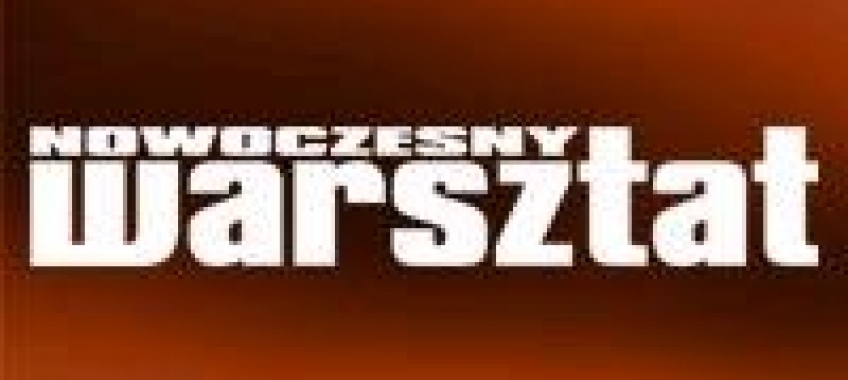
Lakiery poliuretanowe posiadają wieloletnią tradycję, jako wysokiej jakości systemy stosowane w autoreparacji. Po raz pierwszy rozpuszczalnikowe, dwuskładnikowe lakiery poliuretanowe, utwardzane w temperaturze poniżej 80oC zaprezentowane zostały w autoreparacji w latach siedemdziesiątych. Było to możliwe dzięki wcześniejszym badaniom powłok poliuretanowych w wymalowaniach samolotów. Zostały poddane tu szybkim, sięgającym różnicy 80oC zmianom temperatur, ekstremalnemu promieniowaniu UV oraz kontaktom z agresywnymi cieczami. Od tego czasu systemy poliuretanowe stały się dominującą technologią w sektorze lakierów autoreparacyjnych. Atrybutami, które tworzą dwuskładnikowe systemy poliuretanowe tak atrakcyjnymi są szybkie schnięcie w temperaturze otoczenia, wysoki połysk oraz twardość, odporność na czynniki chemiczne i rozpuszczalniki. Przy użyciu poli-izocyjanianów alifatycznych jako utwardzacza otrzymuje się powłoki o doskonałej odporności na warunki atmosferyczne. Udowadniają to testy, które przeprowadza się w ekstremalnych warunkach wysokiego nasłonecznienia np. na Florydzie czy w Australii.
W marcu 1999 r. wprowadzono Europejską Dyrektywę VOC (Volatile Organic Compounds) dotyczącą lotnych składników organicznych, stawiającą za cel redukcję emisji tychże związków do atmosfery o 70% poziomu roku 1999 przed rokiem 2007. Dyrektywa ta musi zostać wprowadzona do ustawodawstwa narodowego wszystkich członków państw Unii Europejskiej. Ma ona zasadnicze znaczenia dla ochrony warstwy ozonowej ziemi oraz eliminacji coraz częściej pojawiających się smogów. Ponieważ, ponad 45% rozpuszczalników emitowanych do atmosfery pochodzi z przemysłu farb i lakierów, stanowi on największe pole dla wprowadzonych ograniczeń.
Istnieją trzy podstawowe możliwości produkcji lakierów o niskiej emisji związków lotnych. Są to: farby proszkowe, farby o wysokiej zawartości części stałych (high-solids) oraz systemy wodorozcieńczalne. Jako wysokotemperaturowe systemy piecowe, farby proszkowe muszą być utwardzane w temperaturze powyżej 180oC. Powoduje to powstanie szeregu ograniczeń (elementy wielkogabarytowe), czy wręcz eliminacji np. w malowaniu tworzyw sztucznych. Lakiery o wysokiej zawartości części stałych reprezentują alternatywę dla rozpuszczalnikowych, dwuskładnikowych poliuretanów (2K-PUR), które posiadają typową zawartość części stałych na poziomie 40-50%. Obecnie dominuje przekonanie o radykalnej redukcji rozpuszczalników w produkowanych farbach i lakierach, przez co technologia systemów wodorozcieńczalnych zyskuje coraz bardziej na znaczeniu.
