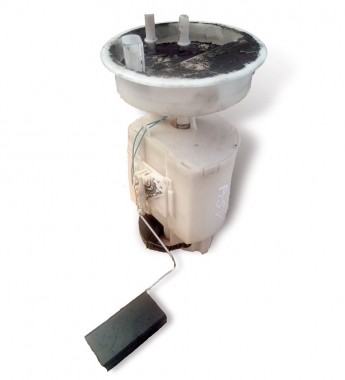
Poprawna praca układu zasilania paliwem uzależniona jest w pełni od właściwego działania pompy paliwa. W przypadku niewłaściwych parametrów pracy pompy paliwa, zwłaszcza ciśnienia, zakłócony zostaje wymagany proces tworzenia mieszanki paliwowo-powietrznej, a tym samym i praca silnika.
Zadaniem pompy paliwa jest bowiem zapewnienie ciągłości doprowadzania paliwa do wtryskiwaczy we wszystkich warunkach eksploatacyjnych pojazdu. Objawami nieprawidłowej pracy lub uszkodzenia pompy paliwa są: spadek mocy przy wzroście obciążenia silnia lub przerwanie pracy silnika oraz brak możliwości ponownego uruchomienia. Podstawowymi parametrami pracy pompy paliwa są: wydatek oraz ciśnienie tłoczenia.
W konstrukcjach współczesnych pojazdów samochodowych i zastosowanych w nich silnikach benzynowych stosowane są różne rozwiązania techniczne pomp oraz ich usytuowanie. Ze względu na pełnione w układzie paliwowym funkcje stosowane są pompy wstępne oraz główne pompy zasilające. Stosowane są więc w poszczególnych układach paliwowych następujące konfiguracje:
- jednostopniowa pompa paliwa – umiejscowiona w przewodzie zasilania lub w zbiorniku paliwa,
- dwustopniowa pompa paliwa – umieszczona na przewodzie zasilania lub w zbiorniku,
- dwie pompy jednostopniowe (wstępna i główna), usytuowane szeregowo (pompa wstępna na przewodzie zasilania lub w zbiorniku, a pompa główna w pobliżu wtryskiwaczy paliwa).
Konstrukcja pompy jednostopniowej wykorzystuje jeden mechanizm pompujący. Rozwiązanie pompy dwustopniowej to dwa, zwykle różne mechanizmy pompujące. Pompa jednostopniowa umieszczona jest zwykle na przewodzie paliwowym poza zbiornikiem paliwa lub zabudowana jest wewnątrz zbiornika. Usytuowanie poza zbiornikiem jest korzystniejsze w przypadku konieczności wymiany pompy. Wadą tego rozwiązania jest konieczność stosowania filtra wstępnego, zabudowanego w zbiorniku. W praktyce był on stosunkowo rzadko sprawdzany, w związku z czym dochodziło do powstawania zjawiska kawitacji na wirniku pompy i jego dość szybkiego uszkodzenia.
Drugim rozwiązaniem przy zastosowaniu jednostopniowej pompy paliwa jest umieszczenie jej wewnątrz zbiornika. To rozwiązanie zapewnia lepszą ochronę mechanizmu pompy.
Przy konstrukcji układu paliwowego z wykorzystaniem dwóch pomp paliwa połączonych szeregowo stosowane jest zwykle rozwiązanie polegające na umieszczeniu jednej z nich na zewnątrz zbiornika, a drugiej wewnątrz. Pompa wewnętrzna pełni w tym rozwiązaniu funkcję pomocniczą (o małym ciśnieniu tłoczenia), mającą na celu podawanie paliwa do obwodu ssącego pompy głównej.
Innym stosowanym w konstrukcjach układów paliwowych rozwiązaniem jest pompa dwustopniowa umieszczona w zbiorniku paliwa.
