującego jest przenoszenie oraz zwielokrotnienie siły nacisku z pedału hamulca lub dźwigni (w przypadku uruchamiania ręcznego) do mechanizmu hamulcowego. Mechanizm sterujący hamulcami powinien:
- umożliwić uzyskanie dużych przełożeń siłowych;
- zapewnić proporcjonalność siły działającej na mechanizm hamulcowy w stosunku do siły wywieranej przez kierowcę na pedał hamulca (umożliwia to kierowcy panowanie nad przebiegiem hamowania);
- zapewnić założony rozkład sił hamowania na kołach poszczególnych osi pojazdu, co umożliwia pełniejsze wykorzystanie przyczepności opon do jezdni w zależności od rozkładu obciążeń osi;
- zapewnić możliwie najkrótszy czas przenoszenia siły od pedału hamulca do mechanizmów hamulcowych.
Analiza rozwiązań konstrukcyjnych układów hamulcowych stosowanych we współczesnych pojazdach samochodowych pozwala stwierdzić, że w przypadku:
- mechanizmów hamulcowych – powszechnie stosuje się hamulce tarczowe oraz szczękowo-bębnowe. W ostatnich latach, ze względu na liczne zalety, hamulce tarczowe poza samochodami osobowymi są coraz szerzej stosowane również w samochodach ciężarowych, autobusach, przyczepach i naczepach;
- mechanizmów sterujących hamulcami – powszechnie stosuje się hydrauliczne mechanizmy sterujące w samochodach osobowych i dostawczych. Natomiast w samochodach ciężarowych, autobusach, przyczepach oraz naczepach najbardziej rozpowszechnione są pneumatyczne mechanizmy sterujące hamulcami. W nowych odmianach samochodów ciężarowych i autobusów zostały wprowadzone elektropneumatyczne mechanizmy sterujące w celu skrócenia czasu reakcji hamulców oraz ułatwienia współpracy z układami przeciwblokującymi ABS i przeciwpoślizgowymi ASR.
Układ hamulcowy należy do tych układów pojazdu samochodowego, które mają bezpośredni wpływ na bezpieczeństwo. Jednym z podstawowych warunków bezpieczeństwa ruchu drogowego jest panowanie kierowcy w każdej chwili nad prędkością jazdy (obok panowania nad kierunkiem jazdy). Z tego powodu stan techniczny układu hamulcowego pojazdu dopuszczonego do ruchu po drogach publicznych nie może budzić zastrzeżeń. Dlatego wymagania dotyczące układów hamulcowych zostały określone w odpowiednich aktach prawnych.
1. Rodzaje i zadania układów hamulcowych
Zgodnie z kryterium funkcjonalności, w pojazdach samochodowych stosuje się następujące rodzaje hamulców:
- robocze (zasadnicze), które umożliwiają kierowcy zmniejszanie prędkości pojazdu lub jego zatrzymanie;
- awaryjne (pomocnicze), uruchamiane w sposób niezależny, w przypadku awarii roboczych;
- postojowe, służące do utrzymywania samochodu w spoczynku, także na wzniesieniu, a w szczególności w czasie nieobecności kierowcy;
- dodatkowe (zwalniacze), które pozwalają kierowcy na utrzymywanie stałej prędkości ruchu samochodu lub jej zmniejszenie, szczególnie na długim spadku drogi.
