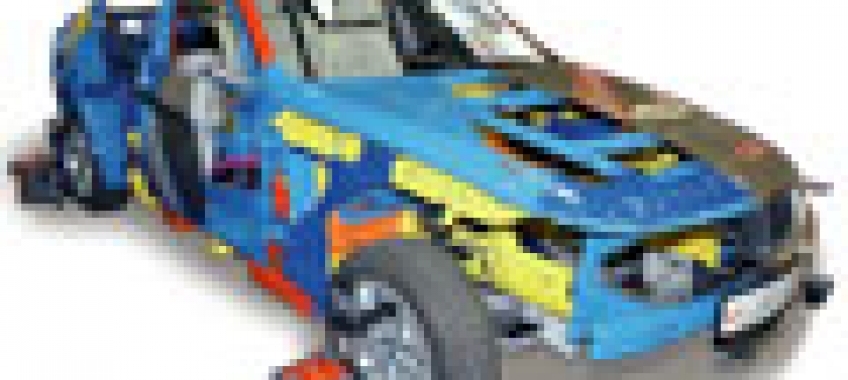
Głównym wyzwaniem dla branży automotive jest oczywiście odchudzanie karoserii. Im mniejsza waga pojazdu, tym lepsze osiągi, mniejsze zużycie paliwa i mniejsza emisja CO2, więc i energochłonność przemysłu motoryzacyjnego. Już kiedyś rewolucją były blachy wysokoprężne, dzięki którym udało się obniżyć masę karoserii o ok. 20 procent. Czy w przyszłości czeka nas rewolucja kompozytowa? Biura projektowe od kilku dekad poważnie myślą o adaptacji rozwiązań stosowanych w produkcji dóbr ekskluzywnych na potrzeby branży motoryzacyjnej. Z kompozytów od lat budowane są rakiety tenisowe, narty czy deski snowboardowe i od całkiem niedawna także modele samochodów ekskluzywnych producentów. Przykładowo, Mercedes-Benz klasy C zbudowany jest m.in. z ponad 30 części wykonanych z włókien naturalnych, ale prawdziwy przełom odnotowano 2 lata temu. W konstrukcji niewielkiego sportowego samochodu Artega GT wykorzystano m.in. poliuretanowe systemy typu duromer koncernu Elastogran. Dziś głównym producentem chemii samochodowej i materiałów kompozytowych jest firma BASF. Elastogran to firma-córka, która na potrzeby niemieckiego koncernu stworzyła opatentowany proces technologiczny produkcji poszyć kompozytowych. Najciekawiej wygląda konstrukcja prototypowej maski silnikowej. Pokrywa silnika musi być przecież umocowana do szkieletu karoserii. Poszycie jest więc co prawda sklejane z dwóch płaszczyzn kompozytowych, ale pomiędzy nie „wstawiane” są belki usztywniające ze stali. Takie użebrowanie zapobiega drganiom płaszczyzny i wzmacnia całość w miejscach mocowanie zawiasów. Dodatkowo, aplikowana jest w tą przestrzeń (między kompozytami) pianka wygłuszająca i izolująca. Mamy więc do czynienia z konstrukcją hybrydową. Karoseria Artega GT została zaś wytłoczona w całości z włókna węglowego, które trafiło na ramę przestrzenną ze stopów aluminium. Zaawansowane rozwiązanie znacząco ograniczyło masę pojazdu do 1100 kg. Błotniki, tylna część pojazdu, jego przód i elementy boczne wykonane zostały z Elastolitu, czyli wzmocnionego włóknem węglowym mikrokomórkowego poliuretanu. Odznacza się on ponadprzeciętną solidnością i zwartością budowy oraz bardzo dobrą odpornością na uderzenia – to nawet w ekstremalnie niskich temperaturach. Dlaczego nie zaadaptować walory kompozytu na potrzeby wielkoseryjnej produkcji? Przed kilkoma dekadami poważnym ograniczeniem był brak przemysłowej metody wytwarzania kompozytowych karoserii samochodowych. Dziś barierą jest już w zasadzie tylko kosztowność technologii i brak wypracowanych technologii napraw. Pomimo faktu, że kompozyty wykazują się wyjątkowo pożądanymi parametrami wytrzymałościowymi i są wyjątkowo lekkie, problemem jest łączenie elementów karoserii w jedną całość. Dlaczego? Stalowe poszycia można spawać, a dzięki plastyczności metalu można przywracać im pierwotny kształt itp.
