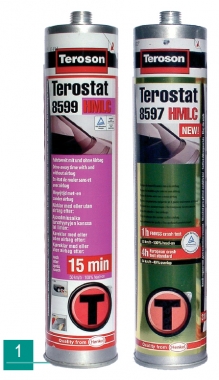
Szyby w nowoczesnych samochodach, poza szybami ruchomymi, mocowane są do nadwozia przy pomocy poliuretanowych mas klejąco-uszczelniających, potocznie zwanych klejami. Takie mocowanie ma bardzo istotny wpływ na bezpieczeństwo oraz na komfort jazdy samochodem. Zarówno kleje, jak i technologia wklejania szyb znane są, mniej lub więcej, w każdym warsztacie. Jednak spotykam się jeszcze w warsztatach z różnymi praktykami, które mają bardzo mało wspólnego z profesjonalnym wklejaniem szyb. Widocznie ci, których wcześniej uczyłem, nie przekazali wszystkiego młodszym kolegom, a ci zmodyfikowali i uprościli swoje czynności i stąd różne odmiany technologiczne. Dlatego chciałbym dla przypomnienia omówić rodzaje klejów i ich znaczenie w połączeniu szyby z nadwoziem.
W technologii wklejania szyb możemy spotkać się z jednym z trzech systemów – dwupodkładowym, jednopodkładowym i bezpodkładowym. W każdym z systemów mamy do dyspozycji różne rodzaje klejów: standardowe (2-4-godzinne); szybkie (1-2-godzinne); superszybkie – nakładane na gorąco (15-minutowe) i kleje dwuskładnikowe. Wszystkie te kleje dla nowoczesnych samochodów powinny być wykonane w formule HMLC (fot. 1).
HMLC – to znaczy High Modulus i Low Conductivity, czyli wysoki moduł sprężystości i mała przewodność elektryczna.
Oznacza to, że konstruktorzy nowoczesnych samochodów wymagają od sposobu montowania szyb do nadwozia spełnienia wielu nowych parametrów. Są to:
- zwiększenie sztywności nadwozia, a szczególnie kabiny pasażerskiej, na działanie momentów skręcających;
- niepowodowanie korozji punktowej nadwozia pod warstwą kleju;
- niezakłócanie odbioru fal radiowych.
Wysoki moduł sprężystości kleju
Zwiększenie sztywności nadwozia i zredukowanie poziomu hałasu pochodzącego z nadwozia prowadzi do zwiększenia stopnia komfortu podróżowania. Nadwozia nowoczesnych samochodów wykonywane są coraz częściej z lekkich i bardzo wytrzymałych materiałów, łączonych ze sobą także technologię klejenia, spawania laserowego oraz nitowania sztancowego, dlatego też podatne są bardziej na działanie momentów skręcających. Stosowanie do wklejania szyb w takich samochodach klejów standardowych prowadzi do nadmiernego deformowania się nadwozia podczas jazdy i pękania szyb bez żadnej mechanicznej przyczyny.
Dlatego też od klejów do szyb wymaga się wysokiego modułu sprężystości (minimum 3 MPa). Gwarantuje on zwiększenie sztywności nadwozia na skręcanie i aktywne przyczynienie się do podwyższenia bezpieczeństwa (fot. 2).