Ze względu na konstrukcję sekcji tłoczącej pompy paliwa podzielić można na wyporowe (rolkowo-komorowe, zębate, łopatkowe i śrubowe) oraz przepływowe (obwodowo-
-wirnikowe i bocznikowo-wirnikowe).Współcześnie stosowane w układach wtryskowych silników benzynowych są – jako zasilające, pompy paliwa niskiego ciśnienia, zasilane elektrycznie. Ich zadaniem jest zagwarantowanie ilości paliwa wystarczającej do przygotowania i dawkowania przez pompę wysokiego ciśnienia. Konstrukcje tego typu powstają jako jeden zespół z silnikiem elektrycznym i umieszczane są najczęściej w zbiorniku paliwa. Wydajność tego typu pompy jest od kilku do kilkunastu razy większa od zapotrzebowania paliwa przez silnik. Zasada działania pompy paliwa oparta jest na pracy ciągłej, niezależnej od prędkości obrotowej silnika. Jej zadaniem jest tłoczenie paliwa ze zbiornika, przez filtr paliwa do układu wtryskowego. Nadmiar paliwa przepływa przez zawór przelewowy z powrotem do zbiornika paliwa.
Elektryczne, zasilające pompy paliwa spełniać muszą następujące wymagania:
- wydajność 60-200 dm3/h przy napięciu znamionowym,
- ciśnienie w obwodzie zasilania w zakresie 300-450 KPa,
- odpowiednie ciśnienie w obwodzie już przy 50-50% napięcia znamionowego.
Pompy paliwa napędzane elektrycznie składają się z trzech zasadniczych zespołów, umieszczonych we wspólnej obudowie:
- zespołu tłoczącego,
- silnika elektrycznego,
- pokrywy.
Wykorzystywane są w pompach paliwa dwa rozwiązania konstrukcyjne zespołu tłoczącego:
- wyporowy,
- przepływowy.
W pompach wyporowych paliwo zasysane i sprężane jest w zamkniętej przestrzeni z wykorzystaniem wirujących elementów pompy i przemieszczane dalej na stronę tłoczącą (wysokiego ciśnienia). W przypadku tej konstrukcji pomp zasilających stosuje się rozwiązania rolkowo-komorowe lub zębate o zazębieniu wewnętrznym. Pompy wyporowe mają zastosowanie przy wysokich ciśnieniach w układach zasilania (od 400 KPa). Zdecydowaną ich zaletą jest praca przy niskim napięciu. Od wartości napięcia uzależniona jest charakterystyka działania pompy. Sprawność pomp tego rodzaju wynosi do 25%. Pompę napędza silnik komutatorowy prądu stałego. W tego typu konstrukcji uzwojenie wirnika i stojana oraz komutator wraz ze szczotkami chłodzone są w trakcie pracy paliwem wypełniającym wnętrze pompy. Pary paliwa, będące w równowadze termodynamicznej z cieczą, nie wywołują zapłonu paliwa. Stojan pompy w tego typu konstrukcji mocowany jest do obudowy. Po stronie ssawnej pompy umieszczany jest filtr siatkowy, zatrzymujący większe zanieczyszczenia stałe.
Wadą tego typu pomp są hałaśliwe pulsacje ciśnienia spowodowane niedokładnością wykonania części oraz usytuowaniem pompy w układzie. Dodatkową niedoskonałością są spadki mocy spowodowane powstającymi korkami paliwa przy nagrzanym paliwie, zakłócającym ciągłość przepływu. Coraz częściej w praktyce tego typu pompy zastępowane są przez pompy przepływowe.
W konstrukcjach pomp przepływowych wirnik z wieloma łopatkami, umieszczonymi na obwodzie obraca się w komorze stworzonej przez dwie nieruchome, połączone ze sobą części obudowy. Obie części obudowy w obszarze pracy obracających się łopatek tworzą obwodowe kanały zaczynające się na wysokości otworu ssawnego, a kończące w miejscu, w którym paliwo sprężone do ciśnienia o odpowiedniej wartości opuszcza pompę. Przerwa pomiędzy początkiem i końcem kanału umożliwia zapewnienie wewnętrznej szczelności pompy. W celu polepszenia parametrów pracy pompy przy nagrzaniu paliwa wykonuje się niewielki otwór w odpowiedniej odległości kątowej od otworu ssawnego, służący odgazowywaniu paliwa. Zapewnia on wylot ewentualnych pęcherzy i korków paliwa. Ciśnienie paliwa narasta w pompie wzdłuż kanału wskutek wymiany energii pomiędzy łopatkami wirnika i cząstkami paliwa.
