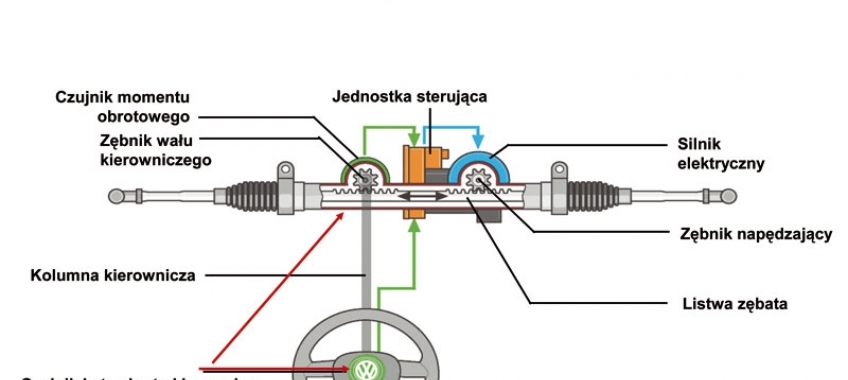
Układy EPS wypierają z rynku układy hydrauliczne dzięki nowoczesnym rozwiązaniom technologicznym, takim jak automatyczna korekta kierunku jazdy czy kompensacja niezrównoważenia na kole kierownicy. Konstrukcje tego typu idą w kierunku zmniejszenia liczby komponentów systemu, a miniaturyzacja i redukcja połączeń lutowanych w sterownikach jeszcze bardziej podnosi reżim prac warsztatowych.
W przeciwieństwie do tradycyjnych układów hydraulicznych elektryczne wspomaganie kierownicy EPS (Electronic Power Steering System) napędzane jest silnikiem elektrycznym, który pozwala na wykorzystanie energii wyłącznie podczas faktycznych manewrów kierownicą. Kiedy np. podczas jazdy na wprost lub skręcania kierownica pozostaje w pozycji nieruchomej, silniczek nie włącza się, przez co nie zużywa energii. Ten walor cieszy nie tylko zatroskanych zmniejszeniem energochłonności pojazdów silnikowych – wszak ze zmniejszeniem zużycia paliwa idzie w parze redukcja emisji dwutlenku węgla do atmosfery. Przewagą EPS nad hydraulicznymi układami jest łatwość adaptacji zaawansowanych systemów komfortu i bezpieczeństwa, takich jak system wspomagania parkowania (Park Assist), system kontroli momentu obrotowego (Steering Torque Control) i systemów utrzymania pojazdu na pasie ruchu (Lane Keeping Systems). Do wspomnianych funkcji należą też coraz częściej: integracja z elektronicznymi programami kontroli stabilności, kompensacja sił bocznych, kompensacja ściągania w trakcie przyśpieszania.
Skonstruowanie układu kierowniczego obywającego się bez mechanicznego połączenia kierownicy z kierowanymi kołami pojazdu (mowa o rozwiązaniu Steer-by-Wire) już od dawna jest technicznie realne, a uzasadniane pokusą indywidualizacji stylu jazdy przez m.in. dostrajanie oporu kierownicy, więc i trybu pracy układu, który aktywujemy w dowolnej chwili spośród kilku propozycji (np. Sport, Normal, Snow, Eco). Takie układy znajdziemy np. w modelach Infiniti Q50, w których (poprawnie działający) układ kierowniczy pozbawiony jest mechanicznego połączenia kierownicy z przekładnią. Sygnał z kierownicy przesyłany jest drogą elektroniczną do siłownika, który napędza przekładnię kierowniczą. Tego typu koncepcje otwierają nowe możliwości wyjątkowych interfejsów prowadzenia i estetyki oraz elastyczności montażu układów EPS we wnętrzu i pod maską samochodu.
Przybliżając coraz to bardziej zaawansowane układy kierownicze, nie sposób nie pokusić się o pytanie, na co mamy – mechanicy – jeszcze wpływ, a co stanowi przykład awansu technologii, więc i konieczną praktykę tylko wymiany „starego na nowe”?
