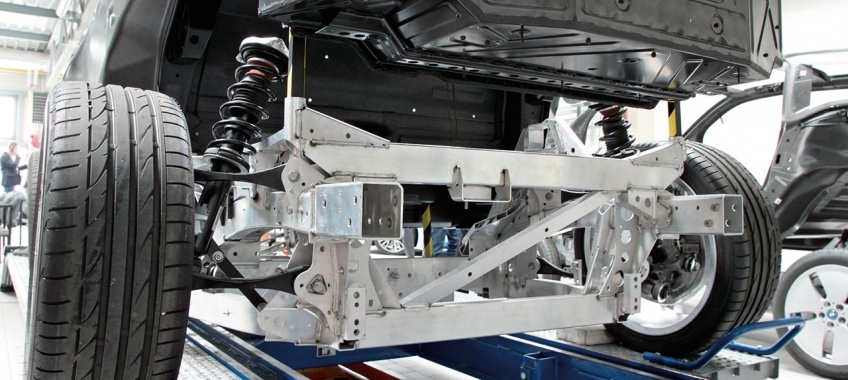
Rosnące wymagania użytkowników pojazdów dotyczące komfortu i bezpieczeństwa jazdy skłaniają producentów samochodów do opracowania nowych rozwiązań konstrukcyjnych zawieszenia i doskonalenia dotychczasowych. Dlatego też mechanik musi wiedzieć, jak działa zawieszenie i jak dokonać właściwej diagnozy, aby zapewnić bezpieczeństwo i komfort kierowcy oraz jego pasażerom.
Systemy zawieszenia zapewniają kontakt kół z powierzchnią jezdni w każdych warunkach (w czasie przyspieszania, hamowania i skrętu). Amortyzatory, łożyska i stabilizatory gwarantują elastyczne połączenie poszczególnych komponentów po obu stronach zawieszenia, dzięki czemu dobrze znosi ono wibracje samochodu wywołane przez nierówności na drodze (wyboje, dziury). Specjaliści często powtarzają: problemy z zawieszeniem poznasz po zużyciu bieżnika kół. Źle ustawiona zbieżność kół to częsty powód ściągania pojazdu, ale również przyspieszonego zużycia elementów zawieszenia i opon. Skutki złego ustawienia geometrii lub pomijania kontroli ciśnienia w oponach łatwo zauważyć po nierównomiernym zużyciu opony. Na szczęście korekta zbieżności kół, kątów pochylenia i wyprzedzenia osi sworznia zwrotnicy najczęściej eliminuje przyczynę problemów.
Gdy poniechać geometrii wszystkich kół, ryzykujemy podróż samochodem, którego parametry mogą znacznie odbiegać od norm producenta. Problemy przy ustawianiu geometrii zwieszenia to materiał na osobny artykuł. Tu nadmieńmy tylko, że producent pojazdu dopuszcza regulację wyłącznie na dedykowanych urządzeniach, do których dane regulacyjne są na bieżąco uaktualniane.
– Przykładem mogą być dane regulacyjne dla ostatnich modeli M-Power marki BMW, które są dostępne jak na razie dla autoryzowanych serwisów „M” – mówi Jerzy Pająk, Aftersales Project Manager BMW Group. – Od wielu lat spotyka się oryginalne felgi BMW z otworami umożliwiającymi montaż dedykowanych głowic pomiarowych, zapewniając tym samym dokładność pomiaru bez konieczności kompensacji bicia koła. Powtarzającymi się problemami przy ustawianiu geometrii jest kąt wyprzedzenia sworznia zwrotnicy – serwis radzi sobie np. wymieniając seryjną część na tzw. zwrotnicę korekcyjną +/-20’. W przypadku problemów z kątem pochylenia koła, po dokładnym sprawdzeniu nadwozia na ramie pomiarowej stosuje się tzw. wahacze korekcyjne. Ustawienie zbieżności osi tylnej to odrębne wyzwanie.
