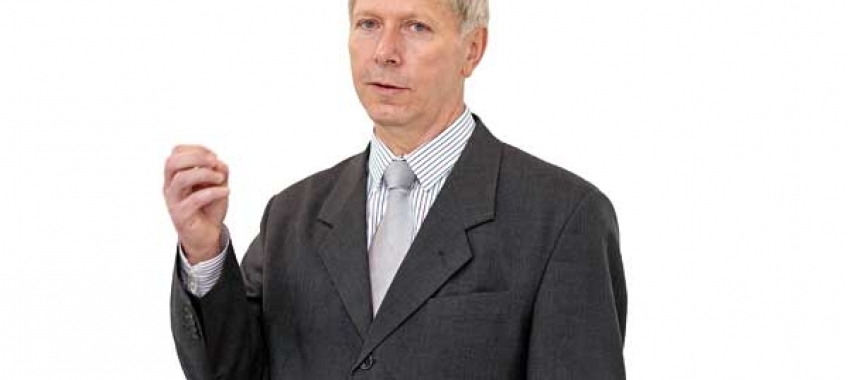
Warunkiem wyjściowym prawidłowej obsługi i prawidłowego diagnozowania układu hamulcowego zawsze jest znajomość charakterystyki technicznej (cech konstrukcyjnych układu, jego budowy i zasady działania) oraz charakterystyki eksploatacyjnej (węzłów regulacyjnych i obsługowych, materiałów eksploatacyjnych, parametrów diagnostycznych) układu hamulcowego danego typu pojazdu.
Diagnozowanie układów hamulcowych można podzielić na dwie części: diagnozowanie mechanizmów sterujących (uruchamiających) hamulce oraz określenie skuteczności działania układu hamulcowego. Sposoby diagnozowania poszczególnych rodzajów mechanizmów uruchamiających są zasadniczo odmienne, natomiast ocena skuteczności działania hamulców jest taka sama dla wszystkich rodzajów układów hamulcowych pojazdów kołowych.
Wymagania eksploatacyjne
Wymaganiami eksploatacyjnymi nazywamy zmienną podczas eksploatacji pojazdu część zbioru wymagań konstrukcyjnych. Dla użytkownika wymagania eksploatacyjne stanowią kryteria prawidłowości działania (symptomy stanu technicznego) danego układu. W przypadku niespełnienia określonego wymagania eksploatacyjnego wystąpią niedomagania w funkcjonowaniu danego układu.
Dla układów hamulcowych sterowanych pneumatycznie wymagania eksploatacyjne można określić następująco:
- właściwa skuteczność działania układu,
- pełne odhamowanie po odjęciu siły uruchamiającej układ,
- proporcjonalne, płynne zwiększenie siły hamowania w stosunku do wzrostu siły uruchamiającej układ,
- możliwie krótki czas reakcji (czas uruchamiania) hamulców,
- stateczność ruchu hamowanego pojazdu,
- brak lub niski poziom hałaśliwości hamulców (przy kołach niezablokowanych),
- niezbędna szczelność obwodów pneumatycznych.
Między tak określonymi wymaganiami występują wzajemne związki przyczynowo-skutkowe. Co do pierwszego z wymienionych tu wymagań należy podkreślić, że skuteczność działania układu hamulcowego pojazdu zależy wyłącznie od konstrukcji i stanu technicznego układu, natomiast skuteczność hamowania pojazdu zależy ponadto od przyczepności kół do nawierzchni jezdni (tj. stanu ogumienia, rodzaju i stanu nawierzchni, obciążenia pojazdu itp.). Skuteczność hamowania pojazdu ze względu na bezpośredni związek z bezpieczeństwem jazdy określana jest w dokumentach normatywnych mających moc prawną. Układy hamulcowe z uruchamianiem powietrznym charakteryzują się dłuższymi czasami reakcji od układów z uruchamianiem hydraulicznym. O ile uzyskiwanie krótkich czasów reakcji w układach hydraulicznych nie stanowi problemu technicznego, o tyle w układach powietrznych osiągnięcie czasów reakcji mieszczących się w granicach ustalonych przepisami wymaga zastosowania w wielu rozwiązaniach samochodów ciężarowych i przyczep specjalnych zaworów przyspieszających działanie. Często w toku eksploatacji pojazdu mogą nastąpić niedomagania układu powodujące wydłużenie czasu reakcji powyżej wymaganych granic.
