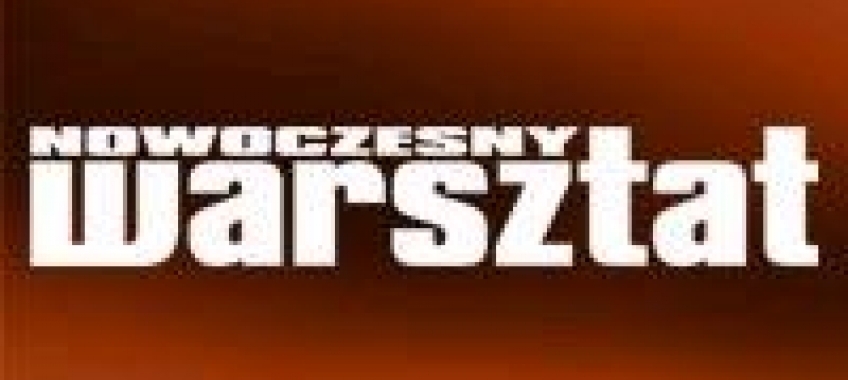
Czystość powierzchni i jej odpowiednie przygotowanie stanowi podstawę prawidłowej i skutecznej ochrony przeciwkorozyjnej, a także jest bardzo istotne dla osiągnięcia zakładanej żywotności systemu powłokowego.
Przygotowanie powierzchni do czyszczenia
Już samo przystąpienie do czyszczenia powierzchni wymaga odpowiednich przygotowań.
Norma ISO 8501 opisuje trzy klasy przygotowania powierzchni metalu:
- P1 – przygotowanie wymagane w stosunku do powierzchni eksploatowanych w warunkach niskiej agresywności
korozyjnej,
- P2 – dotyczy eksploatacji w agresywnych warunkach korozyjnych,
- P3 – dotyczy powierzchni konstrukcji eksploatowanych w bardzo agresywnej korozyjnie atmosferze.
Przygotowanie powierzchni przed czyszczeniem obejmuje przede wszystkim:
• usunięcie odprysków spawalniczych,
• sfazowanie lub zaokrąglenia wolnych krawędzi,
• zeszlifowanie lub zaszpachlowanie wżerów i wgnieceń,
• usunięcie wad spoin.
Rodzaje zanieczyszczeń powierzchni
Do podstawowych zanieczyszczeń powierzchni należą: zendra, rdza, zanieczyszczenia jonowe, zatłuszczenia, pyły i wilgoć.
Zendra
Zendra, inaczej zwana zgorzeliną, jest produktem termicznej obróbki stali w procesie jej przetwarzania. Składa się z tlenków żelaza Fe2O3 ściśle przylegających do podłoża. Grubość warstwy zendry wynosi 5 do 65 µm, a średnio 15 µm.
Pozostawienie zendry stanowi niebezpieczeństwo dla trwałości powłoki malarskiej ze względu na:
• odrywanie się od stali płatów zendry i tym samym powłoki malarskiej,
• wytworzenie się ogniwa korozyjnego zendra (katoda) – stal (anoda) w przypadku obecności elektrolitów i możliwości zaistnienia korozji wżerowej.
Rdza
Rdza jest produktem korozji stali – są to uwodnione tlenki żelaza tworzące warstwy o zmiennych grubościach i składach. Rdza może mieć różny kolor – od żółtego, poprzez odcienie żółto-czerwone, żółto-brązowe, brązowe aż do czarnego. Rdza zawiera zawsze zaadsorbowaną na swej powierzchni i wewnątrz agregatów wodę z rozpuszczonymi solami, toteż pozostawienie jej na powierzchni sprzyja powstaniu korozji podpowłokowej.
Zanieczyszczenia jonowe
Najczęściej są to sole – niewidoczne zanieczyszczenia powierzchni obniżające trwałość powłoki. Sole rozpuszczalne w wodzie, takie jak chlorki, siarczany, azotany działają destrukcyjnie na powłoki malarskie i stymulują korozję podpowłokową.
Najbardziej niekorzystny wpływ mają siarczany pochodzące z zanieczyszczeń atmosfery, a następnie chlorki osadzające się w atmosferze morskiej lub pozostające na powierzchniach zalanych wodą morską. Czyszczenie strumieniowo ścierne nie usuwa tych zanieczyszczeń.
