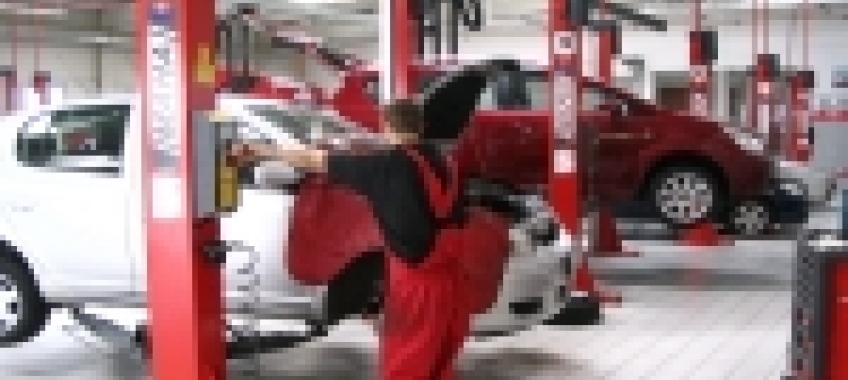
w halach obsługowo-naprawczych
Obiekty serwisowe samochodów należą do najliczniejszej grupy obiektów zaplecza motoryzacji. Wyróżnia je duża różnorodność, od małych jedno- lub dwustanowiskowych warsztatów, do dużych kompleksów obsługowo–naprawczych samochodów ciężarowych i autobusów. W przeciwieństwie do stacji kontroli pojazdów, nie ma jednoznacznych wytycznych określających wyposażenie technologiczne warsztatów obsługowych. Obiekty te powinny jednak spełniać wymagania w zakresie warunków technicznych dla obiektów budowlanych i bezpieczeństwa pracy oraz zapewniać komfort pracy podczas wykonywania czynności obsługowych. Jednak podstawową zasadą obowiązującą przy projektowaniu powinna być funkcjonalność tych obiektów. Warunek ten – wbrew pozorom – nie jest łatwy do spełnienia.
Ogólne zasady dotyczące projektowania warsztatów samochodowych
Czas użytkowania obiektu budowlanego zazwyczaj znacznie przekracza czas związany z trwałością wyposażenia technologicznego i użytkowania pojazdów, których parametry techniczne były brane pod uwagę przy projektowaniu. Zatem, podstawowym zagadnieniem jest umiejętność doboru rozwiązań w zakresie technologii i organizacji pracy w obiekcie, z uwzględnieniem trwałości substancji budowlanej, przewidywanego postępu techniki samochodowej i urządzeń obsługowo–naprawczych oraz rozwoju firmy. Inaczej powinien być zaprojektowany i wyposażony obiekt, którego czas użytkowania ocenia się na około 10 lat, w porównaniu z obiektem, dla którego nie określa się perspektywy czasowej użytkowania. W pierwszym przypadku przyjęte rozwiązania technologiczne powinny być związane z trwałością zastosowanych urządzeń, tzn. można założyć, że po dającym się określić w przybliżeniu czasie nastąpi np. modernizacja obiektu ze zmianą organizacji pracy, wymianą urządzeń, remontem substancji budowlanej itd. W przypadku drugim obiekt powinien być tak zaprojektowany, aby możliwa była zmiana aranżacji stanowisk czy wymiana urządzeń bez potrzeby wykonywania adaptacyjnych prac budowlanych. Wymaga to m.in. zaprojektowania podłoża o odpowiedniej nośności na określonej powierzchni, wysokości hali oraz takiego prowadzenia instalacji technicznych, aby możliwa była zmiana usytuowania punktów przyłączeń. Przy projektowaniu rozmieszczenia stanowisk należy uwzględnić także konieczność przeprowadzania prac obsługowych zamontowanych urządzeń. Prowadzenie prac związanych z naprawą urządzeń obsługowych na stanowisku nie powinno zakłócać pracy na stanowiskach sąsiednich.

