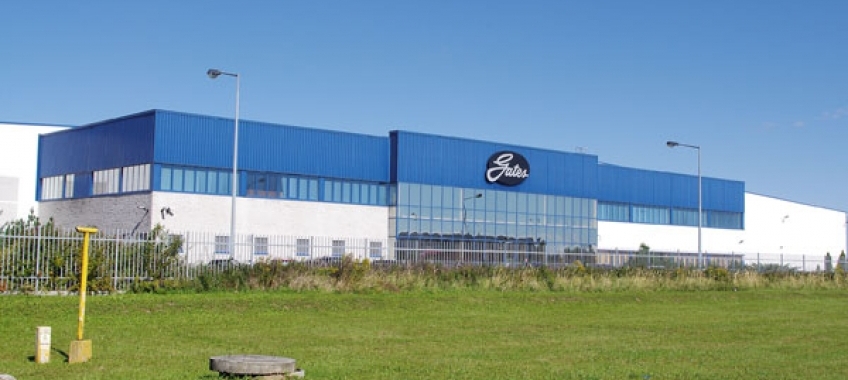
Korporacja Gates, która obchodziła w 2011 roku 100. rocznicę działalności, jest liderem wśród producentów zaawansowanych technologicznie pasków gumowych, przewodów, napinaczy mających zastosowanie w motoryzacji, przemyśle wytwórczym, górniczym, hydraulice oraz w wielu innych gałęziach przemysłu. W Polsce firma działa w Legnickiej Specjalnej Strefie Ekonomicznej i rok temu celebrowała 10. rocznicę rozpoczęcia produkcji. Ten nowoczesny zakład, zbudowany od podstaw, w który zainwestowano ponad 200 mln PLN, jest obecnie największą firmą Grupy w Europie, zatrudniającą ponad 500 osób. Z legnickiej fabryki rocznie wysyłanych jest do kluczowych klientów prawie 5 tys. różnych referencji, włączając w to światowe koncerny motoryzacyjne. Fabryka produkuje na 9 liniach prawie 15 mln pasków klinowych, wieloklinowych, synchronicznych, mających zastosowanie w motoryzacji, rolnictwie, pralkach i wielu innych aplikacjach produktowych. W zakładzie w Legnicy na dwóch mikserach produkowane są również mieszanki gumowe, dostarczane do innych europejskich zakładów. Od 2011 roku Gates Polska może poszczycić się kolejną inwestycją – montażem zestawów naprawczych pasków rozrządu.
W Legnicy znajdują się także laboratoria i centrum rozwoju, w których powstają projekty nowych, innowacyjnych produktów i mieszanek gumowych. I właśnie tam mogliśmy zobaczyć, jak powstają z pozoru proste w budowie paski napędowe. Zaprezentujemy jeden z wielu różnych procesów produkcji pasków z linii, z której schodzą codziennie tysiące pasków samochodowych wieloklinowych, wykorzystywanych do napędzania dodatkowych układów w samochodzie, takich jak: pompy, klimatyzacja, układ wspomagania i innych, w zależności od konfiguracji wymagań klienta. Pierwszym etapem produkcji pasków Micro-V jest operacja budowania, w trakcie której na formę stalową w kształcie walca nakładane są warstwowo odpowiednie komponenty pasków. Podstawową strukturę pasków Micro-V stanowi: nylonowa tkanina impregnowana gumą EPDM – część zewnętrzna paska, kord (rodzaj sznura) wykonany z włókien poliestrowych lub poliamidowych decydujący o wytrzymałości paska na zrywanie oraz guma EPDM wzmocniona odpowiednimi rodzajami włókien – ta warstwa gumy odpowiada za kontakt paska z kołem pasowym. Długość finalna paska determinowana jest za pomocą rozmiaru formy w taki sposób, że obwód formy jest równy długości paska. W operacji budowania pasków następuje także ich oznakowanie zgodne z wymogami klientów, tj. jego kolorem i np. logo. Wiele z pasków trafia na pierwszy montaż, dlatego wykonywane są one ściśle według życzeń koncernów motoryzacyjnych.
