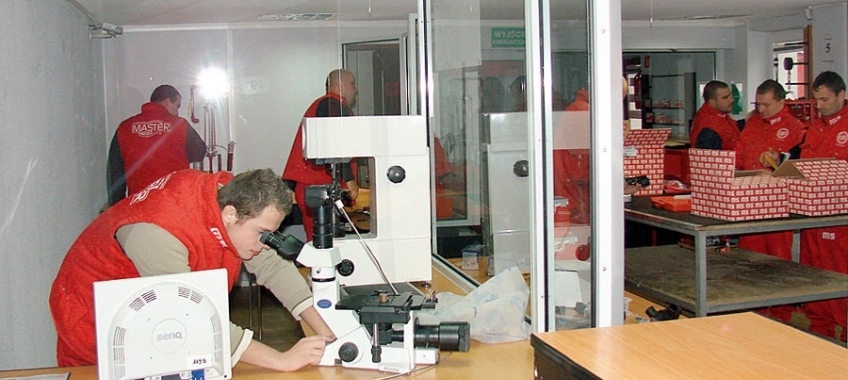
Odpowiedzialność spoczywa na każdym ogniwie łańcucha dostaw, ale to od osoby serwisującej układ hamulcowy wymagamy odpowiedzialności za bezpieczeństwo powierzonego pojazdu. Ryzyko zastosowania produktu wątpliwej jakości to pewność, że klient wróci ze skargą na piski. Gorzej, gdy w trakcie hamowania pęknie tarcza, która zablokuje koło lub pod wpływem temperatury drastycznie spadnie skuteczność hamowania.
Wiemy, że klocki hamulcowe należy odpowiednio dobierać do tarcz hamulcowych, tak, aby możliwe było uzyskanie czystej i równej powierzchni tarczy. Przekształcenie energii kinetycznej w ciepło wymaga by wszystkie parametry – mechanizm formowania warstwy ochronnej, wymiary powierzchni trących, materiał okładziny ciernej i materiał tarczy hamulcowej – były idealnie dopasowane. Podczas zwykłej jazdy miejskiej i normalnych hamowań temperatura okładzin ciernych sięga zazwyczaj od 80 do 120OC, acz podczas zjazdu ze wzniesienia czy po kilku mocnych hamowaniach sięga ok. 400OC. Oryginalne klocki hamulcowe testowane są w cyklu powtarzających się ostrych hamowań, symulujących najcięższe warunki jazdy. Wymagana jest ich stabilność w temperaturach przekraczających 600OC.
Podczas opracowywania systemu hamulcowego pojawia się znacznie więcej zagadnień decydujących o jakości i bezpieczeństwie produktu. W przypadku produktów do motoryzacji mamy kilka typów certyfikatów i homologacji. Jednym z częściej stosowanych jest ogólny certyfikat ISO. Dotyczy on głównie organizacji systemów zarządzania produkcji, pośrednio ma on wpływ na jakość produktu, a szczególnie na jego powtarzalność. Może się jednak zdarzyć produkt mający problemy z jakością, mimo że został wyprodukowany w fabryce z certyfikatem ISO. Żeby ograniczyć nie tylko takie sytuacje na terenie Unii Europejskiej obowiązuje homologacja ECE R90. Jest to norma, która ma określać minimalne parametry elementów bezpieczeństwa w samochodach, np. klocków hamulcowych.
Jakość elementów użytych w układach zapewniających bezpieczeństwo wydaje się na tyle ważna, że od kilku lat mówi się o konieczności podnoszenia standardów i konieczności objęcia obowiązkiem certyfikowania pozostałych składowych układu hamulcowego.
- Według Meritora certyfikowanie samego tylko klocka to zdecydowanie za mało, bo układ hamulcowy składa się z kilku podstawowych elementów roboczych, np. w przypadku najpopularniejszego systemu tarczowego są to: tarcza, zacisk i klocki hamulcowe – wyjaśnia Jarosław Tokarz, Key Account Manager CEE & Baltics, Meritor. - Niestety, do dzisiaj nie ma żadnych regulacji dotyczących zacisków – ten ważny element w polskich realiach często naprawiany jest przy użyciu młotka i przecinaka i nikt tego nie zabrania. Od około roku na terenie UE została wprowadzona homologacja na tarcze, ale póki co obowiązek dotyczy tylko nowych aplikacji, bo stworzonych po 2014 roku, a przy „starszych tarczach” homologacja jest dobrowolna. Niestety, do dzisiaj nie ma żadnych regulacji dotyczących zacisków. Co dziwne, na tę chwilę niewiele niezależnych jednostek laboratoryjnych wykonuje takie testy uwieńczone certyfikatem. Nasza firma pokusiła się o takie zewnętrzne testy w laboratoriach w Wielkiej Brytanii, bo jakkolwiek mamy także swoje laboratoria, to przecież nie możemy sami dla siebie udzielać certyfikatów. Wszystkie nasze tarcze, a jest ich ponad 60 referencji, poddane zostały niezależnej ocenie, która potwierdziła wysoką jakość produktów. To o tyle istotne, że spotykamy się z przykładami bezmyślności niektórych mechaników. Zdarza się, że zacisk i układ hamulcowy bywają naprawiane w sposób mogący doprowadzić do tragedii na drodze.
