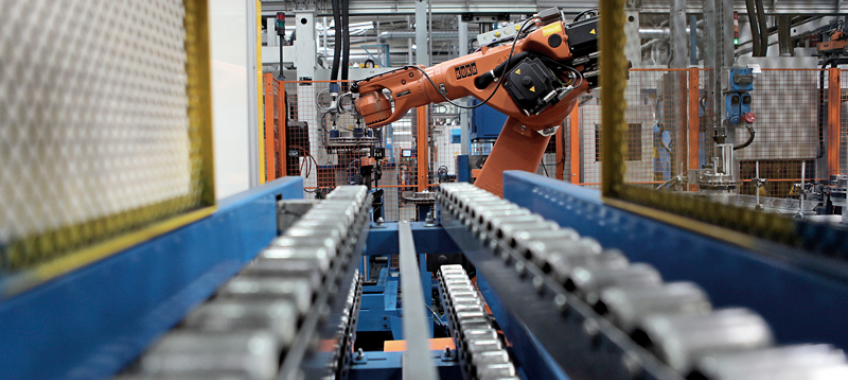
Centrum produkcyjne w Dąbrowie Górniczej jest jednocześnie ośrodkiem badawczo-rozwojowym włoskiego koncernu Brembo. To tu testuje się najnowsze rozwiązania. Tu też powstaje najwięcej tarcz hamulcowych, zarówno na pierwszy montaż, jak i na rynek wtórny. Tegoroczne spotkanie z dziennikarzami prasy branżowej stanowiło okazję do poznania technologii gwarantującej identyczną jakość produktów.
Brembo – o portfolio produktów wiele można by mówić. To oczywiście światowy lider w projektowaniu, rozwoju i produkcji układów hamulcowych oraz komponentów do samochodów, motocykli, pojazdów przemysłowych i maszyn na rynkach wyposażenia oryginalnego, wtórnego i pojazdów wyścigowych. W roku 1972 rozpoczął się fabryczny montaż hamulców Brembo w motocyklach Moto Guzzi, co w krótkim czasie zapewniło ich dostawcy pozycję europejskiego lidera na rynku jednośladów. Dziś hamulce oraz sprzęgła projektowane, produkowane i montowane w najlepszych zespołach w świecie wyścigów Formuły 1, GT Touring Car i Rally to efekt współpracy Grupy Brembo z AP Racing – wiodącą marką na rynku samochodów wyścigowych.
Globalny koncern dynamicznie umacnia swą pozycję w branży motoryzacyjnej. Firma ma 4 centra badawczo-rozwojowe, 19 zakładów produkcyjnych i 22 oddziały handlowe. Jeśli nie liczyć kryzysowego roku 2009, od co najmniej dekady Brembo notuje nieustanny wzrost obrotów. W roku 2013 wskaźnik ten wzrósł aż o 12,8%. Wiele wskazuje, że ten rok zapisze się kolejnym rekordem, a na pewno rekordem produkcji w Polsce.
Pierwszą nowoczesną odlewnię w Dąbrowie Górniczej firma uruchomiła w roku 2006 i niemal natychmiast przystąpiła tam do budowy następnego zakładu odlewniczego. Teraz oddano kolejny, więc pozycja polskiej placówki w globalnej sprzedaży na pewno wzrośnie. A przynajmniej takie wrażenie można było odnieść podczas spotkania z dziennikarzami prasy branżowej (10 lipca br.).
Gigantyczny obiekt – ponad 0,5 km długości i aż 9 hektarów powierzchni, wzbogacił się o nową halę pieców indukcyjnych. Inwestycję zrealizowano w ramach unijnego projektu pod nazwą: „Dywersyfikacja produkcji poprzez wprowadzenie tarcz hamulcowych o podwyższonym poziomie bezpieczeństwa”.
Na pewno centrum produkcyjne w Dąbrowie Górniczej jest dziś najnowocześniejszym zakładem włoskiego koncernu. Całkowita moc produkcyjna odlewni to ponad 140.000 ton rocznie. Od niedawna w piecach odlewniczych w ciągu 50 minut topi się 12 ton żeliwa, by finalny produkt mógł powstawać na 49 zautomatyzowanych gniazdach produkcyjnych. Miesięcznie produkuje się tam już milion tarcz hamulcowych. Przy okazji wspomnijmy, że najnowszym przykładem nowatorskiej technologii jest partnerski projekt zrealizowany we współpracy z Daimlerem. Nowe tarcze powstają z dwóch różnych materiałów: żeliwa i stali. Dzwon nowej tarczy jest wykonany ze stali i ma grubość tylko 2,5 mm, podczas gdy dzwony tradycyjnie wykonane z żeliwa mają grubość 7,9-9 mm. W efekcie nowe tarcze są o 10-15% procent lżejsze od tradycyjnych. Kluczowe znaczenie dla nowej technologii miało zaprojektowanie przez Brembo uzębienia na dzwonie tarczy. Inspiracją dla włoskich inżynierów była technologia kół zębatych, którą stosuje się w mechanizmach zegarków szwajcarskich. Ten szczególny kształt dzwonu pozwala również przekroczyć wysokie granice podczas prób wytrzymałościowych wymaganych przez Daimlera. Inżynierowie Brembo zawsze poszukują nowych rozwiązań technologicznych, które szanują środowisko i powalają spełnić coraz bardziej rygorystyczne wymagania rynku. Koncepcja nowych lekkich tarcz hamulcowych to ważny krok w ciągłym procesie poszukiwania sposobów na redukcję masy samochodu. Przyczynia się to do zmniejszenia zużycia paliwa, a tym samym redukcji negatywnego wpływu na środowisko naturalne – priorytetu w projektowaniu współczesnych samochodów. Istotną informacją pozostaje dewiza: produkt na pierwszy montaż i dla aftermarketu jest identyczny! Wystarczy informacja, że proces formowania zgodny z OE gwarantuje najlepszą dokładność wykonania produktu. Takiej procedurze standardowo podlegają np. okładziny cierne – procedura wypalania (thermal scorched) minimalizuje okres docierania i występowania zjawiska fadingu.
