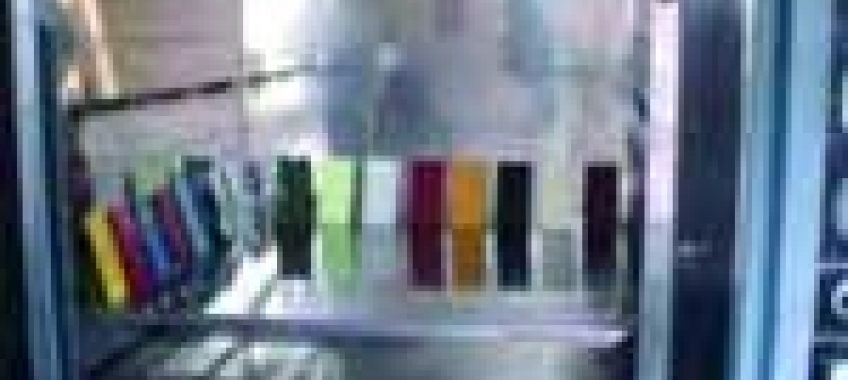
powłok lakierniczych w komorze klimatycznej – Odporność na wilgoć
Jednym z czynników zewnętrznych, na których działanie narażone są powłoki eksploatowane na zewnątrz, jest wilgoć. Czynnik ten jest szczególnie istotny właśnie w przypadku powłok samochodowych, które eksploatowane są w warunkach zewnętrznych.
W celu przeprowadzenia testu na odporność na działanie wilgoci danej powłoki samochodowej można wyeksponować ją w warunkach zewnętrznych lub przeprowadzić testy przyspieszone w komorach. Pierwsza metoda wydaje się być tańsza, jej przeprowadzenie wymaga jednak czasu przynajmniej kilku lat. W rzeczywistości tego typu testów nie przeprowadza się (za wyjątkiem niektórych powłok wodorozcieńczalnych).
Fot. 1. Umieszczenie próbek w komorze do testu odporności na wilgotność. (Źródło: www.corrosiondoctors.com)
Rodzaje uszkodzeń spowodowanych ekspozycją w środowisku o dużej wilgotności:
- chemiczne i elektrochemiczne uszkodzenie powłoki lakierniczej,
- utlenianie metalu pod powłoką na skutek korozji galwanicznej,
- zmiany lepkości powłoki,
- puchnięcie powłoki na skutek efektów sorpcji,
- degradacja właściwości izolacyjnych,
- zmiana plastyczności powłoki,
- optyczna zmiana powłoki – względy estetyczne.
Fot. 2. Umieszczenie próbek w komorze do testu odporności na wilgotność przy jednoczesnym badaniu wpływu temperatury. (Źródło: www.corrosiondoctors.com)
Testy przyspieszone w komorach
Testy przyspieszone przeprowadza się w zamkniętych komorach umożliwiających kontrolę warunków ekspozycji. Parametry testu dobiera się w taki sposób, aby warunki jak najdokładniej symulowały warunki rzeczywistej eksploatacji powłoki z uwzględnieniem mechanizmów korozji. W celu zapewnienia możliwości odniesienia otrzymanych wyników testu przyspieszonego do prawdopodobnych wyników eksploatacji w warunkach rzeczywistych, konieczne jest przyjęcie odpowiedniego współczynnika korelacji.
Testy kontrolowane
Istnieje kilka typów testów odporności na wilgoć:
- testy badające odporność na wilgotność,
- testy badające odporność na wilgotność przy jednoczesnym badaniu wpływu temperatury,
- testy badające odporność na zanurzenie powłoki w cieczy.
Fot.3. Test zanurzeniowy na odporność powłoki na wilgoć. (Źródło: www.corrosiondoctors.com)
Testy te pozwalają stwierdzić jak dana powłoka znosi eksploatację w atmosferze dużej wilgotności i braku czynników korozyjnych. Wszystkie te metody wykorzystują dużą wilgotność i dodatkowo mogą wykorzystywać zmiany temperatury.
Testy badające odporność na wilgotność
Opis metody
Próbki montuje się ponad zbiornikiem z ogrzewaną wodą. Wysokość ponad poziomem wody w zbiorniku powinna być taka, aby na powierzchni badanych próbek osiadała para wodna. Stosuje się trzy metody:
- Testy badające odporność na wilgoć (patrz tabela 1).