Czynnikami wpływającymi na wydłużenie czasu reakcji mogą być:
- nadmierne powiększenie się skoku siłowników hamulcowych wskutek zużycia mechanizmów hamulcowych,
- niedomagania części ruchomych w zespołach instalacji między głównym zaworem hamulcowym i siłownikami prowadzące do dławienia przepływu powietrza,
- przedostanie się do przewodów zanieczyszczeń mechanicznych ,ograniczających przekrój przepływu powietrza.
W związku z tym wskazane jest przeprowadzenie raz w roku kontroli czasu reakcji układu w ramach badań diagnostycznych instalacji powietrznej, aby wykryć w porę oddziaływanie wyżej wymienionych czynników. W wielu krajach wprowadzono przepisy zobowiązujące użytkowników pojazdów do takiej okresowej kontroli. Ocenę stopnia spełnienia wymienionych wymagań eksploatacyjnych i ustalenie przyczyn stwierdzonych niedomagań umożliwiają warunki zdatności technicznej, jakim powinien odpowiadać badany układ.
Warunki zdatności technicznej
Warunki zdatności technicznej układu hamulcowego określają jego stan techniczny. Część zbioru warunków zdatności technicznej wyrażona jest w sposób opisowy (np. kompletność układu, prawidłowość zamocowania elementów), a część za pomocą parametrów diagnostycznych. Zakres spełnienia opisowych warunków zdatności technicznej oceniany jest głównie w sposób organoleptyczny, natomiast do pomiaru wartości parametrów diagnostycznych stosowane są metody przyrządowe.
Dla układów hamulcowych sterowanych pneumatycznie warunki zdatności technicznej można określić następująco:
- kompletność układu – układ powinien być skompletowany zgodnie z dokumentacją techniczną pojazdu,
- prawidłowość zamocowania elementów układu,
- właściwy stan zewnętrzny elementów układu – niestwierdzenie uszkodzeń mechanicznych,
- szczelność obwodów pneumatycznych,
- prawidłowe wartości parametrów diagnostycznych pneumatycznego mechanizmu uruchamiającego hamulce – ciśnienie zasilające i sterujące, szczelność układu przenoszącego, czas reakcji hamulców,
- odpowiednie wartości parametrów opisujących stan mechanizmów hamulcowych – luz w mechanizmach hamulcowych, skok roboczy tłoczysk siłowników hamulcowych,
- prawidłowe wartości parametrów oceny skuteczności działania hamulców (wskaźnik skuteczności hamowania, opóźnienie hamowania) oraz parametrów uzupełniających określających rozdział siły hamowania na strony i osie pojazdu, a także zależność zmian siły hamowania na poszczególnych kołach od siły nacisku na pedał hamulca (stabilność siły hamowania),
- wymagane wartości parametrów opisujących stan zespołów układu hamulcowego (np. czas napełniania zbiorników powietrza, szczelność, stopniowalność, czułość działania).