Wymienione hamulce muszą działać niezależnie, jednak niektóre z nich mogą być konstrukcyjnie zintegrowane i wykorzystywać te same mechanizmy. Układ roboczy i awaryjny oraz awaryjny i postojowy mogą mieć wspólne sterowanie, natomiast niedopuszczalne jest wspólne sterowanie hamulca roboczego i postojowego. Cechy konstrukcyjne mechanizmów hamulcowych i sterujących stanowią podstawowe kryteria identyfikacyjne układów hamulcowych danego typu pojazdu. Hamulce robocze działają na wszystkie koła pojazdu i są tak skonstruowane, że kierowca stale ma możliwość regulowania chwilowej skuteczności ich działania. Są one uruchamiane za pomocą pedału i działają tylko podczas wywierania nacisku na ten pedał. Hamulce robocze są przystosowane do hamowania z możliwie dużą skutecznością, lecz w krótkim czasie. Hamulce awaryjne są uruchamiane niezależnie od hamulca roboczego i są przeznaczone do zatrzymywania pojazdu w razie awarii hamulca roboczego. Hamulec awaryjny działa podczas wywierania nacisku na jego mechanizm uruchamiający. W stosowanych obecnie dwuobwodowych układach hamulcowych za hamulec awaryjny uważa się każdy z obwodów, na które jest podzielony roboczy układ hamulcowy. Każda z części podzielonego w ten sposób roboczego układu hamulcowego powinna działać niezależnie i zapewniać uzyskanie dostatecznej skuteczności hamowania w przypadku awarii drugiej części. Hamulec postojowy służy do utrzymywania pojazdu w spoczynku na drodze płaskiej lub pochyłej. Hamulec ten jest uruchamiany ręcznie z miejsca kierowcy (z wyjątkiem przyczep i naczep), niezależnie od hamulca roboczego i działa bez konieczności wywierania trwałego nacisku na dźwignię.
W wielu pojazdach ciężarowych i autobusach stosuje się hamulce dodatkowe (zwalniacze), to znaczy urządzenia przystosowane do długotrwałej pracy, lecz hamujące z umiarkowaną skutecznością. Zwalniaczy używa się na przykład podczas zjeżdżania po dłuższym odcinku pochyłej drogi, gdy zachodzi obawa, że długotrwałe hamowanie hamulcami roboczymi mogłoby spowodować ich uszkodzenie wskutek przegrzania. Układy hamulcowe powinny odznaczać się niezawodnością, dużą skutecznością działania oraz powinny zapewniać taki rozdział sił hamowania, aby proces hamowania nie powodował utraty stateczności pojazdu. Ponadto, układ hamulcowy powinien być łatwy w obsłudze, a wysiłek kierowcy związany z jego uruchomieniem powinien być jak najmniejszy. Dlatego w układach hamulcowych pojazdów stosuje się urządzenia wspomagające, automatyczne korektory siły hamowania osi zależne od ich obciążenia, a także urządzenia przeciwblokujące ABS.
2. Rozwiązania konstrukcyjne układów hamulcowych
Układ hamulcowy jest jednym z głównych układów samochodu i ma decydujący wpływ na bezpieczeństwo ruchu drogowego. Układem hamulcowym nazywamy zespół mechanizmów umożliwiających zmniejszenie prędkości jazdy oraz zatrzymanie pojazdu samochodowego. Układ ten składa się z dwóch grup zespołów:
- mechanizmów hamulcowych;
- mechanizmów sterujących (uruchamiających) hamulcami.
Oddzielną konstrukcyjnie grupę stanowią zwalniacze, które mogą być silnikowe lub podwoziowe. Wśród zwalniaczy podwoziowych wyróżnia się dwie odmiany konstrukcyjne: zwalniacze hydrodynamiczne lub elektromagnetyczne.
2.1. Mechanizmy hamulcowe
Mechanizmy hamulcowe są bezpośrednio związane z kołami jezdnymi i służą do wytworzenia momentu tarcia w hamulcach. Pod względem konstrukcyjnym mechanizmy hamulcowe dzieli się na:
- szczękowo-bębnowe,
- tarczowe,
- taśmowe.
