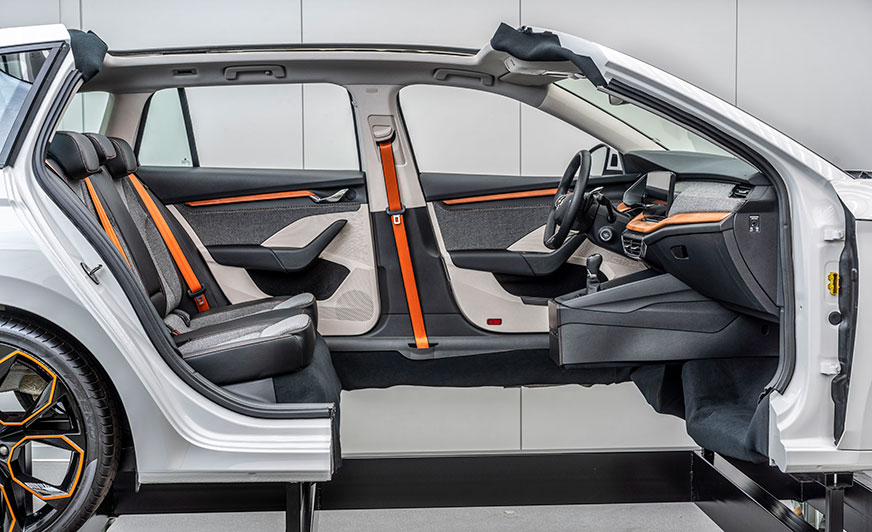
Dla modeli ENYAQ iV i KAROQ dostępne są już tkaniny wykonane w 70% z przetworzonych butelek. Po recyklingu są one zamieniane w przędzę. Pokrowce na siedzenia w modelu ENYAQ iV (w wersji wyposażenia Lodge Design Selection) są wykonane z połączenia przędzy
W miejsce Dyrektywy 2000/53/WE wejdzie zapowiadane unijne rozporządzenie, które będzie obowiązywało w każdym kraju Unii Europejskiej. Niedawno ruszyły konsultacje wniosku w sprawie wymogów dotyczących obiegu zamkniętego w odniesieniu do projektowania pojazdów i zarządzania tymi wycofanymi z eksploatacji.
13 lipca 2023 r. Komisja Europejska (KE) opublikowała Proposal for a Regulation on circularity requirements for vehicle design and on management of end-of-life vehicles (tj. wniosek dotyczący rozporządzenia w sprawie wymogów dotyczących obiegu zamkniętego w odniesieniu do projektowania pojazdów i zarządzania pojazdami wycofanymi z eksploatacji). Wniosek dotyczy rozporządzenia w sprawie wymogów dotyczących obiegu zamkniętego w projektach pojazdów i zarządzania pojazdami wycofanymi z eksploatacji, zmieniającego rozporządzenia (UE) 2018/858 i 2019/1020 oraz uchylającego dyrektywy 2000/53/WE i 2005/64/WE. Projekt rozporządzenia oraz dokumenty towarzyszące dostępne są m.in. na witrynie Ministerstwa Klimatu i Środowiska, gdzie do 1 września można było składać propozycje.
KE zaproponowała nowe środki prawne mające na celu zwiększenie obiegu zamkniętego w sektorze motoryzacyjnym. Preferowanym wariantem jest podejście polegające na stopniowym objęciu nowymi przepisami UE większej liczby pojazdów poprzez wymaganie od producentów dostarczania informacji na temat ich składu. 25% plastiku użytego do budowy nowego samochodu będzie musiało pochodzić z recyklingu – to jedno z założeń nowej propozycji, która ma wspomóc transformację.