Ocenę zachowania niektórych z wymienionych warunków zdatności technicznej wykonuje się na etapie wstępnego diagnozowania układu hamulcowego. Nie wymaga to specjalistycznego wyposażenia diagnostycznego, a więc może i powinno być dokonywane (przynajmniej w ograniczonym zakresie) przez kierowcę pojazdu podczas obsługi codziennej. Etap wstępnego diagnozowania układu hamulcowego ma na celu ustalenie jego stanu na podstawie oceny stopnia zużycia elementów układu bez jego demontażu. Negatywny wynik badań wstępnych wskazuje na konieczność przeprowadzenia odpowiednich regulacji (lub innych czynności obsługowych) bądź napraw przed wykonaniem dalszych pomiarów mających na celu ocenę skuteczności działania hamulców. Drugi etap diagnozowania wymaga specjalistycznych urządzeń kontrolnych i obejmuje pomiary: ciśnienia i szczelności układu przenoszącego, czasu reakcji hamulców, parametrów oceny skuteczności działania układu hamulcowego oraz parametrów opisujących stan zespołów.
Parametry diagnostyczne i kryteria oceny stanu technicznego
Parametry diagnostyczne służące do oceny stanu technicznego układu hamulcowego sterowanego pneumatycznie można podzielić na następujące grupy:
- parametry dotyczące powietrznych układów przenoszących,
- parametry charakteryzujące stan mechanizmów hamulcowych,
- parametry oceny skuteczności działania hamulców,
- parametry określające zdatność poszczególnych zespołów powietrznych.
W dalszej części, w sposób bardziej szczegółowy, opisano wymienione parametry diagnostyczne i podano ich wartości wymagane (kryteria oceny stanu).
Parametry dotyczące powietrznych układów przenoszących
Do parametrów diagnostycznych charakteryzujących powietrzne układy przenoszące należą: ciśnienie i szczelność układu przenoszącego oraz czas reakcji hamulców. Pojęcia te wymagają wyjaśnienia.
Ciśnienie nominalne – ciśnienie, względem którego dobrano maksymalną i minimalną wartość ciśnienia ustalaną w układzie przez regulator ciśnienia. Ciśnienie obliczeniowe – najniższe ciśnienie przyjęte do obliczeń podczas projektowania układu powietrznego; ciśnienie, w którym osiągnięta jest skuteczność hamowania przewidziana dla danego pojazdu z maksymalnym dopuszczalnym obciążeniem. Ciśnienie asymptotyczne – wartość ciśnienia, która ustali się w siłownikach po jednorazowym pełnym zahamowaniu. Zakres ciśnień jest to przedział ciśnień ograniczony minimalną i maksymalną wartością ciśnienia ustaloną przez regulator. Szczelność układu przenoszącego (instalacji powietrznej) w pojazdach samochodowych mierzy się czasem spadku ciśnienia w zbiornikach powietrza. Czas reakcji układu powietrznego samochodu określa się czasem wzrostu ciśnienia w siłownikach od chwili uruchomienia hamulca roboczego do chwili uzyskania ciśnienia równego 75% wartości asymptotycznej. Czas reakcji hamulców przyczepy liczony jest od uzyskania w przewodzie sterującym ciśnienia równego 10% wartości asymptotycznej do uzyskania ciśnienia w siłownikach przyczepy równego 75% wartości asymptotycznej. Czas wzrostu ciśnienia w przewodzie sterującym przyczepy liczony jest od rozpoczęcia nacisku na pedał hamulca roboczego do uzyskania określonej wartości ciśnienia asymptotycznego (10 lub 75%).
Ciśnienie powietrza w instalacji pneumatycznej
Wartości ciśnienia powietrza w układzie przenoszącym są podawane przez wytwórcę pojazdu i tak na przykład dla układów dwuprzewodowych pojazdów samochodowych i przyczep zakres ciśnień wynosi 0,62÷0,75 MPa. Obowiązujące wartości ciśnienia w układach przenoszących wynoszą: nominalnego 0,7 MPa, a obliczeniowego 0,6 MPa. Jeżeli w układach pojazdów samochodowych stosowane są inne ciśnienia niż obowiązujące, to wszystkie trzy rodzaje ciśnień powinny być określone przez wytwórcę pojazdu.