- Zacznijmy od ogólnej uwagi dotyczącej części powypadkowych – wszystkie one obarczone są ryzykiem z powodu braku możliwości wiarygodnej oceny pod kątem uszkodzeń osłabiających wytrzymałość. Naturalnie to właśnie może stanowić zagrożenie dla bezpieczeństwa kierowców i pasażerów – dowodzi Ryszard Iskra, dyrektor ds. technicznych Nexteer Automotive Poland. - Dodatkową komplikacją związaną z układami kierowniczymi wspomaganymi elektrycznie jest fakt, że są one wyposażone w skomplikowane i precyzyjne układy elektryczne i elektroniczne, które w szczególności podatne są na uszkodzenia zarówno mechaniczne, jak i elektryczne. Ponadto oprogramowanie, jak i układy elektroniczne sterujące pracą układu kierowniczego podlegają nieustannym zmianom, a wersja oprogramowania układu kierowniczego musi być kompatybilna z wersją programu zainstalowanego w danym samochodzie. Niewiele warsztatów dysponuje odpowiednim oprogramowaniem pozwalającym na poprawne zestrojenie systemu z samochodem i jego adaptacji po ponownym montażu. O ile system będzie funkcjonalny, o tyle istnieje ryzyko, że nie będzie on pracował optymalnie. Co więcej, może on zaburzać poprawną pracę systemów kontroli trakcji i rozdziału mocy, potencjalnie także systemu ABS, a to bezpośrednio wpływa już na bezpieczeństwo.
Budowa współczesnych układów kierowniczych oznacza wysoki reżim prac regulacyjnych w warsztacie. Przykładowo, z uwagi na dużą współzależność pomiędzy czujnikiem kąta skrętu i układem CAN-Bus już nawet sama diagnostyka awarii może być skomplikowana. W razie problemów należy sprawdzić wtedy alternator i akumulator, czujnik kąta skrętu, jednostki sterujące oraz połączenia elektryczne. Należy także sprawdzić, czy aby oprogramowanie jednostek sterujących jest jeszcze aktualne.
Jedno jest pewne. Jeżeli przekładnia jest wymieniana z powodu kolizji drogowej, inne elementy współpracujące, takie jak obręcze kół, opony, rama pomocnicza, elementy zawieszenia osi i mechaniczne połączenia, powinny zostać skontrolowane i w razie potrzeby naprawione lub wymienione. Wtedy też nakrętki, śruby, elementy uszczelniające i zabezpieczenia wymieniamy tylko na nowe. Skoro postęp jest nieubłagany, to nic dziwnego, że taka operacja wymagać będzie coraz częściej także nowego zestawu okablowania pomiędzy przekładnią kierowniczą a elektroniką pojazdu. Przykładowo, w pojazdach grupy VW (Audi, Seat, Škoda, VW) stosowane są przekładnie kierownicze ze wspomaganiem silnikiem elektrycznym ZF Servolectric trzech generacji.
- Trzecia generacja przekładni weszła do wyposażenia seryjnego pojazdów Grupy Volkswagena w 2008 r. Obecnie na rynku wtórnym oferowane są wyłącznie przekładnie III generacji, ale można je również zamontować w pojazdach mających w wyposażeniu oryginalnym przekładnie I lub II generacji. Z myślą o praktyce warsztatowej stworzyliśmy poradnik szkoleniowy, który pozwoli na montaż „nowej w miejsce starej” – podkreśla Grzegorz Fedorowicz, ZF Services. - Podczas wymiany przekładni konieczna jest też wymiana okablowania, które nie jest oferowane wraz z przekładnią. Okablowanie, właściwe dla danego pojazdu, jest dostępne w autoryzowanych serwisach danej marki pojazdu. Wymagane jest też zastosowanie dedykowanego testera diagnostycznego, np. VCDS Software.
W przekładniach kierowniczych Servolectric I i II generacji czujnik momentu obrotowego i czujnik skrętu były umieszczone osobno. Czujnik momentu obrotowego był zabudowany w przekładni i w przypadku jego uszkodzenia należało wymienić całą przekładnię. Czujnik kąta skrętu znajdował się na kolumnie kierowniczej. W przekładni III generacji oba te czujniki są zintegrowane i umieszczone przy przekładni, a uszkodzenie jednego z nich również wymaga wymiany całej przekładni. Różnica dotyczy też montażu. Przekładnie I i II generacji miały 4 punkty mocowania, a przekładnia III generacji tylko 3.
