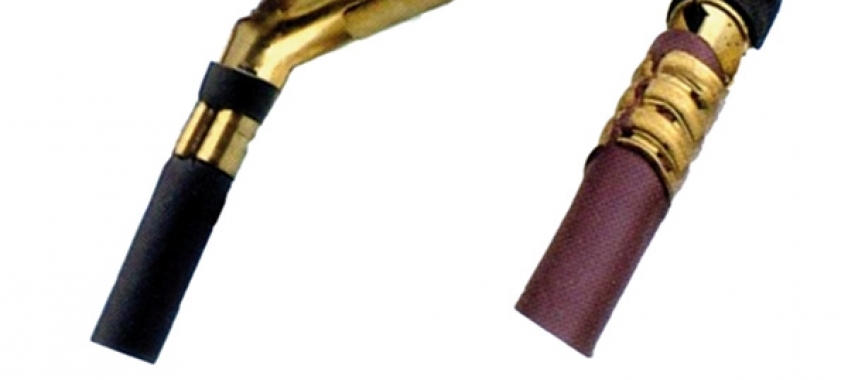
Wysoka jakość przewodów zapłonowych zależy od wielu czynników. Wielkie znaczenie odgrywa oczywiście surowiec, z którego wykonany jest kabel, ale wcale nie mniejsze zastosowana na poszczególnych etapach produkcji technologia oraz wykorzystywany park maszynowy. Gdy jest on zautomatyzowany, maleje prawdopodobieństwo popełnienia jakiegokolwiek błędu i jednocześnie rośnie szansa, że ewentualne wadliwe wyroby zostaną szybko wyeliminowane. Jak zatem wygląda proces produkcji od chwili, gdy odpowiedni kabel trafi już do nowoczesnego zakładu wytwarzającego przewody zapłonowe?
Operacja po operacji
Pierwszym etapem procesu produkcyjnego jest cięcie przewodu dostarczanego na dużych szpulach na odcinki o odpowiedniej długości. W zależności od rodzaju kabla wykonuje się to przy użyciu różnego oprzyrządowania, choć na takich samych maszynach. Następnie w przypadku przewodu z rdzeniem miedzianym lub węglowym przeprowadzane są następujące operacje:
- odizolowanie końcówki kabla;
- wywinięcie rdzenia;
- zaciśnięcie końcówki metalowej;
- sprawdzenie rezystancji.
Nieco inaczej cykl ten przebiega przy przewodach z rdzeniem wire wound (nierdzewnym przewodnikiem elektrycznym gęsto, spiralnie nawiniętym na rdzeń ferromagnetyczny), gdyż po cięciu następuje:
- wbicie spinki kontaktowej;
- sprawdzenie przewodności, wywinięcie spinki kontaktowej;
- zaciśnięcie końcówki metalowej;
- sprawdzenie rezystancji.
Dodatkowa spinka kontaktowa sporządzona z odpowiedniego metalu jest stosowana przede wszystkim po to, by przeciwdziałać powstawaniu ogniska korozji elektrochemicznej, które istotnie może zmniejszyć przepływ prądu. Niestety, w przypadku przewodów z rdzeniem węglowym zjawiska tego nie sposób wyeliminować tak prostą metodą.
Dwa typy
Końcówki metalowe znajdujące się z jednej i drugiej strony każdego przewodu mogą być zaciskane na dwa sposoby. Pierwszy i starszy, czyli „w serce“ (zacisk w przekroju poprzecznym ma kształt serca), dość powszechnie stosowany jest wciąż do połączeń o niedużym obciążeniu mechanicznym i termicznym oraz do przewodów o izolacji o dużej wytrzymałości na rozdarcie. Drugi, tzn. „na okrągło”, możliwy do wykonania tylko za pomocą bardzo precyzyjnych narzędzi, wykorzystywany jest z kolei do przewodów o izolacji podatnej na rozerwanie (np. w przewodach silikonowych) oraz wszędzie tam, gdzie konieczne będzie umieszczenie zaciśniętej końcówki metalowej w specjalnej obudowie, która wymaga zachowania kształtu kołowego. Warto podkreślić, że po zaciśnięciu końcówek (w dowolny sposób) zawsze powinno nastąpić sprawdzenie rezystancji przewodu. Trzeba tu oczywiście uwzględnić, iż przewody z rozłożoną opornością mają rezystancję zależną od ich długości.
Automaty górą
W nowoczesnych zakładach wytwarzających przewody zapłonowe wszystkimi opisanymi powyżej operacjami zajmuje się jedna zautomatyzowana maszyna wykonująca je w jednym cyklu. Wielką zaletą takiego urządzenia jest to, że sterowanie nim odbywa się komputerowo, a zatem proces produkcyjny można łatwo przeprogramować. Urządzenia te ponadto gwarantują nieustanną kontrolę wykonywanych operacji, a także umożliwiają ciągłe zbieranie danych pomiarowych. Odmiennie wygląda tylko produkcja przewodów z rdzeniem miedzianym i specjalnymi końcówkami z opornikiem. W tym przypadku po odcięciu kawałka przewodu końcówka (z opornikiem) jest wkręcana bezpośrednio w jego metalowy rdzeń.
Niezbędna precyzja
Kolejny etap produkcji to montaż osłon izolujących, wykonywanych z różnego rodzaju materiałów oraz w rozmaitych kształtach w zależności od przeznaczenia przewodów. Osłony te względem końcówki metalowej powinny zostać osadzone bardzo precyzyjnie, by zapewnić później szybki, bezproblemowy i dokładny montaż na świecy zapłonowej bądź w rozdzielaczu zapłonu.
Powstają wiązki
Do tej pory przewody o różnych długościach znajdowały się oddzielnie. W końcu jednak przychodzi czas na skompletowanie z nich wiązek. W przypadku wiązek, które wymagają połączenia przewodów specjalnym uchwytem jest to wykonywane na odpowiednim stanowisku. Większość konfekcjonuje się jednak od razu do opakowań zbiorczych lub bezpośrednio do indywidualnych. Do pudełka, w zależności od potrzeb i wymagań klienta, wkładane są wówczas także dodatkowe uchwyty lub inne wyposażenie.
Ciągła kontrola
Przed wysłaniem do odbiorcy zapakowane już wiązki poddawane są losowej kontroli przez dział jakości. Wcześniej, na każdym z etapów produkcji, wnikliwemu sprawdzeniu podlegały pojedyncze przewody. Badana była m.in. ich rezystancja, a to w celu weryfikacji jakości kabla oraz połączeń pomiędzy jego rdzeniem i metalowymi końcówkami. Każdej powstającej wiązce przez cały proces jej produkcji towarzyszy karta kontrolna. W istotny sposób ułatwia to wykrycie, a następnie eliminowanie ewentualnych zakłóceń w procesie wytwarzania. Z kolei staranna organizacja i zsynchronizowanie kolejnych etapów produkcji sprzyja zapewnieniu wysokiego poziomu jakościowego produktów i ma pozytywny wpływ na funkcjonowanie całego zakładu.
Komentarze (0)