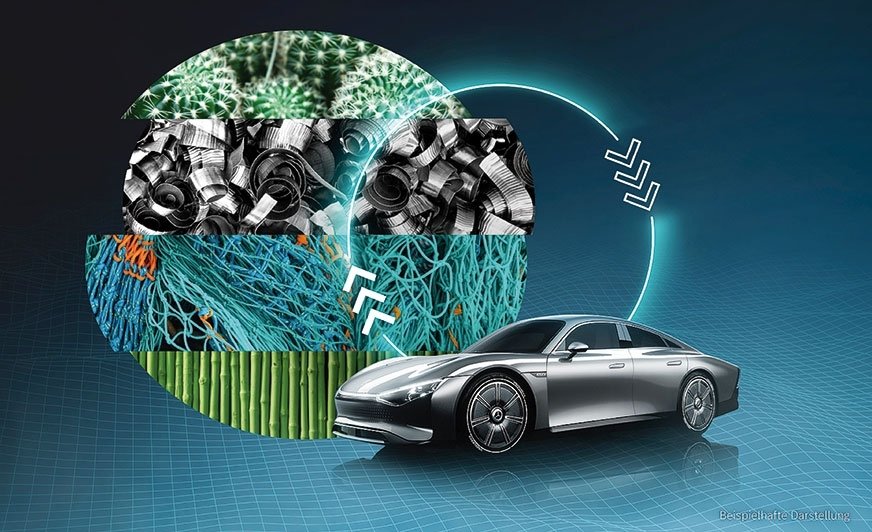
Gospodarka cyrkularna wkracza w nową erę – przekonują koncerny samochodowe. Przykładowo 14 października 2022 r. Grupa Renault ogłosiła utworzenie The Future Is NEUTRAL – nowego podmiotu w całości poświęconego gospodarce obiegowej dla osiągnięcia znacznie
Zwłaszcza jeśli chodzi o aluminium, które można używać w nieskończoność, bo ponowne wykorzystanie pokonsumenckiego złomu ma bardzo mały ślad węglowy. Okazuje się, że przetop dodaje tylko 5% początkowej energii używanej do produkcji aluminium pierwotnego.
Samochody należą do najczęściej poddawanych recyklingowi produktów konsumenckich na świecie, a odpowiedzialność środowiskowa to dziś jeden z najistotniejszych aspektów działalności biznesu motoryzacyjnego. Idzie generalnie o to, by przemysł samochodowy używał wyłącznie odnawialnych materiałów lub tych pochodzących z recyklingu. To o tyle istotne, że o ile produkty aluminiowe w budownictwie są wykorzystywane średnio przez 50 lat, więc mają długą żywotność, to propozycje przemysłu motoryzacyjnego „wytrzymują” jakieś 15 lat.
Z europejskiego punktu widzenia zagospodarowanie złomu aluminiowego jest szczególnie pożądane. Surowiec ten stanowi przedmiot handlu na całym świecie, jednak aby zaspokoić obecny popyt, UE importuje ok. 30% potrzebnego aluminium pierwotnego, a zapotrzebowanie wciąż rośnie. Idzie zatem o to, by jak największą pulę stanowiło aluminium, które może być ponownie wprowadzone do gospodarki obiegu zamkniętego. Tylko w ten sposób uda się znacząco ograniczyć ślad węglowy np. podczas produkcji karoserii samochodowych. Otóż proces recyklingu (przetopienia) aluminium wymaga jedynie 5% energii potrzebnej do produkcji pierwotnego metalu, co skutkuje emisją gazów cieplarnianych na poziomie „tylko” 0,5 t CO2 na tonę przetworzonego aluminium. Inaczej mówiąc, ponowne przetworzenie tony aluminiowego złomu pozwala zaoszczędzić 6 t boksytu i 9 t emisji CO2.
Dlaczego zbiórka aluminiowego złomu zyskała na znaczeniu?
Zdaniem ekspertów spektakularne ożywienie gospodarki po załamaniu z 2020 r. to główny czynnik wpływający na światowy rynek aluminium. Okazuje się, że wzrost popytu i zakłócenia podaży wywindowały ceny metalu do najwyższego poziomu w ostatnich kilkunastu latach. Według European Aluminium – organizacji branżowej z siedzibą w Brukseli – w latach 2021-2022, kiedy ceny energii zaczęły rosnąć, Europa musiała zamknąć lub wstrzymać połowę produkcji aluminium pierwotnego, co odpowiada 1,1 mln ton.
