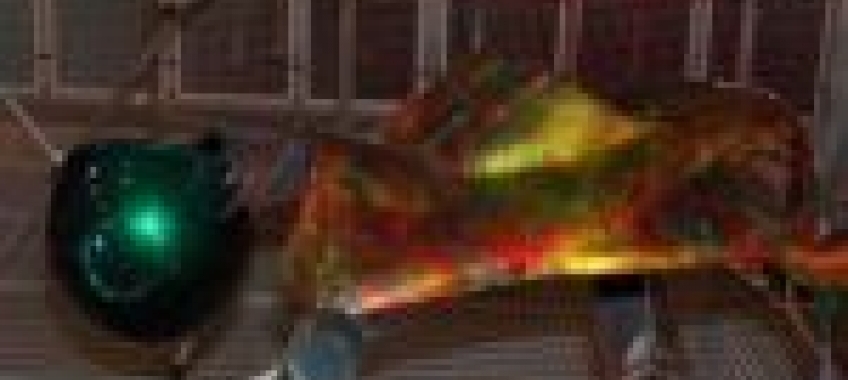
na elementy z mas plastycznych
Przygotowanie powierzchni do lakierowania
Odtłuszczenie powierzchni
Powierzchnię należy dokładnie odtłuścić i przemyć elementy za pomocą zmywacza. Do przemywania zalecany jest bezkłaczkowy miękki papier ręcznikowy o dużej zdolności wchłaniania. Używanie do przemywania tkanin bawełnianych z domieszką włókien syntetycznych oraz wełnianych powoduje, że tłuszcze oraz brud zamiast zostać usunięte z powierzchni, zostają rozcierane. Przyczyną tego jest mała zdolność wchłaniania, a drugim niepożądanym efektem jest elektryzowanie się powierzchni lakierowanej. Matowanie powierzchni przed odtłuszczeniem powoduje zapychanie się papieru tłuszczami razem z brudem i opiłkami szlifowanej powierzchni, co pociąga za sobą większe jego zużycie oraz wydłużenie czasu trwania tej czynności. Niedopuszczalne jest również nakładanie kitu szpachlowego na nie odtłuszczoną powierzchnię, a następnie szlifowanie. Efektem takiego działania jest:
po pierwsze - bardzo mała przyczepność kitu szpachlowego do powierzchni;
po drugie - podczas matowania tłuszcz zostaje wcierany w szpachel (tłuszcz ujawnia się dopiero podczas gruntowania w postaci niepozwalających się wypełnić kraterów).
Zlokalizowanie nierówności i uszkodzeń
Należy dokładnie obejrzeć elementy, aby zlokalizować wszystkie nierówności, oraz miejsca wymagające wyrównania. UWAGA! Wszystkie spękania i uszkodzenia elementów wykonanych z laminatu epoksydowego należy najpierw wypełnić żywicą epoksydową wzmocnioną matą z włókien, natomiast elementy wykonane z mas polipropylenowych lub etylenowo-propylenowych trzeba naprawić przy pomocy klejów do tego przeznaczonych. Powierzchnie płaskie nowych elementów wykonanych z laminatu należy wstępnie przeszlifować papierem ściernym P120-180, a następnie zaznaczyć miejsca wymagające wypełnienia.
Przemycie powierzchni przed szpachlowaniem
Należy zastosować środek antystatyczny do zmywania elementów wykonanych z tworzyw sztucznych, który zapobiega elektryzowaniu powierzchni w czasie przecierania. Miejsca, które mają zostać wypełnione należy dokładnie przemyć zmywaczem.
Wyrównanie powierzchni
Małe i większe nierówności powierzchni wypełniamy szpachlą poliestrową, nakładając cienkie warstwy, a następnie szlifujemy je papierem ściernym na sucho, do momentu uzyskania oczekiwanego efektu.
Szpachle:
Dwukomponentowa szpachla poliestrowa mająca doskonałą przyczepność do podłoża wykonanego z galwanizowanej lub cynkowanej blachy, aluminium, blachy nierdzewnej i włókien szklanych.