Podejmując się wymiany generacji I oraz II na generację III, kierownicę ustawiamy na wprost (koła przedniej i tylnej osi muszą się pokrywać) i blokujemy ją w tej pozycji. Na czas demontażu przekładni wyłączamy obwód zasilania prądem (zapłon), zdejmujemy też klemę bieguna ujemnego akumulatora, odłączamy połączenia elektryczne i dopiero wtedy możemy przystąpić do demontażu drążków kierowniczych.
- Nowa przekładnia jest dostarczana w podstawowej konfiguracji elektronicznej (Default Software). Przed demontażem uszkodzonej przekładni I lub II generacji należy zgrać ze sterownika ECU dane robocze do pamięci urządzenia diagnostycznego, np. ZF Testman Pro. Brakująca adaptacja jest sygnalizowana w testerze przez oznaczenie „KL.000” – podpowiada Z. Fedorowicz. - Oprócz mechanicznych czynności związanych z wymontowaniem i zamontowaniem przekładni oraz podłączeniem okablowania należy dokonać też adaptacji czujników i jednostki sterującej. Po pierwsze, urządzeniem diagnostycznym trzeba zaadaptować czujnik kąta skrętu. Wewnętrzny czujnik skrętu musi zostać dezaktywowany, gdyż wcześniejsze wersje nie miały wewnętrznego czujnika i wykorzystywały sygnał z czujnika zewnętrznego. Przy problemach z adaptacją czujnika skrętu trzeba przeprowadzić manualnie proces adaptacji. Wartość adaptacyjna (dla większości testerów) „0” oznacza, że czujnik skrętu w przekładni jest aktywowany, a wartość adaptacyjna „1” – czujnik skrętu w przekładni jest nieaktywny. Po drugie, należy zaadaptować diagnoskopem jednostkę sterującą wspomagania.
W trakcie montażu pamiętajmy, by uszczelniacz na przekładni posmarować środkiem antyadhezyjnym (ślizgowym), a przed przykręceniem śrub precyzyjnie wypozycjonować przekładnię. Po posadowieniu przekładni należy uważać, aby uszczelniacz na przekładni przylegał bez zagięć do powierzchni styku płyty montażowej. Zwróćmy też uwagę na czystość powierzchni uszczelniających oraz szczelność osłon i na ich ewentualne uszkodzenia (przykładowo, otwór w karoserii należy uszczelnić, by zapobiec przedostawaniu się wody do kabiny). Po pracach mechanicznych podłączamy wtyczki elektryczne do gniazd i minusową klemę akumulatora, a pojazd poddajemy kontroli (i korekcie) geometrii osi według danych producenta.
Powyższe czynności stanowią gwarancję długotrwałego i... szczelnego zabezpieczenia przekładni. W przypadku montażu przekładni kierowniczej ZF Parts z zamontowanym fabrycznie drążkiem kierowniczym i gumowymi osłonami dodatkowe uszczelnianie nie jest już konieczne. Podczas montażu przekładni kierowniczych marki ZF Parts bez dołączonych osłon rekomendowane jest stosowanie wyłącznie elementów gumowych marki Lemförder. Zaczepy zapinające osłony powinny być zawsze zakładane przy użyciu odpowiednich narzędzi i zgodnie z instrukcją dostarczoną przez producenta. Dlaczego to takie ważne?
- Nietypowe hałasy oraz konieczność użycia większej niż normalnie siły do skrętu kierownicą, występujące po wymianie przekładni, mogą być spowodowane nieszczelnością układu kierowniczego. Przyczyną problemów są zwykle niskiej jakości gumowe osłony, które nie przylegają ściśle do przekładni. Również w przypadku drążków kierowniczych dostarczanych przez niektórych producentów średnica uszczelek różni się od tej stosowanej w oryginalnych zamiennikach. ZF Services stanowczo odradza też używanie złączek i cybantów w celu naprawy lub dopasowania gumowych osłon, ponieważ może to prowadzić do jeszcze większej nieszczelności oraz przedostawania się brudu i wilgoci. Efektem jest postępująca korozja drążka kierowniczego – dodaje Z. Fedorowicz.
Rafał Dobrowolski
Fot. ZF Services
Komentarze (0)