Dwuskładnikowy, wodorozcieńczalny układ poliuretanowy składa się z wodnej, stabilnej dyspersji poliolu (najczęściej poliakrylu) z wolnymi i reaktywnymi grupami hydroksylowymi (-OH) – składnik A oraz poliizocyjanianu – składnik B. Idea budowy układu wodorozcieńczalnego jest identyczna z systemem rozpuszczalnikowym. Oba składniki przechowywane są oddzielnie. Miesza się je bezpośrednio przed aplikacją tworząc stabilną dyspersję. Po aplikacji na podłoże zachodzi reakcja pomiędzy grupami –OH z poliolu z grupami – NCO z poliizocyjanianu, tworząc usieciowaną powłokę poliuretanową.
Pomysł zaprezentowania poliizocyjanianów jako reaktywnego składnika w wodorozcieńczalnych systemach poliuretanowych, kilka lat temu przedstawiał zupełnie nowatorską ideę. Zjawiska, zachodzące podczas formowania dwuskładnikowych wodorozcieńczalnych poliuretanów, takie jak specyfika procesu mieszania, morfologia roztworu, dystrybucja oraz rozmiar cząsteczek, charakterystyka dyspersji poliolowej, a także pH, nie występujące w systemach rozpuszczalnikowych, mają istotny wpływ na właściwości aplikacyjne lakieru wodorozcieńczalnego oraz charakterystykę powstałej z niego powłoki końcowej. Unikalność technologii wodorozcieńczalnych systemów poliuretanowych bierze się przede wszystkim stąd, że poliizocyjaniany reagują bezpośrednio z wodą dając dwutlenek węgla oraz aminę pierwszorzędową. Wysokoreaktywna amina reaguje następnie z poliizocyjanianem dając wiązanie mocznikowe. Reakcja poliizocyjanianu (utwardzacza, składnika B) z wodą konkuruje z preferowaną reakcją poliizocyjanianu z grupami hydroksylowymi poliolu (składnika A) dającą wiązanie uretanowe, a w konsekwencji poliuretan. Jedynie ta reakcja odpowiada za budowę łańcucha polimeru, a tym samym za końcowe właściwości powstałej powłoki.
Z uwagi na łatwość reakcji poliizocyjanianów (utwardzaczy) z wodą we wczesnych pracach skoncentrowano się na modyfikacji
wych (nierozpuszczalnych w wodzie) poliizocyjanianów. Modyfikacja ta polegała na wbudowaniu do cząsteczki poliizocyjanianu, hydrofilowych (rozpuszczalnych w wodzie) łańcuchów polieterowych, tworząc w ten sposób poliizocyjanian dyspergowalnym w wodzie. Powstały więc dwie, zasadniczo różne opcje utwardzaczy poliizocyjanianowych:
- hydrofobowe, poliizocyjaniany o niskiej lepkości, jak te używane w rozpuszczalnikowych systemach 2K-PUR;
- modyfikowane hydrofilowe, samoemulgujące poliizocyjaniany przeznaczone do dwuskładnikowych systemów wodorozcieńczalnych.
Jeżeli utwardzacz w układzie wodorozcieńczalnym mieszany jest ręcznie (niskie siły ścinające) rekomendowane jest użycie poliizocyjanianów modyfikowanych, hydrofilowych. Aby wprowadzić hydrofobowe poliizocyjaniany o niskiej lepkości do dyspersji wodnej poliolu wymagane jest dostarczenie wysokich sił ścinających osiąganych np. w specjalistycznych głowicach natryskowych czy dyspergatorach. Może stanowić to zasadnicze ograniczenie technologiczne dla typowych warsztatów samochodowych.