- Tymczasem naprawa elementów kompozytowych jest w zasadzie niemożliwa, zwłaszcza tych z włókien węglowych. Niewskazane są także wszelkie reparacje elementów z siatki stalowej wtopionej w materiał PU, czyli np. elementów wzmocnień zderzaków – podkreśla Toni Seidel z firmy C.T.S. Sp. z o.o. - Na dzisiaj tylko kompozyty z włókna szklanego można naprawiać.
Kompozyt
Jest wiele definicji kompozytu, jednak ich istota jest taka sama. Kompozyty to materiały składające się z co najmniej dwóch różnych pod względem chemicznym materiałów z wyraźną granicą rozdziału między komponentami (fazami). Struktura taka ma lepsze właściwości, a czasem nawet nowe (dodatkowe) w stosunku do komponentów użytych osobno lub wynikające z prostego sumowania tych właściwości. „Zewnętrznie” kompozyt pozostaje nadal materiałem monolitycznym, choć w ich strukturze ciągle widoczne są granice między komponentami. Zastosowanie materiałów kompozytowych w pojazdach różnego typu pozwoliło na zwiększenie wytrzymałości i sztywności przy jednoczesnym zmniejszeniu masy elementów. Ich zaletą jest wysoka sztywność i wytrzymałość mechaniczna, łatwość montażu i wysoka odporność na typową bolączkę tradycyjnych materiałów, czyli „zmęczenie” i korozję. Nie bez znaczenia, zwłaszcza w budowie szybkich bolidów, jest skuteczne tłumienie drgań.
Zwiększony udział kompozytów pozwala ograniczyć zużycie materiałów nieodnawialnych (kopalnianych). Wszystko to przekłada się na czynniki ekologiczne i ekonomiczne, które w obecnych czasach znacznie bardziej brane pod są pod uwagę niż miało to miejsce w poprzednich dekadach. Pomimo kryzysu w gospodarce światowej, potrzeby na różnorakie rodzaje kompozytów nie maleją. Według ocen specjalistów, do 2013 roku na całym świecie będziemy notować rokroczny wzrost rzędu 4% zapotrzebowania na tego typu materiały. Już dziś przyjmuje się, że nawet do 28% wszystkich kompozytów stosowanych jest jako elementy konstrukcyjne w motoryzacji, budownictwie i lotnictwie. Co ciekawe też, producenci wyrobów kooperacyjnych dla przemysłu samochodowego upatrują impulsów do poprawy sytuacji właśnie w popularyzacji materiałów kompozytowych, a szerzej: w zainteresowaniu lekkimi pojazdami elektrycznymi. Dla tych ostatnich wymóg obniżenia masy jest zewsząd pożądany. Prace nad stworzeniem wielkogabarytowych elementów karoserii są już dziś bardzo zaawansowane.
Czego mogą się bać tradycyjne warsztaty samochodowe?
Co by nie sądzić o wizji wielkoseryjnej produkcji samochodów wszelkich typów z karoserią kompozytową – jedno jest pewne. Takie karoserie (dziś) są nienaprawialne! Brak też na razie metod naprawczych takich elementów. Łączone są fabrycznie do karoserii nitami, śrubami i klejem. Takie elementy są już gotowe do aplikacji lakieru. Co takie zmiany oznaczają dla branży, zwłaszcza dla warsztatów zajmujących się dziś naprawami blacharsko-lakierniczymi?
- Adhezja kompozytów jest bardzo dobra, więc nie widzę problemów z wymalowaniami cząstkowymi – informuje Toni Seidel. - Najbardziej prawdopodobne jest dziś, że takie uszkodzone elementy w postaci przełamań, wgnieceń nie będą jednak podlegać naprawie! Pozostaje wymiana na nowy element, co na pewno jest podyktowane zyskiem producenta; ten chce sprzedawać wymienne poszycia kompozytowe. Można mieć tylko nadzieję, że tak jak dziś spawamy owiewki motocykli, tak w przyszłości doczekamy się napraw elementów nienośnych, jakimi są poszycia karoserii samochodowych. Oczywiście, nie będzie problemu z wymontowaniem zniszczonych elementów poszycia. Technologia przypomina tą stosowaną i omawianą przy okazji wymiany poszycia dachu.