Niezależnie od ciśnienia zastosowanego w układzie pojazdu samochodowego ciśnienie na wejściu do układu dwuprzewodowego przyczepy powinno mieścić się w niżej zestawionych granicach:
- 0,65÷0,85 MPa – dla przewodu zasilającego,
- 0,65÷0,80 MPa – dla przewodu sterującego.
Szczelność układu przenoszącego
Szczelność układu przenoszącego (instalacji pneumatycznej) w pojazdach samochodowych mierzy się czasem spadku ciśnienia w zbiornikach powietrza, w następujących warunkach: silnik nie pracuje, hamulce w stanie odhamowanym, początkowe ciśnienie w zbiornikach równe nominalnemu. Wymagania odnośnie do szczelności układu przenoszącego dla pojazdu samochodowego i przyczepy zostały podane poniżej.
Pojazd samochodowy
Spadek ciśnienia w zbiorniku każdego z niezależnych obwodów układu, w ciągu 10 minut, powinien być nie większy niż 2% ciśnienia początkowego (równego nominalnemu). Spadek ciśnienia w zbiorniku każdego z niezależnych obwodów układu, w ciągu 3 minut, powinien być nie większy niż 5% ciśnienia początkowego. Podczas sprawdzania szczelności należy nacisnąć na pedał hamulca roboczego, aby uzyskać częściowe zahamowanie zapewniające ciśnienie 0,3 MPa w siłownikach, odczekać 1 minutę i określić, czy w ciągu 3 minut spadek ciśnienia powietrza jest nie większy niż 5%. Spadek ciśnienia w zbiorniku każdego z niezależnych obwodów układu, podczas jednokrotnego pełnego zahamowania, powinien być nie większy niż 0,06 MPa.
Przyczepa
Spadek ciśnienia w zbiornikach układu, w ciągu 10 minut, powinien być nie większy niż 2% ciśnienia początkowego, które ustali się po odłączeniu przyczepy od pojazdu ciągnącego.
Czas reakcji hamulców
Ważnym parametrem związanym z hamowaniem jest czas zadziałania układu (czas reakcji). Wymagania odnośnie czasu zadziałania układów powietrznych zawarte są w załączniku nr 6 Regulaminu 13 EKG ONZ.
Pojazd samochodowy
Pomiar czasu reakcji odbywa się przy ciśnieniu początkowym w zbiorniku powietrza równym dolnej wartości granicznej ustalonej przez regulator, czasie uruchamiania hamulca roboczego (czasie odpowiadającym pełnemu skokowi pedału hamulca) 0,2 s, po wyregulowaniu skoku roboczego siłowników na 1/3.
Wymagania dotyczące czasu reakcji hamulców są następujące:
- w siłownikach hamulcowych pojazdu samochodowego czas wzrostu ciśnienia powietrza do 75% wartości asymptotycznej nie powinien być dłuższy niż 0,6 s, licząc od momentu naciśnięcia na pedał hamulca roboczego,
- w przewodzie sterującym czas od rozpoczęcia nacisku na pedał hamulca roboczego do chwili uzyskania ciśnienia równego 10% wartości asymptotycznej powinien wynosić nie więcej niż 0,2 s, a do chwili uzyskania ciśnienia równego 75% wartości asymptotycznej nie więcej niż 0,4 s.
Przyczepa
Pomiar wykonuje się przy ciśnieniu początkowym w zbiornikach przyczepy równym 0,65 MPa, siłownikach wyregulowanych na 1/3 skoku roboczego i przyczepie odłączonej od pojazdu ciągnącego. Podczas badań należy stosować symulator odtwarzający w przewodzie sterującym przyczepy wzorcowy impuls ciśnieniowy z pojazdu samochodowego.
Czas reakcji hamulców przyczepy, liczony od uzyskania w przewodzie sterującym ciśnienia równego 10% wartości asymptotycznej do uzyskania w siłownikach przyczepy ciśnienia równego 75% wartości asymptotycznej, nie powinien przekraczać 0,4 s.