Fot. 1. Minimalna szerokość stanowiska do obsługi samochodów osobowych powinna wynosić 4 m. Długość pola pracy powinna zapewnić pas roboczy z przodu pojazdu o szerokości ok. 1,2–1,5 m, a z tyłu min. 0,8 m. Fot. WSOP.

Fot. 2. Podnośniki podposadzkowe zapewniają wysoki komfort pracy. Fot. WSOP.
Etapy projektowania
Podczas projektowania obiektu warsztatowego podstawowe znaczenie ma w miarę dokładne sprecyzowanie przeznaczenia obiektu, określenie zakresu prac obsługowo–naprawczych jakie będą wykonywane i typów obsługiwanych samochodów. Na podstawie przyjętych założeń powinny być określone wymagania dotyczące minimalnych wymiarów stanowisk pracy, tzw. pola pracy i wysokości “w świetle” nad stanowiskiem. Niezbędne jest określenie czy będą stosowane podnośniki całopojazdowe, kanały obsługowo–naprawcze oraz specjalistyczne stanowiska, takie jak naprawy nadwozi, komory lakiernicze, stanowiska diagnostyki podwozia, montażu ogumienia oraz myjnie bramowe. Stanowiska specjalistyczne wymagają dodatkowej przestrzeni roboczej związanej z montażem różnego rodzaju wyposażenia dodatkowego. Następnym etapem powinno być ustalenie liczby poszczególnych rodzajów stanowisk oraz wymagań dotyczących ciągów komunikacyjnych. Można przyjąć, że na hali obsługowo–naprawczej szerokość minimalnego przejścia pomiędzy elementami wyposażenia trwale mocowanymi do podłoża (lub elementem a ścianą) powinna wynosić 0,8 m (min. 70 cm). Szerokość pasa komunikacyjnego, który będzie wykorzystywany do transportu części zamiennych i opakowań z materiałami eksploatacyjnymi nie powinna być mniejsza niż 1,5 m.

Tabela 1. Wymiary pól pracy.
Stanowisko robocze obsługi samochodów powinno zapewniać niezbędne pole pracy do wykonywania czynności obsługowo–naprawczych. Można przyjąć, że dla samochodów o d.m.c. do 3,5 tony szerokość przestrzeni roboczej nie powinna być mniejsza niż 1,1–1,2 m, a dla pojazdów o d.m.c. powyżej 3,5 tony – 1,5 m. Przy czym w przypadku, gdy stanowiska znajdują się obok siebie, część pasa roboczego między samochodami może być traktowana jako wspólna dla obu stanowisk. Można przyjąć, że minimalna szerokość stanowiska do obsługi samochodów osobowych wynosi 4 m, samochodów dostawczych 4,4 m, samochodów ciężarowych i autobusów 5,5 m. Długość pola pracy powinna zapewnić pas roboczy z przodu pojazdu o szerokości ok. 1,2–1,5 m, a z tyłu min. 0,8 m. Wymiary pól pracy przedstawiono w tabeli 1. W przypadku urządzeń obsługowych, na stałe mocowanych do posadzki, należy uwzględnić powierzchnię technologiczną, niezbędną do zamontowania urządzenia i jego funkcjonowania, np. przestrzeń zajętą przez ruchome elementy, wymagany niezbędny dostęp związany z utrzymaniem czystości czy pracami naprawczymi oraz pole pracy związane z wykorzystywaniem tych urządzeń. Pole pracy urządzeń może częściowo znajdować się w obrębie pola pracy stanowiska obsługowego (rys. 1).

Rys. 1. Przykład rozmieszczenia urządzeń przy stanowiskach podnośnikowych (schemat firmy WSOP).
