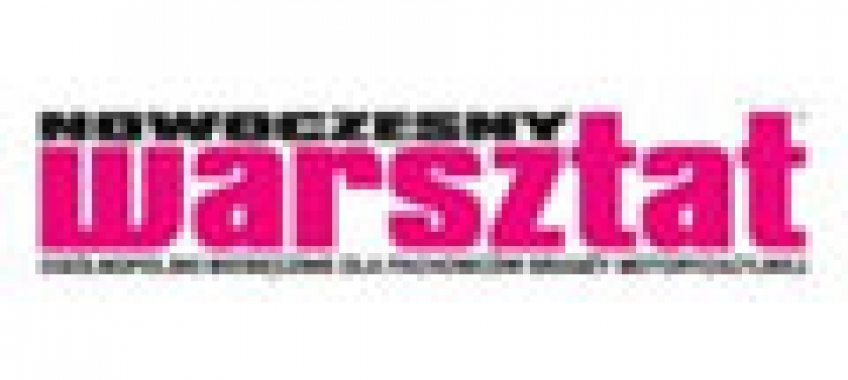
Ścierniwa używane do usunięcia farby i podkładu mają niewielki lub żaden wpływ na powierzchnię metalu – przy zachowaniu zalecanych parametrów obróbki usuwają farby bez uszkodzenia powierzchni. Powstaje przy tym kurz na zmontowanym samochodzie, ale nie w postaci twardego, ostrego żwiru, jak przy piasku czy żużlach odpadowych szkodzących częściom mechanicznym. Ścierniwa te nie zawsze są jednak wystarczająco twarde, aby usunąć rdzę z dolnych paneli i nadkoli (musi ona wówczas zostać usunięta za pomocą małych szlifierek i szczotek drucianych, co jest bardzo czasochłonne). Ścierniwa nowoczesne są nieco droższe niż piasek, ale niektóre z nich mogą być użyte kilkakrotnie, pod warunkiem posiadania i zastosowania odpowiednich urządzeń zbierających użyte ścierniwo i usuwających jego zanieczyszczenia oraz zbyt drobno rozbite ziarna ścierne. Tabela 1 pokazuje dobitnie, dlaczego nie powinno się stosować wymienionych w niej kulek szklanych. Pył kwarcowy zawarty w rozbitym ścierniwie powoduje u operatora oczyszczarki zwłóknienia płuc w poważnym stopniu (jednostka chorobowa – „krzemica”) i raka płuc, żużel paleniskowy wywołuje zwłóknienia płuc i prawdopodobne ich rakowacenie, a żużel pomiedziowy jest lekko promieniotwórczy, powoduje zwłóknienia płuc po dłuższym okresie pracy oraz zagraża ich rakowaceniem. Należy on też, jak i inne żużle odpadowe, do ścierniw brudnych, które pozostawione na powierzchni zawilgoconej wywołują korozję. Wymienione ścierniwa szczególnie źle wpływają na stan środowiska naturalnego (dramatycznie wysokie wartości odniesienia pokazane w ostatniej kolumnie). Kulki szklane i granulat szklany nie przekraczają poziomu NDS (Najwyższe Dopuszczalne Stężenie) na stanowisku pracy. Pozostałe ścierniwa nie mają wyznaczonego NDS i w niewielkim stopniu wpływają na środowisko. Odpad ścierniw szklanych, jeśli nie zawiera szkodliwych zanieczyszczeń usuwanych z powierzchni oczyszczanej, może być przekazany na składowisko komunalne. Poziom radioaktywności ścierniw charakteryzują faktory f1 (suma dopuszczalnych względnych wartości promieniowania K40, Ra226 i Tr228), których średnia wartość winna być mniejsza od 1 oraz faktor f2, nieprzekraczający 25 Bq/kg. Faktor f1 dla piasku kwarcowego wynosi 0,02-0,16, granulatu szklanego 0,02-0,10, a żużla pomiedziowego 1,1-1,8. Faktor f2 dla piasku kwarcowego wynosi 0,7-30, żużla pomiedziowego 220-320, Bq/kg (dużo > 25 Bq/kg), a granulatu szklanego 0,7-4 Bq/kg. Z powyższego powodu nie opisuję zastosowania żużla pomiedziowego do usuwania lakieru samochodowego. Tabela 3 pokazuje cechy fizyczne i parametry technologiczne stosowanych w lakiernictwie samochodowym ścierniw i inne własności. Szczegółowe zalecenia do stosowania w lakiernictwie samochodowym oraz parametry stosowania z uwzględnieniem rodzaju oczyszczanego materiału podane są w opisie poszczególnych ścierniw.