Forma wraz z nawiniętymi odpowiednio warstwami gumy i kordów jest przesyłana w cyklu automatycznym do kolejnej operacji, w trakcie wszystkie komponenty są trwale łączone w procesie wulkanizacji. Firma Gates stosuje metody wulkanizacji w środowisku sprężonej pary wodnej w temperaturze ponad 180OC, co zapewnia trwałe połączenie wszystkich składowych oraz nadaje wymaganą wytrzymałość paska. Półproduktem uzyskiwanym po procesie wulkanizacji jest slab, czyli rura wykonana z komponentów paska o długości około 1 m. Slab jest ściągany z formy po uprzednim jej wychłodzeniu do temperatury około 30OC. W kolejnym etapie slab poddawany jest procesowi obróbki wstępnej, polegającemu na szlifowaniu jego powierzchni zewnętrznej w celu uzyskania wymaganej grubości, która odpowiada grubości paska. Proces szlifowania slabów stosowany jest także, aby zapewnić pełną jednorodność powierzchni slabu, która będzie stanowić bazę dla kształtowania w niej właściwego profilu paska. Następnie obrobiony slab jest cięty na półprodukty odpowiadające na szerokość wymiarom gotowych pasków – powstają tzw. paski bez profilu. W celu nadania odpowiedniego profilu paski są ponownie szlifowane z użyciem specjalnych narzędzi, tzw. kół szlifierskich pokrytych powłoką diamentową. W procesie profilowania paskom nadawany jest kształt oraz następuje odpowiednie ukierunkowanie i ekspozycja włókien będących składnikami mieszanek gumowych. W ten sposób tworzy się odpowiednia warstwa, która będzie współpracować z powierzchnią koła napędowego, zapewniając cichą pracę paska bez poślizgu. Chociaż wytworzenie takiego paska wymaga sporo zaangażowania, pracuje on cicho i długo, zwiększając żywotność nie tylko samego silnika, ale i innych agregatów współczesnego samochodu. Opisany proces produkcyjny stosowany jest także do produkcji w zakładzie w Legnicy najnowszej generacji pasków Micro-V HORIZON, które właśnie ukazały się na rynku i – jak zapewniają inżynierowie firmy – są jeszcze bardziej trwałe, elastyczne i ciche w stosunku do konkurencji.
Elastyczność produkcji jest imponująca. W Legnicy produkowanych jest prawie 5000 różnych pasków. Pomimo tego ogromu produkcja nie sprawia wrażenia obciążającej pracowników. Dzięki systemowi informatycznemu pracownik otrzymuje pełne informacje o tym, co ma zrobić z tym czy innym surowcem. Na każdym kroku widać też zabiegi kontrolne, wykonywane przez samych operatorów maszyn, jak i specjalistów z działu jakości. Gotowe paski trafiają do magazynu przejściowego, buforowego. Jego zadaniem jest jedynie ułatwić pracę działu logistyki. Zamówienia na paski są bowiem realizowane na bieżąco. Tak jak płynnie zmienia się produkcja samochodów, podobnie musi reagować firma Gates. O tym, jaki pasek klinowy będzie potrzebny, de facto decyduje klient zakupujący samochód – gdy wybiera jeden z rodzajów silnika, pośrednio wybiera też do niego pasek. Czas oczekiwania na gotowy pojazd sięga obecnie 4-8 tygodni. Przed tym terminem wszystkie komponenty pojazdu muszą znaleźć się na linii produkcyjnej, w tym paski. A w celu redukcji kosztów magazyny wręcz nie istnieją – są na kołach ciężarówek. Po odjęciu montażu, transportu gotowego pojazdu i ewentualnego oczekiwania na placu dealera zostaje naprawdę niewiele dla dostawców komponentów, takich jak Gates. Dlatego firma dużą wagę przykłada do logistyki. Konfekcjonowanie pasków to „pestka” przy pakowaniu zestawów naprawczych. Złożone z kilku do kilkunastu różnych części „kity” powstają na specjalnym stanowisku. Znajdujący się tam pracownicy pobierają elementy wskazane przez zielone lampki i kompletują w opakowaniu. Pozostaje już tylko wysyłka. Zwiedzając zakład, trudno nie docenić osiągnięć firmy Gates. Guma nie jest wdzięcznym surowcem, a powstają z niej tak potrzebne paski i to najwyższej jakości. Gates posiada certyfikacje systemów zarządzania: ISO 9001, ISO/TS 16949, ISO 14001 i OHSAS 18001, a dzięki swoim rozwiązaniom firma uzyskała na całym świecie status „uprzywilejowanego dostawcy” oraz liczne nagrody przyznawane przez kluczowych klientów potwierdzające najwyższą jakość produkcji.
Łukasz Lubnau
Komentarze (0)