Określenie rodzaju stanowisk, ich wyposażenia oraz minimalnych pól pracy jest niezbędne do obliczenia wymiarów powierzchni warsztatowej. W przypadku stosowania rozmieszczenia równoległego stanowisk, przynajmniej z jednej strony, z przodu lub z tyłu pojazdów, powinien być zapewniony transportowy pas komunikacyjny o szerokości 1,5 m. (rys. 2). Pas komunikacyjny może zajmować wspólną powierzchnię z polem pracy, ale nie może być zajęty przez stałe wyposażenie technologiczne, np. pulpity sterujące, stoły lub szafki warsztatowe itp.

Fot. 3. Kanał czy podnośnik? W przypadku pojazdów o d.m.c. do 3,5 tony tańszym rozwiązaniem jest podnośnik. Przy pracach wykonywanych przez jednego pracownika korzystanie z kanału jest kłopotliwe oraz zmusza do długotrwałego przyjmowania niewygodnej pozycji. Fot. WSOP.
W przypadku stanowisk wyposażonych w podnośniki kolumnowe należy uwzględnić minimalne odległości między kolumnami podnośników znajdujących się obok siebie oraz kolumnami a ścianami. Minimalna odległość między elementami na stałe mocowanymi do podłoża powinna być zachowana bez względu na to czy planowane jest przejście między nimi, czy nie. Związane jest to zarówno z wymogami bezpieczeństwa pracy, jak i umożliwieniem wykonywania prac obsługowych urządzeń (rys. 3). W przypadku stanowisk z kanałami obsługowo–naprawczymi wymiary stanowiska powinny uwzględniać obecność schodów prowadzących do kanału i wyjść awaryjnych (rys. 4). Jeżeli planowane jest boczne usytuowanie schodów, to nie powinny one zawężać pasa roboczego wzdłuż samochodu. Odrębnym zagadnieniem jest wzajemne usytuowanie stanowisk w hali warsztatowej. Przy wspólnej bramie wjazdowej i wyjazdowej dla kilku stanowisk należy uwzględnić niezbędną przestrzeń manewrową, zapewniająca, prawidłowy najazd na stanowisko. Niezbędne jest również uwzględnienie minimalnych promieni skrętu dla poszczególnych grup pojazdów (tabela 2).

Rys. 2. Przykład rozmieszczenia stanowisk podnośnikowych dla samochodów osobowych (schemat firmy WSOP).

Rys. 3. Rozmieszczenie stanowisk podnośnikowych bez przejścia między kolumnami podnośników sąsiednich stanowisk (schemat firmy WSOP).
Szerokość przestrzeni manewrowej zależy także od rodzaju wyposażenia stanowiska. Przy najeździe na stanowisko kanałowe lub podnośnikowe z najezdnicami, samochód przed stanowiskiem powinien być ustawiony do jazdy na wprost. Na stanowiskach wyposażonych w podnośniki dwukolumnowe lub stemplowe możliwa jest korekta kierunku najazdu w obrębie stanowiska.
Kanał czy podnośnik?
Stanowiska obsługowo-naprawcze mogą być wyposażone w kanały obsługowe, podnośniki na stałe zamontowane na stanowisku, podnośniki przestawne (stanowiska płaskie). Na wybór rodzaju stanowiska ma wpływ planowany rodzaj prac jaki będzie wykonywany na stanowisku, rodzaj obsługiwanych pojazdów, planowane nakłady inwestycyjne, ograniczenia wynikające z konstrukcji obiektu czy terenu, na którym obiekt jest zlokalizowany. W przypadku prac związanych z obsługami okresowymi samochodów stanowiska kanałowe są najbardziej uniwersalne. Na tym samym, prawidłowo zaprojektowanym i wykonanym, kanale można z powodzeniem obsługiwać zarówno małe samochody osobowe, jak i duże samochody ciężarowe. Kanał może być wyposażony w instalacje technologiczne i urządzenia znacznie ułatwiające prace naprawcze podzespołów o znacznej masie. Zagwarantowany jest szybki i bezpośredni dostęp do wszystkich elementów podwozia samochodu. W przypadku wieloczłonowych zestawów niektóre czynności obsługowe, jak np. kontrolę i regulację geometrii układu jezdnego, można wykonać właściwie wyłącznie na stanowisku kanałowym. Przy pracach związanych z koniecznością naprzemiennego dostępu do elementów układu jezdnego lub zawieszenia od strony zewnętrznej i wewnętrznej kół, przy pracach wykonywanych przez jednego pracownika, korzystanie z kanału jest kłopotliwe ze względu na konieczność częstego przechodzenia wzdłuż kanału i wykorzystywania schodów. Wykonywanie na stanowiskach kanałowych czynności naprawczych czy regulacyjnych w obrębie kół jezdnych w samochodach osobowych zmusza pracownika do długotrwałego przyjmowania bardzo niewygodnej pozycji.

