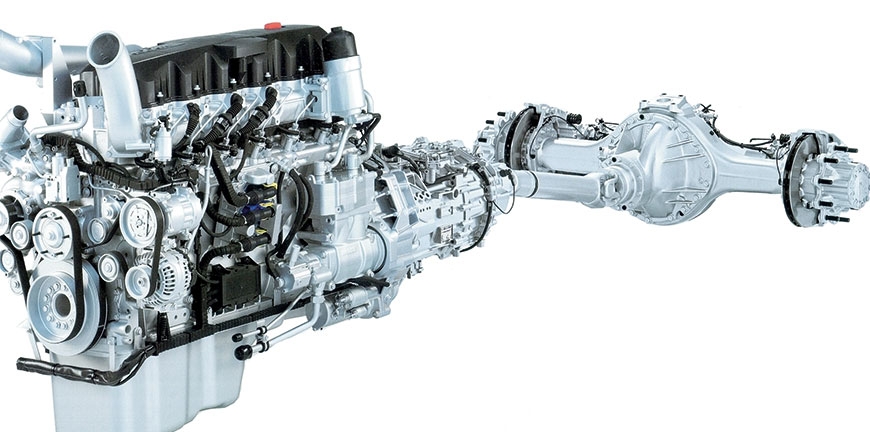
Rys. 1. Zespoły układu napędowego samochodu ciężarowego DAF serii CF (źródło: DAF).
Diagnozowanie mechanicznych skrzyń biegów sprowadza się do prawidłowej interpretacji informacji uzyskanych od użytkownika pojazdu oraz zebranych dostępnymi metodami (najczęściej organoleptycznymi) i podczas jazdy testowej (badań drogowych). Trudności w przełączaniu biegów występują w przypadku nadmiernego zanieczyszczenia oleju i odkształcenia elementów mechanizmu zmiany biegów. Występujące sporadycznie lub stale samoczynne wyłączanie się biegów podczas jazdy może świadczyć o uszkodzeniu synchronizatorów lub mechanizmu przełączania biegów. Nadmierny hałas występujący podczas zmiany biegów jest często spowodowany uszkodzonymi synchronizatorami, wodzikami lub widełkami mechanizmu zmiany biegów. Stwierdzone wycieki oleju mogą być spowodowane pęknięciem obudowy, uszkodzeniem pierścieni uszczelniających lub nieszczelnością korków spustowych i kontrolnych.
Diagnozowanie automatycznych skrzyń biegów (rys. 4) obejmuje wykonanie niżej wymienionych czynności:
- kontrolę przekładni hydrokinetycznej polegającą przede wszystkim na sprawdzeniu szczelności obudowy,
- sprawdzenie prawidłowości przełączania biegów (wykonuje się podczas próby drogowej lub podczas testu na hamowni podwoziowej),
- pomiar ciśnienia oleju (uzyskanie informacji o bieżącym stanie technicznym i prawidłowości współpracy elementów mechanicznych przekładni).
Diagnozowanie przekładni automatycznych polega przede wszystkim na właściwej interpretacji informacji uzyskanych od użytkownika pojazdu oraz zebranych podczas diagnozowania wstępnego i szczegółowego.
Badanie wstępne
Istotną czynnością, którą należy wykonać na początku, jest sprawdzenie podstawowych parametrów pracy silnika i układu przeniesienia napędu (prędkości obrotowej biegu jałowego silnika, temperatury płynu chłodzącego, poziomu oleju w skrzyni biegów i innych).
W następnej kolejności należy przeprowadzić diagnozowanie wstępne przekładni, które polega na wykonaniu następujących sprawdzeń:
- próby gaśnięcia silnika,
- próby czasu włączania biegów.
Podczas wykonywania próby gaśnięcia silnika pojazd powinien być zatrzymany. Polega ona na określeniu spadku wartości prędkości obrotowej silnika w trakcie przełączania biegów z pozycji N (luzu) do pozycji D (jada do przodu) lub R (jazda do tyłu) przy równoczesnym gwałtownym zwiększaniu nacisku na pedał przyspieszenia.
W trakcie wykonywania próby czasu włączania biegów należy zmierzyć czas od momentu przesunięcia przełącznika zmiany biegów z pozycji N do położenia D lub R. Ten parametr pozwala na orientacyjną ocenę zużycia okładzin ciernych hamulców i sprzęgieł oraz poprawności działania hydraulicznego układu sterowania.
Wartość zmierzonych podczas wykonywania tych prób parametrów nie powinna odbiegać od wartości dopuszczalnych określonych przez wytwórcę pojazdu.
Diagnozowanie szczegółowe
W czasie przeprowadzania szczegółowego diagnozowania automatycznych skrzyń biegów należy wykonać niżej wymienione czynności:
- kontrolę przekładni hydrokinetycznej,
- sprawdzenie prawidłowości przełączania biegów,
- pomiar ciśnienia oleju,
- sprawdzenie elektronicznego układu sterowania przekładni.
