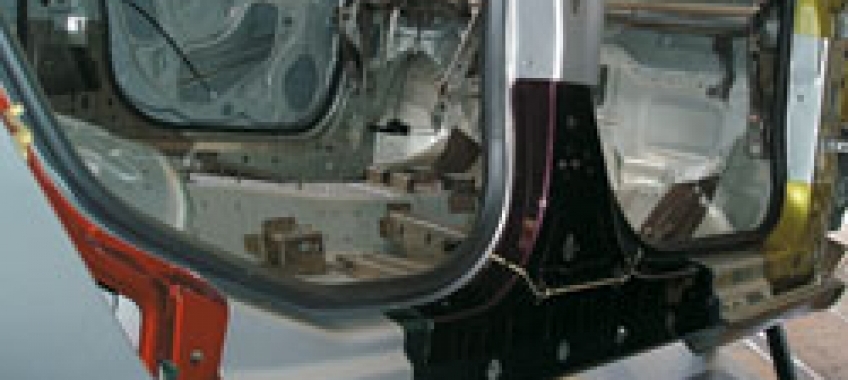
Specjaliści są zgodni – czekają nas zmiany w koncepcji projektowania współczesnych samochodów. Wymóg mniejszej energochłonności przemysłu samochodowego wzmaga pokusę odchudzania karoserii i poszyć nadwozi. Taki trend wynika w dużej mierze z pokusy wyposażania pojazdów w elementy komfortu i bezpieczeństwa, a te stanowią coraz większy udział w ogólnej masie pojazdu. Coraz większe wymagania stawiane przed przemysłem motoryzacyjnym w zakresie ekologii mobilizują naukowców, inżynierów i producentów do prac nad zastosowaniem materiałów, które zapewnią nie tylko lepsze właściwości trakcyjne pojazdów czy większy komfort jazdy, ale spowodują ograniczenie ich negatywnego oddziaływania na środowisko. Pod uwagę bierze się oczywiście cały cykl życia pojazdu: od wytworzenia, przez czas eksploatacji, po jego kres i recykling użytych materiałów. Odchudzanie karoserii samochodów nie może rzecz jasna odbywać się ze szkodą dla sztywności i bezpieczeństwa bryły. Ostatnie kilkanaście lat w dziedzinie motoryzacji charakteryzowały się przede wszystkim ogromnym wzrostem poziomu bezpieczeństwa pojazdów (np. ABS) oraz coraz nowszymi elementami ich dodatkowego wyposażenia (elektryczne szyby, klimatyzacja itp.). Szacuje się, że mogło to spowodować około 30-proc. przyrost masy pojazdów, co oczywiście nie pozostaje bez wpływu na zużycie paliwa. W sukurs projektantom przychodzą nowe, lekkie materiały. Na razie barierą jest koszt zastosowania ich na skalę przemysłową, zwłaszcza w segmencie popularnych modeli i marek pojazdów. Pokusa jest jednak ogromna. Tendencja do stosowania materiałów konstrukcyjnych o mniejszej gęstości oraz większej wytrzymałości daje szanse zmniejszenia masy pojazdu i ograniczenia negatywnego wpływu na środowisko naturalne (emisja dwutlenku węgla). Z chęci odchudzenia poszycia konstruktorzy z coraz większą odwagę próbują adaptować rozwiązania konstrukcyjne w postaci struktur warstwowych typu sandwicz. Takie rozwiązania od lat stosuje się przy zabudowach pojazdów kempingowych, gdzie wymóg lekkości jest pierwszorzędny.