Przykłady przebiegu omówionych ciśnień w funkcji czasu (dla sterowania dwuprzewodowego) oraz wymagane czasy reakcji hamulców dla pojazdu samochodowego i przyczepy przedstawiono na rys. 1.
Parametry charakteryzujące stan mechanizmów hamulcowych
Do tej grupy parametrów diagnostycznych zalicza się:
- luz w mechanizmach hamulcowych,
- skok roboczy tłoczysk siłowników hamulcowych.
Luz w mechanizmach hamulcowych
Zużywanie się elementów ciernych mechanizmów hamulcowych podczas eksploatacji pojazdu powoduje stopniowe zwiększanie luzu w mechanizmach hamulcowych (np. luzu między szczękami i bębnem hamulcowym). Luz ten można zmierzyć bezpośrednio szczelinomierzem (jeśli rozwiązanie konstrukcyjne umożliwia taki pomiar) lub ocenić pośrednio na podstawie wartości skoku roboczego tłoczysk siłowników hamulcowych (w hamulcach sterowanych pneumatycznie). Luz między nakładkami hamulcowymi i bębnem hamulcowym powinien wynosić 0,2÷0,6 mm. Powodem nieprawidłowego luzu jest najczęściej zużycie się nakładek i bębnów hamulcowych lub niewłaściwie wykonana regulacja. Może to być przyczyną małej skuteczności hamowania, przegrzewania się bębnów, blokowania kół.
Skok roboczy tłoczysk siłowników hamulcowych
Prawidłowo wyregulowana wartość skoku roboczego tłoczysk siłowników hamulcowych niezbędna do pełnego zahamowania powinna być równa 1/3 skoku całkowitego. W żadnym przypadku nie wolno eksploatować pojazdu, w którym skok roboczy tłoczysk siłowników osiągnął wartość stanowiącą 2/3 skoku całkowitego. Szczególnie niebezpieczne jest to w siłownikach przeponowych, ponieważ po przekroczeniu podanej wyżej wartości gwałtownie zmniejsza się wartość siły na tłoczysku, a tym samym maleje siła docisku szczęk hamulcowych do powierzchni bębna. Ponadto nadmierny skok roboczy może być przyczyną dużych spadków ciśnienia w zbiornikach powietrza po każdorazowym zahamowaniu, a także wydłużonego czasu reakcji hamulców z uwagi na konieczność napełnienia w czasie hamowania zwiększonych objętości komór roboczych siłowników. Należy wziąć pod uwagę również fakt, że dźwignia hamulcowa wymusza wówczas zwiększone wychylenie kątowe tłoczyska siłownika, co wpływa niekorzystnie na trwałość oraz pracę jego elementów wewnętrznych. W przypadku zastosowania dźwigni z automatyczną regulacją skoku (luzu w mechanizmach hamulcowych) regulacja powinna odbywać się samoczynnie w całym okresie eksploatacji. Obsługa ogranicza się wówczas tylko do okresowego sprawdzania (przez pomiar skoków dźwigni), czy automatyczna regulacja działa prawidłowo. Taki sam wpływ na działanie układu ma wielkość skoków siłowników współpracujących z klinowymi rozpieraczami mechanizmów bębnowych, jak i uruchamiających mechanizmy tarczowe. W tych przypadkach stosuje się jednak z reguły automatyczną regulację luzów. Zgodnie z wymaganiami przepisów międzynarodowych powinna istnieć możliwość łatwego sprawdzenia stanu zużycia okładzin hamulcowych, na przykład przez zastosowanie wzierników w osłonach mechanizmów hamulcowych.
Parametry oceny skuteczności działania hamulców
Do oceny skuteczności działania hamulców podczas badań eksploatacyjnych (na stacjach kontroli pojazdów) przyjęto następujące parametry:
- całkowita (sumaryczna) siła hamowania i obliczony na tej podstawie wskaźnik skuteczności hamowania,
- maksymalne opóźnienie hamowania,
- wzniesienie, na którym pojazd powinien być utrzymany nieruchomo.