Kontrola przekładni hydrokinetycznej obejmuje przede wszystkim sprawdzenie szczelności obudowy i ocenę jej sprawności. Szczelność obudowy przekładni można sprawdzać po wprowadzeniu do jej wnętrza sprężonego powietrza o ciśnieniu 0,05-0,1 MPa, zaślepieniu wszystkich otworów i zanurzeniu jej w wodzie. W przypadku stwierdzenia nieszczelności skrzynię biegów uznaje się za niezdatną.
W celu kontroli sprawności przekładni hydrokinetycznej należy unieruchomić wałek wyjściowy skrzyni i zmierzyć obrotomierzem prędkość obrotową silnika przy pełnym otwarciu przepustnicy lub maksymalnym wydatku pompy wtryskowej. Jeżeli otrzymane wyniki pomiarów odbiegają od danych podawanych przez wytwórcę, można z dużym prawdopodobieństwem stwierdzić, że uszkodzona jest turbina lub pompa.
Sprawdzenie prawidłowości przełączania biegów można wykonać podczas próby drogowej (badania trakcyjne) lub na hamowni podwoziowej (badania stanowiskowe). Hamownia podwoziowa umożliwia m.in. pomiar prędkości pojazdu, prędkości obrotowej silnika i jego obciążenia. Następnie należy porównać uzyskane wyniki pomiarów z danymi dostarczonymi przez wytwórcę w programach testujących.
Wartość ciśnienia oleju jest parametrem diagnostycznym, który pozwala uzyskać istotne informacje o stanie technicznym i prawidłowości współpracy części mechanicznych przekładni. Wartość tego parametru może także informować (w ograniczonym zakresie) o funkcjonowaniu elektronicznego układu sterującego. Sprzęt diagnostyczny niezbędny do wykonania pomiaru ciśnienia oleju dostarczają wytwórcy pojazdów i automatycznych skrzyń biegów.
Kolejną czynnością jest diagnozowanie elektronicznego układu sterowania przekładni. Podstawowe elementy systemu diagnostycznego skrzyni biegów Voith DIWA.3 pokazano na rys. 5. Program diagnostyczny pracuje w czasie rzeczywistym i może współpracować z testerem diagnostycznym lub dowolnym komputerem klasy PC (np. laptopem) bez pośrednictwa dodatkowych interfejsów. Przekładnie automatyczne sterowane elektronicznie umożliwiają odczytanie, za pomocą testera podłączonego do gniazda diagnostycznego, zarejestrowanych kodów usterek. Ponieważ automatyczne skrzynie biegów wyposażone są w różne czujniki i własną pamięć, możliwa jest analiza zarejestrowanych w trakcie pracy przebiegów wybranych parametrów w funkcji czasu. Jeżeli podczas eksploatacji wystąpią różnice między wartościami rzeczywistymi tych parametrów a wartościami dopuszczalnymi, to są one rejestrowane w pamięci sterownika i wyświetlane za pomocą testera w postaci kodów usterek.
Funkcje systemu diagnostycznego automatycznych skrzyń biegów są nierozłącznie związane z funkcjami zastosowanego sterownika. Na przykład dla sterownika stosowanego w przekładniach automatycznych Voith DIWA.3 (autobusy miejskie) funkcje systemu można podzielić na następujące grupy logiczne [1]:
- diagnozowanie elementów peryferyjnych, to jest urządzeń połączonych ze skrzynią wiązkami elektrycznymi (ocena stanu przewodów elektrycznych i nadajników),
- diagnozowanie elementów składowych przekładni (zawory elektrohydrauliczne, przekaźniki, czujniki prędkości obrotowej i temperatury),
- zapamiętywanie i odczytywanie usterek (różny sposób sygnalizowania usterek w zależności od nadanego im priorytetu, odczytywanie usterek za pomocą programu diagnostycznego lub lampki kontrolnej),
- identyfikacja sterownika i elementów peryferyjnych (np. typ sterownika, dane wprowadzone do pamięci sterownika),
- badania trakcyjne pojazdu (testowanie elementów przekładni pod obciążeniem, udokumentowanie aktualnego stanu technicznego),
- niezależne nadzorowanie stanów krytycznych przekładni (np. nieoczekiwana jazda do tyłu przy wciśniętym przycisku D, dodatkowy procesor włączy wówczas automatycznie bieg neutralny),
- prognozowanie zużycia elementów ciernych – miarą zużycia jest wartość ciśnienia w siłowniku hydraulicznym podczas włączania sprzęgła ciernego (czas poślizgu podczas włączania zależy od ciśnienia w siłowniku).
Komentarze (0)