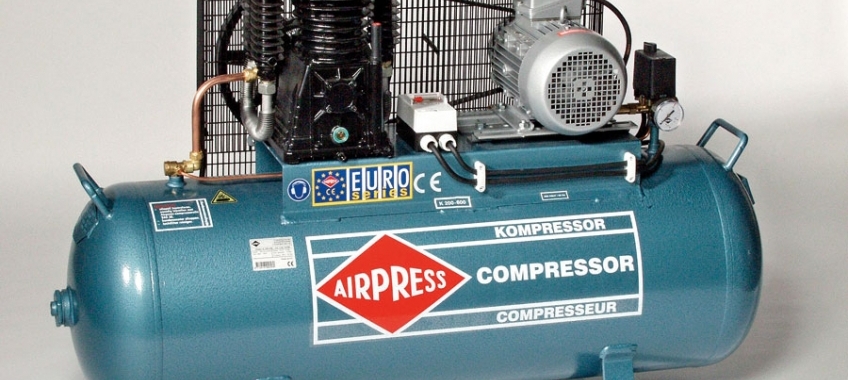
Warsztaty praktycznie każdej specjalizacji usług motoryzacyjnych w zdecydowanej większości wykorzystują obecnie sprężone powietrze jako czynnik roboczy przy napędzie i sterowaniu urządzeń i narzędzi warsztatowych. Wykorzystywane jest ono nawet przy najprostszych czynnościach obsługowych, choćby przy czyszczeniu (przedmuchiwaniu) naprawianych elementów i mechanizmów (przewodów, części itp.).
W zdecydowanej większości sprężone powietrze wykorzystywane jest jednak do napędów montażownic, podnośników, różnego rodzaju narzędzi z ruchem posuwisto-zwrotnym (wyrzynarek), narzędzi udarowych (młotków, punktaków), rotacyjnych (polerek, szlifierek, wkrętarek), kluczy udarowych, urządzeń do obsługi (opróżniania, czyszczenia, napełniania) układów hamulcowych, chłodzenia, paliwowych, smarowania wykorzystujących zasadę nadciśnienia i podciśnienia oraz urządzeń, w których ruch sprężonego powietrza, kierowany przez dyszę wylotową, wymusza ciągły przepływ głównego czynnika w postaci cieczy lub zawiesiny cząstek stałych (pistoletów lakierniczych, pistoletów do konserwacji, urządzeń do piaskowania).
Zdecydowanymi zaletami sprężonego powietrza, jako czynnika roboczego do napędu zautomatyzowanych narzędzi warsztatowych, są:
- niezawodna i prosta konstrukcja,
- wysoka sprawność,
- wygodne sterowanie,
- stosunkowo niewielka masa w stosunku do uzyskiwanej mocy roboczej,
- znaczna trwałość,
- możliwość pracy w trudnych warunkach.
Ze względu na coraz większą liczbę narzędzi i urządzeń warsztatowych wykorzystywanych w warsztacie obiekty tego typu muszą posiadać odpowiednio zaprojektowaną i wykonaną instalację sprężonego powietrza, zapewniającą należytą wydajność i właściwą jakość wytwarzanego powietrza pod wymaganym ciśnieniem. Tego typu instalacja powinna być dobrana pod względem wielkości i wydajności w taki sposób, aby jej możliwości odpowiadały zapotrzebowaniu na sprężone powietrze wszystkich odbiorników (maszyn i urządzeń) pracujących w obiekcie warsztatowym.
Niezbędna jest więc przy jej projektowaniu informacja o liczbie przewidywanych stanowisk odbiorczych, wymaganych ciśnieniach roboczych odbiorników, nominalnego zużycia sprężonego powietrza oraz długościach poszczególnych odcinków instalacji wynikających z usytuowania poszczególnych stanowisk.
W skład każdej warsztatowej instalacji sprężonego powietrza wchodzą: sprężarka, chłodnica, zbiornik, urządzenia uzdatniające (filtry, osuszacze, separatory oleju), przewody oraz przyłącza urządzeń odbiorczych. Najważniejszym elementem instalacji jest sprężarka. Stosowane są ich dwie wersje konstrukcyjne: tłokowe oraz śrubowe. Stosowanymi najczęściej w warsztatowych instalacjach sprężonego powietrza konstrukcjami sprężarek są ich wersje tłokowe, posiadające przemieszczający się w cylindrze tłok (mający zawór wlotowy i wylotowy), wytwarzający podciśnienie. Przy tej budowie sprężarki tłok napędzany jest z wału korbowego silnika. Posiadają one, w zależności od wymaganej wydajności, jeden lub więcej cylindrów. Z kolei w związku z wymaganym ciśnieniem roboczym sprężarki tego typu mogą mieć budowę jedno- lub wielostopniową. W wersji wielostopniowej powietrze wstępnie sprężone w jednym z cylindrów przechodzi do następnego, gdzie ulega dalszemu sprężaniu. Te wersje sprężarek posiadają zwykle wbudowany zbiornik ciśnieniowy oraz chłodnicę wraz z urządzeniami uzdatniającymi. Ich wadą jest dość wysoki poziom hałasu oraz znaczna temperatura wytwarzanego sprężonego powietrza, a także spore nasycenie oleju, co wymusza stosowanie bardziej zaawansowanego procesu jego uzdatniania.
