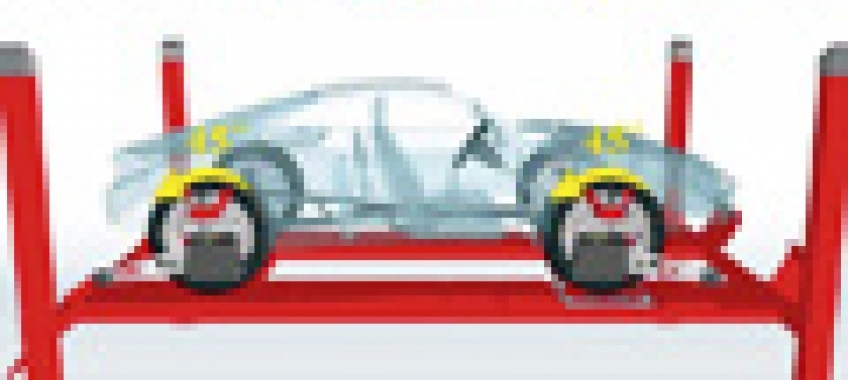
Układ kierowniczy pojazdu ma zapewnić przede wszystkim zmianę kierunku jazdy zgodnie z wolą kierującego. Poza tym, konieczne jest nadanie poszczególnym jego podzespołom i elementom takich własności konstrukcyjnych, które umożliwiać będą:
- samoczynne utrzymywanie się kierunku jazdy, przy ustawieniu kół do jazdy na wprost;
- toczenie się kół kierowanych bez poślizgu w trakcie pokonywania zakrętu;
- samoczynny powrót kół kierowanych do jazdy na wprost po wykonanym skręcie.
Realizowanie przez układ kierowniczy tych zadań możliwe jest poprzez nadanie odpowiednich parametrów konstrukcyjnych ustawienia poszczególnym elementom układu oraz zawieszenia. Zespół wszystkich parametrów ustawienia względem siebie poszczególnych elementów układu kierowniczego określa się jako geometrię ustawienia kół i osi pojazdu. Wpływ na zachowanie się pojazdu w trakcie jazdy ma zarówno kinematyka zawieszenia, czyli zmiana ustawienia kół przy pionowych ruchach nadwozia i jego poprzecznych przechyłach kątowych, jak również elastokinematyka, czyli przemieszczenia kół pod wpływem występujących w śladzie opony sił wzdłużnych i poprzecznych. Dlatego też konstruktorzy i projektanci pojazdów samochodowych określają wymagane w trakcie eksploatacji wartości poszczególnych kątów ustawienia kół wraz z dopuszczalnymi odchyłkami od wartości nominalnych. W związku z tym, że nawet niewielkie zmiany ustawienia kół od tych nadanych konstrukcyjnie mogą mieć znaczny wpływ na zachowanie się (kierowalność) pojazdu w trakcie jazdy oraz zdecydowanie szybsze zużycie opon, poprawność parametrów ustawienia kół i osi powinna być kontrolowana okresowo nie tylko w trakcie badań technicznych pojazdu. Przy pomiarze i kontroli parametrów geometrii ustawienia kół i osi pojazdów konieczne jest spełnienie odpowiednich wymogów dotyczących samego stanowiska kontrolno-pomiarowego. Warunkiem uzyskania poprawnych i wiarygodnych warunków mierzonych parametrów w przypadku pojazdów o dopuszczalnej masie całkowitej do 3,5 t jest wykorzystanie odpowiednio wypoziomowanej ławy pomiarowej, w której odchylenie od poziomu nie może przekraczać 3 mm na 1 m bieżący stanowiska pomiarowego. Kolejnym warunkiem zapewniającym odpowiednią dokładność uzyskiwanych wyników pomiarów mierzonych parametrów jest zapewnienie prawidłowego (podawanego przez producenta pojazdu) ciśnienia w oponach. Na poprawność i dokładność pomiaru parametrów geometrii ustawienia kół i osi pojazdu wpływ ma również odpowiedni stan techniczny układu kierowniczego oraz zawieszenia. Ewentualne, nadmierne luzy układu kierowniczego oraz zawieszenia należy bezsprzecznie wyeliminować. Dokonywanie jakichkolwiek pomiarów i kontroli parametrów ustawienia geometrii kół i osi pojazdu w takim stanie technicznym jest zupełnie pozbawione sensu. Ze względu na coraz większą różnorodność konstrukcji zawieszeń eksploatowanych pojazdów konieczne jest przed przystąpieniem do pomiarów parametrów geometrii ustawienia kół określenie wysokości nadwozia względem podłoża. Obniżone wysokości nadwozia są bowiem przyczyną różniących się od standardowych wielkości wartości poszczególnych parametrów. Prawidłowe warunki pomiaru poszczególnych parametrów geometrii kół można uzyskać dopiero po zapewnieniu odpowiedniej wartości ugięcia zawieszenia samochodu. W zależności od konstrukcji pojazdu producenci podają ten parametr na różne sposoby, tj. poprzez:
