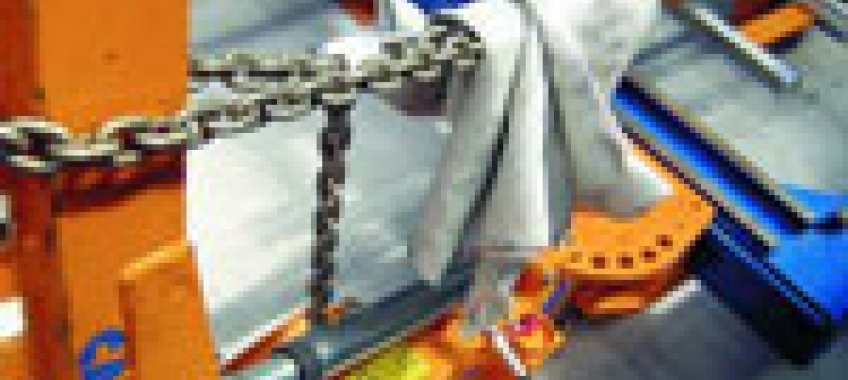
– prostowanie nadwozia (2)
Wiedza z zakresu materiałów użytych do budowy elementów nośnych współczesnych pojazdów jest nieodzowna – o czym pisaliśmy w pierwszej części artykułu dotyczącego przykładania sił rozciągających do usuwania deformacji typu “banan”. Do mierzenia odkształceń płyty podłogowej nieodzowne okazuje się posiadania nie tylko kart pomiarowych. Wysoka kultura pracy ogranicza czasochłonność takich napraw i eliminuje niepotrzebne koszty.
Do lat dziewięćdziesiątych ubiegłego wieku konstrukcje nośne i poszycia samochodów osobowych budowane były niemal z jednego rodzaju stalowego materiału. Była to blacha nazywana z powodu swej plastyczności głębokotłoczną. Współczesne konstrukcje muszą spełniać coraz ostrzejsze normy z zakresu bezpieczeństwa biernego, więc udział blach głębokotłocznych maleje. Lekka, a zarazem sztywna karoseria z optymalizacją struktury sztywności jest wiodącym trendem w przemyśle motoryzacyjnym.
Aerodynamika i rozwój struktury karoserii
Pożądana cechą współczesnych pojazdów jest spełnienie oczekiwań wymogów aerodynamiki przy jednoczesnym wzroście odporności karoserii na deformacje. Sztywność karoserii rzutuje na kilka innych cech pojazdu jak: wytrzymałość, żywotność i bezpieczeństwo. Zbyt mała sztywność karoserii prowadzi do niepożądanych drgań i wibracji w karoserii, które dają się odczuć podczas jazdy. A że poprawa sztywności karoserii ma ogromne znaczenie świadczy wysiłek konstruktorów najnowszego Opla Vectry, w którym aż o 74 proc. poprawiono ten parametr, co ciekawe przy jednoczesnej poprawie sprężystości aż o 62 proc.! Podczas dynamicznego obciążenia częstotliwość drgań powyższej konstrukcji została obniżona poniżej 40Hz. W konstruowaniu karoserii Opla pomógł bardzo program komputerowy, który podzielił ją na “siatkę” 400 tys. elementów, dzięki czemu można było zdiagnozować lokalny rozkład sił.
Ciężki koc przerzucony na łańcuchach odciągów zamortyzuje siłę zrywającą w krytycznej sytuacji.
Istotne znaczenie w mocnej strukturze karoserii Opla Vectry ma oczywiście zastosowanie stali o wysokiej i podwyższonej wytrzymałości. Udział tych ostatnich zwiększył się z 9 do aż 52 proc. w porównaniu z poprzednim modelem. W słupkach A i B – czyli w miejscach, w których najprawdopodobniej przyjdzie nam naprawiać karoserię po uderzeniach bocznych – zastosowano stal borową charakteryzującą się najwyższym wskaźnikiem wytrzymałości na rozciąganie, nawet do 1700 Nmm. Konstrukcja progów wykonana jest w nowym Oplu ze stali typ “Dual Phasen” (DP) – twardej, wytrzymalszej i lżejszej o 1,5 kg od poprzedniej konstrukcji progów typu “Bake Hardening (BH stal), a przy tym dającej się łatwiej kształtować i obrabiać.
Dostęp do aktualnej bazy danych fabrycznych punktów pomiarowych to spory wydatek.