W hamulcach szczękowo-bębnowych moment hamowania powstaje wskutek tarcia wewnętrznej powierzchni obracającego się wraz z kołem bębna hamulcowego o umieszczone wewnątrz bębna nieobracające się szczęki (rys. 1). Szczęki te dociskane są do bębna rozpieraczem, sterowanym przez kierowcę za pomocą mechanizmu uruchamiającego. Z chwilą, gdy kierowca przestaje wywierać nacisk na pedał, rozpieracz przestaje naciskać na szczęki i sprężyna odciągająca powoduje ściągnięcie szczęk do położenia, w którym przestają one trzeć o bęben. Szczęki hamulcowe mają okładziny cierne, odznaczające się dużym współczynnikiem tarcia oraz znaczną odpornością na ścieranie. Elementem przenoszącym moment hamowania ze szczęk na elementy nośne pojazdu jest tarcza hamulcowa. W obecnie produkowanych samochodach z reguły stosuje się urządzenia do samoczynnej regulacji luzu między szczękami a bębnem.
W hamulcach tarczowych moment tarcia powstaje wskutek dociskania elementów ciernych (tzw. klocków) do płaskich powierzchni tarczy wirującej wraz z kołem (rys. 2). Zacisk z elementami ciernymi jest mocowany do mechanizmów nośnych pojazdu. W hamulcach sterowanych hydraulicznie docisk klocków uzyskuje się za pomocą umieszczonego w zacisku siłownika (jednego lub kilku) w postaci cylinderka z tłoczkiem. Warunkiem prawidłowej pracy hamulca tarczowego jest zachowanie odpowiednio małego luzu pomiędzy klockami ciernymi a tarczą. Ze względu na duże naciski, szybkie zużywanie się okładzin i bardzo małe wartości stosowanego luzu właściwe działanie hamulca tarczowego bez automatycznej regulacji luzu byłoby niemożliwe.
W ostatnich latach hamulce tarczowe coraz szerzej są stosowane również w samochodach ciężarowych i autobusach. Od hamulców samochodów osobowych różnią się konstrukcją zacisku, który musi być uruchamiany siłownikiem pneumatycznym. Zamiana postępowego ruchu tłoka na przesuw wkładek ciernych następuje w mechanizmie mimośrodowym. W celu zmniejszenia siły tarcia pomiędzy pierścieniem mimośrodowym a gniazdem i popychaczem zacisku hamulca, wprowadza się łożyska igiełkowe. Duże jednostkowe naciski powierzchniowe powodują silne nagrzewanie się hamulców tarczowych i konieczność skutecznego ich chłodzenia. W przypadku bardziej obciążonych hamulców tarczowych stosuje się tzw. tarcze wentylowane.
W porównaniu z hamulcami szczękowo--bębnowymi hamulce tarczowe mają następujące zalety:
- korzystniejszy rozkład nacisków na powierzchni przylegania elementów ciernych do tarczy (równomierniej zużywają się klocki cierne);
- możliwość stosowania większych nacisków jednostkowych (większa skuteczność hamulców);
- dobre warunki chłodzenia;
- łatwiejsza regulacja luzów i wymiana elementów ciernych;
- mniejszy moment bezwładności mas wirujących.
2.2. Mechanizmy sterujące hamulcami
We współczesnych pojazdach samochodowych stosuje się następujące rodzaje mechanizmów sterujących (uruchamiających) hamulcami:
- mechaniczne,
- hydrauliczne,
- pneumatyczne,
- elektropneumatyczne.
W niektórych pojazdach samochodowych występują mechanizmy uruchamiające hamulce mieszane (np. hydropneumatyczne).
