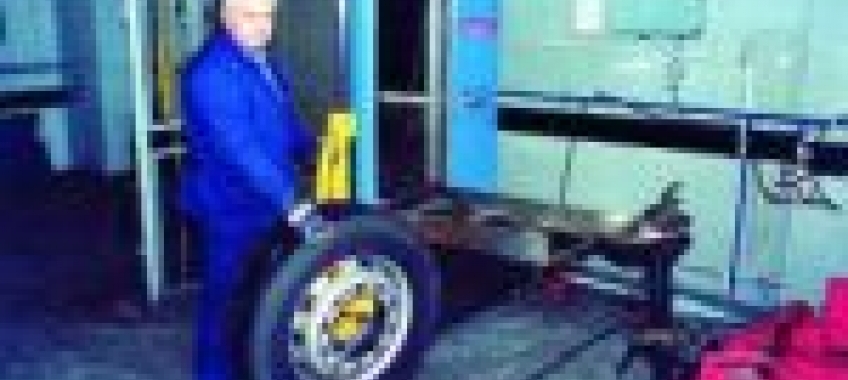
Obecnie na rynku istnieje spora ilość warsztatów decydująca się na rozszerzenie zakresu działalności o serwis ogumienia.
Opona jest elastycznym łącznikiem pojazdów samochodowych z powierzchnią drogi. W przeszłości właściciele pojazdów nie przykładali aż tak dużej wagi do stanu technicznego ogumienia. Obecnie ze względu na prędkości rozwijane przez współczesne samochody, niemalże każdy użytkownik pojazdu zdaje sobie sprawę z tego, jak wielkie znaczenie ma jej właściwy stan techniczny dla bezpieczeństwa ruchu drogowego. Poza aspektem bezpieczeństwa, utrzymywanie prawidłowego stanu technicznego opon oraz dbałość i przestrzeganie zaleceń fabrycznych odnośnie ciśnienia wpływa znacząco na komfort jazdy oraz żywotność opon.
To właśnie wzrastająca ciągle świadomość użytkowników pojazdów w zakresie bezpieczeństwa jazdy oraz wprowadzanie nowych rozwiązań konstrukcyjnych, nie tylko opon, ale również obręczy (zwłaszcza ze stopów lekkich), doprowadziło do znacznego rozwoju w zakresie techniki warsztatowej dotyczącej obsługi ogumienia, a także zwiększenia ilości nowo powstających placówek zajmujących się tego typu usługami. Ponadto powszechne wprowadzenie do użytku opon sezonowych (letnich i zimowych) spowodowało, że czynności związane z obsługą ogumienia należą do grupy najczęściej wykonywanych operacji technicznych we współczesnych pojazdach samochodowych.
Wszystkie te czynniki powodują, że coraz większa ilość warsztatów decyduje się na rozszerzenie zakresu działalności o serwis ogumienia lub całkowicie się na niego nastawia. Jak w każdej branży, wielkość i charakter placówki tego typu zależy od możliwości finansowych inwestora. Ze względu na fakt sezonowości wymiany ogumienia, tego typu warsztat może być częściowo zlokalizowany na zewnątrz, poza obiektami zamkniętymi. Największe obłożenie pracami występuje wiosną i jesienią, a o tej porze roku z całą pewnością można śmiało pracować na zewnątrz obiektu zamkniętego. Dlatego jako zasadę przy tworzeniu tego typu placówki przyjmuje się wydzielenie kilku stanowisk na zewnątrz, a w związku z tym wystarczy tylko zadaszyć całe stanowisko robocze. Podstawą współczesnego warsztatu samochodowego zajmującego się obsługą ogumienia jest zapewnienie ciągłego dostarczania do pracujących w nim urządzeń sprężonego powietrza w odpowiedniej ilości i o właściwej jakości. Nowoczesna instalacja sprężonego powietrza montowana jest z elementów wykonanych z tworzyw sztucznych. Materiały te w odróżnieniu od stosowanych w przeszłości elementów metalowych są odporne na wahania temperatury, co zapewnia zachowanie szczelności połączeń oraz zabezpiecza instalację przed powstawaniem wody w przewodach. Instalacja sprężonego powietrza powinna być tak dobrana, aby jej wielkość i wydajność odpowiadały zapotrzebowaniu na sprężone powietrze wszystkich pracujących w warsztacie maszyn i urządzeń. Parametrami technicznymi niezbędnymi do rozpoczęcia jakichkolwiek prac projektowych instalacji są:
- ilość przewidywanych stanowisk odbiorczych,
- nominalne zużycie sprężonego powietrza na poszczególnych stanowiskach,
- wymagane ciśnienie robocze odbiorników (maszyn i urządzeń) na poszczególnych stanowiskach,
- długości poszczególnych odcinków przewodów (przewidywane usytuowanie stanowisk odbiorczych).