W propozycji pojawia się także zestaw minimalnych wymagań dotyczących przetwarzania wycofanych z eksploatacji pojazdów kategorii L3e-L7e, ciężarówek, autobusów i przyczep. Oczekuje się, że preferowany wariant będzie miał pozytywny wpływ na środowisko poprzez ograniczenie śladu środowiskowego związanego z wymogami dotyczącymi produkcji i wycofania z eksploatacji pojazdów. Ogólne korzyści dla środowiska ocenia się jako roczną redukcję ekwiwalentu CO2 o 12,3 mln ton w 2035 r. (przy 10,8 mln ton w 2030 r. do 14,0 mln ton w 2040 r.), co jest kluczem do dekarbonizacji przemysłu motoryzacyjnego. Te oszczędności CO2 w ujęciu pieniężnym stanowić mają 2,8 mld euro.
Nie tylko tworzywa sztuczne
Także stal, aluminium, miedź można by poddać recyklingowi z wyższą jakością lub ponownie wykorzystać. 350 ton pierwiastków ziem rzadkich w materiałach z magnesami trwałymi już w 2035 r. byłoby zbieranych oddzielnie w celu ponownego wykorzystania i recyklingu (oraz 1500 ton w 2040 r.), co znacznie przyczyniłoby się do realizacji celu UE, jakim jest osiągnięcie strategicznej autonomii w zakresie surowców krytycznych.
Dlaczego samochody? Ponieważ ich produkcja pochłania najwięcej zasobów. Wyliczono, że europejski sektor motoryzacyjny odpowiada za 19% zapotrzebowania przemysłu stalowego UE (ponad 7 mln ton/rok), 10% całkowitego zużycia tworzyw sztucznych (6 mln ton/rok), znaczną część popytu na aluminium (42% na całe wyposażenie transportowe, czyli ok. 2 mln ton/rok), miedź (6% na części samochodowe), gumę (65% produkcji wyrobów gumowych ogólnego przeznaczenia) oraz szkło (1,5 mln ton szkła płaskiego wyprodukowanego w UE).
KE odnotowała swoją drogą, że postęp w motoryzacji, a także przechodzenie na pojazdy bezemisyjne pociąga za sobą wzrost zapotrzebowania na miedź i surowce krytyczne.
A co to może oznaczać dla przemysłu motoryzacyjnego? Szacuje się, że koszt preferowanego wariantu wyniesie 66 euro na pojazd wprowadzony na rynek w 2035 r. Stworzy też ok. 22 tys. dodatkowych miejsc pracy, z czego blisko 80% w sektorze MŚP, głównie w podmiotach zajmujących się demontażem i recyklingiem. I, jak podkreśla się w dokumencie KE, chociaż przemysł motoryzacyjny UE poniesie pewne koszty krótkoterminowe, preferowany wariant przyniesie również oszczędności oraz nowe miejsca pracy. Oszczędności energii zmniejszą zależność Europy od materiałów pochodzących z państw trzecich.
Jak to możliwe? Preferowany wariant będzie generował zarówno koszty (związane z inwestycjami w nowe technologie), jak i przychody (związane z wyższą wartością części zamiennych i materiałów pochodzących z recyklingu). Znawcy tematu są pewni, że jakkolwiek sytuacja przejściowa będzie inna w poszczególnych państwach członkowskich i operatorach ze względu na różnice w stosowanych technologiach czy kosztach pracy, planowane zmiany znacznie wzmocnią oraz zmodernizują unijny przemysł demontażu, rozdrabniania i recyklingu. Oczekuje się też, że organy państw członkowskich poniosą ograniczone koszty związane z monitorowaniem i egzekwowaniem przestrzegania nowych przepisów.
O jakich kosztach mowa? Będą one wynikać przede wszystkim z kontroli, kontroli wywozu pojazdów wycofanych z eksploatacji i pojazdów używanych oraz konieczności dostosowania systemów rejestracji. W zamian zwiększona cyfryzacja (w zakresie zgłaszania świadectwa złomowania) poprawi nadzór nad pojazdami wycofanymi z eksploatacji i używanymi.