Zastosowanie granulatu szklanego zamiast piasku kwarcowego
Granulat szklany jest ścierniwem ekologicznym, niewpływającym na środowisko naturalne oraz jest nieszkodliwy dla pracownika. Dzięki temu można go stosować w terenie otwartym, w środowisku wiejskim, miejskim i przemysłowym oraz nad zbiornikami wodnymi, bez obowiązku jego usuwania, jeśli nie zawiera toksycznych zanieczyszczeń, np. farb na bazie chromu, kadmu i ołowiu. Nie wymaga specjalistycznego sprzętu, a więc można zastosować posiadane „piaskarki” pneumatyczne z otwartym obiegiem ścierniwa w terenie. W warsztacie samochodowym wymaga izolacji stanowiska w postaci pomieszczenia wentylowanego lub oczyszczarek podciśnieniowych, tak zwanych „bezpyłowych”, posiadających głowice z przylgą do oczyszczanej powierzchni dobieranej do jej kształtu. Oczyszczarka bezpyłowa posiada dyszę natryskującą ścierniwo i podciśnieniowe odsysanie ścierniwa użytego. Jeśli posiada ona wbudowany filtr, może być eksploatowana nawet w pomieszczeniu ślusarskim. Szkło kruszone jest produkowane najczęściej z recyklingu szkła butelkowego. Korzystanie ze ścierniwa uzyskiwanego z odpadu szkła pozytywnie wpływa na środowisko z powodu zmniejszenia ilości odpadów na składowisku odpadów w ramach recyklingu oraz kierowanie odpadów po ich użyciu ponownie wprost na składowiska odpadów szklanych, pod warunkiem nietoksycznego zanieczyszczenia, jakim są lakiery samochodowe (bez pigmentów chromianowych, kadmowych i ołowianych). Podobnie do wielu żużli odpadowych szkło kruszone ma twardości 5-6 w skali Mohsa. Granulat szklany, produkowany ze specjalnie wytapianych sztabek szkła o twardości 6-7 według skali Mohsa jest szczególnie czysty, ale nieco droższy. Kruszywo szklane, z wyjątkiem chińskiego, wolne jest od metali ciężkich, takich jak arsen, ołów, azbest, beryl, tytan itp., które zwykle znajdują się w dużych ilościach w żużlach odpadowych. Granulat szklany nie zawiera wolnej, niezwiązanej krzemionki, jest więc nietoksyczny i obojętny chemicznie, a więc nie stanowi, tak jak żużle odpadowe, zaczynu korozji. Uzyskuje się o połowę mniejszą chropowatość (RZ = 25µm) od żużli odpadowych, a więc mniej ubywa materiału z obrabianego podłoża. Ponieważ chropowatość nie może być większa niż 1/3 grubości lakieru, po jego utwardzeniu jest to okoliczność pozytywna. Szkło posiada stabilny poziom pH < 11. Pozwala uzyskać drobny profil (kształt) chropowatości, który eliminuje potrzebę szlifowania oczyszczonej powierzchni paneli, daje w ten sposób duże oszczędności czasu podczas przygotowania części przed malowaniem, zapobiega konieczności mycia powierzchni chemikaliami i płukania, jak ma to miejsce po obróbce strumieniowej powierzchni sodą oczyszczoną przed nakładaniem lakieru. Nie zawiera praktycznie wolnej, krystalicznej krzemionki SiO2 (< 0,1%, a norma < 1%), a zawartość chloru w masie: < 0,0005%, przewodnictwo właściwe: 80 – 230 µS/cm (norma: < 250 µS/cm). Zapewnia bardzo nieliczne osadzanie niewidocznych i neutralnych chemicznie cząstek na powierzchni obrabianej (tylko do 2%), które daje wizualnie bielszy, czystszy wygląd, a jego pył nie powoduje uszkodzenia łożysk ani silników. Zapewnia znakomitą wydajność w stosunku do ścierniw mineralnych i żużlowych. Jest on lżejszy od wielu żużli odpadowych (pomiedziowego, paleniskowego, poniklowego), co sprawia, że przy ciśnieniu 2,17 barów koszt granulatu szklanego na 1 m2 oczyszczonej powierzchni jest 5 razy mniejszy, czas obróbki dwukrotnie niższy, a zużycie ścierniwa 8-krotnie mniejsze niż żużla pomiedziowego, przy zastosowaniu 5-krotnego zawracania ścierniwa. Wymaga stosowania skafandra ochronnego, butów i rękawic oraz maski z filtrem kategorii P–1 (nie wymaga kasku przewietrzanego).
Ostrokątne cząstki pokruszonego szkła pozwalają na agresywne profilowanie powierzchni i usuwanie nawet twardych powłok, takich jak epoksydowe, alkidowe, winylowe, mocznikowe, smołowo-węglowe i elastomerowe. Granulat szklany może być użyty ponownie 3-5 razy, gdy posiada się urządzenia do jego zawracania i separowania jego zanieczyszczeń. Według firmy Opta Minerals Inc., granulat szklany potrzebny jest wtedy, gdy należy zapewnić lepszą wydajność w stosunku do sody na delikatnych częściach oraz przy renowacji zabytkowych samochodów z karoserią stalową i usuwania farby, a nawet ciężkiej rdzy, uzyskując równomiernie chropowate, oczyszczone do gołego metalu panele. Skutecznie eliminuje pracochłonne i uciążliwe w stosowaniu preparaty chemiczne i rozpuszczalniki organiczne. Stosuje się go do powierzchni stalowych, aluminiowych, ocynkowanych, stali nierdzewnej, tworzyw sztucznych i drewna, za wyjątkiem laminatów szklanych i węglanowych oraz o strukturze plastra miodu. Przy ciśnieniu potrzebnym dla motoryzacji rzędu 2,4-2,8 bar i wielkości ziaren 35/60 (500/250 µm) pokruszone szkło pracuje doskonale przy usuwaniu lakieru, jest agresywne i pozostawia ładne, białe, jednolite wykończenie. Można też na końcu obrabiać nieco drobniejszą wielkością szkła kruszonego o wielkości 90 (163 µm), które pozostawia bardzo drobny profil na wszystkich panelach. Soda jest dobra do tego celu, ale nie dość agresywna na panelach i wymaga zmywania oraz neutralizacji powierzchni, a zaniechanie tego procesu grozi korozją podpowłokową z powodu reakcji alkalicznej pozostałości z lakierem. Granulat szklany jest tańszy od kulek szklanych i innych ścierniw ekologicznych. Zaproponowałem w pierwszym rzędzie obróbkę strumieniowo-ścierną, ponieważ dodatkowo jest to metoda najłatwiejsza do zastosowania z uwagi na najniższe koszty inwestycyjne i koszty tego procesu.
mgr inż. Marek Marcinkowski
Literatura artykułu dostępna w redakcji.
Komentarze (0)