Hydrauliczne mechanizmy sterujące hamulcami znalazły zastosowanie w roboczych układach hamulcowych samochodów osobowych, osobowo-terenowych, dostawczych i lżejszych ciężarowych. Siła nacisku na pedał jest przenoszona do mechanizmów hamulcowych za pośrednictwem cieczy (płynu hamulcowego). Podstawowe elementy takiego mechanizmu uruchamiającego to dwusekcyjna główna pompa hamulcowa, siłowniki hydrauliczne w mechanizmach hamulcowych kół oraz sztywne i elastyczne przewody hamulcowe, łączące pompę z siłownikami (rys. 3). Wywieranie nacisku na pedał hamulca powoduje przesunięcie tłoków pompy głównej, wzrost ciśnienia w przewodach i uruchomienie siłowników (cylinderków), które dosuwają klocki do tarcz w hamulcach tarczowych lub szczęki do bębnów w hamulcach bębnowych. Po zwolnieniu pedału hamulca tłoki pompy wracają do położenia początkowego, ciśnienie w układzie spada, co sprawia, że sprężyny powrotne mogą odsunąć szczęki od bębnów (w hamulcach bębnowych), a elastyczne pierścienie uszczelniające – klocki cierne (w hamulcach tarczowych). Wypchnięty z siłowników płyn hamulcowy powraca do pompy. Ze względu na duże ciśnienie robocze (8÷10 MPa), wymiary pompy głównej i siłowników mechanizmów hamulcowych są niewielkie. W obwodzie hamulców tylnych kół zwykle występują korektory siły hamowania. W samochodach z hydraulicznymi mechanizmami uruchamiającymi często stosuje się urządzenia wspomagające, których zadaniem jest zwiększenie skuteczności hamowania i zmniejszenie wysiłku kierowcy. Powszechnie są stosowane urządzenia przeciwblokujące ABS.
Pneumatyczne mechanizmy sterujące hamulcami stosuje się w samochodach ciężarowych średniej i dużej ładowności, autobusach oraz przyczepach i naczepach, a więc w pojazdach wymagających znacznych sił hamowania, niemożliwych do uzyskania przy zastosowaniu hydraulicznych mechanizmów uruchamiających. W układach pneumatycznych siła z jaką kierowca naciska na pedał hamulca służy do sterowania czynnikiem roboczym (sprężonym powietrzem), który doprowadzony do siłowników wykonuje pracę potrzebną do dociśnięcia elementów ciernych. Siła z jaką kierowca naciska na pedał zależy od sztywności sprężyny w zaworze sterującym, natomiast siła w rozpieraczach zależy od ciśnienia w instalacji oraz wymiarów siłownika. Rozwiązanie takie umożliwia uzyskanie dużych sił hamowania przy małym wysiłku kierowcy. Pneumatyczne mechanizmy uruchamiające cechują się mniejszą wrażliwością na nieszczelność oraz większą niezawodnością działania. Jest też możliwość wykorzystania nadciśnieniowej instalacji pneumatycznej do napędu urządzeń pomocniczych. W przypadku przyłączenia urządzeń pomocniczych należy je zasilać z osobnych zbiorników, połączonych z układem hamulcowym tak, aby nawet w czasie awarii nie wpłynęło to niekorzystnie na sprawność układu hamulcowego. Ważną zaletą układów pneumatycznych jest dogodna możliwość podłączenia układu hamulcowego przyczepy (naczepy) do układu hamulcowego pojazdu ciągnącego. Wadą pneumatycznych układów hamulcowych jest dość długi czas uruchamiania hamulców (czas reakcji), szczególnie w siłownikach bardziej oddalonych od głównego zaworu hamulcowego.
Zgodnie z obowiązującymi przepisami pneumatyczne mechanizmy uruchamiające powinny być dwuobwodowe, natomiast sposób połączenia pojazdu silnikowego z przyczepą lub naczepą powinien być dwuprzewodowy. Na rys. 4 pokazano przykładowo schemat pneumatycznego mechanizmu sterującego hamulcami, przystosowanego do współpracy z przyczepą (dwuobwodowy, dwuprzewodowy, z układem ABS/ASR). Składa się z następujących obwodów funkcjonalnych:
- zasilania sprężonym powietrzem,
- hamulca roboczego,
- hamulca awaryjnego i postojowego,
- hamulca dodatkowego (zwalniacza),
- sterowania hamulcami przyczepy,
- ABS/ASR.