Przemysł motoryzacyjny coraz częściej wykorzystuje innowacyjne materiały i surowce odpadowe w celu poprawy zrównoważonego rozwoju i możliwości recyklingu pojazdów. Przy współpracy z organizacjami ekologicznymi zaczęto zbierać i poddawać recyklingowi stare sieci rybackie i plastik z oceanów
Szczegółowe instrukcje dla stacji demontażu
KE wyjaśnia, że rozporządzenie koncentruje się na kilku kluczowych elementach, a w pierwszym rzędzie skupi się na obowiązkach sprawozdawczych. Przede wszystkim producenci samochodów będą musieli zapewnić osobom zajmującym się demontażem „jasne i szczegółowe instrukcje dotyczące wymiany i usuwania części i komponentów podczas użytkowania i na etapie wycofania pojazdu z eksploatacji”.
KE chce ponadto, by 30% tworzyw sztucznych z pojazdów wycofanych z eksploatacji było poddawane recyklingowi. Dodatkowo 25% plastiku użytego do budowy nowego pojazdu będzie musiało pochodzić z recyklingu, z czego 25% z recyklingu pojazdów wycofanych z eksploatacji.
„Nowe przepisy wzmocnią odpowiedzialność producenta poprzez ustanowienie krajowych systemów rozszerzonej odpowiedzialności producenta. Systemy te będą miały na celu zapewnienie odpowiedniego finansowania obowiązkowych działań związanych z przetwarzaniem odpadów, zachęcanie podmiotów zajmujących się recyklingiem do poprawy jakości materiałów pochodzących z recyklingu pojazdów wycofanych z eksploatacji, a tym samym wspieranie ściślejszej współpracy między podmiotami zajmującymi się przetwarzaniem a producentami”, czytamy w uzasadnieniu projektowanych zmian.
Jak dodano, zakres rozporządzenia miałby być stopniowo rozszerzany o nowe kategorie pojazdów, jak motocykle, samochody ciężarowe czy autobusy. Wniosek KE będzie teraz rozpatrywany przez Parlament Europejski i Radę w ramach zwykłej procedury ustawodawczej.
Należy oczekiwać raczej zaostrzenia regulacji, skoro Bruksela podkreśla, że co roku ponad 6 mln pojazdów kończy swój żywot i jest w Europie traktowanych jako odpady. Na drodze do gospodarki cyrkularnej koncerny motoryzacyjne mają projektować i produkować swoje wyroby zgodnie z zasadami gospodarki o obiegu zamkniętym. Na rynku wtórnym mają powstawać zachęty, by używać części zregenerowanych i z recyklingu. Aby tak się stało, zbiórka pojazdów wycofywanych z eksploatacji (i przetwarzania odpadów z nich powstałych) ma być efektywniejsza. A to dopiero początek zmian, bo w niedalekiej przyszłości z uwzględnieniem rozszerzenia zakresu prawodawstwa o dodatkowe kategorie pojazdów.
Omawiany tu dokument to także czytelna definicja działalności warsztatów (z ang. repair and maintance). Za takie podmioty uznaje się zajmujących naprawami i konserwacją, co oznacza każdą osobę fizyczną lub prawną, która w związku z prowadzoną działalnością handlową, gospodarczą, rzemieślniczą lub zawodem świadczy usługi naprawcze lub konserwacyjne niezależnie od producentów lub za ich zgodą. Załączniki zawierają m.in. listę warunków, na podstawie których samochód można uznać za niezdatny do naprawy. Wylicza też ciecze i elementy, które należy usunąć ze starego samochodu na koniec użytkowania, wraz ze wskazaniem sposobu gromadzenia odpadów, które powstaną przy tych czynnościach. Określają też wytyczne co do strategii cyrkularnych producentów samochodów, wraz z aktualizacją co 5 lat i wymogiem oceny postępów z ich realizacji.
