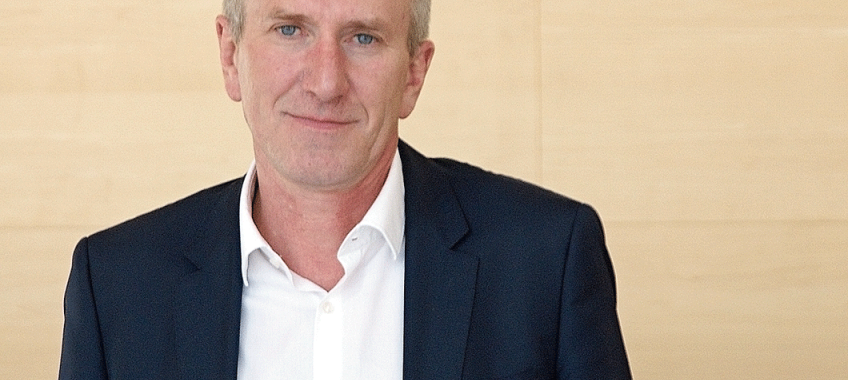
Rozmawiamy z Markiem Żakiem, prezesem zarządu, głównym udziałowcem i założycielem firmy Lumag.
- Nawiązując do kampanii „Montuję polskie części”, w której firma Lumag bierze udział, proszę krótko streścić jej główne założenia oraz powiedzieć, jakie są główne problemy, z którymi zmaga się polski rynek części?
Kampania „Montuję polskie części” ma na celu budowanie pozytywnego wizerunku polskich producentów części motoryzacyjnych. Kampania skierowana jest w głównej mierze do pracowników warsztatów samochodowych i docelowo ma ona zachęcać także do postawy patriotyzmu konsumenckiego, czyli stosowania do napraw polskich produktów wtedy, kiedy polski produkt jest na porównywalnym poziomie jakościowym jak zagraniczny.
- Czy są już widoczne efekty kampanii? Czy polscy sprzedawcy części zamiennych i serwisy wykazują chęć pomocy w rozwiązaniu ww. problemów?
Jest jeszcze za wcześnie na mówienie o wymiernych efektach kampanii. Wszystkie działania wizerunkowe wymagają czasu. Kampania wystartowała niecałe pół roku temu. Na jej pierwszym etapie ważne jest, aby zwrócić uwagę grupy docelowej na podstawowe założenia kampanii. Jak do tej pory spotykamy się ze strony mechaników z bardzo dużą ilością życzliwych głosów poparcia idei montowania polskich części.
- Jaki jest udział firmy Lumag w kampanii „Montuję...”?
Lumag jest jedną z firm, które zainicjowały kampanię. Nasz udział polega między innymi na merytorycznym wspieraniu kampanii. Nasi pracownicy uczestniczą w formułowaniu głównych komunikatów, jednak już bezpośrednim prowadzeniem kampanii zajmuje się wyspecjalizowana firma, z którą wspólnie z innymi producentami współpracujemy.
- W 2013 roku firma Lumag zrealizowała 111,9% założonego planu sprzedaży. Czy równie dobrze zapowiada się rok bieżący?
Rok 2014 jak dotąd charakteryzuje się dość dużą dynamiką wzrostu i wszystko wskazuje na to, że tak będzie nadal. Zainteresowanie produktami wytwarzanymi przez firmę Lumag jest obecnie tak duże, że nie jest ona w stanie zrealizować wszystkich zamówień. Stąd konieczność realizacji kolejnych projektów inwestycyjnych zwiększających moce produkcyjne firmy, nie tylko na ten rok, ale również na rok 2015. Na ten rok założyliśmy 10-procentowy wzrost w stosunku do roku poprzedniego i z pewnością uda nam się ten przyrost osiągnąć. Obecny popyt na nasze produkty pokazuje, że wzrost obrotów mógłby być znacznie większy, gdyby nie ograniczenia wydajnościowe w niektórych referencjach i procesach produkcyjnych. Problem ten zostanie rozwiązany w 2015 roku.
- Działający od września ubiegłego roku zakład produkcyjny w Budzyniu to największa inwestycja w dotychczasowej historii firmy. Proszę opowiedzieć o kolejnych planach inwestycyjnych spółki.
Nowa fabryka została zaplanowana perspektywicznie, tak aby można było w przyszłości dokładać kolejne linie technologiczne. Obecnie jesteśmy w fazie wdrażania II etapu inwestycyjnego, mającego na celu zwielokrotnienie możliwości produkcyjnych naszej fabryki poprzez zakup kilku linii technologicznych. Pod koniec maja uruchomiliśmy linię do szlifowania klocków połączoną z malarką proszkową oraz maszyną do znakowania wyrobów metodą tampondruku. Kolejne zamówione już linie technologiczne to linia do piaskowania oraz nakładania kleju na płytki nośne klocków hamulcowych oraz dwa centra prasowalnicze połączone z piecami do wygrzewania klocków hamulcowych. Priorytetowe dla nas są również inwestycje w dynamiczny rozwój własnego centrum badawczego poprzez zakup kolejnego dynamometru.