Urządzenia przeciwblokujące ABS i przeciwpoślizgowe ASR stosuje się również w samochodach ciężarowych i autobusach, które mają pneumatyczną instalację uruchamiania hamulców. Do głównych zespołów systemu ABS należą: elektroniczny moduł sterujący, czujniki prędkości obrotowej kół jezdnych i elektropneumatyczne modulatory ciśnienia powietrza w siłownikach. Dodatkowo, mogą występować odrębne moduły kontroli i sygnalizacji. Celem działania urządzenia ABS jest zapobieganie blokowaniu (ściślej nadmiernemu poślizgowi) kół podczas hamowania. Urządzenie przeciwblokujące tak reguluje ciśnienie w siłownikach hamulcowych poszczególnych kół, aby ich poślizg podczas hamowania utrzymywał się w obszarze występowania największej przyczepności ogumienia. Zwykle taki stan jest osiągany przy poślizgu obwodowym koła wynoszącym 20-30%. Elektropneumatyczne mechanizmy sterowania hamulcami EBS pojawiły się w pojazdach użytkowych w ostatnich latach ubiegłego wieku. Zostały wprowadzone w celu skrócenia czasu uruchamiania (reakcji) mechanizmów hamulcowych. Układy EBS dają duże możliwości regulacji siły hamowania i ułatwiają współpracę z układami zapobiegającymi blokowaniu kół (ABS) podczas hamowania oraz układami zapobiegającymi poślizgowi kół (ASR) podczas rozpędzania.
Rozmieszczenie podstawowych zespołów elektropneumatycznego układu sterowania hamulców EBS firmy Wabco w ciągniku siodłowym pokazano na rys. 5. Elektropneumatyczny mechanizm sterowania hamulców EBS został zbudowany z wykorzystaniem wielu elementów dotychczasowej instalacji pneumatycznej pojazdu. Powstał układ hamulcowy o dwóch obwodach pneumatycznych z nadrzędnym elektronicznym układem sterującym. Pneumatyczna instalacja hamulcowa w tym zestawieniu pełni funkcję układu rezerwowego, w którym zastosowano przewody powietrzne o mniejszych średnicach i pominięto wiele urządzeń (niektóre zawory, korektor siły hamowania i inne). Zadania pominiętych zespołów pneumatycznych zostały przejęte przez elektroniczny sterownik układu hamulcowego i zawory elektropneumatyczne.
Kierowca naciskając nogą na pedał hamulca oddziałuje na potencjometr elektronicznego zaworu hamulcowego, który pełni rolę głównego zaworu sterującego względem elektronicznego sterownika EBS systemu. Moduł sterujący (sterownik) EBS odpowiada za przebieg procesu hamowania i współpracuje z urządzeniami przeciwblokującym ABS oraz przeciwpoślizgowym ASR. Na podstawie sygnału elektrycznego, nadanego od elektronicznego zaworu hamulcowego do sterownika EBS, następuje wygenerowanie przez ten sterownik sygnałów elektrycznych do elektropneumatycznych zaworów (tzw. modulatorów ciśnienia). Modulatory są to zespoły wyposażone w zawory sterowane elektromagnetycznie przez sygnały nadawane z procesora sterownika. Otwierają one przepływ sprężonego powietrza oraz wpływają na wartość ciśnienia powietrza przepływającego do siłowników hamulcowych kół przednich i tylnych oraz do zaworu sterującego hamulce przyczepy. Jednocześnie informacja o przebiegu procesu hamowania, przez magistralę sterującą CAN może być kierowana do sterowników silnika i skrzyni biegów w celu zmiany stanu ich pracy, stosownie do przebiegu procesu hamowania. Sterownik EBS współpracuje również z systemem sterowania zawieszenia powietrznego ECAS oraz sterowania zwalniaczem.