- Metoda BS 3900-F2 zaleca testowanie w najostrzejszych warunkach i jest ona najczęściej stosowana. Test zwykle przeprowadza się przez okres 500 godzin. Jeśli po tym czasie powłoka nie wykazuje zmian, można ją uznać za odporną na działanie wilgoci.
- Umieszczenie próbek w komorze do testu odporności na wilgotność (patrz fot. 1).
Testy badające odporność na wilgotność przy jednoczesnym badaniu wpływu temperatury
Opis metody
Test ten stosuje się, aby określić jak dana powłoka zachowuje się w warunkach dużej wilgotności połączonej z szerokim zakresem zmian temperatury. Test przeprowadza się w specjalnej komorze klimatycznej, która składa się z:
- komory zamontowanej ponad instalacją ogrzewającą powietrze,
- wymiennika ciepła (chłodzenie wodą),
- atomizera wody,
- układu zapewniającego zamknięty obieg powietrza,
- czujnika temperatury,
- czujnika wilgotności.
Tabela 1. Testy badające odporność na wilgoć. Normalizacja. (Źródło: www.corrosiondoctors.com)
Tabela 2. Testy zanurzeniowe. Normalizacja. Pierwsza metoda BS 3900-G5 jest łatwiejsza w wykonaniu i zakłada istnienie łagodniejszych warunków niż metoda BS 3900-G8.
Tego typu komora klimatyczna pozwala na przeprowadzenie testów w ekstremalnych zakresach temperatury i wilgotności. Dostępny zakres temperatur to -5 do +50˚C. Istnieje możliwość przeprowadzania testów zarówno w stabilnych warunkach, jak i testów cyklicznych, np. od wysokich temperatur i dużej wilgotności do niskich temperatur i minimalnej wilgotności. Typowy zakres testu cyklicznego to: 8 godzin ekspozycji w temperaturze 40˚C i wilgotności względnej 95 proc., po których następuje 16 godzin ekspozycji w temperaturze 20˚C i wilgotności względnej 70 proc. W praktyce zdarza się, że nie wszystkie kombinacje temperatury, wilgotności względnej i czasu trwania jednego cyklu badania mogą zostać zrealizowane.
Testy badające odporność na zanurzenie powłoki w wodzie
Opis metody
Testy zanurzeniowe w wodzie pozwalają ocenić jak dana powłoka znosi przedłużoną ekspozycję w warunkach skondensowanej pary wodnej (w środowisku niezawierającym innych promotorów korozji). Test ten nie pozwala jednak na symulację konkretnych warunków o ustalonych parametrach.
Zaleca się stosowanie dwóch metod:
- Testy zanurzeniowe (patrz tabela 2).
- Test zanurzeniowy na odporność powłoki na wilgoć (patrz. fot. 3).
Należy pamiętać, że zaprezentowane tutaj testy mają charakter porównawczy, nie zapewniają więc bezwzględnych danych. Pozwalają stwierdzić czy powłoka A ma lepsze własności antykorozyjne od powłoki B. Często jednak wymagana jest informacja typu:” wyniki testu wskazują, że powłoka A zapewni skuteczną ochronę antykorozyjną stali przez 10 lat użytkowania w warunkach np. ruchu drogowego. ”.Aby otrzymać dane bezwzględne tego typu dla danej powłoki A, należy przeprowadzić taki sam test dla powłoki referencyjnej B, o której wiadomo, że zapewnia skuteczną ochronę antykorozyjną stali przez 10 lat w warunkach ruchu drogowego. Powłoki A i B powinny również charakteryzować się podobnym składem. Przeprowadza się wówczas ten sam test na obu powłokach aż do momentu, gdy jedna z nich ulegnie uszkodzeniu. Jeśli jako pierwsza uszkodzeniu ulegnie powłoka referencyjna B, wówczas stwierdzić można:” wyniki testu wskazują, że powłoka A zapewnia skuteczną ochronę antykorozyjną stali przez 10 lat w warunkach ruchu drogowego”. Należy podkreślić, że niekiedy testy laboratoryjne mogą dostarczać mylnych informacji na temat własności antykorozyjnych powłok. Najbardziej wiarygodny zestaw na ten temat zapewnia kombinacja wyników testów laboratoryjnych i efektów użytkowania powłoki w rzeczywistych warunkach.
Dorota Kropelnicka-Babiak
PRONET-COLOR
Komentarze (0)