Należy pamiętać, że:
- niedopuszczalny jest sposób obróbki na mokro, zawsze na sucho;
- zawsze stosujemy zalecane proporcje przy dodawaniu utwardzacza.
Szlifowanie papierem na sucho:
- maszynowo, kolejno P80-P120-P240;
- ręcznie na bloczku, kolejno P80-P120-P240.
Po usunięciu nierówności należy cały element przeznaczony do gruntowania zmatować na sucho papierem P240.
Przemycie powierzchni przed zagruntowaniem
W pierwszej kolejności należy usunąć pył z pojazdu powstały w czasie obróbki szpachli i matowania metodą przedmuchu powietrzem. Elementy wykonane z tworzywa sztucznego należy przemyć zmywaczem.
Wypełnienie mikrootworów - elementy wykonane z tworzyw epoksydowych
Podstawowym składnikiem elementów wykonanych z laminatu jest żywica epoksydowa. W czasie sieciowania żywicy epoksydowej tworzą się mikrootwory niewidoczne dla oka, a nałożona warstwa żelkotu nie we wszystkich przypadkach jest w stanie je wypełnić. Efektem tego może być występowanie następnych niepozwalających się wypełnić kraterów. Aby uniknąć tego zjawiska, należy przed przystąpieniem do gruntowania je wypełnić.
Szpachle:
- jednokomponentowa szpachla do mikro wypełnień.
Sposób nałożenia: wcierać czystą szmatką, wykonując owalne ruchy, następnie usunąć nadmiar kitu, wcieranie powtórzyć i pozostawić do wyschnięcia około 15 min w 20oC. Usunąć wyschnięty pył za pomocą ściereczki i położyć odpowiedni podkład.
Gruntowanie powierzchni
Powłoka zwiększająca przyczepność
- elementy wykonane z twardych mas plastycznych (ABS, BMC, FRP, GFK, PA, PC, PMMA, PPO, PRO, PUR, PVC, SMC, UP) Stosujemy podkład epoksydowy, którego nakładamy jedną cienką warstwę kryjącą na elementy wykonane z tworzyw sztucznych, stosując pistolet lakierniczy o dyszy 1,4 - 1,6 mm, ciśnienie natrysku 3,5-4 bary.
Grubość powłoki: 10-15 µm.
Następną powłokę należy położyć po upływie około 15 - 20 min w temperaturze 20oC do momentu zmatowienia powłoki. W przypadkach lakierowania „mokro na mokro” lub gdy nie zachodzi konieczność wypełnienia powyżej 60 µm nakładamy podkład epoksydowy systemie “mokro na mokro”
- elementy wykonane z miękkich mas plastycznych
(AAS, ASA, EVA, FEP, HDPE, MODPE, PA, PC, PE, PEP, PET, PP, PPC, PPE, PPF, PTE, TPE, TPO, TPR, PBT, PS, PU, PUR, RRIM, SAN)
Można zastosować gotowy do użytku podkład – przylepiec przeznaczony do pokrywania mas plastycznych opisanych powyższymi symbolami.
Nakładamy jedną cienką warstwę pistoletem lakierniczym o dyszy 1,3 - 1,5 mm, ciśnienie natrysku 3,5-4 bara. Grubość warstwy po wysuszeniu 5µm. Następne warstwy powłoki należy położyć po upływie 30 min w temperaturze 20oC.
Powłoka wypełniająca
Stosujemy wypełniacz natryskowy dwu-składnikowy w przypadkach gdzie wymagane jest duże wypełnienie do 200µm. Aby uzyskać większą elastyczność warstwy wypełniającej należy po zmieszaniu składników dodać 10% środka zmiękczającego. W przypadku bardzo elastycznych mas plastycznych dodajemy do 20% środka zmiękczającego.