Źródłem tych soli na powierzchni metalu mogą być m.in. chłodziwa stosowane w czasie obróbki metalu, lub chociażby sól, którą w zimie posypuje się ulice.
Pozostawienie tego typu zanieczyszczeń na powierzchni powoduje obniżenie pH oraz zwiększone chłonięcie wody, co w efekcie prowadzi do korozji galwanicznej na skutek tworzenia się ogniw stężeniowych.
Zatłuszczenia
Tego rodzaju zanieczyszczenia pochodzą z eksploatacji konstrukcji w środowiskach występowania tłuszczy, smarów, olejów, a także w wyniku procesów walcowniczych, obróbki metali. Powodują one brak przyczepności powłoki malarskiej, powstawanie “rybich oczu” oraz cofanie powłoki.
Pyły
Zapylenie atmosfery wynika z działalności przemysłu, spowodowane jest warunkami atmosferycznymi, a także prowadzeniem prac oczyszczaniu powierzchni.
Pyły sprzyjają utrzymywaniu wilgoci na powierzchni, utrudniają zwilżalność farby w procesie malowania i w efekcie obniżają przyczepność i trwałość powłoki malarskiej.
Wilgoć
Wilgoć występuje na powierzchni w wyniku:
- opadów atmosferycznych,
- mgły,
- zalania powierzchni w wyniku procesu produkcyjnego,
- przekroczenia warunków punktu rosy.
W środowisku o dużej zawartości pary wodnej powierzchnia metalu adsorbuje wodę i pokrywa się cienką warstewką molekularnej wody. W wodzie zawartej na powierzchni rozpuszczają się sole tworząc doskonałe warunki dla korozji elektrochemicznej. Rezultatem jest delaminacja pokryć, korozja podpowłokowa, pęcherzenie pokrycia.
Metody przygotowania powierzchni
Metody przygotowania powierzchni podłoża stalowego pod powłokowe pokrycia antykorozyjne szczegółowo omówiono w normach: PN-EN ISO 8504-1,2,3.
Wyróżnić można następujące rodzaje metod oczyszczania powierzchni:
- metody mechanicznego oczyszczania powierzchni,
- metody chemicznego i elektrochemicznego oczyszczania powierzchni,
- metody termicznego oczyszczania powierzchni.
Metody mechanicznego oczyszczania powierzchni
W obrębie metod mechanicznego oczyszczania powierzchni wyróżnić można oczyszczanie za pomocą narzędzi oraz oczyszczanie strumieniowe.
Do oczyszczania za pomocą narzędzi zalicza się:
Młotkowanie – opukanie oczyszczanej powierzchni za pomocą młotka zwykłego lub pneumatycznego.
Skrobanie – usuwanie za pomocą skrobaków ręcznych lub pneumatycznych luźnych produktów korozji, zniszczonych powłok ochronnych.
Szczotkowanie – usuwanie luźnych produktów korozji za pomocą ręcznych szczotek drucianych lub mechanicznych.
Iglicowanie – usuwanie resztek produktów korozyjnych z drobnych wżerów za pomocą tzw. iglic – cienkich prętów stalowych o zaostrzonych końcach.
Szlifowanie – wygładzanie ostrych krawędzi elementów, oczyszczanie złącz nitowanych, spawanych za pomocą szlifierek posiadających najczęściej elastyczne tarcze ścierne.
Polerowanie – zapewnia najwyższą gładkość powierzchni.
Oczyszczanie strumieniowo–ścierne (mechaniczne) podłoża metalowego
W wyniku zastosowania oczyszczania strumieniowo-ściernego otrzymuje się powierzchni metalicznie czyste, pozbawione zanieczyszczeń stałych, takich jak: tlenki, pozostałości lakierów i farb itp.
Metoda ta pozwala na uzyskanie najwyższego stopnia czystości powierzchni oraz jej określonej chropowatości.
Istotą tej metody są ziarna materiału ściernego unoszone w strumieniu gazu, cieczy lub gazu i cieczy, o dużej prędkości. Zostają one skierowane na przeznaczoną do czyszczenia powierzchnię. Poszczególne ziarna posiadają znaczną energię kinetyczną, która wystarcza do wykonania pracy czyszczenia. Jakość powierzchni po oczyszczaniu metodą strumieniowo-ścierną zależy od energii kinetycznej ścierniwa, jego twardości, kształtu i granulacji. Aby dokładnie usunąć wszystkie zanieczyszczenia powierzchni twardość ścierniwa musi być wyższa od twardości osadzonych zanieczyszczeń; ważne jest, aby nie ulegało ono zbytniemu rozkruszaniu i nie wbijało się w czyszczoną powierzchnię.
