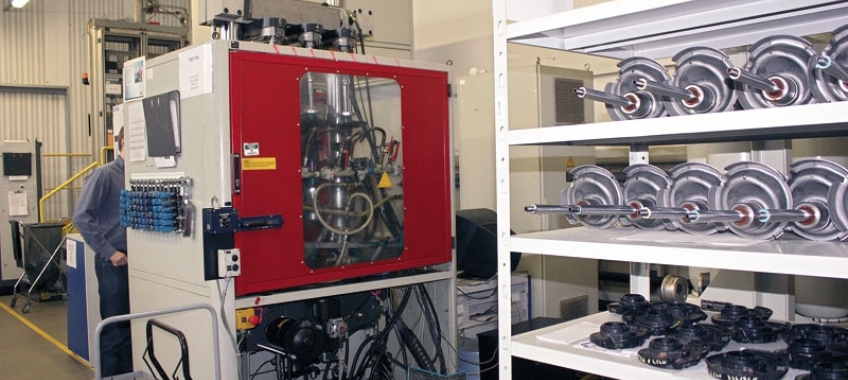
Nie tak dawno w reakcji na wyniki testów przeprowadzonych przez producentów amortyzatorów OEM i nadzorowanych przez SECUR Francja uwzględniła w swoim okresowym przeglądzie technicznym test szczelności amortyzatorów. Stało się tak po tym, jak testy przeprowadzone przez TRW wykazały, że sprawność jazdy może pogorszyć się do 8% w porównaniu z pojazdem wyposażonym w cztery nowe części.
Nie bez powodu amortyzatory uznaje się za kluczowy produkt bezpieczeństwa w ruchu drogowym. Nowoczesne amortyzatory są tak konstruowane, by kompromisowo godzić wymagania komfortu i bezpieczeństwa jazdy. Amortyzatory stosowane w zawieszeniach samochodowych tłumią drgania, zamieniając ruch (energię kinetyczną) w... ciepło. Odbywa się to poprzez wymuszenie przepływu płynu (oleju w amortyzatorach olejowych) przez system kanałów i zaworów tworzących opór hydrauliczny. W amortyzatorach hydrauliczno-gazowych poza olejem znajduje się sprężony gaz. Koncerny motoryzacyjne oczekują dziś bardzo wyśrubowanych charakterystyk pracy amortyzatorów. Pytanie, jak wygląda transfer doświadczeń na rynek aftermarketowy?
- Projektując produkt aftermarketowy, opieramy się też na własnym doświadczeniu. Często konsolidujemy doświadczenie zdobyte przy produkcji elementów na pierwszy montaż. Co to oznacza? Zamiast oferować amortyzatory o 20 charakterystykach, przy dzisiejszej rynkowej presji na cenę, optymalizujemy produkt i produkujemy takie tylko w kilku odpowiednio dobranych charakterystykach. Dzięki temu jesteśmy w stanie oferować produkt sprawdzony na pierwszym montażu, zunifikowany, więc w korzystnej cenie – zauważa Michał Kozyra, Product Engineer AM, Tenneco Automotive. - Transfer wiedzy jest bardzo korzystny dla obu stron. Trudno jednocześnie wymagać, by takim samym zapleczem technologicznym dysponował azjatycki producent, który bazuje tylko na produkcie kopiowanym i wdrażanym do produkcji tylko i wyłącznie z myślą o rynku wtórnym. W gliwickiej siedzibie Tenneco pracuje sztab inżynierów, którzy są odpowiedzialni za produkcję części zamiennych we wszystkich fabrykach (oprócz filii za oceanem). W centrum technicznym EEEC prócz amortyzatorów na pierwszy, tzw. fabryczny montaż, projektuje się, testuje, a następnie wdraża produkcję części na rynek wtórny. Dział projektowy amortyzatorów na After Market w EEEC liczy obecnie 11 inżynierów. Prócz tego w Belgii, w METC funkcjonuje 6-osobowy zespół projektantów. Prace projektowe są podzielone pomiędzy dwa zespoły: METC prowadzi wstępną część projektu oraz go nadzoruje, w EEEC natomiast wykonywana jest zasadnicza część dokumentacji, taka jak: rysunki, spisy części, dokładne badanie i pomiary produktu. Projektowane są poszczególne części składowe amortyzatora, takie jak: siedzisko sprężyny, uchwyty (bracket), górne mocowania, łożyska, odbojniki itp., jak również kompletne złożenia amortyzatora.