Niska przewodność, czyli duża oporność elektryczna
Niska przewodność kleju daje stałą ochronę nadwozia przed powstawaniem korozji punktowej pod warstwą kleju, szczególnie w samochodach z nadwoziem aluminiowym. Dotyczy to samochodów z szybami ogrzewanymi, zarówno tylnymi, jak i przednimi. Czasy nadwozi wyłącznie stalowych mamy już za sobą. Przy produkcji nadwozi samochodowych stosuje się coraz więcej aluminium, magnezu i różnych tworzyw sztucznych. Materiały te, jak wiemy, umożliwiają wprowadzanie nowych koncepcji produkcji, zmniejszanie ciężaru i dają nowe możliwości projektantom nadwozi. Jeżeli w samochodzie stosowane są różne metale, to istnieje niebezpieczeństwo korozji kontaktowej, gdy tylko te metale zostaną połączone ze sobą za pośrednictwem materiału przewodzącego prąd. Taki przypadek występuje często przy wklejaniu szyb samochodowych. Srebrne druty oporowe ogrzewania szyby łączone są ze sobą za pomocą szerokich listew drukowanych na bocznych obrzeżach szyby. Nałożony na takie listwy klej przewodzący prąd może powodować korozję kontaktową nadwozia, szczególnie wykonanego z aluminium (fot. 3). Wygląda to tak, że mamy dwa metale połączone ze sobą materiałem przewodzącym prąd stały. Wokół takiego połączenia występuje wilgoć, w której rozpuszczają się związki chemiczne zawarte w powietrzu, czyli elektrolit. W takich warunkach następuje „zjadanie” jednego metalu przez drugi. Tym słabszym metalem jest zawsze aluminium lub stal. Dlatego w obszarze powierzchni oporowej dla szyby niezbędny jest klej nieprzewodzący prądu. Wymagania przemysłu samochodowego wyznaczają oporność kleju na wartość nie mniejszą niż 108 cm.
Optymalna charakterystyka wysokich częstotliwości
Podczas wklejania szyby do samochodu może zachodzić przypadek zamierzonego lub przypadkowego kontaktu kleju z anteną (srebrny nadruk listwy zbiorczej). Przy takim kontakcie bardzo ważnym parametrem kleju jest impedancja, która jest miarą zachowania się przewodnika elektrycznego pod wpływem działania prądu zmiennego. Prąd ten powstaje od fal radiowych różnej częstotliwości odbieranych przez anteny zamontowane w szybie samochodu. Przy niskiej impedancji kleju prąd zmienny z anteny może trafiać zamiast do odbiornika na nadwozie. Zmniejsza się zatem napięcie sygnału radiowego, co oznacza, że odbiór staje się coraz gorszy. Niejednokrotnie impedancja jest mylona z niską przewodnością. Niektórzy uważają, że wystarczy, aby klej miał niską przewodność, aby był odpowiedni do wklejania szyb z zamontowanymi antenami. Jednak to nie wystarcza. Oporność wpływa bowiem w pierwszym rzędzie na sygnały stałoprądowe, podczas gdy impedancja oddziałuje, w zależności od częstotliwości, na sygnały zmiennoprądowe. Zatem wielkości te mają ze sobą niewiele wspólnego. Klej może, ale nie musi, mieć zarówno niską przewodność, jak i małe wartości impedancji. Jest to wytłumaczenie, dlaczego szyba wklejona takim klejem mimo dużej oporności może utrudniać odbiór radiowy (fot. 4). Stwierdzenie, z jakim klejem mamy do czynienia, też nie jest proste, ponieważ pomiary impedancji są skomplikowane i wymagają drogiej aparatury. Impedancja składa się z trzech części: opornościowej, indukcyjnej oraz pojemnościowej i trzeba każdorazowo dla każdej częstotliwości wyznaczać trzy wielkości.
Materiał klejów
Tworzywem, z którego produkowane są kleje do szyb, jest poliuretan – PUR. Tylko na rynki skandynawskie oferowane są kleje na bazie modyfikowanych silanów – SMP, ponieważ w tych krajach zabronione są produkty zawierające izocyjaniany, czyli masy poliuretanowe – PUR. Jednoskładnikowe masy poliuretanowe utwardzają się pod wpływem wilgoci zawartej w powietrzu. Drugim czynnikiem decydującym o ich utwardzaniu się jest temperatura. Warunki normalne, dla których określane są właściwości wszystkich mas poliuretanowych, to temperatura 20°C i wilgotność względna powietrza 50% (fot. 5). W takich warunkach szybkość utwardzania się masy wynosi około 4 mm/24 godz. Dlatego też dla całkowitego utwardzenia się kleju po wklejeniu szyby samochód musiałby pozostawać w warsztacie przez co najmniej 24 godziny. W praktyce oznacza to, że całkowite, wskrośne utwardzenie się kleju następuje dopiero po 3-5 dniach. Jest to za długi czas przeznaczony na wymianę szyby w samochodzie. Dlatego też wprowadzony został inny parametr określający właściwości i jakość kleju. Jest nim czas gotowości samochodu do wyjazdu z warsztatu po wklejeniu szyby. Czas ten określany jest po przeprowadzeniu odpowiednich badań w warunkach normalnych i potwierdzony certyfikatami. Taka informacja powinna być wydrukowana na każdej tubie z klejem. Czas dopuszczenia pojazdu do ruchu określa się na podstawie testów zderzeniowych po wklejeniu szyby wg normy amerykańskiej FMVSS 208/212 (Federal Motor Vehicle Safety Standards), przy pokryciu 100% i przy prędkości 50 km/godz. W Europie obwiązuje już bardziej rygorystyczna norma Euro NCAP (European New Car Assessment Programme), przy pokryciu 40% i prędkości 64 km/godz. (fot. 6a i 6b). Ale tę normę spełniają jedynie kleje dwuskładnikowe (np. Terostat 8630 2K HMLC) – fot. 7. To znaczy, że już po 2 godzinach od wklejenia szyby pojazd może być dopuszczony do ruchu (5 godzin dla autobusów). Kleje jednoskładnikowe również spełniają tę normę, ale dopiero po ich całkowitym utwardzeniu się, czyli po co najmniej 5 dniach.