Obecnie zdecydowanie bardziej popularną konstrukcją sprężarek są wersje śrubowe. Charakteryzują się one większą wydajnością w porównaniu ze sprężarkami tłokowymi. Są zarazem znacznie cichsze w trakcie pracy. Konstrukcja tego typu sprężarek oparta jest na dwóch przeciwbieżnych wirnikach śrubowych, pracujących we wspólnej komorze. Sprężarki śrubowe zapewniają znacznie większą wydajność niż konstrukcje tłokowe. Posiadają wbudowaną chłodnicę wytwarzanego sprężonego powietrza. Umożliwiają pracę ciągłą, co ogranicza stosowanie dużych zbiorników wyrównawczych.
Do określenia wydajności sprężarki zastosowanej w warsztatowej instalacji sprężonego powietrza konieczna jest analiza rodzaju i liczby zasilanych odbiorników (urządzeń oraz maszyn). Należy w tym celu w pierwszej kolejności określić rzeczywiste pobory powietrza wszystkich odbiorników, a następnie dokonać oceny, które z nich będą miały najwyższy współczynnik wykorzystania, czyli te, których kilkuminutowe użytkowanie w normalnych, rzeczywistych warunkach będzie przekraczało zapas powietrza znajdujący się w zbiorniku wyrównawczym. Maksymalny pobór sprężonego powietrza tych właśnie odbiorników określa wydajność pracy sprężarki.
W rzeczywistych warunkach pracy w warsztacie nie wszystkie maszyny i urządzenia pobierają sprężone powietrze jednocześnie. Nie należy więc sumować wszystkich poborów powietrza do określania wydajności pracy sprężarki. Właściwe jest więc przy określaniu rzeczywistych poborów każdego odbiornika ustalenie współczynnika wykorzystania go w czasie pracy w przedziale od 0 do 1. Zwykle przyjmowane są wartości od 0,1 do 0,2. Średnie zapotrzebowanie na sprężone powietrze przyjmowane do określenia wydajności sprężarki ustalane jest więc jako iloczyn wyznaczonego dla danego odbiornika współczynnika i jego zapotrzebowania znamionowego. Tak więc suma średnich wartości zapotrzebowania wszystkich odbiorników daje wymaganą wydajność sprężarki w danej instalacji sprężonego powietrza. Dla zapewnienia właściwych warunków pracy sprężarki obliczoną wydajność należy zwiększyć dodatkowo o 50%.
Następnym elementem warsztatowej instalacji sprężonego powietrza jest zbiornik ciśnieniowy, którego zadaniem jest bilansowanie wydajności pracy sprężarki z bieżącym zapotrzebowaniem powietrza w instalacji. Jego zastosowanie zapobiega konieczności ciągłej pracy sprężarki. Zastosowany wyłącznik ciśnieniowy steruje uruchamianiem sprężarki w zależności od aktualnego ciśnienia sprężonego powietrza w zbiorniku ciśnieniowym. W przypadku instalacji sprężonego powietrza wykorzystujących sprężarki tłokowe zbiornik ciśnieniowy eliminuje ponadto niekorzystne wibracje w instalacji, będące efektem pracy tej konstrukcji sprężarek. Na wyjściu przewodów ze zbiornika ciśnieniowego umieszczane są reduktory nastawne służące stabilizacji ciśnienia w dalszej części instalacji na poziomie od 6 do 10 barów.
Wytworzone w sprężarce i zmagazynowane w zbiorniku ciśnieniowym sprężone powietrze przed dostarczeniem do urządzeń i narzędzi warsztatowych musi być jeszcze poddane procesowi uzdatnienia. Konieczność jego odpowiedniego przygotowania wynika z faktu, że może ono zawierać zanieczyszczenia pochodzące:
- z zasysanego powietrza (cząstki zanieczyszczeń stałych i para wodna),
- ze sprężarki (olej pochodzący ze smarowania oraz cząstki pyłu pochodzące ze ścierania się współpracujących elementów).
Zanieczyszczenia sprężonego powietrza wytworzonego w sprężarce mogą być niebezpieczne dla stosunkowo precyzyjnych mechanizmów napędów pneumatycznych narzędzi i urządzeń. W związku z tym powietrze musi być przed dostarczeniem do nich odpowiednio przygotowane poprzez:
- oczyszczenie z zanieczyszczeń mechanicznych (pyłu, rdzy, wody oraz oleju) z wykorzystaniem metod mechanicznych, adsorpcyjnych i absorpcyjnych),
- redukcję ciśnienia do wymaganej wartości przy użyciu zaworów redukcyjnych,
- nasycenie olejem poprzez wprowadzenie kontrolowanej ilości czynnika smarnego w postaci mgły olejowej z użyciem smarownic selekcyjnych.
Dostarczenie sprężonego powietrza jednocześnie do kilku urządzeń i narzędzi rozmieszczonych w różnych miejscach warsztatu wymaga stworzenia rozbudowanej instalacji zaopatrującej poszczególne stanowiska odbiorcze w sprężone powietrze. Bardzo istotny jest dobór właściwych rozmiarów średnic przewodów doprowadzających wynikający z wymaganego objętościowego natężenia przepływu i dopuszczalnych spadków ciśnienia.
Współczesne instalacje sprężonego powietrza tworzone są z przewodów rurowych wykonanych z tworzyw sztucznych. Stosowanie jako materiału konstrukcyjnego tworzyw sztucznych wynika z ich odporności na korozję oraz braku kondensacji zanieczyszczeń wewnątrz przewodów. Wykonanie instalacji z rurek plastikowych zapewnia ponadto cichszą pracę instalacji (wynikającą z lepszego tłumienia drgań), znacznie dłuższą żywotność instalacji, zdecydowanie krótszy czas montażu oraz łatwość przeróbek i modernizacji. Przewody instalacji mocowane są zwykle na ścianach pomieszczeń obiektu warsztatowego.
mgr Andrzej Kowalewski
Komentarze (0)