Opracował: Rafał Dobrowolski
Zdjęcia: CTS
- Tymczasem naprawa elementów kompozytowych jest w zasadzie niemożliwa, zwłaszcza tych z włókien węglowych. Niewskazane są także wszelkie reparacje elementów z siatki stalowej wtopionej w materiał PU, czyli np. elementów wzmocnień zderzaków – podkreśla Toni Seidel z firmy C.T.S. Sp. z o.o. - Na dzisiaj tylko kompozyty z włókna szklanego można naprawiać.
Kompozyt
Jest wiele definicji kompozytu, jednak ich istota jest taka sama. Kompozyty to materiały składające się z co najmniej dwóch różnych pod względem chemicznym materiałów z wyraźną granicą rozdziału między komponentami (fazami). Struktura taka ma lepsze właściwości, a czasem nawet nowe (dodatkowe) w stosunku do komponentów użytych osobno lub wynikające z prostego sumowania tych właściwości. „Zewnętrznie” kompozyt pozostaje nadal materiałem monolitycznym, choć w ich strukturze ciągle widoczne są granice między komponentami. Zastosowanie materiałów kompozytowych w pojazdach różnego typu pozwoliło na zwiększenie wytrzymałości i sztywności przy jednoczesnym zmniejszeniu masy elementów. Ich zaletą jest wysoka sztywność i wytrzymałość mechaniczna, łatwość montażu i wysoka odporność na typową bolączkę tradycyjnych materiałów, czyli „zmęczenie” i korozję. Nie bez znaczenia, zwłaszcza w budowie szybkich bolidów, jest skuteczne tłumienie drgań.
Zwiększony udział kompozytów pozwala ograniczyć zużycie materiałów nieodnawialnych (kopalnianych). Wszystko to przekłada się na czynniki ekologiczne i ekonomiczne, które w obecnych czasach znacznie bardziej brane pod są pod uwagę niż miało to miejsce w poprzednich dekadach. Pomimo kryzysu w gospodarce światowej, potrzeby na różnorakie rodzaje kompozytów nie maleją. Według ocen specjalistów, do 2013 roku na całym świecie będziemy notować rokroczny wzrost rzędu 4% zapotrzebowania na tego typu materiały. Już dziś przyjmuje się, że nawet do 28% wszystkich kompozytów stosowanych jest jako elementy konstrukcyjne w motoryzacji, budownictwie i lotnictwie. Co ciekawe też, producenci wyrobów kooperacyjnych dla przemysłu samochodowego upatrują impulsów do poprawy sytuacji właśnie w popularyzacji materiałów kompozytowych, a szerzej: w zainteresowaniu lekkimi pojazdami elektrycznymi. Dla tych ostatnich wymóg obniżenia masy jest zewsząd pożądany. Prace nad stworzeniem wielkogabarytowych elementów karoserii są już dziś bardzo zaawansowane.
Czego mogą się bać tradycyjne warsztaty samochodowe?
Co by nie sądzić o wizji wielkoseryjnej produkcji samochodów wszelkich typów z karoserią kompozytową – jedno jest pewne. Takie karoserie (dziś) są nienaprawialne! Brak też na razie metod naprawczych takich elementów. Łączone są fabrycznie do karoserii nitami, śrubami i klejem. Takie elementy są już gotowe do aplikacji lakieru. Co takie zmiany oznaczają dla branży, zwłaszcza dla warsztatów zajmujących się dziś naprawami blacharsko-lakierniczymi?
- Adhezja kompozytów jest bardzo dobra, więc nie widzę problemów z wymalowaniami cząstkowymi – informuje Toni Seidel. - Najbardziej prawdopodobne jest dziś, że takie uszkodzone elementy w postaci przełamań, wgnieceń nie będą jednak podlegać naprawie! Pozostaje wymiana na nowy element, co na pewno jest podyktowane zyskiem producenta; ten chce sprzedawać wymienne poszycia kompozytowe. Można mieć tylko nadzieję, że tak jak dziś spawamy owiewki motocykli, tak w przyszłości doczekamy się napraw elementów nienośnych, jakimi są poszycia karoserii samochodowych. Oczywiście, nie będzie problemu z wymontowaniem zniszczonych elementów poszycia. Technologia przypomina tą stosowaną i omawianą przy okazji wymiany poszycia dachu.
Opracował: Rafał Dobrowolski
Zdjęcia: CTS
Komentarze (0)