Podczas badań eksploatacyjnych skuteczność hamowania dla hamulców roboczego i awaryjnego określa się wskaźnikiem z, który jest stosunkiem całkowitej siły hamowania do siły wynikającej z dopuszczalnej masy całkowitej pojazdu lub stosunkiem opóźnienia hamowania do przyspieszenia ziemskiego. Wskaźnik skuteczności hamowania może być odnoszony do pojedynczej osi jezdnej pojazdu.
Wymagana skuteczność hamowania powinna być osiągnięta dla siły nacisku na pedał hamulca nie większej niż 500 N (samochody osobowe) lub 700 N (samochody ciężarowe). Szczegółowe wymagania odnośnie nacisku na pedał (dźwignię) hamulca zawarte są w rozporządzeniu ministra infrastruktury w sprawie zakresu i sposobu przeprowadzania badań technicznych pojazdów. Natomiast załącznik nr 7 do rozporządzenie ministra infrastruktury o warunkach technicznych pojazdów określa minimalne wartości wskaźników skuteczności hamowania dla hamulca roboczego i awaryjnego, dla poszczególnych rodzajów pojazdów w zależności od daty ich pierwszej rejestracji – tabela 1.
Dla hamulca roboczego wymaga się dodatkowo, aby siły hamowania kół jednej strony nie różniły się więcej niż o 30% od sił hamowania kół drugiej strony, przyjmując większą wartość jako odniesienie (współczynnik rozdziału sił hamowania na strony b).
W przypadku hamulca postojowego skuteczność hamowania określa się wielkością pochyłości w, na jakiej hamulec powinien utrzymać pojazd. Hamulec postojowy powinien zapewnić unieruchomienie całkowicie obciążonego pojazdu na wzniesieniu i spadku o pochyleniu co najmniej 16%, a całkowicie obciążonego zespołu pojazdów – co najmniej 8%. Dla hamulca postojowego w stanie zdatności musi znajdować się także urządzenie blokujące dźwignię hamulca.
Badanie skuteczności hamulców przez pomiar wartości sił hamowania wykonywane jest w warunkach stacjonarnych (badania stanowiskowe). Pomiaru skuteczności i równomierności działania hamulców podczas eksploatacji (na stacjach kontroli pojazdów) dokonuje się zgodnie z instrukcją zamieszczoną w dziale II załącznika nr 1 do rozporządzenia ministra infrastruktury w sprawie zakresu i sposobu przeprowadzania badań technicznych pojazdów oraz wzorów dokumentów stosowanych przy tych badaniach. Instrukcja nakazuje obliczyć wskaźnik skuteczności hamowania z na podstawie zmierzonej całkowitej siły hamowania odniesionej do siły ciężkości od dopuszczalnej masy całkowitej badanego pojazdu oraz współczynnik rozdziału siły hamowania na strony b. Oprócz tego zaleca się określenie współczynnika rozdziału sił hamowania na osie pojazdu m (jego wartość zależy od konstrukcji pojazdu) oraz współczynnika stabilności siły hamowania s danego koła (stosunku maksymalnej i minimalnej wartości siły hamowania w trakcie jednego obrotu koła). Różna od jedności wartość współczynnika stabilności może między innymi świadczyć o owalizacji bębnów hamulcowych, zmianach grubości tarczy hamulcowej na jej obwodzie.