- podanie odległości jednego lub kilku punktów kontrolnych podwozia od podłoża lub różnice dwóch wybranych punktów kontrolnych. Pomiar parametrów geometrii wykonywać należy, gdy wartości znajdują się w wymaganych zakresach. W razie potrzeby pojazd należy odpowiednio dociążyć lub odciążyć;
- określenie rozkładu obciążenia samochodu paliwem w zbiorniku, obciążonym w bagażniku oraz na miejscach pasażerów i kierowcy;
- pomiar odpowiedniego parametru zależnego od producenta pojazdu (dotyczy to przede wszystkim najnowszych modeli produkowanych pojazdów), np. dla:
- samochodów grupy VW poprzez obliczenie wartości odległości leżącej w płaszczyźnie prostopadłej do podłoża, w której leży oś obrotu koła, pomiędzy punktem dolnego obrzeża wnęki koła a osią obrotu koła,
- samochodów BMW poprzez pomiar odległości mierzonej w płaszczyźnie prostopadłej do podłoża, w której leży oś obrotu koła pomiędzy punktem dolnego obrzeża wnęki koła, a najniżej położonym punktem zewnętrznego obrzeża obręczy tarczy koła.
Odpowiednio, zgodnie z powyższymi zaleceniami, przygotowany pojazd wprowadzany jest na stanowisko kontrolno-pomiarowe w taki sposób, aby koła przedniej osi znajdowały się na obrotnicach umożliwiających swobodne (bez oporów podłoża) wykonywanie zalecanej wartości skrętu kół, a koła osi tylnej były umieszczone na płytach przesuwnych umożliwiających swobodne przemieszczanie się kół w poziomie.
Obecnie na rynku jest znaczna konkurencja w zakresie urządzeń kontrolno-pomiarowych służących do określania poprawności ustawienia geometrii kół i osi pojazdów. W warsztatach są jeszcze najstarsze konstrukcje przyrządów, czyli optyczne (laserowe). Poza tym, coraz częściej wykorzystywane są urządzenia komputerowe z głowicami aktywnymi, wyposażonymi w kamery CCD, a także najnowszej generacji przyrządy z głowicami pasywnymi, pracującymi w tzw. systemie 3D.
Zdecydowanie najszerszą grupę przyrządów stanowią urządzenia komputerowe z aktywnymi głowicami pomiarowymi. Możliwości pomiarowe oraz wygodę prowadzenia samego procesu pomiaru zobrazowane zostaną na przykładzie urządzenia X-631 firmy LAUNCH. Należy nadmienić, że możliwości oraz dokładności prowadzenia pomiaru tego przyrządu poddane były sprawdzeniu w trakcie procesu certyfikacji przez Instytut Transportu Samochodowego i zostały pozytywnie ocenione, dzięki czemu przyrząd ten ma stosowny certyfikat zgodności z wymogami ustawy, uprawniający do stosowania tego urządzenia w trakcie prowadzonych badań technicznych na stacjach kontroli pojazdów.
Prawidłowo przeprowadzony pomiar parametrów geometrii kół jest uwarunkowany wykonaniem przez obsługującego przyrząd wielu różnych skomplikowanych czynności. W praktyce czynności te są często przez diagnostę pomijane, zwykle w celu skrócenia czasu wykonania pełnego pomiaru. Dodatkowym czynnikiem, który wpływa na możliwość popełnianych przez prowadzącego pomiar diagnostę błędów bywa skomplikowana i złożona procedura pomiarowa.