Sterownik EBS na podstawie analizy nacisku kierowcy na pedał hamulca oraz sygnałów z czujników prędkości obrotowej kół jezdnych i od sił w urządzeniu sprzęgającym przyczepy (złącze elektryczne EBS), określa wartość opóźnienia hamowania. Stosownie do obliczonej wartości opóźnienia hamowania sterownik EBS może spowodować tylko uruchomienie zwalniacza lub także siłowników hamulca roboczego kół jezdnych. Przez cały okres hamowania sterownik EBS analizuje sygnały nadawane przez czujniki prędkości obrotowej kół i ciśnienia w miechach zawieszenia pneumatycznego (od systemu ECAS). Informacja o aktualnej prędkości obrotowej kół jezdnych pozwala na utrzymanie efektywnej współpracy EBS z urządzeniem ABS. Natomiast informacja o zmianach ciśnienia w miechach zawieszenia pozwala w sterowniku EBS ustalić przebieg zmian nacisku na drogę podczas hamowania i stosownie do tego korygować wartość ciśnienia w siłownikach hamulcowych poszczególnych kół. Zatem informacja od systemu ECAS umożliwia dostosowanie chwilowych wartości ciśnienia w siłownikach do nacisku kół na drogę i spełnia część zadań tradycyjnego korektora siły hamowania. W przypadku awarii sterowania elektrycznego, pojazd może być hamowany za pomocą działającego układu pneumatycznego. Przykładowy schemat elektropneumatycznego układu sterowania hamulcami firmy Knorr-Bremse dla pojazdu ciągnącego (silnikowego) przedstawiono na rys. 6.
3. Zakres diagnozowania
Skuteczne oraz niezawodne działanie układów hamulcowych pojazdów samochodowych stanowi podstawę ich bezpiecznego użytkowania. Wynikające z zasad działania hamulców ciernych procesy zużycia elementów układu wpływają niekorzystnie na możliwość realizacji zadań i wymagania stawiane układom hamulcowym. Wobec tego niezbędne jest przeprowadzanie systematycznych kontroli działania hamulców. Kontrole takie są realizowane metodami diagnostycznymi, w ramach okresowych badań technicznych pojazdów. Diagnostyczne metody badań układów hamulcowych zależą od przeznaczenia i rozwiązań konstrukcyjnych tych układów, przy czym zasadnicze znaczenie ma sposób uruchamiania mechanizmów hamulcowych. W praktyce diagnozowanie układów hamulcowych pojazdów można podzielić na:
- diagnozowanie mechanizmów uruchamiających hamulce,
- określanie skuteczności i równomierności działania układu hamulcowego.
Zakres i sposoby diagnozowania poszczególnych rodzajów mechanizmów uruchamiających są zasadniczo odmienne, natomiast ocena skuteczności oraz równomierności działania hamulców jest taka sama dla wszystkich rodzajów układów hamulcowych pojazdów.
Warunkiem niezbędnym do poprawnego wykonania diagnozowania układu hamulcowego pojazdu jest identyfikacja cech konstrukcyjnych tego układu (znajomość jego budowy). Określanie stanu technicznego układu hamulcowego pojazdu samochodowego wymaga także znajomości metod diagnozowania, parametrów diagnostycznych i kryteriów oceny stanu technicznego oraz urządzeń diagnostycznych stosowanych na stacjach kontroli pojazdów. W grupie urządzeń stanowiskowych szczególną rolę odgrywają urządzenia do oceny skuteczności i równomierności działania hamulców: stanowiska rolkowe i stanowiska płytowe do pomiaru sił hamowania na kołach. W urzędowych stacjach kontroli pojazdów najbardziej rozpowszechnione są urządzenia rolkowe do badania skuteczności działania hamulców metodą quasistatyczną. Ogólna budowa i zasada działania urządzeń rolkowych różnych producentów jest podobna, natomiast poszczególne rozwiązania różnią się szczegółami konstrukcyjnymi. W ostatnich latach nastąpił znaczny postęp w konstrukcji urządzeń do badania układów hamulcowych pojazdów samochodowych. W szczególności dotyczy to nowej generacji stanowisk rolkowych, najnowszych rozwiązań przyrządów do badania opóźnienia hamowania i układów przeciwblokujących oraz skomputeryzowanych urządzeń do badania powietrznych układów hamulcowych.
dr inż. Kazimierz Sitek
Literatura: 1. Orzełowski S.: Budowa podwozi i nadwozi samochodowych. WSiP. Warszawa 2002.
Komentarze (0)