- Miałem okazję oglądać takie drzwi wykonane w technologii typu sandwicz – dzieli się swym spostrzeżeniem Mariusz Bogacki, specjalista do spraw szkoleń CTS Car-o-liner. - Pokusa odchudzenia poszycia karoserii jest wielka, bo rdzeń jest ultralekki i zapewnia dużą sztywność, więc oblachowanie zamiast 0,8 milimetra może mieć dwie ściany grubości rzędu 0,2 milimetrów. Przy wykorzystaniu współczesnych technologii napraw blacharskich nie jesteśmy jednak w stanie odtworzyć uszkodzonego poszycia, więc generalnie nie sądzę, by takie rozwiązanie stało się standardem w produkcji popularnych modeli samochodów. Skoro jednym z pożądanych skutków stosowania nowych materiałów ma być zmniejszenie energochłonności przemysłu motoryzacyjnego, to powszechne stosowania oblachowania typu sandwicz, zwłaszcza elementów narażonych na uszkodzenia mechaniczne (stłuczki, szkody parkingowe), mija się z celem. Nowoczesne technologie, takie jak laserowe spawanie i zgrzewanie umożliwiają już dawno łączenie blach o różnej grubości doczołowo i tłoczenie z tak przygotowanych prefabrykatów gotowych elementów, więc można też oczekiwać rozwiązań idących w tę stronę. Nowe gatunki stali o bardzo wysokiej wytrzymałości (borowe), stale niskostopowe stosowane w konstrukcji szkieletu nadwozi już dziś stanowią nawet ponad 50% udziału masy całkowitej pojazdu. Duże nadzieje daje dziś stosowanie 3-krotnie lżejszych od stali stopów aluminium, choć oczywiście stosowanie aluminium na poszycia stanowiące naturalną strefę ochronną dla pasażerów musi być grubsze niż stali (np. drzwi), a to nieco niweczy już zamysł „odchudzenia” karoserii. Stosowanie aluminium na inne elementy nie jest już tak ograniczone. Stopy aluminium już dziś stanowią nawet 1/10 masy całkowitej pojazdu. Aluminium też w ogromnej mierze znajduje zastosowanie w budowie elementów poszycia nadwozi typu błotniki, fragmenty pasa przedniego. Nowością są przestrzenne ramy nośne tłoczone typu space frame. Wymagają one, poza tłoczeniem, specjalnych technologii kształtowania (odlewanie ciśnieniowe czy wyciskanie na zimno) i łączenia (zgrzewanie, nitowanie i klejenie – zamiast spawania). Przykładowo, Audi TT ma kadłub wykonany ze stali o wysokiej wytrzymałości. Podłoga tylna, drzwi, błotniki tylne i pokrywa bagażnika stanowią „aż” 31% masy kadłuba. Aluminium jest też atrakcyjnym materiałem, bo świetnie poddaje się zaleceniom recyklingu materiałów używanych w motoryzacji. Już dziś materiał ten wykorzystuje się do powtórnego przetworzenia w krajach UE na poziomie 85−90%. Oczywiście, barierą powszechniejszego stosowania aluminium pozostaje nadal cena wyjściowa surowca.
Równie ciekawie rysuje się zastosowanie tworzyw sztucznych do budowy wielkoseryjnych poszyć nadwozi. Jednym z powodów wzrostu zainteresowania tymi materiałami jest łatwość polepszenia cech wytrzymałościowych przez tzw. zbrojenie (kompozyt). Od dawna stosuje się już kompozyty na mniej odpowiedzialne elementy poszycia zewnętrznego – błotniki, pokrywy komory silnika i bagażnika, dach, także na zderzaki, klosze i obudowy lamp. Takie hybrydowe karoserie mają przyszłość, o czym przekonuje projekt studentów uniwersytetu w Aachen i Akademii Tuningu w Ingolstadt w postaci Audi A4 quattro, w którym zastosowano drzwi i pokrywę silnika wykonane z tworzywa wzmocnionego włóknem węglowym (CRP). Zastąpienie stali przez powłokę CRP dało oszczędności rzędu 23 procent na masie elementów: każde drzwi odchudzono o 3 kg, a maskę o 5,5 kg. Dużo większe nadzieje wiąże się z europejskim projektem współpracy ośrodków naukowych i biur projektowych (łącznie 37 partnerów) z dziewięciu krajów UE nad stworzeniem tzw. LIGHT Super-CAR-a. Nad pracami czuwa niemiecki instytut badawczy IKA. Zamysł jest ambitny, bo dotyczy zmniejszenia masy karoserii (bazującej na wymiarach płyty podłogowej VW Golf V) o co najmniej 30 procent. Wszystko to za sprawą zastosowania tworzyw sztucznych wzmocnionych włóknami węglowymi. Udział tych materiałów już dziś rośnie w ogólnej masie własnej karoserii, kosztem stali. Przemysł samochodowy jest największym odbiorcą kompozytów tzw. TWM, czyli termoplastów wzmocnionych matami. Kompozyty i włókna, głównie węglowe, znajdują coraz szersze zastosowanie w nadwoziach nowoczesnych samochodów. Przykładowo, w Fordzie GT (2005) pokrywa bagażnika wykonana z włókna węglowego waży 6,4 kg. Element okazał się o ok. 50% lżejszy od wykonanego z aluminium i aż o 75% od stalowego.
