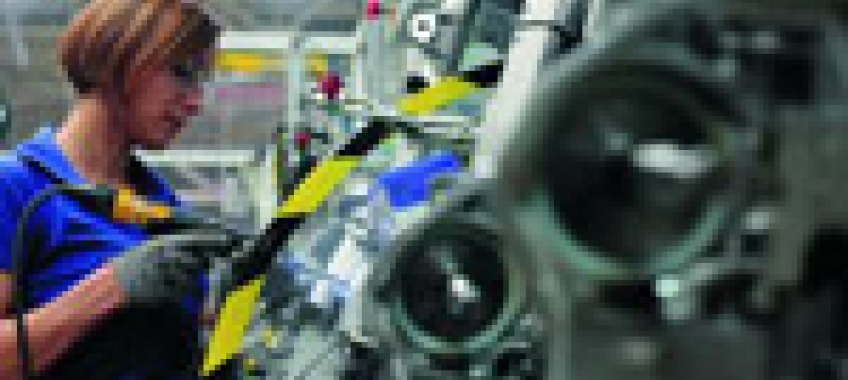
Zwiedzanie linii produkującej EPS dla najnowszego modelu C3, wizyta w specjalistycznej komorze akustycznej i laboratorium, a w końcu jazdy testowe samochodami wyposażonymi w najnowocześniejsze układy kierownicze – tak wyglądał program spotkania prasowego w tyskiej fabryce Nexteer Automotive. Przedstawiciele firmy umożliwili zaproszonym dziennikarzom motoryzacyjnym poznanie tajników produkcji. Przybliżyli też najbliższe plany koncernu w Polsce.
W roku 2009, zatrudniająca 1200 osób tyska fabryka Nexteer Automotive (dawniej Delphi) rozpoczęła produkcję Single Pinion EPS (Electric Power Steering), najnowocześniejszego układu kierowniczego ze wspomaganiem elektrycznym, w który wyposażony jest nowy model grupy PSA – Citroën C3. Dzięki zastosowaniu technologii stworzonych przez inżynierów koncernu z siedzibą w USA, pozwala on na poprawienie właściwości jezdnych auta i tym samym bezpieczniejsze zachowanie w trakcie jazdy. EPS wpływa też na zmniejszenie wagi samochodu i zużycia paliwa (nawet do czterech procent).
Fot. 1. Usuwanie luzów to jedna z operacji kontrolnych poprawnego montażu wspomagania.
Jedna „wtyczka”
Najważniejszym wyzwaniem jest szczelność podzespołu – w końcu odporność obudowy pracującej w niekorzystnym środowisku (zachlapywanie wodą, błotem, duże wahania temperatur, kiepski stan nawierzchni) ma ogromne znaczenie na trwałość układu kierowniczego i bezpieczeństwo jazdy.
- Rozwiązanie tkwi w szczegółach – wyjaśnia Marek Olej, Product Engineer. - Naszym celem było uniewrażliwienie podzespołu na ryzyko zasysania wody. Nasz produkt – odwrotnie do konkurencyjnych ma tylko jedną „wtyczkę” – tak określamy w żargonie inżynierów miejsce, gdzie może nastąpić penetracja wody, np. dzięki różnicy ciśnień, powodowanej typową sytuacją podczas codziennej eksploatacji pojazdu, kiedy temperatura pracującej obudowy mechanizmu jest wysoka, a wody zalegającej na ulicach: niska. Zanim gotowy element trafi do seryjnie produkowanych pojazdów, poddawany jest testowi na szczelność. Do kontrolowania procesu produkcji stosuje się też najnowszą technologię RFID (Radio Frequency Identification). System kontroli RFID pozwala na szczegółowe badanie i zbieranie informacji na każdym etapie procesu produkcji (fot 1). Jak działa?
Fot. 2. Mechanizm wspomagania układu kierowniczego C3.
- Maszyny wyposażone są w czytniki, które identyfikują każdy podzespół i potwierdzają prawidłowe procedury produkcji z poprzednich etapów – wyjaśnia Radosław Bury, Lean Manufacturing Manager. - Jeśli jest inaczej, to na komputerze pojawia się komunikat o błędzie powstałym na poprzedniej operacji. Ale to nie wszystko. Nasze rozwiązanie zapewnia monitoring podzespołów po opuszczeniu bram fabryki. Numer seryjny z informacją o przebiegu montażu i ewentualnie przeprowadzonych poprawkach jest archiwizowany, co w przyszłości może okazać się bardzo pomocne mechanikowi, któremu przyjdzie naprawiać czy serwisować układ kierowniczy.
