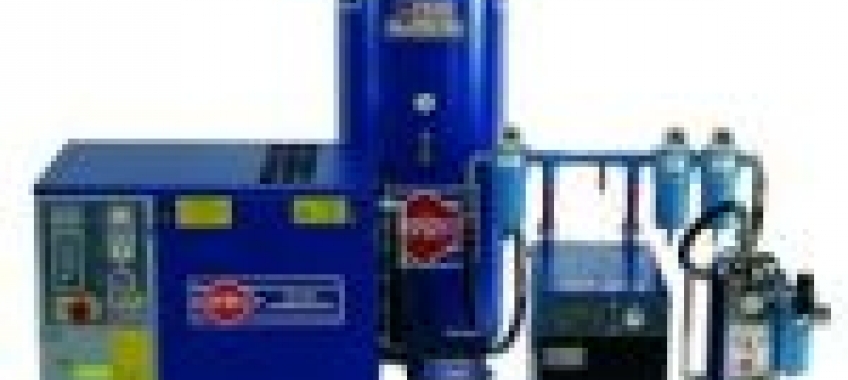
instalacja sprężonego powietrza powinna być tak dobrana, aby jej wielkość i wydajność odpowiadały zapotrzebowaniu na sprężone powietrze wszystkich pracujących w warsztacie maszyn i urządzeń.
Parametrami technicznymi niezbędnymi do rozpoczęcia jakichkolwiek prac projektowych instalacji są:
- ilość przewidywanych stanowisk odbiorczych,
- nominalne zużycie sprężonego powietrza na poszczególnych stanowiskach,
- wymagane ciśnienie robocze odbiorników (maszyn i urządzeń) na poszczególnych stanowiskach,
- długości poszczególnych odcinków przewodów (przewidywane usytuowanie stanowisk odbiorczych).
Podstawowym urządzeniem w całej instalacji jest sprężarka, która wytwarza sprężone powietrze. Kolejnym ważnym ogniwem systemu jest zbiornik ciśnieniowy. Najważniejszą funkcją zbiornika ciśnienia jest bilansowanie wydajności sprężarki z aktualnym zapotrzebowaniem powietrza w instalacji. Dzięki temu nie ma konieczności pracy ciągłej sprężarki, a jej włączaniem i wyłączaniem steruje wyłącznik ciśnieniowy w zależności od aktualnego ciśnienia sprężonego powietrza w zbiorniku. Zbiornik ciśnienia wyrównuje ponadto niekorzystne wibracje w instalacji, będące efektem pracy sprężarki tłokowej. Dla wstępnego ustabilizowania ciśnienia w instalacji sprężonego powietrza na przewodach odpływowych zbiornika ciśnienia instaluje się nastawne reduktory z manometrami. Obecnie w większości warsztatowych instalacji sprężonego powietrza wykorzystuje się ciśnienie robocze od 6 do 10 bar.
W przypadku konieczności korzystania w warsztacie jednocześnie z kilku urządzeń i narzędzi pneumatycznych rozmieszczonych w różnych, oddalonych znacznie od siebie miejscach warsztatu, niezbędne jest stworzenie rozbudowanej instalacji, zaopatrującej poszczególne stanowiska odbiorcze w sprężone powietrze. W związku z wymaganymi objętościowymi natężeniami przepływu i dopuszczalnymi spadkami ciśnienia należy właściwie dobrać rozmiar średnicy przewodów rurociągu zasilającego. W przeszłości wszystkie warsztatowe instalacje sprężonego powietrza wykonane były z rur stalowych. Obecnie zdecydowana większość nowych lub modernizowanych instalacji sprężonego powietrza w warsztatach wykonywana jest z tworzyw sztucznych. Za wykonywaniem instalacji z tworzyw sztucznych (głównie PCV, polietylen, polipropylen) przemawia odporność na korozję, a w związku z tym brak kondensacji zanieczyszczeń. Dodatkowymi zaletami wykonania instalacji sprężonego powietrza z tworzywa sztucznego są:
- cichsza niż w przypadku metalowej konstrukcji praca instalacji ze względu na lepsze tłumienie drgań,
- dłuższa żywotność,
- zdecydowanie krótszy czas montażu,
- wyższa estetyka wykonania,
- znacznie łatwiejsza możliwość ewentualnych przeróbek i modyfikacji.