Stan techniczny układu hamulcowego ocenia się na podstawie uzyskanych podczas badań stanowiskowych parametrów diagnostycznych w sposób przedstawiony niżej:
- ocena skuteczności działania hamulców roboczego i awaryjnego jest pozytywna, jeżeli uzyskany wskaźnik skuteczności hamowania z jest nie mniejszy niż określony w przepisach (patrz tabela 1),
- współczynnik rozdziału sił hamowania na strony b (dla hamulca roboczego) nie może być większy niż 30% (ocena równomierności działania hamulca),
- stabilność siły hamowania każdego z kół uznaje się za zadowalającą, jeżeli wskaźnik s ≤ 1,2 dla każdej siły nacisku na pedał (wartość wskaźnika stabilności dla małych nacisków na pedał hamulca zawiera informacje o nierównomiernym zużyciu tarczy hamulcowej, okładzin ciernych, owalizacji bębna itp., a dla większych nacisków dodatkowo o zmniejszonej sztywności bębna, szczęk),
- rozdział sił hamowania między osiami pojazdu powinien być zgodny z założeniami konstrukcyjnymi, wynikającymi z wymagania optymalnego wykorzystania przyczepności opon w przeciętnych warunkach eksploatacji pojazdu (wartość współczynnika m dla samochodów osobowych wynosi 1÷1,5, a dla samochodów ciężarowych 0,8÷1,2).
Jednoczesne spełnienie dwóch pierwszych wymagań (dotyczących skuteczności i równomierności działania) jest warunkiem koniecznym uznania hamulca roboczego za zdatny. Pozostałe parametry mają znaczenie pomocnicze i wykorzystywane są przede wszystkim do lokalizacji niedomagań układu hamulcowego. Nowoczesne urządzenia do pomiaru sił hamowania, wyposażone w wagę i zbudowane z zastosowaniem techniki mikroprocesorowej mają oprogramowanie, które pozwala diagnoście na wybranie rodzaju badanych hamulców (roboczy, awaryjny, postojowy, sterowany hydraulicznie lub pneumatycznie) i liczby osi pojazdu (rys. 2). Oprócz tego zastosowane oprogramowanie umożliwia samoczynne obliczenie wymaganych parametrów diagnostycznych układu hamulcowego, przedstawienie ich na ekranie monitora w postaci liczbowej (rys. 3) lub wykreślnej (rys. 4) oraz w formie wydruku. Zwalnia to diagnostę z konieczności wykonywania czasochłonnych obliczeń, a jego rola sprowadza się do interpretacji otrzymanych wyników pomiarów i obliczeń. Opóźnienie hamowania bada się podczas próby drogowej. Przy czym zmierzoną wartość opóźnienia odnosi się do opóźnienia minimalnego, wyznaczonego na podstawie wartości granicznej wskaźnika skuteczności hamowania. Skuteczność hamowania jest prawidłowa, jeżeli zmierzone opóźnienie hamowania jest nie mniejsze od wymaganego. Wartość wymaganą opóźnienia oblicza się na podstawie wskaźnika skuteczności hamowania po podzieleniu go przez 10 (patrz tabela 1). Na przykład wskaźnik 50 oznacza, że wymagane opóźnienie hamowania wynosi minimum 5,0 m/s2. Podczas pomiaru opóźnienia, tj. w czasie hamowania pojazdu na drodze od prędkości początkowej około 30 km/h (przy niekorygowanym kierownicą kierunku jazdy), ocenia się również stateczność ruchu hamowanego pojazdu. Odchylenie od prostoliniowego kierunku jazdy nie powinno przekraczać 0,5 m.
Parametry dotyczące zespołów powietrznych
Stan techniczny poszczególnych zespołów powietrznych określa się na podstawie wartości parametrów diagnostycznych lub charakterystyk dotyczących:
- zespołów zasilających (sprężarki, regulatory ciśnienia, zawory zabezpieczające, zbiorniki itp.),
- zespołów sterujących (główne i ręczne zawory sterujące, zawory sterujące hamulcami przyczepy, regulatory siły hamowania, mechanizmy wspomagające itp.),
- zespołów przenoszących (zawory przekaźnikowe, zawory przyspieszające odhamowanie, zawory uruchamiające hamulce przyczepy, siłowniki itp.),
- zespołów obwodów dodatkowych (zespoły hamulca silnikowego, mechanizmy wspomagania sprzęgła, blokady mechanizmów różnicowych itp.).