Fot. 3. Montaż listwy zębatej.
Globalna wizja
Globalny koncern ma aż 15 fabryk na świecie (łącznie w 12 krajach, na 5 kontynentach). Klientami firmy jest 60 koncernów motoryzacyjnych, m.in.: GM, Ford, Fiat, Toyota, grupa PSA. 100 lat doświadczeń w produkcji układów kierowniczych zobowiązuje. Polskie fabryki (druga znajduje się w Gliwicach) produkują rokrocznie ok. 3 mln układów i kolumn kierowniczych. Tyska fabryka jest też największym zakładem produkcyjnym koncernu. Z ponad 12 mln EPS połowę opuściło fabrykę w Tychach! Inwestycja w nowoczesny park maszyn robi wrażenie. Do dyspozycji konstruktorów jest unikatowa komora akustyczna. To niepowtarzalne miejsce, w którym można odtworzyć każdy profil drogi – nagranie realizowane jest wspólnie z klientem, czyli koncernem motoryzacyjnym – z myślą o doskonaleniu cichej pracy układu kierowniczego. Nad wynikami badań czuwa laboratorium w Paryżu. W gliwickiej fabryce realizowany jest już projekt EPSILON II, z myślą o produkcji układów kierowniczych dla nowych modeli: Opla – Insignii i następcy modelu Corsy (rozpoczęcie produkcji w roku 2013) oraz marki Saab – modelu 95. W tyskiej fabryce będą z kolei powstawać układy kierownicze dla Lancii Y (rozpoczęcie produkcji w roku 2011).
Fot. 4. Płytka kontrolera EPS C3.
Jak powstaje układ kierowniczy do C3?
Wysoka precyzja wykonania Single Pinion EPS wymaga zaangażowania pracowników i najnowszej generacji maszyn. Proces produkcji składa się z 24 etapów (9 wykonywanych jest w Tychach; 15 w Gliwicach). W Tychach pierwszym obrabianym elementem jest wałek zębnika. Połączony z górnym wałkiem ulega zaprasowaniu – oczywiście z kontrolą pozycji osiowej względem wałka – w końcu to kluczowa dla przekładni część. Kolejnym etapem jest obróbka aluminiowej obudowy, która chroni podzespół przed czynnikami zewnętrznymi (fot. 2). Każda z obrabiarek sterowanych numerycznie ma kilka głowic, które wiercą, gwintują, planują powierzchnie.
Fot. 5. Poglądowy widok na podzespół kierowniczy najnowszego modelu C3.
- Zamocowanie jest podwójne, czyli jedna z czterech maszyn obrabia naraz dwie sztuki i dzięki temu jesteśmy w stanie wykonać tysiąc układów kierowniczych dziennie na dwóch zmianach; a to jeszcze nie jest pełen wolumen C3! – wyjaśniają nam inżynierowie. Potem całość trafia do myjki i suszarni. Kolejnym etapem jest zazębianie samej listwy. W końcu przychodzi pora na mocowanie wałka zębatego – jeszcze zanim dodamy elektronikę, wspomaganie, czujnik kąta i momentu obrotowego. Ostatnim elementem obrabianym są ślimaki, wałki. Zęby są dogniatane, żeby po szlifowaniu powierzchnia każdego zęba była wolna od niedoskonałości.
Po montażu mechanicznym elementy trafiają do „grey-roomu”, gdzie w sterylnie czystych warunkach montowana jest elektronika (m.in. silnik z czujnikiem Hala) a całość zamykana (fot. 4). Eliminację m.in. ładunków elektrostatycznych gwarantuje specjalna odzież i obuwie ochronne O wstępie do pomieszczenia decydują komputerowe czujniki, które „skanują” każdego wchodzącego.
Fot. 6. Gonzalo Herera i Radosław Bury chwalili się także bezpieczeństwem produkcji w polskich fabrykach – to już milion przepracowanych godzin i ani jeden wypadek przy pracy!
- Polskie zakłady wyznaczają światowy standard. Nie bez powodu też slogan koncernu skojarzyliśmy z nową nazwą firmy: Nexteer od słowa next – bo jesteśmy już za zakrętem, wyznaczając światową jakość i innowację... a konkurencja musi nas teraz gonić – zapewniał dziennikarzy podczas konferencji prasowej Gonzalo Herera, dyrektor tyskiej fabryki Nexteer Automotive, zapraszając po zakończeniu zwiedzania zakładu na jazdy testowe przygotowanymi egzemplarzami najnowszych pojazdów.
Rafał Dobrowolski
Komentarze (0)