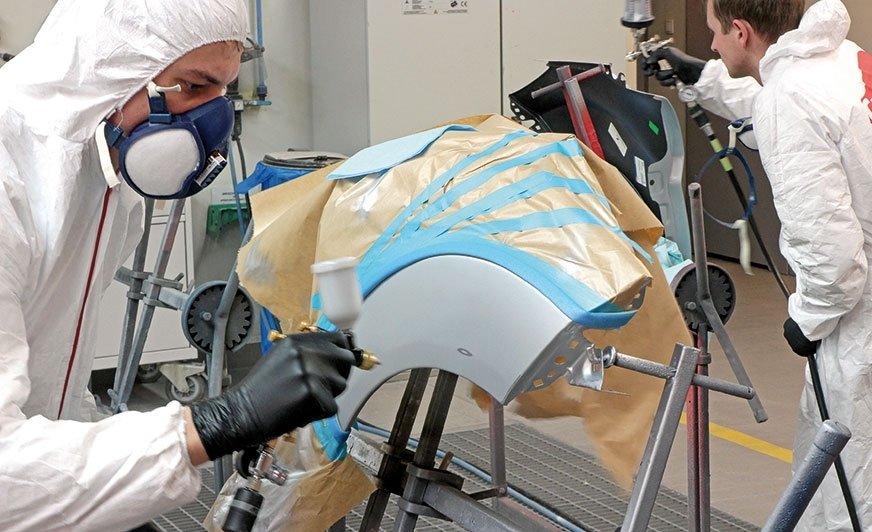
Szybkie czasy przetwarzania i doskonała wydajność energetyczna – materiały lakiernicze o takich walorach mają teraz swoje „5 minut”
Po okresie zmagań z wyzwaniami stawianymi przez pandemię warsztaty lakiernicze muszą liczyć się ze wzrostem kosztów – bez gwarancji, że sytuacja ulegnie zmianie. Bezprecedensowe tempo inflacji w ciągu ostatnich czterech kwartałów obniżyło rentowność zabiegów refinish. Jak nigdy wcześniej liczyć się będzie łatwość możliwie taniej aplikacji materiałów lakierniczych.
Sytuacja na tyle dojrzała, że różnice w kosztach energii dzięki zastosowaniu nowoczesnych lakierów bezbarwnych, które opracowano z myślą o schnięciu w możliwie krótkim czasie i w niższej temperaturze, będą przemawiały na korzyść tych typu „energy save”. I nie bez powodu, gdy mieć w pamięci, jak niemały wpływ na zużycie energii ma różnica pomiędzy temperaturą zewnętrzną a zadaną w kabinie. To wtedy koszty dostarczenia energii (oleju opałowego) różnią się diametralnie w okresie zimowym i letnim.
Szerzej o wpływie procesów technologicznych na zużycie energii w warsztacie podejmującym się prac typu refinish pisaliśmy w artykule pt. Zużycie energii i procesy lakierowania NW 3/2021, w którym na podstawie pomiarów zrealizowanych przez Axalta Coating Systems Poland Sp. z o.o. w różnych warsztatach oceniono ekonomiczność kabin wielu dostawców – acz o podobnych parametrach, zasilanych paliwem olejowym lub gazowym.
Przyjęto, że cykl lakierowania oznacza procentowy (tj. policzalny) udział każdego z trzech procesów na skali zużycia energii: lakierowania i suszenia podkładu mokro na mokro; lakierowania i suszenia lakieru bazowego; lakierowania i suszenia lakieru bezbarwnego. Po wyciągnięciu uśrednionych wyników w okazało się, że w okresie letnim (temp. +24°C) ta proporcja wygląda tak – w kolejności przywołanych procesów: 5%; 30%; 65%. A w sezonie zimowym, gdy przyjąć temperaturę rzędu -8°C, owe proporcje wyglądają tak: 17%; 38%; 45%. Zebrane informacje bazują na pomiarach z 50 warsztatów i przykładzie zlecenia lakierowania całego jednego cyklu, które składa się z dwóch nowych elementów: lakierowanych metodą mokro na mokro i cieniowanego. Technologia lakierowania obejmuje: podkład m/m, lakier bazowy wodny oraz lakier bezbarwny standardowy suszony w temperaturze elementu (60°C) przez 25 minut. Cały proces (od uruchomienia do wyłączenia kabiny lakierniczej) trwa średnio 90 minut.
Koszty zużytej energii (dla kabin lakierniczych o mocy zainstalowanej 2 x 11 kW) w okresie zimowym (-8°C) okazywały się 4-krotnie wyższe niż wtedy, gdy na zewnątrz panowała temperatura +24°C! Wniosek stąd płynie oczywisty – krótszy czas nagrzewania elementu to czysty zysk dla lakierni.