W przypadku konieczności przeprowadzenia diagnozowania zespołów powietrznych należy korzystać z norm zakładowych, dotyczących wymagań i badań zespołów, wydawanych przez ich producentów. Niżej podano przykładowe, wybrane parametry charakteryzujące stan techniczny sprężarek powietrza. Wydatek sprężarki określany jest czasem napełniania zbiorników powietrza do wartości ciśnienia określonej przez wytwórcę pojazdu, przy której pojazd uzyskuje skuteczność hamowania przypisaną hamulcowi roboczemu (wartość tego ciśnienia p powinna być podana w dokumentacji pojazdu). Czas napełniania układu powinien być mierzony w czasie pracy sprężarki przy prędkości obrotowej silnika odpowiadającej maksymalnej mocy lub prędkości obrotowej ograniczonej regulatorem. Dopuszczalne maksymalne czasy napełniania zbiorników powietrza w układzie przenoszącym hamulców przy wyłączonych zbiornikach obwodów dodatkowych podano w tabeli 2. Natomiast na rys.5 przedstawiono charakterystyki wybranych sprężarek powietrza typu HS stosowanych w pojazdach użytkowych. Dla tych sprężarek czas napełniania zbiornika 40 dm3 od ciśnienia 400 kPa do 800 kPa, przy prędkości obrotowej 2800 obr./min., nie powinien przekraczać 65 s. Dopuszczalne maksymalne czasy napełniania zbiorników dodatkowych w pojazdach, w których łączna pojemność zbiorników dodatkowych przekracza 20% pojemności zbiorników pojazdu, podano w tabeli 3. Czas napełniania zbiorników układu przenoszącego może być także określony na podstawie katalogowych czasów napełniania podanych dla sprężarek po przyjęciu, że przyrost czasu jest wprost proporcjonalny do przyrostu objętości zbiorników. Pozostałe zespoły pneumatyczne kierowane są do diagnozowania zwykle po wymontowaniu z pojazdu w sytuacji, gdy zostały uznane jako uszkodzone oraz po naprawie lub regeneracji.
Podczas badań każdego z zespołów na stanowiskach specjalistycznych sprawdza się niżej wymienione parametry diagnostyczne:
- szczelność,
- czułość działania,
- stopniowalność,
- charakterystyki statyczne.
Szczelność sprawdza się przez obserwację spadku ciśnienia w zbiorniku pomiarowym stanowiska podłączonym do badanego zespołu.
Czułość określana jest wielkością ciśnienia odpowiadającego początkowi zadziałania zespołu. Stopniowalność (ciągłość działania) oceniana jest możliwością uzyskania małych przyrostów ciśnienia w przyłączu wyjściowym zaworu przy zmianach ciśnienia w przyłączu sterującym.
Charakterystyka statyczna wyrażana jest zależnością zmian ciśnienia na wyjściu z zaworu od zmian ciśnienia w przyłączu lub przyłączach sterujących, przy stałym poziomie ciśnienia zasilania. Wymagane wartości i tolerancje mierzonych parametrów podawane są przez producentów zespołów pneumatycznych.
dr inż. Kazimierz Sitek
Literatura
Rozporządzenie Ministra Infrastruktury z dnia 31.12.2002 r. w sprawie warunków technicznych pojazdów oraz zakresu ich niezbędnego wyposażenia (Dz.U. Nr 32 z 2003 r., z późn. zm.).
Rozporządzenie Ministra Infrastruktury z dnia 18.09.2009 r. w sprawie zakresu i sposobu przeprowadzania badań technicznych pojazdów oraz wzorów dokumentów stosowanych przy tych badaniach (Dz.U. Nr 155 z 2009 r., z późn. zm.).
Sitek K.: Diagnostyka samochodowa. Układy odpowiedzialne za bezpieczeństwo jazdy. Wydawnictwo AUTO, Warszawa 1999.
Komentarze (0)