W pespektywie długoterminowej, tj. do sądnego roku 2050, inaczej się po prostu nie da, by w sposób znaczący ograniczać ślad węglowy.
Generalnie na świecie mamy obecnie do czynienia z deficytem aluminium, co oznacza, że bieżąca produkcja nie zaspokaja popytu, więc tym bardziej liczy się odzysk tego materiału. Ostatnie badanie sugeruje, że zawartość aluminium w samochodach wzrośnie o 40% do 2028 r. Oznacza to, że firmy zajmujące się recyklingiem samochodów są na początku ścieżki wzrostu. Nie od dziś uważa się, że sektor motoryzacyjny jest w stanie lepiej niż jakikolwiek inny sprzyjać gospodarce tego drogiego surowca w obiegu zamkniętym. To stąd wymóg, by projektować pojazdy tak, by poszczególne komponenty z tego cennego materiału udało się wymontować, dając w ten sposób szansę na ich drugie życie. I stąd apel o inteligentny demontaż w celu maksymalizacji wartości dodanej tegoż materiału.
Samochód poddany recyklingowi skrywa ok. 125 kg aluminium
Lekkość samochodów była tematem badań inżynierów łamiących sobie głowę do czasu, gdy okazało się, że materiały ze stopów aluminium mogą znacząco odchudzić karoserie. Jak bardzo odchudzić? Aluminiowa karoseria samochodu jest o ponad 40% lżejsza od wyrobów stalowych, więc redukcja masy dzięki użyciu jej zamiast stali do produkcji jest znacząca. Na polu efektywności paliwowej taka karoseria zyskuje na znaczeniu!
Przyjęło się szacować, że jeśli masa pojazdu zostanie zmniejszona o 10%, wydajność paliwową można zwiększyć o 6-8%. A skoro aluminium spełnia założenia gospodarki obiegu zamkniętego, ma bardzo mały ślad węglowy, to nie od dziś uchodzi za bardzo obiecujący trop poszukiwań konstruktorów – nie tylko w motoryzacji. Aluminium to jeden z najbardziej ekologicznych surowców na świecie. Posiada wiele zalet: jest nietoksyczny, wyjątkowo lekki, podatny na obróbkę i odporny na korozję. Idealnie nadaje się również do ponownego wykorzystania – poddany recyklingowi nie traci swoich unikatowych właściwości.
Do wyobraźni przemawiają kolejne wyliczenia: na każde 100 kg zmniejszenie masy własnej pojazdu, zużycie paliwa na 100 km można zmniejszyć o 0,3-0,6 l. Z punktu widzenia kosztów eksploatacyjnych ponoszonych przez konsumenta to niebagatelny zysk.
W celu optymalizacji wydajności ekonomicznej i środowiskowej branży motoryzacyjnej nadwozia mają być projektowane tak, by łatwiej było oddzielać np. elementy stalowe od aluminiowych
Zamknięcie pętli w recyklingu
Dlaczego aluminium jest jak bank energii? Ponieważ jest drogie tylko przez chwilę. Po wyprodukowaniu można go używać w nieskończoność, a ponowne wykorzystanie pokonsumenckiego złomu aluminiowego ma bardzo mały ślad węglowy.
– Ilość energii pobieranej do ponownego wykorzystania aluminium z recyklingu jest nawet o 95% niższa niż tej potrzebnej do wytworzenia aluminium pierwotnego – potwierdza Marco Philippi, dyrektor strategii zaopatrzenia w fabryce Audi w Neckarsulm.
W fabryce Audi w Neckarsulm zamknięty obieg aluminium wprowadzono już w roku 2017. Ścinki blachy aluminiowej powstające w tłoczni są przekazywane z powrotem do dostawcy. Ten przerabia je na blachę aluminiową równorzędnej jakości, a Audi wykorzystuje ten odzyskany materiał w produkcji.
Jak wygląda recykling aluminiowego złomu, tj. nie tylko karoserii samochodowych? Na początku aluminium jest selekcjonowane z reszty odpadów, np. z tworzyw sztucznych. Separacja magnetyczna oddziela metal od aluminium. Po przetransportowaniu do recyklera jest rozdrabniane na cząstki i strzępione na płatki, a następnie przesiewane w sitach w celu usunięcia zanieczyszczeń, by następnie metodą termiczną usunąć powłoki lakierowane, farby i inne zanieczyszczenia. Potem następuje ponowne przesiewanie, wreszcie topienie surowca w piecach, rafinowanie i filtrowanie stopionego aluminium. Finałem jest odlewanie (produktów czy półproduktów) oraz walcowanie do postaci arkuszy.
