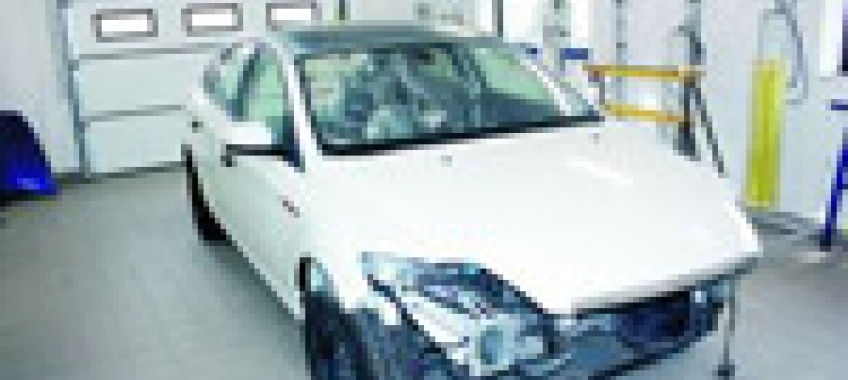
Forda Mondeo IV generacji
Ford Mondeo Mk III, produkowany w latach 2000-2007, miał typową dla seryjnie produkowanych pojazdów koncepcję łączenia poszycia dachu do wzmocnień konstrukcyjnych słupków dachowych. Produkowana obecnie generacja modelu ma już zupełnie inną konstrukcję dachu. Taka, a nie inna wizja biura projektowego Forda wymusza na serwisach swoiste metody naprawcze.
W 2005 roku biuro projektowe Forda zdecydowało się na zastosowanie nowych technologii służących łączeniu elementów składowych dachu w przygotowywanym do produkcji seryjnej najnowszym wcieleniu Mondeo o kryptonimie CD345. Samochód otrzymał płaską linię dachu, przywodzącą na myśl eleganckie konstrukcje dużo bardziej luksusowych pojazdów. Zrezygnowano tym samym z tradycyjnych dla popularnych modeli pojazdów przetłoczeń, które zwykle maskuje się elastycznymi listwami, jeśli nie mocujemy tam stóp bazowych bagażnika dachowego (fot. 1).
Fot. 1. Różnice w budowie dachu Forda Mondeo III i IV generacji.
Zamysły designerów Forda wprowadziły dużo bardziej istotne zmiany w technologii produkcji, łączenia dachu i wreszcie wymiany poszycia na nowy w przypadku uszkodzenia fabrycznych elementów. W sieci dealerskiej koncernu znajdziemy płaski element poszycia dachu i jak się okazuje, co miesiąc w autoryzowanych serwisach europejskich wymienia się łącznie nawet 30 takich elementów i liczba takich zleceń wcale nie maleje (fot. 2).
Fot. 2. Nowe poszycie dachu.
Ponieważ proces naprawczy jest dużo bardziej skomplikowany i rodzić może wiele wątpliwości, ośrodek szkoleniowy znajdujący się w Calw (w pobliżu Stuttgartu) opracował w połowie 2008 roku dokument pod nazwą: Strategie naprawcze poszycia dachu Forda Mondeo IV generacji.
Lut miękki w warunkach warsztatowych
Najważniejszą zmianą technologiczną jest sam proces łączenia dachu.
- W poprzedniej generacji Mondeo zgrzewanie jest oporowe – wyjaśnia Mariusz Bogacki, odpowiedzialny za szkolenia blacharskie w firmie CTS Caroliner. - W najnowszym modelu, w warunkach fabrycznych zgrzewanie dachu odbywa się techniką laserową, zaś szczeliny (szwy) między dachem a konstrukcją nośną wypełniane są lutem twardym. Dach nie opiera się też na wzmocnieniu w postaci przetłoczeń, w których umieszczane bywają stopy mocowania bagażnika dachowego. W warunkach warsztatowych zaleca się łączenie płaszczyzny dachu z konstrukcją nośną lutem miękkim (alternatywną metodą mocowania nowego poszycia w miejsce starego jest klejenie blach). Proces technologiczny polega kolejno na: zdjęciu starego (zniszczonego) dachu, przygotowaniu nowego, dopasowaniu płaszczyzny (przy użyciu ściągaczy – fot. 3), założeniu mas z myślą o cynowaniu krawędzi łączonych elementów (pasta pod podkład cynowy – fot. 4), lutowaniu i wreszcie oczyszczeniu powierzchni przed lakierowaniem.