Urządzenie X-631 firmy LAUNCH dzięki odpowiedniemu oprogramowaniu umożliwia szybkie wykonanie pomiaru, przy jak najmniejszej liczbie czynności dodatkowych i stosunkowo ograniczonym udziale obsługującego, którego nieodpowiednio przeprowadzone czynności są najczęściej przyczyną powstawania błędów pomiaru. Dzięki zastosowaniu w nim odpowiedniej technologii przetwarzania sygnałów i przesyłania informacji pomiar tym urządzeniem jest szybki i wygodny. Program prowadzi diagnostę przez cały proces pomiarowy. Dzięki zastosowanym procedurom pomiarowym eliminowane są na bieżąco ewentualne błędy obsługowe popełniane przez diagnostę. Urządzenie ma bardzo przystępne dla obsługującego oprogramowanie wraz z bazą danych parametrów wzorcowych, umożliwiającą porównanie wartości wzorcowych, podawanych przez producenta pojazdu z rzeczywistymi otrzymywanymi w trakcie wykonywania pomiaru. W programie zawarte są ponadto graficzne obrazy punktów regulacyjnych pojazdów, zalecane wartości ich obciążenia oraz wskazane wartości ugięcia zawieszenia. Program ma także różnego rodzaju pomocne animacje obrazujące poszczególne czynności obsługowe wykonywane w trakcie pomiaru. Przyrząd wykorzystuje technikę kamer CCD, bazującą na promieniowaniu podczerwonym emitowanym i odbieranym przez poszczególne głowice pomiarowe, dzięki czemu uzyskuje się wokół pojazdu tzw. elektroniczną ramę, oplatającą pojazd wokół wiązkami promieniowania, co pozwala na ustalenie względem siebie położenia poszczególnych czujników umieszczonych w głowicach pomiarowych osadzonych na kołach, a tym samym odpowiedniego położenia kątowego wszystkich kół.
Podobnie jak w innych urządzeniach pomiarowych tej klasy, głowice pomiarowe przyrządu X-631 zasilane są akumulatorowo. Ich ładowanie realizowane jest każdorazowo po odwieszeniu głowic na szafce lub w trakcie wykonywania pomiaru przy wykorzystaniu przewodów zasilania awaryjnego. Przesyłanie danych i wzajemna wymiana informacji pomiędzy głowicami pomiarowymi i jednostką centralną (komputerem) przebiega z wykorzystaniem transmisji radiowej.
Zgodnie z obowiązującymi przepisami przyrząd do pomiaru i kontroli geometrii ustawienia kół musi umożliwiać pomiar:
- zbieżności połówkowej kół przednich,
- zbieżności całkowitej kół przednich,
- zbieżności całkowitej kół tylnych,
- kątów pochylenia kół przednich i tylnych,
- kątów nieprostopadłości osi kół do osi symetrii ramy,
- kątów nierównoległości osi kół,
- bocznego przestawienia kół względem osi symetrii ramy,
- kątów wyprzedzenia i pochylenia osi sworzni zwrotnic,
- różnicy kątów skrętu kół przy skręcie o 20O,
- maksymalnych kątów skrętu kół.
Przyrząd X-631 jako mający certyfikat ITS oczywiście spełnia powyższe wymagania. Bardzo ciekawą i przydatną funkcją programową urządzenia jest możliwość wykorzystania czynności przeprowadzania kompensacji bicia obręczy na trzy sposoby. Celem przeprowadzenia kompensacji jest jak wiadomo uniknięcie błędów pomiarowych, spowodowanych odkształceniem obręczy i wynikającym z tego powodu biciem tarczy koła oraz niedoskonałością montażu uchwytu głowicy na obręczy koła, bądź głowicy na uchwycie głowicy. Kompensacja bicia w przyrządzie X-631 może być przeprowadzana poprzez:
- uniesienie i obrót koła o 90O,
- uniesienie i obrót koła o 180O,
- przetoczenie pojazdu.