Techniki rozpoznawania stopów
Rozpoznawanie rodzajów stali będzie więc miało decydujące znaczenie dla niezależnych warsztatów, bo o ile współczesne technologie zdecydowanie ułatwiają wykonywanie napraw powypadkowych, to ich zakres ogranicza koszt takiej usługi; koszt aktualizacji bazy danych debiutujących modeli może być zbyt dużym obciążeniem dla niejednego nowoczesnego warsztatu. Jeśli warsztat nie dysponuje oryginalną dokumentacją techniczną, konieczne staje się zastosowanie innych, bardziej pracochłonnych metod identyfikacji użytych materiałów.
Przykładanie punktów do skrzywionej ramy.
- Oczywiście ze względów technologicznych łączenia blach różnych stopów nie wolno tego zagadnienia pomijać w procesie naprawczym. We wspomnianym Oplu blacharz natknie się na aż 15 różnych stopów, więc każdemu z nich odpowiadać będą ściśle określone zasady prostowania odkształceń a także odmienne techniki spawalnicze – uważa T. Seidel.
Podgrzewacz indukcyjny.
Dla odróżnienia blachy stalowej od aluminiowej (gdy obie pokrywa lakier) trzeba użyć magnesu stałego – najlepiej małych rozmiarów, ale najprościej można to ustalić na elementach które możemy podnieść ponieważ waga ich będzie się znacząco różnić ze wskazaniem na elementy aluminiowe które będą zdecydowanie lżejsze.
Prostowanie boczne karoserii skutkować może czasem odchyleniem kielichów zawieszenia – wtedy nieodzowne okaże się użycie siłowników rozpierających.
W elemencie z blachy głębokotłocznej po uderzeniu szpicem młotka powstanie wyraźnie wklęsłe wgniecenie. Przy stali o podwyższonej wytrzymałości młotek zostanie sprężyście odbity, a na materiale pozbawionym powłoki lakierniczej pojawi się najwyżej słabo widoczna rysa; zaś na stali borowej młotek nie pozostawi żadnych śladów. Inna metoda wymaga użycia ręcznej szlifierki. Przy lekkim szlifowaniu blachy głębokotłocznej iskry będą koloru białego. Materiał o podwyższonej wytrzymałości tworzy iskry żółte, a blachy borowane – iskry w charakterystycznym, głęboko pomarańczowym kolorze.
- Jednak najbardziej wiarygodne informacje na temat rodzaju stalowej blachy daje nowoczesna zgrzewarka z funkcją automatycznego testowania materiałów blacharskich metodą pomiaru charakterystycznej dla nich oporności elektrycznej. Uzyskany wynik wyświetla się natychmiast na czytniku urządzenia, oddzielnie dla każdej z występujących w tym miejscu metalowych warstw – dodaje T. Seidel.
Kultura pracy
Coraz większego znaczenia w dobie różnorodnych stopów budujących współczesne karoserie ma kultura pracy blacharza. Narzędzia blacharskie (młotki, klepaki) używane do napraw blach stalowych nie wolno nam używać do aluminiowego poszycia. Dziś technika lutospawania znajduje zastosowanie bezwzględnie w łączeniu poszyć nadwozia dzięki: niższej temperaturze procesu i małej degradacji powłoki cynkowej, natomiast dużej odporności spoiny na korozję. Sprężystość blach użytych do budowy podłużnic karoserii (np. ram) sprawia, że podgrzewanie indukcyjne – choć nie zalecane przez producentów przy naprawach powypadkowych – staje się czasem jedynym sposobem zachowania uzyskanego efektu naciągania ich siłownikami, bo te nie mają zwykle siły większej niż 10 ton. Przegrzanie podłużnic i innych wzmocnień karoserii jest niedopuszczalne, bo nieodwracalnie zmienia strukturę materiału i obniża sztywność karoserii. Z tych też względów niskotemperaturowe podgrzewanie prostowanych elementów niemal w całości wypiera dziś zupełnie użycie palnika. Podgrzewanie indukcyjne prostowanych elementów ogranicza zmianę struktury materiałów. W przypadku aluminium nie zaleca się podgrzewania elementu powyżej temp. 200OC i powyżej 450-500OC w przypadku pozostałych stopów.
Czasem nieodzowne okaże się podgrzanie miejscowe prostowanych podłużnic.
Opracowano na podstawie specjalnego wykładu wygłoszonego przez pana Toniego Seidla z firmy Car-o-Liner dla redakcji „Nowoczesnego Warsztatu”
Notował: Rafał Dobrowolski
Zdjęcia: R. Dobrowolski
Komentarze (0)