Pierwsze powłoki otrzymane przy użyciu modyfikowanych, hydrofilowych poliizocyjanianów charakteryzowały się niską odpornością na wodę, zredukowaną twardością oraz wolnym schnięciem. Wprowadzenie hydrofilowego łańcucha polieteru do poliizocyjanianu spowodowało obniżenie ilości grup izocyjanianowych, przez co powłoka posiadała niskie usieciowanie, co w dalszej konsekwencji prowadziło do jej słabej odporności chemicznej. Niemożliwe było do chwili obecnej otrzymanie hydrofilowych poliizocyjanianów, które łączyłyby dobrą emulsyfikowalność przy niskich siłach ścinających (mieszanie ręczne) z dobrymi odpornościami powłoki końcowej, twardością oraz szybkim schnięciem.
Obecny rozwój nowej generacji hydrofilowych poliizocyjanianów doprowadził do eliminacji powyżej opisanych wad systemów wodnych. W pracach badawczych wyróżniono oraz skupiono się na dwóch podstawowych procesach: wewnętrznej i zewnętrznej emulsyfikowalności, prowadzących do otrzymania poliizocyjanianów mieszalnych z wodą. Emulsyfikowalność wewnętrzna polega na wyborze metody syntezy hydrofilowych utwardzaczy, poprzez wprowadzenie do ich cząsteczki różnego rodzaju hydrofilowych łańcuchów poliolowych, zewnętrzna zaś na doborze emulgatorów, które nie są chemicznie związane z izocyjanianem, lecz pomagają w jego dyspergowalności w sposób fizykochemiczny. Wyeliminowano w ten sposób m.in. problem niskiej odporności powłok na wodę, uzyskano stabilny kolor czystego utwardzacza. Wykonano również prace nad zmianą struktury chemicznej samego poliizocyjanianu. Podwyższyło to jego funkcjonalność (zawartość grup izocyjanianowych).
Chemia dwuskładnikowych, wodorozcieńczalnych systemów poliuretanowych zaoferowała unikatową możliwość sprostania wymogom VOC, w odniesieniu do rynku lakierów autoreparacyjnych. Technologia ta może być użyta w każdej warstwie, od podkładu aż po lakier bezbarwny, sprostając wymaganiom co do właściwości poszczególnych warstw powłok.
Wodorozcieńczalne 2K-PUR podkłady akrylowe posiadają szybki czas schnięcia, wczesną szlifowalność, doskonałą przyczepność do podłoża oraz warstw następnych. Szybki czas schnięcia, fizyczny oraz chemiczny, osiągnięto poprzez kombinację poliizocyjanianów na bazie HDI i IPDI z wysokocząsteczkową żywicą akrylową, która charakteryzując się wysoką wartością Tg (temperatury zeszklenia) poprawia szlifowalność powłoki. Wysoki stopień usieciowania daje doskonałą adhezję międzyfazową (przyczepność warstw) oraz odporność na agresywne rozpuszczalniki. Lakiery bazowe charakteryzują się wysoką stabilnością koloru oraz pozwalają na produkcję powłok z efektem metalicznym. Bezbarwne lakiery nawierzchniowe poza tym, że są szybkoschnące mają wysoki połysk oraz twardość. Połysk, doskonała rozlewność, wysoka odporność na czynniki atmosferyczne są nierozerwalnymi elementami wodorozcieńczalnych lakierów poliuretanowych. Szybki czas schnięcia osiągany przez te lakiery pokazuje, że technologia wodorozcieńczalnych lakierów autoreparacyjnych może świetnie konkurować z powszechnie znanymi i stosowanymi systemami rozpuszczalnikowymi, dając jednocześnie rozwiązanie problemu emisji niebezpiecznych dla naszego zdrowia i życia związków organicznych do atmosfery.
Robert Tomczak
Bayer Sp. z o.o., Warszawa
www.bayer.com.pl
Na podstawie:
“Two-Component waterborne Polyurethane Coatings” Bayer Polymers, Pitsburg, USA, 2002
Komentarze (0)