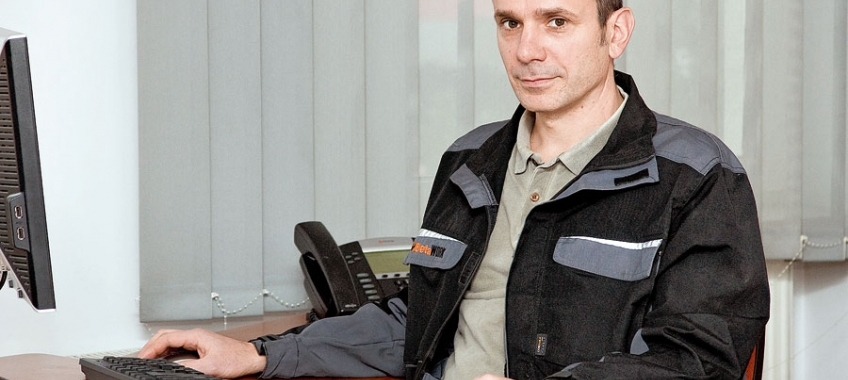
Rozmawiamy z Maciejem Młodzikowskim, specjalistą ds. badań w firmie Lumag.
- Jakie nowe rozwiązania w dziedzinie hamowania wprowadziła ostatnio firma? Czy któreś z nich można uznać za przełomowe?
Dział Badań i Rozwoju Lumag opracował nową generację ceramicznych mieszanek ciernych, niezawierającą miedzi, do klocków hamulcowych dla samochodów klasy premium. Ceramiczne klocki same w sobie mają ogromne zalety w postaci niskiego zużycia materiału ciernego, ale przede wszystkim – tarczy hamulcowej. Są dużo cichsze od tradycyjnych klocków „low steel”, najczęściej używanych w Europie, nie powodują wibracji podczas hamowania i nie brudzą felg pyłem powstającym przy zużyciu klocków i tarczy. Typową wadą zwykłych klocków ceramicznych (nazywanych też w nomenklaturze NAO – Non Asbestos Organic) jest mniejsza skuteczność hamowania w warunkach jazdy sportowej, przy dużych obciążeniach termicznych i mechanicznych. Klocki hamulcowe opracowane przez naszą firmę, przy wszystkich wspominanych zaletach, praktycznie nie mają wad związanych z mniejszym współczynnikiem tarcia podczas bardzo „ostrego” użytkowania hamulców. Dodatkowo są one"ekologiczne", nie posiadając miedzi, której to zawartość według nowych wytycznych ma być stopniowo zmniejszana aż do całkowitego jej wyeliminowania w klockach i okładzinach hamulcowych w 2025 roku.
- Na czym powinien polegać dalszy rozwój układu hamulcowego? Na których jego elementach powinni skupić się inżynierowie?
Jest z tym pewien problem. Z jednej strony na przestrzeni ostatnich dziesięcioleci trwa naturalny postęp motoryzacji polegający m.in. na zwiększaniu osiągów pojazdów samochodowych (wzrost masy, prędkości maksymalnych oraz przyspieszeń) czy powstaniu nowych kategorii pojazdów typu SUV. Ten przyrost osiągów jest spowodowany głównie znacznym zwiększeniem mocy zastosowanych silników, polepszeniem właściwości aerodynamicznych pojazdów, a w ostatnich latach także zmniejszaniem masy całkowitej. Porównajmy sobie parametry samochodów sprzed 35-40 lat. Na przykład VW Golf pierwszej generacji z podstawowym silnikiem benzynowym 1100 cm3 miał 50 KM, ważył zaledwie 750 kg i osiągał 140 km/h (w wersji GTI miał 110 KM, ważył niewiele ponad 800 kg i osiągał maksymalnie około 180 km/h). Współczesny Golf VII generacji ma najsłabszy silnik o mocy 85 KM, natomiast najmocniejsze wersje, osiągające 250 km/h – nawet do 300 KM przy masie około 1400 kg. Oczywiście zastosowanie mocniejszych silników (większe osiągi) wymusza zastosowanie mocniejszych i skuteczniejszych hamulców. Z drugiej strony, dzisiaj wydaje się, że dalsze zwiększanie osiągów tak silników, jak i hamulców nie ma większego sensu. Również warunki typowego sposobu użytkowania pojazdów, spowodowane zarówno przepisami o ruchu drogowym, jak również sytuacją, w której ogromna większość użytkowników pojazdów – także tych o bardzo dobrych osiągach – często stoi w miejskich korkach (gdzie przeciętna prędkość to 20-30 km/h), sprawiają, że mało kto wykorzystuje zarówno moc silnika, jak i możliwości hamulców. Dodajmy do tego fakt, że coraz więcej koncernów ma w swojej ofercie auta hybrydowe oraz elektryczne, a ich udział w rynku będzie się stopniowo zwiększał. W tego rodzaju pojazdach, w porównaniu do zwykłych aut, wyposażonych tylko w silniki spalinowe, hamulce mają „lżejszą pracę”, bo część ich zadania przejmuje silnik elektryczny (czasem jest ich kilka), który podczas hamowania w normalnym użytkowaniu zamienia się w prądnicę, ładując akumulatory i odzyskując dużą część energii kinetycznej, która przy użyciu tradycyjnego hamulca ciernego zamieniłaby się bezpowrotnie w ciepło. W konstrukcjach pojazdów, w tym także układów hamulcowych, widzimy takie tendencje, jak:
- nastawienie na ekologię: zmniejszenie zużycia paliwa (emisji CO2), zmniejszenie użycia materiałów nieprzyjaznych dla środowiska;
- unowocześnienie i integracja wielu systemów (np. coraz szersze zastosowanie elektrycznego hamulca postojowego, integracja układu hamulcowego z innymi systemami samochodu, np. układem kontroli trakcji, układem stabilizacji toru jazdy, automatycznego osuszania tarczy hamulcowej podczas jazdy w deszczu itd.); w samochodach całkowicie elektrycznych może występować wyeliminowanie tradycyjnej pompy hamulcowej i układu wspomagania na rzecz innego rodzaju rozwiązań, natomiast część hamulca odpowiadająca bezpośrednio za wytworzenie siły tarcia – tarcza hamulcowa, materiał cierny – nie podlegają zasadniczo rewolucji (ich zasada działania pozostaje niezmienna).
Jeśli chodzi o sam element wykonawczy, jakim jest hamulec (zacisk z klockami i z tarczą), ewolucji podlegają materiały, z których są wykonane oraz są wprowadzane pewne rozwiązania poprawiające jego pracę. Jeśli chodzi o funkcjonalność, konstruktorzy mogą zmniejszać jego masę (ale tylko do pewnego stopnia), optymalizując kształt zacisku lub typ użytego innego materiału (aluminium zamiast żeliwa sferoidalnego), zmniejszając masę klocków hamulcowych poprzez np. zastosowanie tzw. blach nośnych z lżejszych, innowacyjnych materiałów lub o specjalnych kształtach czy zmniejszenie ilości materiału ciernego (np. poprzez użycie innego o mniejszym zużyciu). Użycie materiałów do produkcji mieszanki ciernej wiąże się też z wymogami legislacyjnymi dotyczącymi ekologii. W klockach dawno już został wycofany azbest, antymon, natomiast w najbliższej przyszłości przewiduje się stopniową redukcję, aż do całkowitej eliminacji miedzi.
Co do tarcz hamulcowych, to od pewnego czasu stosuje się różne rozwiązania zmniejszające masę tego elementu i poprawiające pewne jego właściwości w wysokich temperaturach. Różni producenci mają różne rozwiązania, natomiast ogólnie koncepcja polega na zachowaniu klasycznej, wentylowanej bieżni wykonanej z żeliwa szarego i wykonanej ze stopów aluminium środkowej części tarczy (tej, która jest mocowana bezpośrednio do piasty koła). Tradycyjna tarcza żeliwna jest jednym elementem wykonanym z jednego materiału. Nowoczesne tarcze z aluminiowym mocowaniem do piasty i żeliwną bieżnią mogą być wykonywane w różnej technologii. Niektóre z tych rozwiązań polegają na tym, że najpierw wykonuje się odlew żeliwnej bieżni, następnie odlew ze stopów lekkich (środkowa część tarczy – flansza), łącząc w tym drugim kroku oba elementy. Tarcza wykonana w takiej technologii jest jednym elementem. Istnieją też rozwiązania podobne, w których element środkowy tarczy ze stopów lekkich połączony jest z tradycyjną bieżnią za pomocą śrub i różnych elementów sprężystych, podobnie jak ma to miejsce w hamulcach motocyklowych.