Kleje bezpodkładowe
Drugim, bardzo ważnym składnikiem wpływającym na wytrzymałość połączenia szyby z nadwoziem jest podkład i aktywator. Taki wymóg stawiany jest klejom poliuretanowym, ponieważ masy poliuretanowe wymagają ochrony przed działaniem promieni ultrafioletowych.
Do niedawna stosowane były dwa podkłady: podkład na nadwozie i podkład na szybę. Po wprowadzeniu szyb powlekanych doszedł jeszcze jeden podkład, który aktywował warstwę kleju na szybach powlekanych. Powodowało to wiele błędów i nieporozumień w zakresie stosowania tych preparatów. Dlatego producenci klejów do szyb od dawna już pracowali nad klejami, które nie będą wymagały stosowania czarnego podkładu. Pierwszą próbą było zastosowanie podkładu przezroczystego przez firmę Makra. Był to jednak w dalszym ciągu klej poliuretanowy, a stosowanie podkładu przezroczystego do szyb nasłonecznionych nie zawsze się sprawdzało. Następnym krokiem było opracowanie klejów do szyb na bazie MS polimerów przez firmę Kent. Klej ten nie spełniał jednak wymogów stawianych nowym klejom do wklejania szyb: dużej oporności, wysokiego modułu sprężystości i dużej impedancji. Poza tym nie były to kleje kompatybilne z klejami poliuretanowymi.
Dopiero od niedawna firma Teroson wprowadziła do stosowania kleje poliuretanowe, które nie wymagają stosowania żadnego podkładu i spełniają wszystkie parametry nowoczesnych klejów do szyb. Są to zatem również kleje HMLC – np. Terostat 8597 PL HMLC (PL oznacza w tym przypadku – Primer Lose). Zastosowanie klejów bezpodkładowych ułatwia proces wklejania szyb i czyni go bezpieczniejszym. Nie ma bowiem obawy, że podkład został nałożony za grubo, za cienko, na warstwę starego kleju czy czas na odparowanie był za krótki lub za długi. Wspomniane wcześniej kleje silanowe (SMP) to też kleje bezpodkładowe (np. Terostat 9000 PL HMLC), które mogą być stosowane przy wymianie szyb wklejanych wcześniej na kleje poliuretanowe. Wymagania dotyczące jakości szyb samochodowych oraz klejów wciąż rosną wraz z tendencją do projektowania lekkich konstrukcji przy zastosowaniu cieńszych szyb, aluminium i nowych rodzajów stali. Dotyczy to nie tylko oryginalnego łączenia szyb z nadwoziem w zakładach produkcyjnych, lecz także w warsztatach naprawczych. Jak wykazują tzw. crash testy znanych firm samochodowych, zachowanie właściwych parametrów wytrzymałościowych połączenia szyby z karoserią znacznie podnosi bezpieczeństwo bierne kierowcy i pasażerów (fot. 8).
