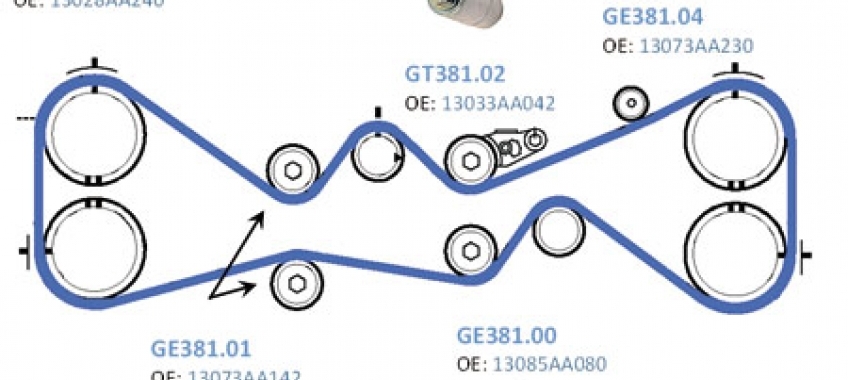
Subaru to marka kultowa, znana i lubiana, wydaje się więc, że nikomu nie musimy jej przedstawiać. Auta tej marki w zdecydowanej większości modeli wyposażone są w silniki typu boxer.
W układzie tym tłoki skierowane są parami przeciwsobnie, zaś wał korbowy znajduje się dokładnie w centrum tego układu. Z tego, że każda para tłoków silnika przeciwsobnego zawsze wykonuje ruchy w przeciwnych kierunkach, wynika, że siły bezwładności takiej pary tłoków samoistnie się równoważą, a zatem układ korbowo- -tłokowy przekazuje na zewnątrz znacznie mniej drgań, niż ma to miejsce w silnikach o innym układzie cylindrów. Silnik w układzie boxer pracuje z wyjątkowo małymi oporami wewnętrznymi w każdym zakresie obrotów wału korbowego i nie wymaga stosowania dodatkowych mas wyważających. Ważną zaletą silnika przeciwsobnego są jego małe wymiary, a zwarta konstrukcja pozwala na skuteczne zastosowanie aluminium do budowy jego kadłuba. W efekcie jednostka jest sztywna i lekka, co pozwala na obniżenie środka ciężkości, dzięki czemu auto pozostaje idealnie wyważone.
Dziś zmierzymy się z wymianą rozrządu w tej specyficznej konstrukcji. Nietrudno przy tak skomplikowanym układzie o błędy w montażu, z pozoru prozaiczne, ale skutkujące poważnymi awariami silników. Zacznijmy zatem od schematu (rys. 1) i podstawowych informacji na temat takiego układu rozrządu. Rolki prowadzące oraz napinające pracują na jednym pasku o 281 zębach. Warto zwrócić uwagę na charakterystyczną budowę rolki napinającej. Jej nietypowe wykonanie charakteryzuje się kompaktowym połączeniem ramienia napinającego z hydraulicznym napinaczem oraz rolką. Pod żadnym pozorem nie należy zwalniać zabezpieczenia napinacza hydraulicznego przed zmontowaniem kompletnego układu.
Jeżeli jest konieczne ustawienie wałków rozrządu, należy obracać nimi pojedynczo i ostrożnie, by nie doprowadzić do kontaktu między zaworami ssącymi i wydechowymi i nie spowodować ich uszkodzenia. Kierunek obrotu pokazują strzałki umieszczone na kółkach wałków rozrządu.
Efektem zbyt słabo napiętego paska jest uszkodzenie spowodowane wysoką temperaturą, która powstaje na styku zewnętrznej części paska (grzbiecie) i rolki napinającej. Pasek, ocierając się o rolkę swoją zewnętrzną powierzchnią, topił się i przenosił wysoką temperaturę na bieżnię rolki napinacza. Na rys. 2 widać wyraźnie efekty wysokiej temperatury, która doprowadziła do zniszczenia łożyska rolki napinacza.
Kolejnym przykładem jest uszkodzenie wynikające ze słabego momentu dokręcenia śruby napinacza. Obciążenia odpowiedzialne za ścięcie śruby widocznej na rys. 3 powstają właśnie z tej przyczyny, a co za tym idzie – nieprawidłowej pracy napinacza. Za słabo dokręcona śruba jest narażona na oddziaływanie większych sił ścinających aniżeli rozciągających. Nieprawidłowy naciąg paska spowodowany ww. zależnością powoduje niepokrywanie się punktów odniesienia układu rozrządu.
Po zerwaniu śruby rolka pozostaje bliżej korpusu napinacza, co zazwyczaj prowadzi do jej dalszej degradacji. Zewnętrzny pierścień rolki jest zatem często przebarwiony na skutek wzrostu temperatury w wyniku kontaktu z paskiem. Biorąc pod uwagę wszystkie powyższe aspekty:
- zalecany moment dokręcania wszystkich rolek wynosi 39 Nm,
- do montażu należy użyć specjalnego przyrządu (tulejka blokująca koło wału korbowego – OE 4999 87500).
Na co zwrócić uwagę podczas montażu paska?
Podczas instalacji nowego zestawu konieczne jest ustawienie odległości pomiędzy zewnętrzną powierzchnią paska a prowadnicami koła pasowego wału korbowego oraz kół pasowych wałków rozrządu. Według instrukcji producenta odległość ta powinna wynosić 1 ±0,5 mm. Po wyregulowaniu wszystkich prowadnic należy dokręcić je śrubami mocującymi siłą 9,75 Nm. W przypadku niewyregulowania ww. szczelin drobne na pozór niedopatrzenie spowoduje niebezpieczeństwo uszkodzenia paska podczas eksploatacji.
Jeśli zdarzy się nam wcześniejsze odbezpieczenie napinacza, niekoniecznie musimy go wymieniać na nowy – możemy powoli wcisnąć trzpień w obudowę za pomocą prasy, aż otwory w trzpieniu i obudowie pokryją się (rys. 4).
Pamiętajmy! Operacja ta musi być przeprowadzona w położeniu pionowym, zaś siła nacisku nie może przekraczać 1000 kg.
Aby utrzymać trzpień w odpowiednim położeniu, wsuwamy sworzeń o średnicy 2 mm w otwory w korpusie i trzpieniu (rys. 5). Czas wciskania trzpienia siłownika w obudowę może trwać około trzech minut.
Komentarze (0)