Skrócenie nieefektywnego suszenia i czasu suszenia do absolutnego minimum
Kryzys energetyczny, nazywany przez niektórych najbardziej ekstremalnym, jaki kiedykolwiek miał miejsce w Europie, pogłębia się. Przedsiębiorstwa stoją w obliczu podwójnego uderzenia spirali kosztów i rosnącej inflacji. To stąd pożądanie szybkoschnących materiałów lakierniczych.
Przykładowo, najnowszy lakier bezbarwny QRS Extreme Clear schnie tylko 5 min, a czas liczony jest od momentu, gdy kabina osiągnie 60°C i wprowadzimy element. Produkt ten stanowi rozszerzenie gamy lakierów bezbarwnych z linii QRS w portfolio Grupy CSV. Nowy lakier szybkoschnący nadaje się do napraw nie tylko 2 czy 3-elementowych, ale nawet liczniejszych, bo 5-elementowych. Co ważne, wymaga standardowego podejścia, tj. aplikacji na 1,5 warstwy, a też takich standardowych narzędzi, by wspomnieć pistolet z dyszą 1.3.
Przyspieszenie procesu lakierowania w przypadku najnowszych produktów Axalta jawi się spektakularnie, skoro zamiast 7 kroków mamy tylko 3. Produkty Fast Cure Low Energy to skrócenie czasu procesu o 50%, skrócenie czasu pracy kabiny lakierniczej o 25% i takie samo zmniejszenie zużycia farby. A w ostatecznym rozrachunku oznacza to niebagatelne zmniejszenie zużycia energii elektrycznej, bo aż o 49%, natomiast gazu o 57%. Wspomnijmy, że z technologią FCLE, czyli Fast Cure Low Energy, spotkamy wśród wielu brandów: Spies Hecker i Speed-TEC, Standox i X-treme system, Cromax i Ultra Performance Energy System.
Warsztaty lakiernicze nie muszą już wybierać między szybkim schnięciem a oszczędnością energii, np. zasilającej kabinę lakierniczą
Sprężone powietrze, ale jak bardzo zanieczyszczone?
Co można zrobić na tym polu, by było taniej? Sprężone powietrze w lakierni, tak jak zresztą w każdym innym warsztacie, potrzebne jest do: napędzania maszyn i urządzeń pneumatycznych (szlifierki, polerki, podnośniki itp.), zasilania pistoletów lakierniczych, pistoletów do mas, a też dla działania środków ochrony (maski pełne z wymuszonym przepływem powietrza).
W warsztacie sprofilowanym na usługi refinish sprężone powietrze produkują kompresory śrubowe (aktualnie najbardziej zaawansowane urządzenia) lub kompresory tłokowe (tradycyjnie dalej wykorzystywane rozwiązania). Te drugie są mniej skomplikowane oraz tańsze w nabyciu. Obojętnie jakie urządzenie, za każdym razem będziemy mieli do czynienia z szeregiem elementów, takich jak: butla, osuszacz, reduktor, a wreszcie linia przesyłowa, filtry z reduktorem i/lub naolejacz, wąż.
W poszukiwaniu oszczędności zwróćmy uwagę na rodzaj potrzebnego powietrza. Tu propozycja usystematyzowania.
– Bardzo czyste powietrze konieczne jest dla ochrony osobistej, to stąd np. filtr naścienny, 3-stopniowy z wkładem węglowym – powietrze musi być odpowiednio przygotowane, aby można było nim bezpiecznie oddychać, a ciśnienie zredukowane zgodnie z zaleceniami producentów masek lakierniczych – zaznacza Mateusz Witkowski, wiceprezes Auto-Color Witkowscy, którego firma to autoryzowany dystrybutor kabin Saico Zero w Polsce, Austrii, Czechach, Niemczech i na Słowacji. – Dla satysfakcjonujących efektów lakierowania czy nakładania mas potrzebne jest także czyste powietrze, stąd filtr 2-stopniowy. Idzie o to, by powietrze było odolejone i pozbawione wody, skoro ma przenosić materiał na naprawiany element oraz nie wywoływać wad lakierniczych. W tym przypadku kierujemy się instrukcjami urządzeń, np. pistoletów, i zaleceniami producentów materiałów lakierniczych. Jak można zmniejszyć zapotrzebowanie na sprężone powietrze? Ano stosując np. szlifierki elektryczne. Jest tak, bo do napędu szlifierki elektrycznej potrzeba mniej energii niż do wyprodukowania sprzężonego powietrza zasilającego szlifierkę pneumatyczną.
A jeśli efektywniej czerpać z instalacji sprężonego powietrza, to na pewno stosując pistolety lakiernicze oszczędne w zapotrzebowaniu na to medium. Czy też stosując szybkozłączki i minimalizując odległości między kompresorem a odbiornikiem – w myśl zasady: mniejsza odległość to mniejsza strata. Oczywiście warto regularnie serwisować maszyny i pistolety.
Często zapomina się, jak istotne w procesie lakierowania jest zapewnienie odpowiedniej jakości powietrza.