Należy pamiętać, że:
- proporcja farby do utwardzacza jest stała, gęstość farby regulujemy ilością rozpuszczalnika;
- należy zachować odpowiednie przerwy pomiędzy warstwami na odparowanie rozpuszczalników zawartych w mieszaninie;
- czas odparowania rozpuszczalnika możemy skrócić lub wydłużyć stosując odpowiedni rozcieńczalnik;
- czas odparowania zależy od grubości warstwy farby, od temperatury i ilości wymiany powietrza w komorze lakierniczej.
Warstwy podkładu nakładamy pistoletem o dyszy 1,8 mm (ciśnienie 4 bary) Okres przydatności po zmieszaniu to około 2,5 godz. (20°C). Grubość powłoki
- 50-70 µm - dwie warstwy, elementy gruntowane w pozycji pionowej
- 80-100 µm - trzy warstwy, elementy gruntowane w pozycji pionowej (miejsca szpachlowane oraz ich otoczenie)
- 60-80 µm - dwie warstwy, elementy gruntowane w pozycji poziomej (miejsca szpachlowane)
- 150-200 µm – miejsca wymagające dużego wypełnienia, nakładane maksimum trzy warstwy.
- zastosowanie pistoletów lakierniczych o zredukowanej ilości mgły lakierniczej HVLP może zwiększyć wydajność używanych farb o 10-20 proc. w porównaniu z wydajnością pistoletów konwencjonalnych.
Czas schnięcia wynosi:
- 20°C – 5 godz. (przed matowaniem przesuszyć w 60°C – 15 min);
- 60°C – 40 min;
- 70°C – 30 min.
Matowanie powierzchni gruntowanej
Aby skutecznie zlokalizować rysy, dziurki, małe wgłębienia przeoczone w trakcie równania powierzchni należy przed matowaniem pokryć powierzchnię pudrem kontrolnym lub cienką warstwą czarnej farby. Do matowania zagruntowanych powierzchni płaskich należy używać szlifierek mimośrodowych o minimalnej średnicy talerza f150mm.
Matować papierem na sucho:
- maszynowo f150 - papierem P320-P400
- ręcznie P320-P400 (gąbka z papierem ściernym drobnym i bardzo drobnym)
Dopuszczalne jest szlifowanie powyższego podkładu na mokro papierem o gradacji P400-800.
Następnie dokonujemy mycia powierzchni. Kolejny etap to poprawki wyrównujące powierzchnię, przeszlify, wypełnienie małych dziurek.
W przypadku stwierdzenia małych zadrapań dziurek około 1,5 mm, należy wypełnić je kitem szpachlowym. Wszystkie przeszlify do szpachli oraz do gołego tworzywa należy pokryć podkładem epoksydowym przed nałożeniem warstwy kolorystycznej.
Lakierowanie lakierem zewnętrznym
Przemycie powierzchni
Lakierowanie lakierem zewnętrznym o bezpośrednim połysku
Stosujemy dwuczęściowy lakier zewnętrzny o dużym połysku, odporny na działanie środków chemicznych.
Aby uzyskać większą elastyczność warstwy kolorystycznej, należy po zmieszaniu składników według proporcji dodać 10 proc. środka zmiękczającego. W przypadku bardzo elastycznych mas plastycznych dodajemy do 20 proc. środka zmiękczającego. Maksymalna ilość dodawanego środka uelastyczniającego wynosi 20 proc. w stosunku do gotowej mieszanki lakieru. Taką proporcję stosuje się jednak w przypadku bardzo elastycznych tworzyw. Nadmierna ilość rozcieńczalnika spowoduje utratę połysku. Dopuszczalne odstępstwo od normy to +/- 10% proc.
Ilość powłok:
- jedną średnią warstwę,
- jedną pełną do rozlania.
Pistoletem o dyszy 1,4-1,6 mm,
ciśnieniem od 3,5-4,5 bara.
Grubość powłoki: 40-60 µm - dwie
warstwy.
Dorota Kropelnicka – Babiak
PRONET COLOR ®
Komentarze (0)