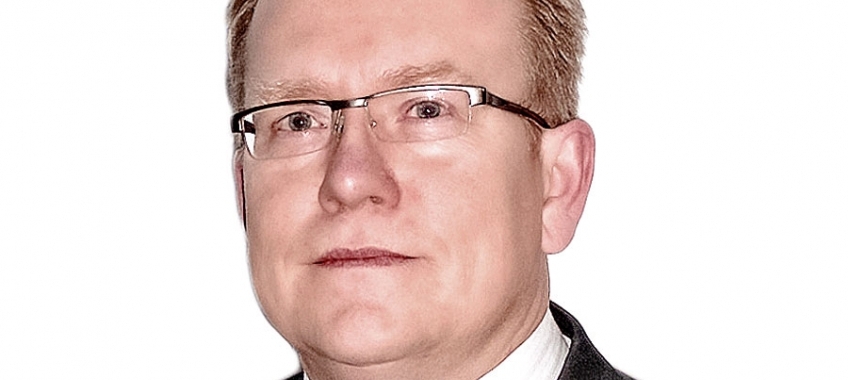
Z lakierem samochodu sytuacja jest analogiczna jak w przypadku góry lodowej. Mianowicie widzimy tylko „wierzchołek”, czyli jedną trzecią całej powłoki lakierniczej. Pozostała część lakieru ukryta jest przed naszym wzrokiem, ale to właśnie ona decyduje o tym, jak długo możemy się cieszyć idealnym wyglądem powłoki.
Na wstępie należy podkreślić, że lakierowanie fabryczne – w szczególności warstwa antykorozyjna – jest aplikowana w zupełnie inny sposób niż w trakcie naprawy lakierniczej. Grunty antykorozyjne w fabryce samochodów nakłada się poprzez kąpiele całych karoserii, a następnie ich wygrzewanie w wysokich temperaturach. Takich warunków nie jesteśmy w stanie odtworzyć w warsztacie. Mimo to producenci lakierów renowacyjnych poradzili sobie z tym wyzwaniem i oferują kompletne technologie napraw, które czasami przewyższają pod względem trwałości oryginalne, fabryczne zabezpieczenia powłok.
Wyzwaniem dla producentów lakierów renowacyjnych jest odpowiedni dobór rodzaju preparatu w zależności od rodzaju materiału, z jakiego zbudowany jest pojazd. Dzisiejsze karoserie to swoista kombinacja różnych materiałów od aluminium, stali aż po tworzywa sztuczne. Dlatego ważne jest dobranie odpowiednich materiałów i technologii do naprawy, aby w skuteczny sposób odbudować cechy ochronne karoserii.
Jak wspominałem wyżej, lakier samochodowy składa się z kilku warstw, każdej z nich przypisane jest konkretne zadanie. W zależności od przypisanej roli dzielimy je na:
- warstwę antykorozyjną,
- warstwę podkładu izolacyjnego,
- warstwę nawierzchniową dekoracyjną.
Pierwszą z tych powłok – antykorozyjną, w naprawach lakierniczych tworzy się, korzystając z dwóch rodzajów produktów: gruntu epoksydowego (np. CP 395 marki Profix) lub gruntu reaktywnego (tzw. Wash Primer, np. CP 590).
Oba produkty aplikuje się, wykorzystując pistolety natryskowe. Zacznę od zalet tych dwóch produktów. Grunty reaktywne nakłada się w bardzo cienkich warstwach (5-15 mm). Aktywatorem do tych produktów jest rozcieńczony kwas fosforowy. W wyniku kontaktu z żelazem otrzymujemy warstewkę fosforanów żelaza tworzącą skuteczną barierę przed czynnikami korozyjnymi. Ze względu na właściwości grunt reaktywny zapewnia bardzo wysoki stopień ochrony antykorozyjnej.
Z kolei zaletą podkładów epoksydowych jest doskonała przyczepności do metalu oraz silne usieciowanie, co stanowi doskonałą barierą dla wody. Wiadomo, że woda to główny czynnik powstawania rdzy. Po wysuszeniu epoksyd możemy spokojnie szpachlować. Podkłady epoksydowe mają jedną zasadniczą wadę – długi czas utwardzania.
Grunt reaktywny z kolei ma pewne ograniczenie, o którym należy bezwzględnie pamiętać – nie wolno na niego nakładać produktów poliestrowych, głównie szpachli, ponieważ następuje niepożądana reakcja chemiczna i w efekcie tego brak przyczepności. Wash Primer nie może być jedynym podkładem nałożonym na powierzchnię naprawianą, bo po pierwsze stworzy zbyt cienką powłokę, a po drugie nie można nakładać na niego lakierów bazowych. Na warstwie bazy mogą powstać przebarwienia lakieru pod wpływem kwasu fosforowego, szczególnie mocno widoczne na jasnych kolorach, np. srebrnych.
Używając gruntów, reaktywnego czy epoksydowego, możemy stosować metodę mokro na mokro, nakładając następne warstwy podkładów wypełniających. Dzięki tej technice aplikacji uzyskujemy lepszą przyczepność między kolejnymi warstwami, ale, co ważne, w znaczny sposób skracamy również czas naprawy.
Komentarze (0)