Innowacyjność jakby natura tego chciała
Na marginesie surowców krytycznych warto pewnie wspomnieć o obiecujących badaniach nad produkcją naturalnych materiałów dla zrównoważonej mobilności. Jaką rolę odgrywają obecnie zrównoważone materiały, takie jak plastikowe butelki, krowie odchody i sieci rybackie?
Recykling plastikowych butelek jest rosnącym trendem w przemyśle motoryzacyjnym, wykorzystywanym do produkcji takich elementów pojazdów, jak: dywaniki, poszycia siedzeń i materiały izolacyjne. Forvia, na przykład, opracowała Ecorium, alternatywę dla skóry zwierzęcej i sztucznej o znacznie zmniejszonym śladzie węglowym, redukując emisję CO2 do jednej trzeciej w porównaniu ze sztuczną skórą i o 90% w porównaniu ze skórą zwierzęcą. Dzięki wielowarstwowej kompozycji politereftalanu etylenu (PET) pochodzącego z recyklingu, z którego powstają również dobrze znane plastikowe butelki PET, oraz włókien konopnych Ecorium oferuje wrażenie niesamowicie wysokiej jakości. Pokrowce na fotele samochodowe wykonane z plastikowych butelek są już niemal na porządku dziennym, ponieważ były używane na przykład w pierwszym Nissanie Leaf. Stopniowo coraz więcej producentów zwraca się ku nietypowemu ponownemu zastosowaniu plastikowych butelek, jako materiału na poszycia siedzeń w samochodach. Także sieci rybackie i odpady z tworzyw sztucznych są wyławiane z morza, aby tworzyć nowe materiały dla pojazdów.
A skoro mowa o włóknach konopnych, naukowcy z firmy z siedzibą w stanie Teksas pracują nad takim akumulatorem do pojazdów zasilanych energią elektryczną. Do czynników ułatwiających wybór włókien należą niskie koszty, trwałość i porowatość. To o tyle istotne, że w przypadku baterii litowo-jonowych można by w ten sposób rozwiązać problemy z deficytem grafenu. Konopie zamiast grafenu? Grafen uważany jest za jeden z najlepszych materiałów dla elektrod superkondensatorów. Jego produkcja jest jednak bardzo droga. Szukając tańszego rozwiązania, amerykańscy naukowcy opracowali proces przekształcania odpadów konopi włóknistych w unikatowy, podobny do grafenu nanomateriał. Konopie byłyby w tym przypadku lepszym i tańszym rozwiązaniem, ponieważ ich trwałość może pomóc katodzie wytrzymać setki cykli kurczenia i rozciągania.
Póki co konopie jako surowiec odnawialny są coraz częściej wykorzystywane w przemyśle motoryzacyjnym. Ich włókna są lekkie, mocne i mają wysoką wytrzymałość na rozciąganie. Mogą być stosowane jako alternatywa dla włókien szklanych w materiałach kompozytowych w celu zmniejszenia masy pojazdów i zużycia paliwa. Mogą być również wykorzystywane do produkcji bioplastików i elementów wnętrza, dzięki czemu pojazd jest bardziej przyjazny dla środowiska.
Mimo że, podobnie jak wykorzystanie krowiego łajna jako surowca może początkowo wydawać się niezwykłe, naukowcy pracują nad przekształceniem odpadów organicznych w materiały biologiczne. Magicznym słowem jest tu dość skomplikowany termin „nanoceluloza”. Istnieją kraje, gdzie produkty papierowe wykonane ze zwierzęcego obornika są dostępne od dawna.
Pokrowce na fotele samochodowe wykonane z plastikowych butelek są już niemal na porządku dziennym, a kolejne możliwości wdrożeń dają włókna buraka jako materiału wypełniającego czy włókna konopne
Rafał Dobrowolski
Fot. materiały firm: Audi AG, Forvia, Škoda
Komentarze (0)