Nowością jest też rozwiązanie wprowadzone z myślą o redukcji czasochłonnych operacji – tarcze z fabrycznie zintegrowanym łożyskiem, gotowe do natychmiastowego montażu. Tarcze są wyposażone w śruby mocujące konieczne do prostego i bezpiecznego montażu. Do tego dochodzą zestawy naprawcze bębnów – oczywiście z homologacją ECE-R90, typu Kit&fit. To ponad 200 numerów referencyjnych dla zestawów ze wstępnie zmontowanymi komponentami. Jest jeszcze Standard Kit – ponad 500 numerów referencyjnych dla zestawów komponentów spakowanych oddzielnie.
Dokumentacja techniczna, kody QR, TecDoc – koncern, rozwijając cykl szkoleń technicznych uwieńczonych programem certyfikowania, tworzy też nowatorski typ Akademii Hamulcowej. Przejść przez sito egzaminu on-line nie jest wcale łatwo! Do tej pory raptem 50 profesjonalistów w Polsce otrzymało certyfikat „Brembo Expert”.
- Brembo chce podzielić się swoimi osiągnięciami z innymi specjalistami z branży, aby tym samym wspierać dążenie do rozwoju, podwyższania jakości i wprowadzania innowacyjnych rozwiązań w zakresie produkcji części. Otóż z myślą o najlepszej jakości tarcz hamulcowych nie czynimy rozróżnienia na produkt OE i dedykowany rynkowi wtórnemu – podkreślał Marco Moretti, Marketing Director Brembo. - Kilka miesięcy temu zadebiutowała nowa witryna internetowa: www.bremboparts.com. Oprócz szkoleń z cyklu Akademia Hamulcowa Brembo narodził się pomysł, aby dać każdemu możliwość zobaczenia, jak wytwarzamy tarcze, a także jak wygląda proces kontroli jakości na każdym etapie produkcji.
Dzięki najnowszej witrynie internetowej koncern rozszerzył gamę narzędzi cyfrowych z myślą o specjalistach od części zamiennych. Katalog on-line z aplikacją Brembo Parts pobrano już ponad 20.000 razy (na urządzenia Apple i Android w Europie). Ważna to informacja dla rynku warsztatowego, skoro klocki hamulcowe na rynek wtórny to ponad 1200 pozycji. Brembo to też kompletna oferta – ponad 2 tys. referencji układów hydraulicznych (cylinderki, pompy hamulcowe, zawory i korektory, siłowniki sprzęgła, pompy sprzęgła, przewody hamulcowe).
Skoro mowa o jakości produktów, globalny producent tarcz, klocków i układów hamulcowych aż 5% obrotu inwestuje w badania i rozwój, a co dziesiąty pracownik firmy to inżynier lub specjalista zatrudniony w dziale badań i rozwoju. Na miejscu przeprowadza się statyczne i dynamiczne testy. To nie wszystko. Mimo badań przeprowadzanych w czasie produkcji, szczegółowej kontroli poddawane są także wykonane gotowe odlewy. Co pół godziny losowo wybierana jest jedna tarcza, która przechodzi analizę w znajdującym się na terenie fabryki laboratorium. Badane są m.in. skład chemiczny i struktura, dokonywane są pomiary. Dość powiedzieć, że na wyposażeniu laboratorium w Brembo znajdziemy też stoły do kalibracji aparatury badawczej.
Rozbudowa zakładów w Dąbrowie Górniczej idzie w parze z dbałością o środowisko naturalne. Dbałość o jakość powietrza ma w tym regionie coraz większe znaczenie. W ciągu ostatnich dwóch lat firma Brembo potroiła liczbę malowanych tarcz hamulcowych – początkowo były one dostępne tylko dla topowych modeli, ale już w tym roku, dzięki rozwojowi technologii UV, oferta została rozszerzona do ponad 440 pozycji i tym samym obejmuje większość pojazdów na europejskich drogach, zarówno topowe marki, średni segment lub niedawno wprowadzone modele.
Technologia malowania wprowadzona przez Brembo przewiduje utrwalanie naniesionej powłoki przy użyciu promieniowania UV (stąd nazwa). Zastosowanie tego procesu przynosi znaczne korzyści dla środowiska naturalnego; farby UV są na bazie wody i, w porównaniu do tradycyjnych żywic epoksydowych lub cynkowo-nośnych powłok, nie wymagają rozpuszczalników. Zapewnia to całkowitą eliminację emisji lotnych związków organicznych, które powodują zmiany środowiskowe i są szkodliwe dla ludzkiego zdrowia. Utrwalanie powłoki przy zastosowaniu promieni UV nie wymaga wysokich temperatur, czyli wymaga mniej energii. Technologia ta eliminuje ryzyko wywołania odkształceń geometrycznych tarczy, jakie mogą wystąpić przy zastosowaniu innych technologii, np. cynkowania, które wymaga zastosowania wysokich temperatur (ponad 300°C).
Rafał Dobrowolski
Fot. Brembo
Komentarze (0)