Fot. 4. Kanał może być wyposażony w instalacje technologiczne oraz urządzenia ułatwiające prace naprawcze podzespołów o znacznej masie. Fot. WSOP.
Koszty wykonania stanowiska kanałowego są porównywalne z kosztami podnośników całopojazdowych, a w przypadku samochodów o d.m.c. do 3,5 tony mogą być nawet wyższe. Niekorzystne warunki geologiczne terenu, na którym zlokalizowany jest obiekt, np. wysoki poziom wód gruntowych, mogą znacznie zwiększyć koszty budowy kanału. Przy kalkulacji kosztów związanych z wykonaniem stanowiska kanałowego należy uwzględnić wykonanie kanału w stanie surowym, o konstrukcji nośnej przystosowanej do obciążeń masą obsługiwanych samochodów, wykonanie obrzeża kanału zapewniającego możliwość użytkowania podnośników kanałowych, zapewnienie prawidłowego odwodnienia dna, wykończenie powierzchni dna i ścian zapewniające łatwość utrzymania w czystości, wykonanie instalacji wentylacji (minimum nawiewnej) do kanału, zapewniającej odpowiedni komfort pracy, oraz instalacji oświetlenia, wykonanie instalacji technologicznych w kanale, tj. sprężonego powietrza, zasilania energetycznego, odbioru i dystrybucji oleju itp. Przy projektowaniu stanowisk podnośnikowych należy uwzględnić wykonanie odpowiedniej płyty nośnej lub zagłębienia fundamentowego. Składniki kalkulacji kosztów wykonania i eksploatacji stanowisk zestawiono w tabeli 3.

Rys. 4. Rozmieszczenie stanowisk obsługowych kanałowych dla samochodów ciężarowych (schemat firmy WSOP).
Stanowiska podnośnikowe mogą być stosowane w obiektach posiadających odpowiednią wysokość hali nad stanowiskiem w obrysie podnoszonego pojazdu. Dla pojazdów o d.m.c. do 3,5 tony powinno to być ok. 4,6 m (przy założonej wysokości podnoszonego pojazdu ok. 2,5 m), a dla pojazdów o d.m.c. powyżej 3,5 t ok. 5,7 m. Mniejsze wysokości mogą być stosowane w przypadku podnośników niskiego podnoszenia, np. na stanowiskach demontażu kół oraz w przypadku stosowania wyłączników krańcowych zabezpieczających przed zbliżeniem się elementu podnoszonego pojazdu do elementów konstrukcji hali lub urządzeń zawieszonych nad stanowiskiem. Zwiększenie wysokości hali związane jest z wyższymi kosztami budowy oraz eksploatacji obiektu. Zastosowanie podnośników przestawnych lub montowanych na posadzce (jeżeli spełnione są wymagania wytrzymałości podłoża) z doprowadzeniem mediów zasilających od góry umożliwia zmianę ustawienia stanowisk lub wymianę urządzeń bez konieczności wykonania kosztownych prac adaptacyjnych. Rozwiązania tego typu są korzystne zwłaszcza w obiektach przeznaczonych do intensywnego użytkowania, których wyposażenie musi myć często modyfikowane w zależności od potrzeb wynikających ze zmieniającej się gamy obsługiwanych pojazdów.