Jeżeli szyba jest uszkodzona, powinna być natychmiast wymieniona, aby przywrócić pojazdowi jego nienaruszony stan. Do montażu powinny być stosowane tylko szyby, które dopuszczone są i zalecane przez producenta samochodów. Szyby jako element konstrukcyjny nadwozia oraz rodzaj kleju, jakim zostały wklejone, zostały dokładnie dobrane do sztywności całego nadwozia. Każda zmiana tych parametrów może wpływać bardzo znacząco na brak zachowania sztywności nadwozia podczas wypadku. Stosowanie dowolnych szyb i klejów może powodować także niespodziewane i samoistne pękanie szyb.
Wiesław Wielgołaski
W technologii wklejania szyb możemy spotkać się z jednym z trzech systemów – dwupodkładowym, jednopodkładowym i bezpodkładowym. W każdym z systemów mamy do dyspozycji różne rodzaje klejów: standardowe (2-4-godzinne); szybkie (1-2-godzinne); superszybkie – nakładane na gorąco (15-minutowe) i kleje dwuskładnikowe. Wszystkie te kleje dla nowoczesnych samochodów powinny być wykonane w formule HMLC (fot. 1).
HMLC – to znaczy High Modulus i Low Conductivity, czyli wysoki moduł sprężystości i mała przewodność elektryczna.
Oznacza to, że konstruktorzy nowoczesnych samochodów wymagają od sposobu montowania szyb do nadwozia spełnienia wielu nowych parametrów. Są to:
- zwiększenie sztywności nadwozia, a szczególnie kabiny pasażerskiej, na działanie momentów skręcających;
- niepowodowanie korozji punktowej nadwozia pod warstwą kleju;
- niezakłócanie odbioru fal radiowych.
Wysoki moduł sprężystości kleju
Zwiększenie sztywności nadwozia i zredukowanie poziomu hałasu pochodzącego z nadwozia prowadzi do zwiększenia stopnia komfortu podróżowania. Nadwozia nowoczesnych samochodów wykonywane są coraz częściej z lekkich i bardzo wytrzymałych materiałów, łączonych ze sobą także technologię klejenia, spawania laserowego oraz nitowania sztancowego, dlatego też podatne są bardziej na działanie momentów skręcających. Stosowanie do wklejania szyb w takich samochodach klejów standardowych prowadzi do nadmiernego deformowania się nadwozia podczas jazdy i pękania szyb bez żadnej mechanicznej przyczyny.
Dlatego też od klejów do szyb wymaga się wysokiego modułu sprężystości (minimum 3 MPa). Gwarantuje on zwiększenie sztywności nadwozia na skręcanie i aktywne przyczynienie się do podwyższenia bezpieczeństwa (fot. 2).
Niska przewodność, czyli duża oporność elektryczna
Niska przewodność kleju daje stałą ochronę nadwozia przed powstawaniem korozji punktowej pod warstwą kleju, szczególnie w samochodach z nadwoziem aluminiowym. Dotyczy to samochodów z szybami ogrzewanymi, zarówno tylnymi, jak i przednimi. Czasy nadwozi wyłącznie stalowych mamy już za sobą. Przy produkcji nadwozi samochodowych stosuje się coraz więcej aluminium, magnezu i różnych tworzyw sztucznych. Materiały te, jak wiemy, umożliwiają wprowadzanie nowych koncepcji produkcji, zmniejszanie ciężaru i dają nowe możliwości projektantom nadwozi. Jeżeli w samochodzie stosowane są różne metale, to istnieje niebezpieczeństwo korozji kontaktowej, gdy tylko te metale zostaną połączone ze sobą za pośrednictwem materiału przewodzącego prąd. Taki przypadek występuje często przy wklejaniu szyb samochodowych. Srebrne druty oporowe ogrzewania szyby łączone są ze sobą za pomocą szerokich listew drukowanych na bocznych obrzeżach szyby. Nałożony na takie listwy klej przewodzący prąd może powodować korozję kontaktową nadwozia, szczególnie wykonanego z aluminium (fot. 3). Wygląda to tak, że mamy dwa metale połączone ze sobą materiałem przewodzącym prąd stały. Wokół takiego połączenia występuje wilgoć, w której rozpuszczają się związki chemiczne zawarte w powietrzu, czyli elektrolit. W takich warunkach następuje „zjadanie” jednego metalu przez drugi. Tym słabszym metalem jest zawsze aluminium lub stal. Dlatego w obszarze powierzchni oporowej dla szyby niezbędny jest klej nieprzewodzący prądu. Wymagania przemysłu samochodowego wyznaczają oporność kleju na wartość nie mniejszą niż 108 cm.