Przykładowo, przy skrętnej osi Integer 5 w serii 5 (F10) obowiązkiem jest wprowadzenie osi, a właściwie jej siłownika skrętu w stan serwisowy przy użyciu sprzętu diagnostycznego. Należy pamiętać, iż ta oś zmienia swoje nastawy w zależności od prędkości pojazdu. Inaczej mówiąc, potrafi ustawić koła współbieżnie do kół przednich lub przeciwbieżnie, aby zachować stabilność auta przy szybko pokonywanych zakrętach lub zacieśnić promień skrętu przy niższych prędkościach.
To oczywiście nie wszystko, co podnosi reżim prac warsztatowych. Począwszy od aut G11/G12, a więc nowej serii 7 BMW serwis musi się zmierzyć ze stabilizatorami elektromechanicznymi. Zresztą od wielu lat stosuje się aktywną regulację siły tłumienia amortyzatorów (EDC), nie tylko w modelach najwyższej klasy, coraz częściej spotykamy to rozwiązanie w tańszych autach np. seria 4, bliźniacza konstrukcyjnie z popularną serią 3.
Jeśli którykolwiek element zawieszenia jest w złym stanie, degraduje kolejny. Ignorowanie problemów z czasem zwiększa zakres wymaganych napraw oraz podnosi koszty serwisu.
W przypadku wymiany elementów zawieszenia należy pamiętać o stosowaniu nowych połączeń śrubowych. Pozornie błaha oszczędność może okazać się dla użytkownika tragiczna w skutkach. Skoro mowa o połączeniach śrubowych, warto przybliżyć awans rozwiązań, które mogą w niedługim czasie zrewolucjonizować podejście inżynierów w dziedzinie projektowania połączeń elementów składowych zawieszenia.
Połączenia śrubowe podwójnie zabezpieczone?
Jak wiadomo, większość tradycyjnych metod zabezpieczania połączeń gwintowych przed poluzowaniem i odkręcaniem wykorzystuje tarcie pomiędzy elementami. Sposób ten bywa nieskuteczny zwłaszcza w przypadku mocowań poddawanych drganiom. Niezależny niemiecki instytut Materialprüfungsamt Nordrhein-Westfalen (MPA NRW) przeprowadził niedawno test wibracyjny z podkładkami Twin-Lock według normy DIN 65151 (test Junkera) i wydał certyfikat zgodności z wymogami normy DIN 25201:2010. Próba wykazała, że Twin-Lock skutecznie zabezpieczają połączenia śrubowe: siła mocowania pozostaje niemal niezmienna po 2000 cykli i tylko minimalnie zmniejsza się na początku próby z powodu normalnego osiadania po dokręceniu.
Nowatorskie podkładki zapobiegają odkręcaniu się śrub i nakrętek poddawanych wibracjom i obciążeniom dynamicznym poprzez zwiększenie napięcia na śrubie. System Twin-Lock składa się z dwóch identycznych podkładek posiadających po wewnętrznej stronie nacięcia w kształcie klina; po zewnętrznej stronie ząbki nacięte promieniowo. Zasadę działania ilustruje rys 1. Kąt nachylenia (α) nacięć klinowych podkładki jest większy niż kąt nachylenia (β) gwintu śruby. Podczas dokręcania zewnętrzne radełkowane powierzchnie „chwytają” zarówno powierzchnię elementu złącznego, jak i materiał, w który wkręcana jest śruba. Zapobiega to przesuwaniu się zespołu podkładek względem zewnętrznych powierzchni. Dokręcanie powoduje również blokowanie się wewnętrznych stron podkładek na zasadzie klina. Poprzez różnicę kąta pomiędzy nacięciami klinowymi podkładek i kąta β gwintu śrub zwiększa się napięcie na śrubie, co uniemożliwia jej samoczynne odkręcenie.
„Podwójne zabezpieczenie” połączeń śrubowych jawi się interesująco. Powyższe rozwiązanie dopiero będzie przedmiotem analiz w firmach automotive.
– W pierwszym rzędzie podkładki Twin-Lock znalazły zastosowanie w taborze kolejowym, a teraz przyszedł czas, by także branża automotive skorzystała z elementów wstępnie sklejonych i gotowych do natychmiastowego użycia – podkreśla Iwona Halczuk, kierownik ds. klientów kluczowych w firmie Bollhoff Technika Łączenia. – Niewątpliwym ich walorem jest możliwość stosowania ze śrubami i nakrętkami niemal każdego typu i każdej klasy wytrzymałości (do 12.9) oraz brak konieczności okresowego dokręcania takich połączeń.