Tabela 2. Promienie skrętu samochodów, jakie należy przyjąć projektując rozmieszczenie stanowisk.

Tabela 3. Składniki kalkulacji wykonania i eksploatacji różnych typów stanowisk.
Autor artykułu jest pracownikiem naukowym Politechniki Śląskiej. Współpracuje z firmą WSOP z Gliwic. W swoim portfelu projektów ma ponad 1000 realizacji.
dr inż. Jan Filipczyk
Artykuł jest przedrukiem z “Poradnika Serwisowego” firmy WSOP, wydanie 5.
Obiekty serwisowe samochodów należą do najliczniejszej grupy obiektów zaplecza motoryzacji. Wyróżnia je duża różnorodność, od małych jedno- lub dwustanowiskowych warsztatów, do dużych kompleksów obsługowo–naprawczych samochodów ciężarowych i autobusów. W przeciwieństwie do stacji kontroli pojazdów, nie ma jednoznacznych wytycznych określających wyposażenie technologiczne warsztatów obsługowych. Obiekty te powinny jednak spełniać wymagania w zakresie warunków technicznych dla obiektów budowlanych i bezpieczeństwa pracy oraz zapewniać komfort pracy podczas wykonywania czynności obsługowych. Jednak podstawową zasadą obowiązującą przy projektowaniu powinna być funkcjonalność tych obiektów. Warunek ten – wbrew pozorom – nie jest łatwy do spełnienia.
Ogólne zasady dotyczące projektowania warsztatów samochodowych
Czas użytkowania obiektu budowlanego zazwyczaj znacznie przekracza czas związany z trwałością wyposażenia technologicznego i użytkowania pojazdów, których parametry techniczne były brane pod uwagę przy projektowaniu. Zatem, podstawowym zagadnieniem jest umiejętność doboru rozwiązań w zakresie technologii i organizacji pracy w obiekcie, z uwzględnieniem trwałości substancji budowlanej, przewidywanego postępu techniki samochodowej i urządzeń obsługowo–naprawczych oraz rozwoju firmy. Inaczej powinien być zaprojektowany i wyposażony obiekt, którego czas użytkowania ocenia się na około 10 lat, w porównaniu z obiektem, dla którego nie określa się perspektywy czasowej użytkowania. W pierwszym przypadku przyjęte rozwiązania technologiczne powinny być związane z trwałością zastosowanych urządzeń, tzn. można założyć, że po dającym się określić w przybliżeniu czasie nastąpi np. modernizacja obiektu ze zmianą organizacji pracy, wymianą urządzeń, remontem substancji budowlanej itd. W przypadku drugim obiekt powinien być tak zaprojektowany, aby możliwa była zmiana aranżacji stanowisk czy wymiana urządzeń bez potrzeby wykonywania adaptacyjnych prac budowlanych. Wymaga to m.in. zaprojektowania podłoża o odpowiedniej nośności na określonej powierzchni, wysokości hali oraz takiego prowadzenia instalacji technicznych, aby możliwa była zmiana usytuowania punktów przyłączeń. Przy projektowaniu rozmieszczenia stanowisk należy uwzględnić także konieczność przeprowadzania prac obsługowych zamontowanych urządzeń. Prowadzenie prac związanych z naprawą urządzeń obsługowych na stanowisku nie powinno zakłócać pracy na stanowiskach sąsiednich.
Fot. 1. Minimalna szerokość stanowiska do obsługi samochodów osobowych powinna wynosić 4 m. Długość pola pracy powinna zapewnić pas roboczy z przodu pojazdu o szerokości ok. 1,2–1,5 m, a z tyłu min. 0,8 m. Fot. WSOP.
Fot. 2. Podnośniki podposadzkowe zapewniają wysoki komfort pracy. Fot. WSOP.