Optymalna charakterystyka wysokich częstotliwości
Podczas wklejania szyby do samochodu może zachodzić przypadek zamierzonego lub przypadkowego kontaktu kleju z anteną (srebrny nadruk listwy zbiorczej). Przy takim kontakcie bardzo ważnym parametrem kleju jest impedancja, która jest miarą zachowania się przewodnika elektrycznego pod wpływem działania prądu zmiennego. Prąd ten powstaje od fal radiowych różnej częstotliwości odbieranych przez anteny zamontowane w szybie samochodu. Przy niskiej impedancji kleju prąd zmienny z anteny może trafiać zamiast do odbiornika na nadwozie. Zmniejsza się zatem napięcie sygnału radiowego, co oznacza, że odbiór staje się coraz gorszy. Niejednokrotnie impedancja jest mylona z niską przewodnością. Niektórzy uważają, że wystarczy, aby klej miał niską przewodność, aby był odpowiedni do wklejania szyb z zamontowanymi antenami. Jednak to nie wystarcza. Oporność wpływa bowiem w pierwszym rzędzie na sygnały stałoprądowe, podczas gdy impedancja oddziałuje, w zależności od częstotliwości, na sygnały zmiennoprądowe. Zatem wielkości te mają ze sobą niewiele wspólnego. Klej może, ale nie musi, mieć zarówno niską przewodność, jak i małe wartości impedancji. Jest to wytłumaczenie, dlaczego szyba wklejona takim klejem mimo dużej oporności może utrudniać odbiór radiowy (fot. 4). Stwierdzenie, z jakim klejem mamy do czynienia, też nie jest proste, ponieważ pomiary impedancji są skomplikowane i wymagają drogiej aparatury. Impedancja składa się z trzech części: opornościowej, indukcyjnej oraz pojemnościowej i trzeba każdorazowo dla każdej częstotliwości wyznaczać trzy wielkości.
Materiał klejów
Tworzywem, z którego produkowane są kleje do szyb, jest poliuretan – PUR. Tylko na rynki skandynawskie oferowane są kleje na bazie modyfikowanych silanów – SMP, ponieważ w tych krajach zabronione są produkty zawierające izocyjaniany, czyli masy poliuretanowe – PUR. Jednoskładnikowe masy poliuretanowe utwardzają się pod wpływem wilgoci zawartej w powietrzu. Drugim czynnikiem decydującym o ich utwardzaniu się jest temperatura. Warunki normalne, dla których określane są właściwości wszystkich mas poliuretanowych, to temperatura 20°C i wilgotność względna powietrza 50% (fot. 5). W takich warunkach szybkość utwardzania się masy wynosi około 4 mm/24 godz. Dlatego też dla całkowitego utwardzenia się kleju po wklejeniu szyby samochód musiałby pozostawać w warsztacie przez co najmniej 24 godziny. W praktyce oznacza to, że całkowite, wskrośne utwardzenie się kleju następuje dopiero po 3-5 dniach. Jest to za długi czas przeznaczony na wymianę szyby w samochodzie. Dlatego też wprowadzony został inny parametr określający właściwości i jakość kleju. Jest nim czas gotowości samochodu do wyjazdu z warsztatu po wklejeniu szyby. Czas ten określany jest po przeprowadzeniu odpowiednich badań w warunkach normalnych i potwierdzony certyfikatami. Taka informacja powinna być wydrukowana na każdej tubie z klejem. Czas dopuszczenia pojazdu do ruchu określa się na podstawie testów zderzeniowych po wklejeniu szyby wg normy amerykańskiej FMVSS 208/212 (Federal Motor Vehicle Safety Standards), przy pokryciu 100% i przy prędkości 50 km/godz. W Europie obwiązuje już bardziej rygorystyczna norma Euro NCAP (European New Car Assessment Programme), przy pokryciu 40% i prędkości 64 km/godz. (fot. 6a i 6b). Ale tę normę spełniają jedynie kleje dwuskładnikowe (np. Terostat 8630 2K HMLC) – fot. 7. To znaczy, że już po 2 godzinach od wklejenia szyby pojazd może być dopuszczony do ruchu (5 godzin dla autobusów). Kleje jednoskładnikowe również spełniają tę normę, ale dopiero po ich całkowitym utwardzeniu się, czyli po co najmniej 5 dniach.