W zależności od sposobu naprowadzania ścierniwa można wyróżnić obróbkę strumieniowo-ścierną, pneumatyczną lub wirnikową.
Stosuje się następujące ścierniwa:
- piasek,
- żużel pomiedziowy,
- saurolit,
- piasek oliwinowy.
Metody chemicznego i elektrochemicznego oczyszczania powierzchni
Do metod chemicznych należą:
Odtłuszczanie, które może być realizowane w rozpuszczalnikach organicznych, roztworach alkalicznych lub odpowiednich emulsjach, a także przez elektrolizę oraz z wykorzystaniem ultradźwięków.
Trawienie, które może być realizowane na drodze trawienia chemicznego lub na drodze elektrolitycznej.
Polerowanie, które może być realizowane na drodze chemicznej, a przede wszystkim elektrolitycznej
Metody termicznego oczyszczania powierzchni
Oczyszczaną powierzchnię, pokrytą śladami korozji, zgorzeliny, stara powłoką malarską lub innymi zanieczyszczeniami, poddaje się działaniu płomienia pochodzącego z palnika gazowego, np. acetylenowo-powietrznego lub acetylenowo-tlenowego.
Nagrzewanie powoduje pękanie zgorzeliny, spalanie lub spulchnianie substancji organicznych czy starej powłoki malarskiej. W wyniku tego procesu powstałe zanieczyszczenia dają się łatwo usunąć różnymi metodami oczyszczania mechanicznego.
Wymagania dotyczące przygotowania powierzchni pod powłoki z tworzyw sztucznych
Dla powłok z tworzyw sztucznych, które z założenia mają zapewnić długi okres trwałości (powyżej 15 lat) wymagania można sformułować, jak niżej:
- STOPIEŃ PRZYGOTOWANIA POWIERZCHNI wg PN-ISO 8501-1 Sa 2 1/2:
oznacza to stosowanie metody strumieniowo-ściernej oraz uzyskanie co najmniej 95% powierzchni metalicznego połysku świadczącego o usunięciu rdzy i zendry.
n PROFIL POWIERZCHNI - wg PN-EN ISO 8503-2 drobnoziarnisty G:
oznacza to, że należy użyć ścierniwa ostrokątnego G (grit) o granulacji zapewniającej parametr Ry5 nie przekraczający 60 µm. Ścierniwa ostrokątne to:
– staliwne i żeliwne śruby ostrokątne,
– piasek kwarcowy,
– piasek oliwinowy.
- STOPIEŃ ODPYLENIA - wg PN-EN ISO 8502-3 – max. klasy 2:
metoda ta polega na zebraniu pyłu i kurzu z powierzchni za pomocą taśmy samoprzylepnej.
- ZATŁUSZCZENIE POWIERZCHNI - nie jest dopuszczalne. Nie ma dotąd dogodnej i prostej ruchowej metody oceny zatłuszczenia. Można m.in. zastosować:
– test wody – nie powinna zbierać się w krople,
– ekstrakcję rozpuszczalnikiem.
- OBECNOŚĆ ZANIECZYSZCZEŃ
JONOWYCH ROZPUSZCZALNYCH W WODZIE
Stosuje się metodę Bresla opisaną w normie PN-EN ISO 8502-6, a następnie oznacza się konduktometrycznie metodą podaną w PN-EN ISO 8502-9.
Należy pamiętać, że oprócz odpowiedniego przygotowania powierzchni zgodnie z przedstawionymi wymaganiami istotną rolę w trwałości zabezpieczenia odgrywa czas, po jakim zostanie na powierzchnię naniesiona powłoka. Generalnie nałożenie powłoki powinno nastąpić bezpośrednio po przygotowaniu powierzchni. W niektórych przypadkach, gdy warunki atmosferyczne są dogodne, wówczas czas ten wynosić może od 4 do 8 godzin. Stosując się do tych zasad zapewnia się, że powierzchnia nie zostanie wtórnie zanieczyszczona. Należy także pamiętać, że powierzchnia po oczyszczaniu strumieniowym jest bardziej aktywna od zupełnie gładkiej powierzchni metalu.
inż. Ewa Miler
Przygotowano na podstawie PN-EN ISO 8501-1,2,3.
Komentarze (0)