Etapy projektowania
Podczas projektowania obiektu warsztatowego podstawowe znaczenie ma w miarę dokładne sprecyzowanie przeznaczenia obiektu, określenie zakresu prac obsługowo–naprawczych jakie będą wykonywane i typów obsługiwanych samochodów. Na podstawie przyjętych założeń powinny być określone wymagania dotyczące minimalnych wymiarów stanowisk pracy, tzw. pola pracy i wysokości “w świetle” nad stanowiskiem. Niezbędne jest określenie czy będą stosowane podnośniki całopojazdowe, kanały obsługowo–naprawcze oraz specjalistyczne stanowiska, takie jak naprawy nadwozi, komory lakiernicze, stanowiska diagnostyki podwozia, montażu ogumienia oraz myjnie bramowe. Stanowiska specjalistyczne wymagają dodatkowej przestrzeni roboczej związanej z montażem różnego rodzaju wyposażenia dodatkowego. Następnym etapem powinno być ustalenie liczby poszczególnych rodzajów stanowisk oraz wymagań dotyczących ciągów komunikacyjnych. Można przyjąć, że na hali obsługowo–naprawczej szerokość minimalnego przejścia pomiędzy elementami wyposażenia trwale mocowanymi do podłoża (lub elementem a ścianą) powinna wynosić 0,8 m (min. 70 cm). Szerokość pasa komunikacyjnego, który będzie wykorzystywany do transportu części zamiennych i opakowań z materiałami eksploatacyjnymi nie powinna być mniejsza niż 1,5 m.
Tabela 1. Wymiary pól pracy.
Stanowisko robocze obsługi samochodów powinno zapewniać niezbędne pole pracy do wykonywania czynności obsługowo–naprawczych. Można przyjąć, że dla samochodów o d.m.c. do 3,5 tony szerokość przestrzeni roboczej nie powinna być mniejsza niż 1,1–1,2 m, a dla pojazdów o d.m.c. powyżej 3,5 tony – 1,5 m. Przy czym w przypadku, gdy stanowiska znajdują się obok siebie, część pasa roboczego między samochodami może być traktowana jako wspólna dla obu stanowisk. Można przyjąć, że minimalna szerokość stanowiska do obsługi samochodów osobowych wynosi 4 m, samochodów dostawczych 4,4 m, samochodów ciężarowych i autobusów 5,5 m. Długość pola pracy powinna zapewnić pas roboczy z przodu pojazdu o szerokości ok. 1,2–1,5 m, a z tyłu min. 0,8 m. Wymiary pól pracy przedstawiono w tabeli 1. W przypadku urządzeń obsługowych, na stałe mocowanych do posadzki, należy uwzględnić powierzchnię technologiczną, niezbędną do zamontowania urządzenia i jego funkcjonowania, np. przestrzeń zajętą przez ruchome elementy, wymagany niezbędny dostęp związany z utrzymaniem czystości czy pracami naprawczymi oraz pole pracy związane z wykorzystywaniem tych urządzeń. Pole pracy urządzeń może częściowo znajdować się w obrębie pola pracy stanowiska obsługowego (rys. 1).
Rys. 1. Przykład rozmieszczenia urządzeń przy stanowiskach podnośnikowych (schemat firmy WSOP).
Określenie rodzaju stanowisk, ich wyposażenia oraz minimalnych pól pracy jest niezbędne do obliczenia wymiarów powierzchni warsztatowej. W przypadku stosowania rozmieszczenia równoległego stanowisk, przynajmniej z jednej strony, z przodu lub z tyłu pojazdów, powinien być zapewniony transportowy pas komunikacyjny o szerokości 1,5 m. (rys. 2). Pas komunikacyjny może zajmować wspólną powierzchnię z polem pracy, ale nie może być zajęty przez stałe wyposażenie technologiczne, np. pulpity sterujące, stoły lub szafki warsztatowe itp.
Fot. 3. Kanał czy podnośnik? W przypadku pojazdów o d.m.c. do 3,5 tony tańszym rozwiązaniem jest podnośnik. Przy pracach wykonywanych przez jednego pracownika korzystanie z kanału jest kłopotliwe oraz zmusza do długotrwałego przyjmowania niewygodnej pozycji. Fot. WSOP.