W niektórych drogich samochodach stosuje się też tarcze karbonowo-ceramiczne, w których bieżnia wykonana jest z bardzo lekkiego materiału i również połączona jest ze środkową częścią (flanszą) za pomocą specjalnych elementów mocujących.
Oprócz zmniejszania masy całego pojazdu wpływ na zużycie paliwa mają wszystkie opory, ruchy, które działają na samochód podczas jazdy. Główne z nich to opory aerodynamiczne i opory toczenia. Wiele elementów i zespołów samochodu mających wpływ na zmniejszenie tych wszystkich oporów poddawanych jest modyfikacjom mającym na celu zmniejszenie tych właśnie oporów. Należą do nich m.in. opony o coraz niższym oporze toczenia, a także hamulce generujące jak najmniejszy tzw. moment resztkowy.
- A co z fadingiem? Czy tu również zostało już wszystko powiedziane? Wielu producentów tarcz hamulcowych chwali się nowoczesnymi, unikalnymi rozwiązaniami tego problemu, będącego skutkiem nadmiernego wzrostu temperatury układu hamulcowego. Czy również firma Lumag ma swoje sposoby radzenia sobie z tym problemem?
Problem fadingu wiąże się ze zmniejszeniem skuteczności hamowania spowodowanej wzrostem temperatury tarczy hamulcowej i klocka. Można temu zaradzić na dwa zupełnie różne sposoby.
Pierwszy z nich to obniżenie temperatury układu hamulcowego. Krokiem milowym w tym temacie było zastąpienie hamulców bębnowych tarczowymi, a następnie, kilkanaście lat temu, wprowadzenie na szeroką skalę tarcz wentylowanych. W przypadku przednich hamulców stosowanie tego typu tarcz to dziś standard. W porównaniu z tarczami niewentylowanymi całkowita powierzchnia bieżni tarczy wentylowanej odprowadzająca ciepło do otoczenia jest znacząco zwiększona, co wiąże się z niższymi temperaturami podczas serii postępujących po sobie hamowań lub po długim zjeździe ze wzniesienia. Porównując między sobą różne rodzaje tarcz wentylowanych o podobnym kształcie czy geometrii, nie da się uzyskać tak dużych korzyści na rzecz pewnych rozwiązań nad innymi, jak między tarczą niewentylowaną i wentylowaną. Różni producenci stosują innowacyjne rozwiązania dotyczące geometrii bieżni hamulcowej (grubości jej ścianek) czy kształtu, rozmieszczenia i liczby żeberek wentylujących. Duży wpływ na dobre chłodzenie hamulców mają inne elementu pojazdu, które są odpowiedzialne za przepływ powietrza w okolicy hamulców (np. specjalne wloty ukierunkowujące strugi powietrza na hamulce, różne osłony zawieszenia czy np. rodzaj felg).
Drugim sposobem na zmniejszenie efektu fadingu jest używanie mieszanek do klocków hamulcowych o takich właściwościach, które nie będą powodowały odczucia dyskomfortu czy wręcz niebezpieczeństwa spowodowanego spadkiem skuteczności wywołanym wzrostem temperatury tarczy do 500 czy nawet 600°C. Doświadczone i dobrze wyposażone w sprzęt badawczy firmy produkujące materiały cierne są w stanie opracować i produkować materiały cierne, które zarówno dzięki specjalnemu składowi mieszanek, jak i technologii ich wytwarzania (np. odpowiednia obróbka cieplna – tzw. schorching), będą w stanie zagwarantować, że ich produkty będą zachowywały się w bardzo wysokich temperaturach niewiele gorzej niż w temperaturach niskich.
Fot. Lumag
Komentarze (0)