Zakład w Neckarsulm stosuje taki zamknięty obieg aluminium, współpracując z dwoma dostawcami, przez co zwiększa się ilość ponownie wykorzystywanego aluminium. Pozwoliło to w 2019 r. zredukować emisję CO2 o około 150 tys. ton – o 2/3 więcej niż rok wcześniej. W zakładach w Ingolstadt i w Győr również wprowadzono zamknięty obieg, a w kolejnych zakładach i liniach modelowych nastąpi to lada moment. Odzyskane aluminium jest obecnie wykorzystywane do produkcji elementów karoserii Audi A3, A4, A5, A6, A7 i A8, a także podzespołów do Audi e-tron i e-tron Sportback.
Karoseria ASF: dokładnie tyle materiału, ile potrzeba
Dzięki konstrukcji ASF oraz inteligentnemu składowi zastosowanej kombinacji aluminium i najtwardszej stali karoseria Audi A8 waży jedynie 231 kg. Taka sama konstrukcja wykonana w całości ze stali ważyłaby ok. 40% więcej. Dzięki ASF ciężar własny Audi A8 3.0 TFSI quattro z normalnym rozstawem osi wynosi jedynie 1830 kg. Wśród samochodów tego segmentu to rekordowo niska waga, biorąc pod uwagę pojazdy z napędem na cztery koła.
Jak odchudzić karoserię bez utraty pożądanych cech wytrzymałościowych i gdzie tkwi przewaga takiej konstrukcji? Źródłem inspiracji dla inżynierów przed z górą 30 laty była natura. Zauważyli, że pszczoły w ulu zużywają do budowy plastra dokładnie tyle materiału, ile potrzeba, tak by stworzyć jak najlepszą konstrukcję. Korzystając z tej wiedzy, eksperci Audi stworzyli karoserię ASF, zbudowaną z prasowanych profili i z elementów odlewanych podciśnieniowo. Z tak stworzoną konstrukcją połączone są blachy tworzące pokrycie dachu, podłogę i elementy boczne, będące jednocześnie jej wzmocnieniem. Zależnie od zadań, poszczególne komponenty charakteryzują się różnymi formami i przekrojami.
ASF (Audi Space Frame) w ciągu minionych dwóch dziesiątków lat podbiła rynek. Kolejne modele, w których ją zastosowano, to: Audi A2 (2000), Audi TT (2006), Audi R8 (2008), a także dwie następne generacje Audi A8 (2002 i 2010). Łącznie od 1994 r. Audi sprzedało ponad 750 tysięcy samochodów z karoserią ASF – wykonaną wyłącznie lub częściowo z aluminium.
Zmniejszanie skutków wycofania pojazdów z eksploatacji
Chociaż ponad 85% części i materiałów pojazdów jest poddawanych recyklingowi i ponownie wykorzystywanych pod koniec okresu ich użytkowania, uzyskanie niektórych elementów może być niewspółmiernie energochłonne i pracochłonne. Producenci samochodów pracują oczywiście nad zminimalizowaniem negatywnego wpływu na klimat zgodnie z Ramową Konwencją Narodów Zjednoczonych w sprawie Zmian Klimatu (Porozumienie Paryskie).
Przykładowo, aby osiągnąć swój cel w zakresie neutralności pod względem przekazywania dwutlenku węgla do atmosfery, Ford koncentruje się na trzech obszarach, które odpowiadają za około 95% emisji CO2. Mowa o produkowanych przez firmę samochodach, globalnej działalności i łańcuchu dostaw. Już dziś dzięki poprawionej efektywności energetycznej, oszczędnościach w zakładach i procesach produkcyjnych ślad węglowy wytwarzany przez producenta zmniejszył się o 35% od 2017 r. Obecny cel produkcyjny zakłada natomiast redukcję emisji o 18% do roku 2023.
Holistyczna ocena zrównoważonego rozwoju wszystkich materiałów obejmuje nie tylko wnętrze pojazdu, ale także nadwozie i karoserię. Szczególną uwagę zwraca się na materiały, które w produkcji są wyjątkowo energochłonne pod względem emisji CO2, takie jak stal i aluminium.