W pompach przepływowych występuje spiralne wirowanie znajdujących się w wirniku i kanałach objętości paliwa. W pompie obwodowo-wirnikowej kanał otacza łopatki wirnika na całym obwodzie. W pompie boczno-wirnikowej (z bocznymi kanałami) oba kanały leżą po obu stronach wirnika, przy łopatkach.
Zdecydowaną zaletą pomp przepływowych jest ich cicha praca. Ciśnienie narasta w nich w sposób ciągły i nie powoduje pulsacji paliwa. Ich sprawność wynosi od 10 do 20%.
Najczęstszymi objawami usterek pomp paliwa są:
- nadmiernie zanieczyszczone filtry paliwa,
- niedrożne przewody zasilania paliwem,
- uszkodzona pompa,
- niesprawny zawór przelewowy.
W przypadku, gdy ciśnienie tłoczenia jest prawidłowe, a ciśnienie w układzie jest nieprawidłowe, wówczas uszkodzony jest regulator ciśnienia paliwa. Bardzo niekorzystna dla elementów roboczych pompy jest nawet chwilowa praca „na sucho”, prowadząca do znacznego przyspieszenia zużycia współpracujących elementów tłoczących oraz przegrzania i przepalenia części elektrycznych pompy.
Obniżenie wydatku pompy spowodowane jest zwykle spadkiem napięcia zasilania albo uszkodzeniem obwodu zasilania lub mechanizmu napędowego silnika elektrycznego pompy.
Głównymi objawami uszkodzenia pompy paliwa są:
- spadek mocy silnika,
- nierównomierna praca silnika,
- gaśnięcie silnika w trakcie pracy,
- problemy z uruchomieniem silnika.
W celu sprawdzenia działania pompy paliwa przeprowadzany jest pomiar wydatku i maksymalnego ciśnienia. Wydatek pompy paliwa sprawdzany jest poprzez odłączenie przewodu powrotnego paliwa od regulatora ciśnienia i podłączenia przewodu ze zbiornikiem o pojemności około 2,5 m3. Przy otwartym zaworze trójdrożnym uruchamiana jest pompa przez około 30 sekund pracy na biegu jałowym i mierzona jest objętość podawanego paliwa przez pompę do zbiornika kontrolnego. Wyznaczone w ten sposób objętościowe natężenie przepływu paliwa powinno mieć wartość podaną przez producenta. Powinno ono wynosić minimum 1,5 dm3/min. W przypadku zbyt małego wydatku pompy należy sprawdzić drożność filtra paliwowego poprzez pomiar ciśnienia na wejściu do filtra paliwa z pompy. Wartość maksymalnego ciśnienia tłoczenia pompy paliwa mierzona jest przy zamkniętym zaworze trójdrożnym. Sprawdzenia dokonuje się bez uruchomienia silnika, przy załączonej pompie.
Odczytana na manometrze wartość porównywana jest z wartościami podanymi przez producenta pompy. Powinna ona mieścić się w zakresie od 0,5 do 0,8 MPa.
Ciśnienie tłoczenia pompy paliwa powinno być wyższe od ciśnienia w układzie o przynajmniej 0,2 MPa. Wartość ciśnienia systemowego sprawdza się bez uruchamiania silnika poprzez połączenie odpowiednich styków w gnieździe przekaźnika pompy. W przypadku, gdy ciśnienie systemowe jest zbyt niskie, uszkodzeniu uległ zawór regulacyjny ciśnienia paliwa, zawór przelewowy pompy określający maksymalne ciśnienie tłoczenia lub sama pompa paliwa. Przyczyną zbyt wysokiego ciśnienia paliwa na listwie zasilającej może być niedrożność przewodu odprowadzającego nadmiar paliwa z regulatora ciśnienia do zbiornika paliwa.
mgr Andrzej Kowalewski
Komentarze (1)