Ewolucja zawieszenia typu McPherson
Pierwotnie dominowały zawieszenia z podwójnymi wahaczami poprzecznymi i sprężynami śrubowymi. Wraz z rozwojem przemysłu motoryzacyjnego i zwiększeniem popytu konsumentów producenci zaczęli rozwijać tańsze i prostsze systemy. Tak powstało zawieszenie kolumnowe McPhersona. Wynalezione w Stanach Zjednoczonych w latach 50. XX wieku zawieszenie McPhersona jest obecnie najczęściej wykorzystywanym oryginalnym systemem zawieszenia w przemyśle motoryzacyjnym: stanowi ponad 80% rynku światowego i 90% rynku europejskiego.
Każdego roku sprzedaje się około 80 mln nowych samochodów wyposażonych w zawieszenie typu McPherson. Łożysko zawieszenia jest częścią zużywalną, związaną z wymianą amortyzatora. Z reguły wymienia się je dopiero przy co trzeciej wymianie amortyzatora, a pożądane jest, by wymieniać komplet łożysk przy każdej wymianie amortyzatorów. Jednak coraz więcej dilerów i warsztatów odmawia wymiany amortyzatora bez wymiany całego zespołu zawieszenia. Warto o tym pamiętać, bo oznacza to duże możliwości rozwoju dla niezależnego rynku automotive aftermarket – o czym zresztą mowa w najnowszej broszurze pt. „Zawieszenia”, anonsowanej przez firmę NTN-SNR. W odpowiedzi na potrzeby rynku światowy lider w produkcji łożysk tocznych rozszerzył gamę swoich produktów o łożyska, które spełniają coraz więcej funkcji (mocowanie sprężyny, łożysko mocowania amortyzatora) i które reagują w innowacyjny sposób na potrzeby producentów branży motoryzacyjnej. Mowa nie tylko o opakowaniu, które zajmuje mniej miejsca, ale o stale rosnącym poziomie komfortu posiadaczy pojazdów oraz zwiększonej przyczepność do nawierzchni drogi.
Dlaczego należy wymieniać łożysko zawieszenia i poduszkę? Uprzedzając pytania klientów warsztatu, przy wymianie kompletnego zestawu mocowania kolumny McPhersona, bez poświęcania dodatkowego czasu, kierowca dostaje gwarancję bezpieczeństwa i optymalnego komfortu. Wymieniając amortyzatory, korzystaj z możliwości wymiany wszystkich elementów zawieszenia! Taka procedura polepsza przyczepność i skraca drogę hamowania (zużyte zawieszenie to ok. +15% drogi hamowania).
Skądinąd ewolucję zawieszenia typu McPherson obrazuje doskonalenie łożyska mocowania amortyzatora (rys. 2). Obecnie na rynku funkcjonują dwie technologie przedniego zawieszenia: zawieszenie kolumnowe McPhersona oraz bardziej zaawansowane zawieszenie z podwójnym wahaczem poprzecznym i sprężyną śrubową. Druga z technologii zapewnia lepszy komfort, dynamikę i przyczepność. Koszty produkcji zawieszenia z podwójnym wahaczem poprzecznym i sprężyną śrubową są wyższe, dlatego też zawieszenie tego typu stosowane jest w modelach z wyższej półki (takich jak Mercedes klasy E i S, BMW seria 5 i 7, Audi A4 etc.) oraz w samochodach o wysokich osiągach czy też sportowej charakterystyce. Ten rodzaj konstrukcji nie wymaga łożyska zawieszenia, ale jest wyposażony w odbój amortyzatora, pomagający w wytłumieniu drgań.
Producenci stosują ten rodzaj zawieszenia zarówno na przedniej, jak i tylnej osi, początkowo w pojazdach klasy wyższej i średniej, a obecnie również kompaktowej.
Zawieszenie wielowahaczowe
Samochód wyposażony w zawieszenie wielowahaczowe pozwala kierowcy cieszyć się z doskonałego komfortu i znakomitych parametrów jezdnych.