Ciekawych wniosków dostarczają wyniki testów, jakie przeprowadzono w niezależnym ośrodku badawczym w Wielkiej Brytanii – Brake Testing International Ltd UK, na zlecenie firmy Meritor. Przy wykorzystaniu oryginalnego materiału jako wzorcowego – mowa o klockach stanowiących oryginalne wyposażenie pojazdu, oceniono też nowy materiał cierny M520 klocków Meritor MDP3000 oraz siedem innych dostępnych na rynku wtórnym klocków hamulcowych w skrajnych warunkach prędkości, temperatury, ciśnienia oraz hamowania. Na potrzeby wewnętrznych testów te ostatnie – 7 propozycji z rynku wtórnego, oznaczono pierwszymi literami alfabetu. Jakość siódmego, najtańszego zestawu klocków hamulcowych, była tak niska, że w ogóle nie udało się przeprowadzić testu odporności na zużycie do samego końca, tj. 6000 cykli hamowań w różnych temperaturach (sic!). Konkurent E (patrz wykres nr 1) deklarował się co prawda porównywalnymi z wzorcem i M520 poziomem zużycia klocka, ale aż dwukrotnie większym zużyciem tarczy hamulcowej, co oczywiście skutkuje wysokimi kosztami eksploatacji! Konkurent F wypadł nieco tylko lepiej, ale niskie zużycie klocka wynikało z zastosowania niezwykle agresywnego materiału ciernego, co skutkowało nadmiernym zużyciem tarczy (patrz wykres nr 2). Z kolei Konkurent A okazał się być dostawcą klocka tylko do pracy bez nadmiernych obciążeń, bo wspomniany test ujawnił nadmierne zużycie klocka hamulcowego przy temperaturze powyżej 250°C (patrz wykres nr 3).
Dlaczego z dużą rezerwą należy podchodzić do produktów, których jakość deklaruje tylko producent? Po pierwsze, co poniektórzy ograniczają walidację portfolio swoich produktów do ograniczonej liczby referencji, a pomyślnie uwieńczone próby awansem przypisują całej gamie swych produktów, by w tej sposób ograniczyć koszt wspomnianych testów. To oczywiście skrajny przykład, ale dość powszechnie wykorzystywany przy okazji debiutu rynkowego marki dotąd nieobecnej w krajach UE. Po drugie, niezależne testy wg standardów ECE R90 stanowią absolutne minimum, bo dotyczą tylko czterech z sześciu aspektów! Cztery pierwszy próby testowe są obligatoryjne i dotyczą badań skuteczności hamowania: na zimno, w wysokiej temperaturze, podczas fadingu, z przerwami na chłodzenie. Producenci mogą pokusić się także o badania dodatkowe – te są dobrowolne, które służą określeniu stopnia zużycia materiału i ocenie komfortu użytkowania produktu. Większość renomowanych producentów elementów układów hamulcowych wykonuje na własne potrzeby takie testy, które daleko wykraczają poza obowiązkowy zakres badań certyfikacyjnych, by w pełni ocenić jakość swoich wyrobów. Przykładem takiego działania może być obecna również na rynku polskim niemiecka firma Master Sport Automobiltechnik (MS) GmbH. Firma zajmuje się projektowaniem, produkcją i dystrybucją części samochodowych i działa zarówno na rynku dostaw pierwszomontażowych (OEM), jak i aftermarketowym (IAM) pod własną marką Master Sport.
- Bazując na doświadczeniach z rynku OEM, wszystkie produkty firmy testowane są w ten sam sposób i podlegają takim samym reżimom jakościowym. Poza testami laboratoryjnymi i stanowiskowymi prowadzone są zawsze badania eksploatacyjne w realnych warunkach drogowych – przybliża obowiązujące standardy szef działu badań i rozwoju Master Sport. - Badanie takie trwa 4 sezony, a prowadzone jest na min. 3 samochodach w różnych warunkach eksploatacyjnych na dystansie min. 60 tys. km z równomiernym rozłożeniem przebiegu. W przypadku układów hamulcowych badanie obejmuje: test trwałości elementów układu hamulcowego, test efektywności hamowania w warunkach mokrego układu hamulcowego, test hałasu przy hamowaniu.
Test trwałości elementów układu hamulcowego pozwala określić okres, w jakim hamulce mogą prawidłowo działać. Celem testu jest określenie maksymalnej równowagi pomiędzy zużywaniem się klocków i tarcz przy zachowaniu maksymalnej efektywności hamowania. Test efektywności hamowania w warunkach mokrego układu hamulcowego jest rozszerzeniem badania homologacyjnego ECE R90, które obejmuje test efektywności hamowania hamulców zimnych i rozgrzanych wyłącznie w warunkach suchych. Badanie w warunkach mokrych ocenia skuteczność hamowania w zmiennych, czyli rzeczywistych warunkach drogowych i ma kluczowy wpływ na bezpieczeństwo jazdy. Z kolei test hałasu przy hamowaniu służy zapewnieniu właściwych warunków do prowadzenia pojazdu. Nadmierny hałas przy hamowaniu powoduje wszak irytacje kierującego potęgowaną wrażeniem, że hamulce działają nieprawidłowo.
Rafał Dobrowolski
Fot. R. Dobrowolski i materiały firm: Meritor, Master Sport
Komentarze (0)