- W gliwickim „aftermarkecie” od 2010 roku działa również inżynier do spraw kontaktów z klientem (tzw. Customer Service Engineer). Jego zadaniem jest udzielanie porad oraz rozwiązywanie problemów technicznych związanych z instalacją naszych produktów. Doradza on również naszym odbiorcom w zakresie doboru właściwego produktu do danego samochodu. Porady te są udzielane poprzez e-maile, jak również telefonicznie. Regiony obsługiwane przez naszego inżyniera to głównie rynek niemiecki, austriacki i szwajcarski. Służy on także wsparciem biurom handlowym z całej Europy w przypadku bardziej skomplikowanych zapytań – dodaje M. Kozyra. Bywa, że to właśnie niewłaściwy montaż lub po prostu źle dobrany amortyzator (do odpowiedniego modelu nadwozia, silnika itp.) jest głównym powodem odmowy reklamacji ze strony niezadowolonego klienta (kierowcy). Produkt aftermarketowy uwzględnia oczywiście typowe przywary kierowcy. Pod uwagę bierze się bowiem fakt, że nowy amortyzator częstokroć będzie musiał „współpracować” z elementami, których kierowca (ze względów oszczędnościowych) po prostu nie zechce wymienić na nowe. Zwykle posiadacz pojazdu rezygnuje z kompleksowej wymiany elementów, które są osłabione (drążki, sprężyny, stabilizatory, łączniki, elementy gumowo-metalowe). Nowy amortyzator (aftermarketowy) ma trudniejsze zadanie do spełnienia, bo musi uwzględniać zużycie pozostałych elementów zawieszenia. Ekspert od zawieszenia (mechanik) powinien w pierwszym rzędzie potrafić zdiagnozować przyczynę problemów z prowadzeniem samochodu. Bezpieczeństwo jest priorytetem. W momencie, gdy wybiera produkt dla klienta, ważne jest, by kierował się doświadczeniem producentów, którzy gwarantują rozwiązania sprawdzone – najlepiej oczywiście, gdy jest to jednocześnie dostawca na „pierwszy montaż”.
- Spotyka się przecież na rynku amortyzatory za 35-45 zł za sztukę. Ktoś, kto montuje takie, bierze na siebie duże ryzyko. Nie jest możliwe, by przy dzisiejszych kosztach materiałów i zastosowaniu odpowiednich technologii wyprodukować amortyzator odpowiedniej jakości w tak niskiej cenie – informuje Jarek Danel, Country Manager Poland Aftermarket Southern & Central Europe Tenneco Automotive Polska Sp. z o.o. Zwróćmy uwagę, dziś unika się przewymiarowania produktu aftermaretowego – bo właśnie koszt materiału jest niemały. Zysk kilku gramów na amortyzatorze wydawać się może niewielki, ale w produkcji masowej odchudzenie konstrukcji to ogromne oszczędności.
Inżynierowie pracują bez przerwy nad nowymi rozwiązaniami, ale w dziedzinie elementów zawieszenia przyświecają dziś dwa główne cele: zwiększenie bezpieczeństwa oraz redukcja masy, zwłaszcza gdy chodzi o tak zwaną masę nieresorowaną.
- Do lamusa odchodzi żeliwo, standardem staje się aluminium, wchodzą już na rynek tworzywa i kompozyty (włókno węglowe), wracają na tylnej osi specjalne, nowej generacji resory piórowe (włókno szklane). Te działania pozwalają ponownie na redukcję o ok. 10% na masie. Standardowe amortyzatory zastępowane są systemami z ciągłą kontrolą tłumienia CDC, integracją czujników przyspieszeń kół w wahaczach – zauważa Grzegorz Fedorowicz – Key Account Manager, ZF Friedrichshafen AG. Jak projektuje się takie układy i co wspomaga inżynierów? Czyżby żmudne testy drogowe zastępowano dziś symulacjami komputerowymi? Owszem. Na pewnym etapie udział komputerów jest znacząco większy, ale też wzrasta rola testów (zwłaszcza niszczących na prasach hydraulicznych). Często to indywidualne narzędzia, które zaprojektowali inżynierowie pod kątem jednej aplikacji amortyzatorów. Kilkaset tysięcy cykli – kompresji amortyzatora, do tego siły zginające i boczne; odporność korozyjną. Przeważnie testy przeprowadzane są w górnym limicie „trudności”. Prace nad nowym produktem aftermarketowym zaczyna się dziś w środowisku CAD (modelowanie produktu) i analiz FEM.
- Następnie wykonywane są prototypy elementów zawieszenia, testy pojedynczych elementów i testy zbudowanego zawieszania na stanowiskach hydrauliczno-pulsacyjnych, gdzie w symulacji różnych warunków drogowych możliwe są nieograniczone przebiegi – wyjaśnia G. Fedorowicz. - Potem przychodzi czas na testy na torach ze starymi jeszcze nadwoziami, dopiero później są udostępniane do testów przed OE u producentów modelu pojazdu. Oczywiście koncerny samochodowe od początku współpracują z nami przy konstruowaniu nowych zawieszeń; mają biura przy naszych ośrodkach OBR. Jeżeli chodzi o końcowy montaż na OE, wymagane jest dostarczanie już pełnych modułów „just on time”. Przy projektowaniu oczywiście wspomaga inżynierów wszechobecna elektronika i coraz bardziej zaawansowane i szybsze systemy obliczeniowe.
Rafał Dobrowolski
Fot. Tenneco, ZF, R. Dobrowolski
Komentarze (0)