– Jak widać, ten typ zawieszenia ma same zalety, jednak skomplikowanie i znacznie większa ilość elementów konstrukcyjnych w porównaniu chociażby do zawieszenia z kolumną McPhersona skutkuje większym prawdopodobieństwem wystąpienia usterek. Stąd zapewne bierze się wiele opinii o niskiej trwałości i wysokiej awaryjności zawieszeń wielowahaczowych – dowodzi Łukasz Cudek, kierownik działu kontroli jakości i wdrożeń w firmie Master Sport Automobiltechnik (MS). – Tymczasem na problem awaryjności i trwałości zawieszeń wielowahaczowych należy spojrzeć szerzej i rozpatrywać go w trzech głównych aspektach: jakości produktu oferowanego przez producenta zawieszenia; odpowiedniego montażu i serwisowania w warsztatach oraz wczesnej diagnozy usterek; świadomości użytkownika pojazdu dotyczącej wpływu sposobu eksploatacji pojazdu na trwałość poszczególnych części zawieszenia. Decydując się na zakup nowej części, zawsze musimy kierować się jakością, o którą potrafią zadbać jedynie renomowani producenci elementów zawieszenia. Jednym z nich jest firma Master Sport Automobiltechnik (MS), wyspecjalizowana w projektowaniu i produkcji zawieszeń ze stopów lekkich.
Z informacji uzyskanych w dziale wdrożeń i kontroli jakości wynika, że wysokiej jakości wahacz aluminiowy to element: dobrze zaprojektowany, kuty na precyzyjnych prasach, obrobiony w zautomatyzowanym cyklu z dokładnością do 0,001 mm. Niby szczegół, ale wahacz zaprasowany jest z wysoką precyzją i zwiększoną siłą (wymóg OE to min. 15 kN, podczas gdy standard w Master Sport to min. 20 kN), z gniazdem sworznia o podwyższonej wytrzymałości, z optymalną ilością smaru dla lepszej ochrony sworznia i z osłoną o zwiększonej wytrzymałości i mrozoodporności oraz sprężynką mocującą o zwiększonej odporności na korozję.
Potwierdzeniem wysokiej jakości wahaczy jest gwarancja udzielana przez producentów. Przykładowo Master Sport Automobiltechnik udziela gwarancji na 5 lat lub 80 tys. przebiegu przy montażu zgodnie z zaleceniami producenta pojazdu. Oczywiście demontaż i montaż elementów zawieszenia powinien być wykonywany za pomocą odpowiednich narzędzi.
– Do rozłączania połączeń stożkowych należy wykorzystywać ściągacze – wyjaśnia A. Kmiecik. – Użycie ciężkich młotów i łyżek może doprowadzić do uszkodzeń innych elementów. Przed przystąpieniem do montażu nowych wahaczy koniecznie należy oczyścić wszystkie powierzchnie – szczególnie na zwrotnicy, do których przylegają gumowe osłony sworzni. Bardzo ważne jest dokręcanie śrub mocujących wahacze wyłącznie wtedy, gdy zawieszenie jest obciążone masą pojazdu, a koła znajdują się w położeniu naturalnym. Dokręcając je na podniesionym pojeździe przy maksymalnie rozprężonym zawieszeniu, wprowadzamy dodatkowe naprężenia skręcające do elementów metalowo-gumowych. Powodują one często uszkodzenie nowego elementu już w czasie stawiania pojazdu na kołach oraz zawsze przyspieszone zużycie. Jest to najczęściej popełniany błąd podczas montażu zawieszeń wielowahaczowych, mający wpływ na ich późniejszą trwałość. Należy także zwrócić uwagę, aby w czasie montażu nie uszkodzić gumowych osłon przegubów kulistych, ponieważ nawet mikrouszkodzenia gumowych osłon skutkują ich szybkim zużyciem. Po dokonaniu naprawy należy bezwzględnie dokonać kontroli geometrii pojazdu.
Przekazując samochód po naprawie klientowi, powinno się wyjaśnić, jak wielki wpływ na dużo szybsze zużycie części zawieszenia ma niewłaściwa eksploatacja pojazdu.
Rafał Dobrowolski
Fot. R. Dobrowolski i materiały firm: Bollhoff, NTN-SNR
Komentarze (0)