– Są lakiernicy twierdzący, że wystarczy zamontować pod pistoletem odwadniacz, aby kwestię powietrza „mieć z głowy”. Tymczasem każdy kompresor, niezależnie od rodzaju, będzie w mniejszym lub większym stopniu zanieczyszczał powietrze olejem – dowodzi Bernard Kołodziej z firmy Fama Sp. z o.o., która jest autoryzowanym reprezentantem marki SATA w Polsce. – Samo powietrze o temperaturze 25°C zawiera około 2% wody, a do tego dochodzą wszelkiego rodzaju zanieczyszczenia, które się w nim znajdują: kurz, pyły, także często dodatkowe, typowe dla warsztatów samochodowych opary olei, lakierów i innych środków chemicznych. Słowem, jeśli nie zadbamy o odpowiednie przefiltrowanie powietrza, istnieje duża szansa, że zanieczyszczenia te nałożymy razem z lakierem, a to już gwarantuje wystąpienie wad lakierniczych.
Przy naprawach punktowych można zrezygnować z kabiny lakierniczej, co daje ogromną oszczędność kosztów. Jednak wtedy system odpylania należy dobrać do stosowanego procesu produkcyjnego. Jest tak, ponieważ z reguły urządzenia odciągu mgły lakierniczej nie pozwalają na użytkowanie w trybie powietrza obiegowego! Mobilny system odciągu i oczyszczania powietrza stosujemy do mniejszych prac lakierniczych (naprawy punktowe).
Typowe wady lakiernicze spowodowane zanieczyszczeniem powietrza
Granicą dla oszczędzania powinna być jakość prac, tj. niepogorszony efekt wysiłków lakiernika. Kratery/oczka – tego typu zaokrąglone wgłębienia o średnicy sięgającej kilku milimetrów spowodowane są obecnością w powietrzu olei, smarów i silikonów. Zdarza się, że nieprzefiltrowane resztki silikonu trafiają z lakierem na powierzchnię, osłabiając przyczepność poszczególnych warstw, i tylko czekać łuszczenia się lakieru. Słaba jakość powietrza to prosta droga do wtrąceń kurzu – widocznych gołym okiem zanieczyszczeń naniesionych wraz z brudnym powietrzem. Wystąpienie dowolnej z tych wad praktycznie wymusza konieczność szlifowania i ponownego lakierowania. Marnujemy więc materiały szlifierskie, marnujemy lakier, ale przede wszystkim marnujemy czas i energię, nie mając żadnej gwarancji, że wada nie wystąpi ponownie.
– Tymczasem wysokiej klasy filtr zabezpieczający nas niemal w 100% przed tego typu problemami jest na wyciągnięcie ręki. SATA od lat produkuje sprawdzone filtry, zapewniające usuwanie zanieczyszczeń o wielkości powyżej 0,01 μm. Pierwszy stopień filtrów SATA zawiera separator cyklonowy, w którym siła odśrodkowa wirującego powietrza powoduje osiadanie ciężkich zanieczyszczeń, jak oleje i woda, na ściankach filtra, a następnie spływanie ich na dno filtra, skąd są usuwane przez automatyczny zawór. Następnie powietrze trafia na drugi stopień filtrowania, gdzie jest przepuszczone przez filtr dokładnego oczyszczania, który zatrzymuje pozostałe zanieczyszczenia. Opcjonalnie filtr może mieć 3. stopień z filtrem węglowym usuwającym także resztki aerozoli z powietrza – chwali rozwiązanie Bernard Kołodziej.
W ofercie wciąż dostępne są także poprzednie filtry SATA serii 100 występujące zarówno w wersji dwu, jak i trzystopniowej. Doskonale nadają się do pojedynczych stanowisk lakierniczych. Gdzie tkwi przewaga najnowszej propozycji? Filtry serii 500 charakteryzują się jeszcze łatwiejszą obsługą i wydłużoną trwałością wkładów węglowych. Dzięki temu komplet wkładów filtrujących wystarcza na 6 miesięcy – użytkownik nie musi martwić się ich nierównomiernym zużyciem. Dodatkowe timery przyklejane na obudowie przypominają, kiedy nadejdzie czas wymiany wkładów. Sama wymiana także jest szybka i łatwa – obudowy filtrów mają montaż bagnetowy zamiast gwintu, wyeliminowano więc sytuację, w której są za mocno dokręcone i potrzeba dodatkowych narzędzi, aby je odkręcić. Nie ma też konieczności wymiany gumowych uszczelnień.
Co więcej, filtry serii 500 mają bardzo dużą wydajność – aż 3800 l na minutę przy ciśnieniu 6 barów. Tak wysoki przepływ powietrza umożliwia stosowanie pojedynczego bloku filtrującego dla kilku stanowisk lakierniczych. A jak wiadomo, większa sprawność elementów współpracujących to większa wydajność i mniejsze straty.
Tekst i fot. Rafał Dobrowolski
Komentarze (0)