Fot. 3. Do pasowania dachu używamy ściągaczy.
Fot. 4. Nakładanie pasty pod podkład cynowy.
W sprzedaży dostępne są oczywiście tylko dachy w autoryzowanych serwisach, dostarczane tylko od producenta pojazdu. W przypadku pojazdów 5-drzwiowych długość dachu wynosi 1515 mm (5-D) i 2200 mm dla odmiany kombi (WGN).
W przypadku nowej generacji Mondeo sam proces wymiany dachu na nowy jest zdecydowanie trudniejszy i pracochłonniejszy.
- Mamy do czynienia z większą ilością operacji i łatwiej o pomyłki – zauważa M. Bogacki. - Nieautoryzowany serwis, który nie zna tej technologii, nie podoła zleceniu. Rzemieślnicy oczywiście pokuszą się w takim wypadku o wycięcie dachu w okolicach słupków i wykonanie przysłowiowej “przekładki”. Oczywiście taka technologia nie będzie właściwa, bo blachy budujące słupki dachowe bardzo trudno spawać bez utraty sztywności i ryzyka wystąpienia naprężeń.
Narzędzia dedykowane przy wymianie dachu
Centrum serwisowe Forda przygotowało z myślą o wymianie poszyć dachowych Mondeo specjalnej konstrukcji ściągacze. Ich użycie bywa nieodzowne i wynika z przyjętych tolerancji fabrycznych producenta – każdy dach może się minimalnie różnić wymiarami, więc proces wpasowania płaszczyzny blachy w miejsce tej wyciętej ma decydujące znaczenie na efekt końcowy (minimalizacja naprężeń). Powszechnie też blacharze używają korkowych podkładek, by ustawić i ustabilizować płaszczyznę dachu na spodziewanej wysokości wzmocnień dachu (fot. 5). Żeby całość była idealnie spasowana, wykorzystuje się jeszcze taśmy magnetyczne, które przykłada się na obu krawędziach dachu (fot. 6). Te mają grubość 3 mm, więc gdy tylko zlicują się z progami mocowania dachu mamy pewność, że proces pasowania przebiegł należycie i dach na każdym odcinku nie będzie ani “utopiony” (powyżej 3 mm od progu), ani wyniesiony (poniżej 3 mm od progu).
Fot 5. Korkowe podkładki ustawiają i stabilizują poszycie dachu na spodziewanej wysokości.
Fot 6. 3-milimetrowej grubości taśmy magnetyczne przykładamy z myślą o kontroli prawidłowego pasowania.
Tak zamocowany i unieruchomiony korkowymi podkładkami dach gotowy jest do lutowania (fot. 7). Wystarczy wtedy ściągnąć magnetyczne taśmy i “chwycić” dach w kilku miejscach, a potem całość wypełnić lutem miękkim (tzw. stopem srebra). Na samym końcu czeka nas jeszcze obróbka mechaniczna miejsc łączenia. Nadmiar lutu ściągamy specjalnej konstrukcji skrobakiem (fot. 8).
Fot 7. Proces poprzedzający lutowanie dachu.
Fot 8. Nadmiar lutu ściągamy skrobakiem.
Ograniczenia i metody alternatywne
W warunkach warsztatowych nie jesteśmy więc w stanie w 100 procentach odtworzyć technologii fabrycznej. Zastępujemy lut twardy miękkim, bo taka technologia wynika z mniejszej aplikacji ciepła (nagrzewamy blachy maksymalnie do 300 stopni C); inaczej – przy wykorzystaniu technologii MIG aplikacja ciepła byłaby niebezpieczna dla poszycia. Użycie lutu twardego wiąże się z ryzykiem deformacji dachu i dlatego jest to zabronione. Na wstępie wspomnieliśmy o metodach alternatywnych łączenia nowego dachu w miejscu starego. Jedną z nich jest klejenie. Ograniczeniem stosowania tej technologii jest mniejsza sztywność i pewność połączeń (szwu) i brak zapewnienia odpowiedniej szczelności poszycia dachowego.
Fot 9: Dach przygotowany do lakierowania.
Opracowano na podstawie specjalnego wykładu przeprowadzonego dla redakcji “Nowoczesnego Warsztatu” w firmie CTS Caroliner.
Notował: Rafał Dobrowolski
Zdjęcia: Producent i CTS
Komentarze (0)