Kompensacja przez uniesienie i obrót koła o 180O to tryb standardowy, który realizowany jest łącznie dla przedniej i tylnej głowicy. W przypadku kompensacji z uniesieniem i obrotem koła o 90O istnieje możliwość wykonywania jej dla każdego koła z osobna.
Najwygodniejszą i najszybszą zarazem formą przeprowadzenia kompensacji bicia kół jest funkcja z wykorzystaniem przetoczenia pojazdu. Funkcja ta umożliwia przeprowadzenie pełnej kompensacji wszystkich kół po przetoczeniu pojazdu do przodu i do tyłu w trakcie obrotu koła o kąt 45O. Przy przeprowadzaniu kompensacji przez przetoczenie należy bezwzględnie pamiętać o stosowaniu podkładek dystansowych pomiędzy najazdem z obrotnicą, w celu uniknięcia uskoku zawieszenia.
Kolejną, bardzo pomocną przy wykonywaniu pomiarów i prowadzeniu ewentualnych regulacji funkcją programową jest kompensacja pomiaru regulowanych wartości. W celu wykonania ustawienia niektórych parametrów geometrii kół konieczne jest uniesienie pojazdu, w trakcie którego wartości na ekranie będą się zmieniać. Aby proces regulacji przebiegał prawidłowo, można wykorzystać w urządzeniu X-631 funkcję regulacji podniesienia, dzięki której oprogramowanie automatycznie przeprowadza kompensację występujących zmian parametrów. Inną bardzo wygodną funkcją przyrządu X-631 jest możliwość wykonywania pomiaru parametrów geometrii w pojazdach z niskim zawieszeniem. Nie ma konieczności obniżania położenia głowic pomiarowych z wykorzystaniem dodatkowych przedłużaczy, tak jak ma to miejsce w innych przyrządach, lecz wykorzystuje się specjalną procedurę pomiarową, umożliwiającą ukośne pochylenie głowic pomiarowych w celu zapewnienia wystarczającego prześwitu pod podwoziem pojazdu, pozwalającego na komunikowanie się między sobą głowic pomiarowych danej osi. Wykorzystywane jest w tej funkcji tzw. poziomowanie elektroniczne głowicy, zapewniające uwzględnienie kompensacji odchylenia głowicy od poziomu.
Wszystkie stosowane dotychczas tradycyjne urządzenia do kontroli i pomiaru geometrii ustawienia kół i osi pojazdów posiadały technologie pomiarowe, wymagające konieczność wykonywania przez obsługującego znacznej ilości czynności w trakcie całego procesu. Niestety, od dokładności i staranności wykonywania tych zabiegów bardzo uzależniony był końcowy wynik pomiaru poszczególnych parametrów. Poza tym, konieczność wykonywania tych wszystkich operacji związana jest z dość znacznym upływem czasu niezbędnego do wykonania pełnego pomiaru.
Stosowane od niedawna nowoczesne technologie pomiarowe w urządzeniach do pomiaru i kontroli geometrii ustawienia kół i osi pojazdów pozbawione są tych wad. Przyrządy tego typu, których przykładem jest KWA-300 3D firmy LAUNCH, pracują w systemie trójwymiarowego modelowania parametrów podwozia, znanym jako pomiar w systemie 3D. Przyrząd ma tzw. pasywne głowice refleksyjne zakładane na zaciski mocowane na kołach, odbijające promienie światła podczerwonego, wysyłane z odpowiednich nadajników umieszczonych na specjalnych słupach ustawionych z przodu stanowiska pomiarowego. Odbite pod odpowiednim kątem w zależności od ustawienia kątowego kół promieniowania odbierane i rejestrowane są przez cztery kamery (po jednej dla każdego z kół), również umieszczone na słupach. Na podstawie odchyłek kształtu kołowego okręgów z głowic pasywnych, wywołanych zmianą położenia ekranów i zastosowanego odpowiedniego algorytmu przeliczeniowego, program urządzenia oblicza poszczególne parametry ustawienia kół i osi pojazdu. Największą zaletą tego typu urządzenia jest ograniczony zaledwie do 5 minut czas trwania wykonywania pełnego procesu pomiarowego.
mgr Andrzej Kowalewski
Komentarze (0)