Druga fala inwestycji, która pochłonie 35 mln PLN (8,5 mln EUR), okazała się konieczna w celu sprostania obecnemu nadpopytowi na nasze produkty ze strony zarówno stałych, jak i nowych klientów. Ale jest ona zgodna ze strategią przyjętą przez naszą spółkę na najbliższe lata. Należy jednak pamiętać, że proces zamawiania i instalowania kolejnych linii technologicznych trwa z reguły wiele miesięcy. Warto również dodać, że nasza firma rozpoczęła wdrożenie systemu klasy ERP – IFS Applications 8, ze szczególnym uwzględnieniem funkcjonalności B2B. Rozwiązanie usprawni zarządzanie firmą, optymalizując kluczowe procesy biznesowe w spółce oraz usprawniając współpracę z klientem.
- Jak na pozycję spółki (i jej marek) w Polsce i na świecie wpłynęła budowa budzyńskiej fabryki?
Myślę, że jeszcze jest za wcześnie na taką ocenę. Tym niemniej nowa fabryka jest bardzo pozytywnie odbierana przez naszych klientów, zwłaszcza tych bardziej wymagających, którzy rozważają Lumag jako partnera do realizacji nowych projektów pierwszomontażowych. Dlatego też, pomimo że już od kilku lata działamy w oparciu o normy ISO/TS 16 949, w maju poddaliśmy się procesowi certyfikacji tej normy, który zakończył się wynikiem pozytywnym. Firma Lumag jest przygotowana do produkcji wyrobów o wysokich standardach jakościowych oraz spełnia wymagania klientów branży motoryzacyjnej. Z pewnością pomoże to w pozycjonowaniu marek Lumag i Breck, zarówno na rynku polskim, jak i na rynkach zagranicznych.
- Fabryka Lumag to nowoczesny obiekt, w którym zastosowano wiele innowacyjnych technologii. Proszę wymienić kilka najważniejszych, które mają największy wpływ na produkcję.
Zarówno konstrukcja i projekt samego budynku, jak i w pełni zautomatyzowane linie technologiczne, reprezentujące najwyższe standardy jakościowe i wydajnościowe, jakie są obecnie stosowane w branży materiałów ciernych, świadczą o wysokich standardach, jakie przyjęliśmy w tym projekcie. Obecnie wszystkie procesy wytwarzania klocków hamulcowych, począwszy od produkcji mieszanki ciernej, a skończywszy na ich obróbce za pomocą linii do szlifowania i znakowania klocków, są w pełni zautomatyzowane.
Sama mieszalnia jest unikatowym rozwiązaniem w skali światowej. Technologia automatycznego dozowania włókien oraz wełny stalowej w produkcji mieszanek ciernych, jak również koncepcja transportu dozowanych składników przy zastosowaniu transportu kubełkowego, zostały zastosowane po raz pierwszy na świecie właśnie przy realizacji tego projektu.
Projekt nowej fabryki obejmuje również wdrożenie wymaganych w branży automotive systemów jakości i funkcjonowania, w tym filozofię „Lean Manufacturing” – minimalizującą ryzyko strat, błędów, przestojów, a maksymalizującą wydajność. Ma to również bardzo pozytywny wpływ na jakość i wydajność produkcji. Projektując fabrykę, pomyśleliśmy o wielu proekologicznych rozwiązaniach, które przynoszą firmie wymierne korzyści w postaci zmniejszonego zużycia energii oraz gazu. Inteligentnie sterowane falowniki regulują pobór energii przez określone linie technologiczne oraz elementy infrastruktury w zależności od stopnia ich wykorzystania. Natomiast systemy recyrkulacji powietrza oraz ogrzewania opartego na promiennikach podczerwieni pozwalają na tańsze i efektywniejsze ogrzewanie dużych powierzchni, koncentrując ciepło w miejscach, które tego wymagają. Udało nam się również zredukować do minimum poziom hałasu emitowany do środowiska zewnętrznego poprzez instalację trzech stacji filtrów Scheuch, reprezentujących obecnie najwyższy stan techniki w tym zakresie. W dzisiejszych czasach ekologiczne rozwiązania w produkcji są coraz bardziej doceniane przez klientów.
Rozmawiał: Krzysztof Dulny
Fot. Magdalena Bielawska
Komentarze (0)