W przypadku stanowisk wyposażonych w podnośniki kolumnowe należy uwzględnić minimalne odległości między kolumnami podnośników znajdujących się obok siebie oraz kolumnami a ścianami. Minimalna odległość między elementami na stałe mocowanymi do podłoża powinna być zachowana bez względu na to czy planowane jest przejście między nimi, czy nie. Związane jest to zarówno z wymogami bezpieczeństwa pracy, jak i umożliwieniem wykonywania prac obsługowych urządzeń (rys. 3). W przypadku stanowisk z kanałami obsługowo–naprawczymi wymiary stanowiska powinny uwzględniać obecność schodów prowadzących do kanału i wyjść awaryjnych (rys. 4). Jeżeli planowane jest boczne usytuowanie schodów, to nie powinny one zawężać pasa roboczego wzdłuż samochodu. Odrębnym zagadnieniem jest wzajemne usytuowanie stanowisk w hali warsztatowej. Przy wspólnej bramie wjazdowej i wyjazdowej dla kilku stanowisk należy uwzględnić niezbędną przestrzeń manewrową, zapewniająca, prawidłowy najazd na stanowisko. Niezbędne jest również uwzględnienie minimalnych promieni skrętu dla poszczególnych grup pojazdów (tabela 2).
Rys. 2. Przykład rozmieszczenia stanowisk podnośnikowych dla samochodów osobowych (schemat firmy WSOP).
Rys. 3. Rozmieszczenie stanowisk podnośnikowych bez przejścia między kolumnami podnośników sąsiednich stanowisk (schemat firmy WSOP).
Szerokość przestrzeni manewrowej zależy także od rodzaju wyposażenia stanowiska. Przy najeździe na stanowisko kanałowe lub podnośnikowe z najezdnicami, samochód przed stanowiskiem powinien być ustawiony do jazdy na wprost. Na stanowiskach wyposażonych w podnośniki dwukolumnowe lub stemplowe możliwa jest korekta kierunku najazdu w obrębie stanowiska.
Kanał czy podnośnik?
Stanowiska obsługowo-naprawcze mogą być wyposażone w kanały obsługowe, podnośniki na stałe zamontowane na stanowisku, podnośniki przestawne (stanowiska płaskie). Na wybór rodzaju stanowiska ma wpływ planowany rodzaj prac jaki będzie wykonywany na stanowisku, rodzaj obsługiwanych pojazdów, planowane nakłady inwestycyjne, ograniczenia wynikające z konstrukcji obiektu czy terenu, na którym obiekt jest zlokalizowany. W przypadku prac związanych z obsługami okresowymi samochodów stanowiska kanałowe są najbardziej uniwersalne. Na tym samym, prawidłowo zaprojektowanym i wykonanym, kanale można z powodzeniem obsługiwać zarówno małe samochody osobowe, jak i duże samochody ciężarowe. Kanał może być wyposażony w instalacje technologiczne i urządzenia znacznie ułatwiające prace naprawcze podzespołów o znacznej masie. Zagwarantowany jest szybki i bezpośredni dostęp do wszystkich elementów podwozia samochodu. W przypadku wieloczłonowych zestawów niektóre czynności obsługowe, jak np. kontrolę i regulację geometrii układu jezdnego, można wykonać właściwie wyłącznie na stanowisku kanałowym. Przy pracach związanych z koniecznością naprzemiennego dostępu do elementów układu jezdnego lub zawieszenia od strony zewnętrznej i wewnętrznej kół, przy pracach wykonywanych przez jednego pracownika, korzystanie z kanału jest kłopotliwe ze względu na konieczność częstego przechodzenia wzdłuż kanału i wykorzystywania schodów. Wykonywanie na stanowiskach kanałowych czynności naprawczych czy regulacyjnych w obrębie kół jezdnych w samochodach osobowych zmusza pracownika do długotrwałego przyjmowania bardzo niewygodnej pozycji.