Kleje bezpodkładowe
Drugim, bardzo ważnym składnikiem wpływającym na wytrzymałość połączenia szyby z nadwoziem jest podkład i aktywator. Taki wymóg stawiany jest klejom poliuretanowym, ponieważ masy poliuretanowe wymagają ochrony przed działaniem promieni ultrafioletowych.
Do niedawna stosowane były dwa podkłady: podkład na nadwozie i podkład na szybę. Po wprowadzeniu szyb powlekanych doszedł jeszcze jeden podkład, który aktywował warstwę kleju na szybach powlekanych. Powodowało to wiele błędów i nieporozumień w zakresie stosowania tych preparatów. Dlatego producenci klejów do szyb od dawna już pracowali nad klejami, które nie będą wymagały stosowania czarnego podkładu. Pierwszą próbą było zastosowanie podkładu przezroczystego przez firmę Makra. Był to jednak w dalszym ciągu klej poliuretanowy, a stosowanie podkładu przezroczystego do szyb nasłonecznionych nie zawsze się sprawdzało. Następnym krokiem było opracowanie klejów do szyb na bazie MS polimerów przez firmę Kent. Klej ten nie spełniał jednak wymogów stawianych nowym klejom do wklejania szyb: dużej oporności, wysokiego modułu sprężystości i dużej impedancji. Poza tym nie były to kleje kompatybilne z klejami poliuretanowymi.
Dopiero od niedawna firma Teroson wprowadziła do stosowania kleje poliuretanowe, które nie wymagają stosowania żadnego podkładu i spełniają wszystkie parametry nowoczesnych klejów do szyb. Są to zatem również kleje HMLC – np. Terostat 8597 PL HMLC (PL oznacza w tym przypadku – Primer Lose). Zastosowanie klejów bezpodkładowych ułatwia proces wklejania szyb i czyni go bezpieczniejszym. Nie ma bowiem obawy, że podkład został nałożony za grubo, za cienko, na warstwę starego kleju czy czas na odparowanie był za krótki lub za długi. Wspomniane wcześniej kleje silanowe (SMP) to też kleje bezpodkładowe (np. Terostat 9000 PL HMLC), które mogą być stosowane przy wymianie szyb wklejanych wcześniej na kleje poliuretanowe. Wymagania dotyczące jakości szyb samochodowych oraz klejów wciąż rosną wraz z tendencją do projektowania lekkich konstrukcji przy zastosowaniu cieńszych szyb, aluminium i nowych rodzajów stali. Dotyczy to nie tylko oryginalnego łączenia szyb z nadwoziem w zakładach produkcyjnych, lecz także w warsztatach naprawczych. Jak wykazują tzw. crash testy znanych firm samochodowych, zachowanie właściwych parametrów wytrzymałościowych połączenia szyby z karoserią znacznie podnosi bezpieczeństwo bierne kierowcy i pasażerów (fot. 8).
Jeżeli szyba jest uszkodzona, powinna być natychmiast wymieniona, aby przywrócić pojazdowi jego nienaruszony stan. Do montażu powinny być stosowane tylko szyby, które dopuszczone są i zalecane przez producenta samochodów. Szyby jako element konstrukcyjny nadwozia oraz rodzaj kleju, jakim zostały wklejone, zostały dokładnie dobrane do sztywności całego nadwozia. Każda zmiana tych parametrów może wpływać bardzo znacząco na brak zachowania sztywności nadwozia podczas wypadku. Stosowanie dowolnych szyb i klejów może powodować także niespodziewane i samoistne pękanie szyb.
Wiesław Wielgołaski
Komentarze (0)