Nad dekarbonizacją łańcucha dostaw konsekwentnie pracuje się zwłaszcza w zakresie wykorzystania aluminium. Wraz z wprowadzeniem na rynek Mercedesa-AMG SL w blokach startowych pojawiła się kolejna światowa premiera. W nadwoziu białego Mercedesa-AMG SL po raz pierwszy zastosowano odlewy strukturalne ze stopów odlewniczych wykonanych w 100% z przetworzonego aluminiowego złomu. W produkcji aluminium pozwala to zaoszczędzić ponad 90% emisji CO2. I okazuje się, że taki sygnał dla konsumentów dóbr luksusowych jest dziś bardzo pożądany.
Jeszcze przed wybuchem epidemii jasne było, że konsumenci luksusu zmieniają się na dobre. Byliśmy świadkami nie tylko odejścia od dziedziczenia bogactwa na rzecz samodzielnego zdobywania fortuny, oczywiste było również, że pula konsumentów dóbr luksusowych stawała się coraz młodsza, bardziej świadoma ekologicznie, coraz bardziej obeznana z technologią i nie zachwycała się już gromadzeniem bogactwa czy posiadaniem. Z millenialsami i prawdziwymi cyfrowymi tubylcami (generacja Z) napędzającymi ten trend implikacje dla wydatków na luksus są ogromne.
W postpandemicznym świecie, w którym sprzedaż dóbr luksusowych prawdopodobnie spadnie, w szczególności młodsi z pokolenia Z domagają się bardziej otwartej i szczerej komunikacji. A to kolejna szansa na upowszechnienie tego stopu.
To młodzi podyktują następną generację doświadczeń motoryzacyjnych
Kiedyś luksus był definiowany przez nadmiar i przepych. Dziś? Pod wpływem presji środowiska i zmieniających się wartości klientów znane marki luksusowe zaczęły wprowadzać do swojej narracji zrównoważony rozwój. Powstanie samochodów całkowicie elektrycznych jest bez wątpienia największą innowacją zakłócającą przemysł samochodowy klasy premium.
Ciągle mowa o aluminium, ale ten proces zaczyna dotykać także dekarbonizacji łańcucha dostaw stali. W ramach Ambition 2039 Mercedes-Benz realizuje cel dekarbonizacji łańcucha dostaw stali, świadomie skupiając się na unikaniu i redukcji emisji CO2. W Vision EQXX zastosowano stal płaską o obniżonej zawartości CO2 firmy Salzgitter Flachstahl GmbH, która jest produkowana w 100% ze złomu w elektrycznym piecu łukowym. Niskostopowe gatunki o ponad 60-procentowej redukcji emisji CO2 są jednocześnie integrowane w pierwszych zastosowaniach w obecnej Klasie A i Klasie E, nowej Klasie C i EQE. Tym samym Mercedes-Benz jest pierwszym producentem pojazdów, który wprowadził do produkcji seryjnej tę oszczędzającą zasoby naturalne blachę o obniżonej emisji CO2. Współpraca Mercedes-Benz AG i Salzgitter Flachstahl GmbH została wyróżniona Materialica Design + Technology Gold Award 2021 w kategorii „Wydajność CO2”. Ponadto Mercedes-Benz pozyskuje stal od amerykańskiego dostawcy Big River Steel, który redukuje emisję CO2 przy produkcji o ponad 70%, a to dzięki wykorzystaniu złomu stalowego z recyklingu i energii odnawialnej. Dla porównania, stal produkowana przy użyciu klasycznego wielkiego pieca emituje średnio ponad 2 t CO2 na tonę.
Stal bez CO2 już od 2025 roku?
W kolejnym kroku od 2025 roku Mercedes-Benz będzie stosował w różnych modelach pojazdów stal niemal całkowicie wolną od CO2, a to dzięki produkcji z wykorzystaniem wodoru zamiast węgla koksującego. W tym celu firma stała się pierwszym producentem samochodów, który objął udziały w szwedzkim start-upie H2 Green Steel (H2GS).
W ramach partnerstwa ze szwedzkim producentem stali SSAB już w tym roku planowane są pierwsze prototypowe części do aplikacji body-in-white wykonane ze stali niezawierającej kopalin. Partner będzie produkował w swoim zakładzie pilotażowym w Lulea stal z żelazem wytwarzanym przy użyciu wodoru, która może być stosowana w istotnych dla bezpieczeństwa obszarach karoserii.
Rafał Dobrowolski
Fot. Audi, Grupa Renault
Komentarze (0)