Fot. 4. Kanał może być wyposażony w instalacje technologiczne oraz urządzenia ułatwiające prace naprawcze podzespołów o znacznej masie. Fot. WSOP.
Koszty wykonania stanowiska kanałowego są porównywalne z kosztami podnośników całopojazdowych, a w przypadku samochodów o d.m.c. do 3,5 tony mogą być nawet wyższe. Niekorzystne warunki geologiczne terenu, na którym zlokalizowany jest obiekt, np. wysoki poziom wód gruntowych, mogą znacznie zwiększyć koszty budowy kanału. Przy kalkulacji kosztów związanych z wykonaniem stanowiska kanałowego należy uwzględnić wykonanie kanału w stanie surowym, o konstrukcji nośnej przystosowanej do obciążeń masą obsługiwanych samochodów, wykonanie obrzeża kanału zapewniającego możliwość użytkowania podnośników kanałowych, zapewnienie prawidłowego odwodnienia dna, wykończenie powierzchni dna i ścian zapewniające łatwość utrzymania w czystości, wykonanie instalacji wentylacji (minimum nawiewnej) do kanału, zapewniającej odpowiedni komfort pracy, oraz instalacji oświetlenia, wykonanie instalacji technologicznych w kanale, tj. sprężonego powietrza, zasilania energetycznego, odbioru i dystrybucji oleju itp. Przy projektowaniu stanowisk podnośnikowych należy uwzględnić wykonanie odpowiedniej płyty nośnej lub zagłębienia fundamentowego. Składniki kalkulacji kosztów wykonania i eksploatacji stanowisk zestawiono w tabeli 3.
Rys. 4. Rozmieszczenie stanowisk obsługowych kanałowych dla samochodów ciężarowych (schemat firmy WSOP).
Stanowiska podnośnikowe mogą być stosowane w obiektach posiadających odpowiednią wysokość hali nad stanowiskiem w obrysie podnoszonego pojazdu. Dla pojazdów o d.m.c. do 3,5 tony powinno to być ok. 4,6 m (przy założonej wysokości podnoszonego pojazdu ok. 2,5 m), a dla pojazdów o d.m.c. powyżej 3,5 t ok. 5,7 m. Mniejsze wysokości mogą być stosowane w przypadku podnośników niskiego podnoszenia, np. na stanowiskach demontażu kół oraz w przypadku stosowania wyłączników krańcowych zabezpieczających przed zbliżeniem się elementu podnoszonego pojazdu do elementów konstrukcji hali lub urządzeń zawieszonych nad stanowiskiem. Zwiększenie wysokości hali związane jest z wyższymi kosztami budowy oraz eksploatacji obiektu. Zastosowanie podnośników przestawnych lub montowanych na posadzce (jeżeli spełnione są wymagania wytrzymałości podłoża) z doprowadzeniem mediów zasilających od góry umożliwia zmianę ustawienia stanowisk lub wymianę urządzeń bez konieczności wykonania kosztownych prac adaptacyjnych. Rozwiązania tego typu są korzystne zwłaszcza w obiektach przeznaczonych do intensywnego użytkowania, których wyposażenie musi myć często modyfikowane w zależności od potrzeb wynikających ze zmieniającej się gamy obsługiwanych pojazdów.
Tabela 2. Promienie skrętu samochodów, jakie należy przyjąć projektując rozmieszczenie stanowisk.
Tabela 3. Składniki kalkulacji wykonania i eksploatacji różnych typów stanowisk.
Autor artykułu jest pracownikiem naukowym Politechniki Śląskiej. Współpracuje z firmą WSOP z Gliwic. W swoim portfelu projektów ma ponad 1000 realizacji.
dr inż. Jan Filipczyk
Artykuł jest przedrukiem z “Poradnika Serwisowego” firmy WSOP, wydanie 5.
Komentarze (0)