Opracowano na podstawie specjalnego wykładu przeprowadzonego dla redakcji „Nowoczesnego Warsztatu” w firmie CTS Car-o-liner
Notował: Rafał Dobrowolski
Zdjęcia: CTS i R. Dobrowolski
- Miałem okazję oglądać takie drzwi wykonane w technologii typu sandwicz – dzieli się swym spostrzeżeniem Mariusz Bogacki, specjalista do spraw szkoleń CTS Car-o-liner. - Pokusa odchudzenia poszycia karoserii jest wielka, bo rdzeń jest ultralekki i zapewnia dużą sztywność, więc oblachowanie zamiast 0,8 milimetra może mieć dwie ściany grubości rzędu 0,2 milimetrów. Przy wykorzystaniu współczesnych technologii napraw blacharskich nie jesteśmy jednak w stanie odtworzyć uszkodzonego poszycia, więc generalnie nie sądzę, by takie rozwiązanie stało się standardem w produkcji popularnych modeli samochodów. Skoro jednym z pożądanych skutków stosowania nowych materiałów ma być zmniejszenie energochłonności przemysłu motoryzacyjnego, to powszechne stosowania oblachowania typu sandwicz, zwłaszcza elementów narażonych na uszkodzenia mechaniczne (stłuczki, szkody parkingowe), mija się z celem. Nowoczesne technologie, takie jak laserowe spawanie i zgrzewanie umożliwiają już dawno łączenie blach o różnej grubości doczołowo i tłoczenie z tak przygotowanych prefabrykatów gotowych elementów, więc można też oczekiwać rozwiązań idących w tę stronę. Nowe gatunki stali o bardzo wysokiej wytrzymałości (borowe), stale niskostopowe stosowane w konstrukcji szkieletu nadwozi już dziś stanowią nawet ponad 50% udziału masy całkowitej pojazdu. Duże nadzieje daje dziś stosowanie 3-krotnie lżejszych od stali stopów aluminium, choć oczywiście stosowanie aluminium na poszycia stanowiące naturalną strefę ochronną dla pasażerów musi być grubsze niż stali (np. drzwi), a to nieco niweczy już zamysł „odchudzenia” karoserii. Stosowanie aluminium na inne elementy nie jest już tak ograniczone. Stopy aluminium już dziś stanowią nawet 1/10 masy całkowitej pojazdu. Aluminium też w ogromnej mierze znajduje zastosowanie w budowie elementów poszycia nadwozi typu błotniki, fragmenty pasa przedniego. Nowością są przestrzenne ramy nośne tłoczone typu space frame. Wymagają one, poza tłoczeniem, specjalnych technologii kształtowania (odlewanie ciśnieniowe czy wyciskanie na zimno) i łączenia (zgrzewanie, nitowanie i klejenie – zamiast spawania). Przykładowo, Audi TT ma kadłub wykonany ze stali o wysokiej wytrzymałości. Podłoga tylna, drzwi, błotniki tylne i pokrywa bagażnika stanowią „aż” 31% masy kadłuba. Aluminium jest też atrakcyjnym materiałem, bo świetnie poddaje się zaleceniom recyklingu materiałów używanych w motoryzacji. Już dziś materiał ten wykorzystuje się do powtórnego przetworzenia w krajach UE na poziomie 85−90%. Oczywiście, barierą powszechniejszego stosowania aluminium pozostaje nadal cena wyjściowa surowca.
Równie ciekawie rysuje się zastosowanie tworzyw sztucznych do budowy wielkoseryjnych poszyć nadwozi. Jednym z powodów wzrostu zainteresowania tymi materiałami jest łatwość polepszenia cech wytrzymałościowych przez tzw. zbrojenie (kompozyt). Od dawna stosuje się już kompozyty na mniej odpowiedzialne elementy poszycia zewnętrznego – błotniki, pokrywy komory silnika i bagażnika, dach, także na zderzaki, klosze i obudowy lamp. Takie hybrydowe karoserie mają przyszłość, o czym przekonuje projekt studentów uniwersytetu w Aachen i Akademii Tuningu w Ingolstadt w postaci Audi A4 quattro, w którym zastosowano drzwi i pokrywę silnika wykonane z tworzywa wzmocnionego włóknem węglowym (CRP). Zastąpienie stali przez powłokę CRP dało oszczędności rzędu 23 procent na masie elementów: każde drzwi odchudzono o 3 kg, a maskę o 5,5 kg. Dużo większe nadzieje wiąże się z europejskim projektem współpracy ośrodków naukowych i biur projektowych (łącznie 37 partnerów) z dziewięciu krajów UE nad stworzeniem tzw. LIGHT Super-CAR-a. Nad pracami czuwa niemiecki instytut badawczy IKA. Zamysł jest ambitny, bo dotyczy zmniejszenia masy karoserii (bazującej na wymiarach płyty podłogowej VW Golf V) o co najmniej 30 procent. Wszystko to za sprawą zastosowania tworzyw sztucznych wzmocnionych włóknami węglowymi. Udział tych materiałów już dziś rośnie w ogólnej masie własnej karoserii, kosztem stali. Przemysł samochodowy jest największym odbiorcą kompozytów tzw. TWM, czyli termoplastów wzmocnionych matami. Kompozyty i włókna, głównie węglowe, znajdują coraz szersze zastosowanie w nadwoziach nowoczesnych samochodów. Przykładowo, w Fordzie GT (2005) pokrywa bagażnika wykonana z włókna węglowego waży 6,4 kg. Element okazał się o ok. 50% lżejszy od wykonanego z aluminium i aż o 75% od stalowego.
Opracowano na podstawie specjalnego wykładu przeprowadzonego dla redakcji „Nowoczesnego Warsztatu” w firmie CTS Car-o-liner
Notował: Rafał Dobrowolski
Zdjęcia: CTS i R. Dobrowolski
Komentarze (0)