Łatwość montażu i późniejszych modernizacji wynika z prostoty technologii montażu zastosowanych elementów. Zdecydowana większość stosowanych elementów instalacji to samozaciskowe i samouszczelniające się łączniki pozbawione połączeń gwintowanych. Dopiero na końcach instalacji poszczególnych stanowisk odbiorczych stosowane są systemowe końcówki ze znormalizowanymi gwintami do podłączenia zaworów, końcówek przyłączeniowych do węży elastycznych i innych elementów wyposażenia instalacji. W przypadku tworzenia nowej instalacji sprężonego powietrza w warsztacie, coraz częściej umieszcza się rurociąg doprowadzający, czyli główną jej część, pod posadzką zamiast rozwiązania z tradycyjną instalacją poprowadzoną na ścianach obiektu.
Na końcach instalacji w celu wygodnego i szybkiego łączenia odbiorników osadza się końcówki szybkozłączy.
Wytworzone i zmagazynowane w zbiorniku ciśnienia sprężone powietrze przed użyciem musi jeszcze zostać poddane pewnemu procesowi uzdatnienia. Uzyskuje się to poprzez przepływ sprężonego powietrza przez odpowiednie urządzenia uzdatniające. Sprężone powietrze może zawierać zanieczyszczenia pochodzące:
- z zasysanego powietrza – należą do nich cząstki zanieczyszczeń stałych oraz para wodna;
- ze sprężarki – należą do nich olej pochodzący ze smarowania oraz cząstki pyłu będące efektem ścierania się współpracujących elementów. Wszystkie substancje zanieczyszczające sprężone powietrze wytwarzane przez sprężarkę (zanieczyszczenia stałe, cząstki wody i oleju) bez ich wychwycenia i oddzielenia w instalacji mogłyby tworzyć mieszaninę, która stwarzałaby z pewnością spore niebezpieczeństwo dla stosunkowo precyzyjnych mechanizmów napędu pneumatycznego. Dlatego powietrze przed doprowadzeniem go do jakiegokolwiek rodzaju odbiornika musi być najpierw odpowiednio, adekwatnie do konkretnego przypadku przygotowane i uzdatnione poprzez:
- oczyszczenie z zanieczyszczeń mechanicznych (pyłu, rdzy), wody oraz oleju;
- redukcję ciśnienia do wymaganej przez konkretny odbiornik wielkości;
- nasączanie olejem poprzez wprowadzenie kontrolowanej ilości czynnika smarnego w postaci mgły olejowej.
Przygotowanie sprężonego powietrza, polegające na oczyszczeniu, realizowane jest przy pomocy zespołu filtrów wykorzystujących trzy metody filtrowania: mechaniczną, adsorpcyjną i absorpcyjną. W pierwszej – mechanicznej, zespół kanałów i przegród wykorzystuje ruch wirowy powietrza, dzięki czemu duże cząsteczki wody i oleju zatrzymując się na ściankach wytrącają się z powietrza. W drugiej metodzie znacznie mniejsze już cząsteczki wody i oleju zatrzymywane zostają na złożonej powierzchni porowatej przegrody filtru. W pierwszej i drugiej metodzie wytrącone zanieczyszczenia spływają do osadnika. Trzecia metoda wykorzystuje chemiczny wkład absorbujący czynne szkodliwe gazy, wodę oraz olej.
Redukcja ciśnienia uzyskiwana jest poprzez stosowanie zaworów redukcyjnych. Dzięki nim możliwe jest zredukowanie ciśnienia wejściowego do wymaganej na konkretnym stanowisku roboczym wartości i następnie utrzymanie jej, pomimo zmian wartości ciśnienia wejściowego oraz natężenia przepływu powietrza.
Nasączanie olejem powietrza dotyczy napędu siłowników i silników pneumatycznych. Zadaniem oleju zawartego w sprężonym powietrzu jest smarowanie współpracujących części w tego typu odbiornikach. Nasączanie powietrza olejem odbywa się tylko na końcówkach tych stanowisk odbiorczych, na których pracują urządzenia wymagające takiego uzdatnienia sprężonego powietrza. Do nasączania służą smarownice selekcyjne wytwarzające mgłę olejową. Tak nasączone powietrze z pewnością może przenieść olej na odległość co najmniej kilku metrów.
Reasumując, indywidualny układ przygotowania sprężonego powietrza musi mieć zainstalowany: zawór odcinający, zespół filtrów, zawór redukcyjny oraz smarownicę.
Należy bezwzględnie pamiętać, że przy projektowaniu i opracowywaniu nowej instalacji sprężonego powietrza w warsztacie jej parametry dobieramy tylko według aktualnych potrzeb, czyli zaplanowanych ilości stanowisk odbiorczych o określonych parametrach. Tak więc w przypadku rozbudowy warsztatu i tworzenia nowych stanowisk pracy, wymagających doprowadzenia do nich sprężonego powietrza, konieczna będzie modernizacja instalacji i ponowne przeanalizowanie aktualnych potrzeb.
Komentarze (0)