Podstawowym urządzeniem w całej instalacji jest sprężarka, która wytwarza sprężone powietrze. W przeszłości stosowano najczęściej sprężarki tłokowe. Obecnie zostają one wypierane przez sprężarki śrubowe. Charakteryzują się one sprężaniem powietrza w przestrzeniach pomiędzy dwoma wirującymi śrubami w ośrodku olejowym. Ich zaletą w stosunku od wcześniej stosowanych tłokowych jest znacznie niższy poziom wytwarzanego hałasu oraz znacznie wyższa trwałość dochodząca nawet do 30 tysięcy roboczogodzin. Kolejnym ważnym ogniwem systemu jest zbiornik ciśnieniowy. Najważniejszą funkcją zbiornika ciśnienia jest bilansowanie wydajności sprężarki z aktualnym zapotrzebowaniem powietrza w instalacji. Dzięki temu nie ma konieczności ciągłej pracy sprężarki, a jej włączaniem i wyłączaniem steruje wyłącznik ciśnieniowy w zależności od aktualnego ciśnienia sprężonego powietrza w zbiorniku. Dla wstępnego ustabilizowania ciśnienia w instalacji sprężonego powietrza na przewodach odpływowych zbiornika ciśnienia instaluje się nastawne reduktory z manometrami. Obecnie w większości warsztatowych instalacji sprężonego powietrza wykorzystuje się ciśnienie robocze od 6 do 10 bar. Powietrze przed doprowadzeniem go do jakiegokolwiek rodzaju odbiornika musi być najpierw odpowiednio, adekwatnie do konkretnego przypadku przygotowane i uzdatnione, poprzez:
- oczyszczenie z zanieczyszczeń: mechanicznych (pyłu, rdzy), wody oraz oleju;
- redukcję ciśnienia do wymaganej przez konkretny odbiornik wielkości;
- nasączanie olejem poprzez wprowadzenie kontrolowanej ilości czynnika smarnego w postaci mgły olejowej (dotyczy to punktów zasilania kluczy pneumatycznych).
W warsztacie zajmującym się serwisem ogumienia samochodowego niezbędne jest stworzenie optymalnego dla danej placówki rozwiązania problemu całkowitego lub częściowego unoszenia pojazdu w celu odkręcenia kół. Do demontażu jednego koła (np. w przypadku naprawy opony) stosuje się przejezdne podnośniki hydrauliczne podsuwane pod tą część samochodu, po której zachodzi konieczność jego uniesienia. W przypadku konieczności obsługi jednocześnie większej ilości kół w pojeździe, stosuje się podnośniki najazdowe (najczęściej dwukolumnowe). Kolejnym krokiem w serwisie ogumienia jest odkręcanie i ponowne dokręcanie kół (po wykonaniu następnych czynności obsługowych). W przeszłości stosowano tylko ręczny klucz krzyżowy. We współczesnych warsztatach jest to już niedopuszczalna praktyka. Profesjonalnie działające placówki tego typu stosują tylko klucze pneumatyczne. Ich stosowanie znacznie ułatwia pracę i zdecydowanie zwiększa jej wydajność. Do obsługi kół samochodów osobowych i dostawczych w zupełności wystarczy klucz pneumatyczny o momencie ok. 400 Nm. Ze względów bezpieczeństwa niezmiernie ważne jest dokręcanie śrub mocujących koło momentem zgodnym z zaleceniami producenta pojazdu. Dlatego idealnym rozwiązaniem jest stosowanie klucza pneumatycznego z przystawką dynamometryczną. Jednak ze względów ekonomicznych używa się zwykłego klucza pneumatycznego, a w ostatniej fazie dokręcania stosowanie ręcznego klucza dynamometrycznego.
Warunkiem koniecznym do dalszych czynności obsługowych w serwisie ogumienia jest umycie koła. Nie chodzi tu tylko o kulturę obsługi, dbałość o trwałość maszyn (montażownic i wyważarek) oraz zachowanie czystości podczas pracy. Niedokładnie umyte koło na skutek pozostania na oponie i obręczy zanieczyszczeń jest powodem fałszowania wyników wyrównoważenia. Do tego celu stosuje się najczęściej profesjonalne myjki wysokociśnieniowe (najlepiej na gorącą wodę). W pełni profesjonalnym rozwiązaniem jest stosowanie myjki do kompletnych kół w układzie zamkniętym. Najnowsze rozwiązania opierają się na zastosowaniu w niej zimnej wody i drobnych plastikowych kuleczek, które kierowane są z dużą prędkością na obracające się wewnątrz myjki koło. Są one w pełni bezpieczne dla powierzchni obręczy koła, a zarazem bardzo skuteczne w usuwaniu brudu i na trwałe przylegających zanieczyszczeń.
Czas mycia w takim urządzeniu może być regulowany w zakresie do 2 minut, lecz przeciętnie wystarcza w zupełności około 30 sekund. Po przeprowadzonym procesie mycia koło jest dodatkowo odmuchiwane sprężonym powietrzem w celu usunięcia pozostałości wody.
mgr Andrzej Kowalewski
Opona jest elastycznym łącznikiem pojazdów samochodowych z powierzchnią drogi. W przeszłości właściciele pojazdów nie przykładali aż tak dużej wagi do stanu technicznego ogumienia. Obecnie ze względu na prędkości rozwijane przez współczesne samochody, niemalże każdy użytkownik pojazdu zdaje sobie sprawę z tego, jak wielkie znaczenie ma jej właściwy stan techniczny dla bezpieczeństwa ruchu drogowego. Poza aspektem bezpieczeństwa, utrzymywanie prawidłowego stanu technicznego opon oraz dbałość i przestrzeganie zaleceń fabrycznych odnośnie ciśnienia wpływa znacząco na komfort jazdy oraz żywotność opon.
To właśnie wzrastająca ciągle świadomość użytkowników pojazdów w zakresie bezpieczeństwa jazdy oraz wprowadzanie nowych rozwiązań konstrukcyjnych, nie tylko opon, ale również obręczy (zwłaszcza ze stopów lekkich), doprowadziło do znacznego rozwoju w zakresie techniki warsztatowej dotyczącej obsługi ogumienia, a także zwiększenia ilości nowo powstających placówek zajmujących się tego typu usługami. Ponadto powszechne wprowadzenie do użytku opon sezonowych (letnich i zimowych) spowodowało, że czynności związane z obsługą ogumienia należą do grupy najczęściej wykonywanych operacji technicznych we współczesnych pojazdach samochodowych.
Wszystkie te czynniki powodują, że coraz większa ilość warsztatów decyduje się na rozszerzenie zakresu działalności o serwis ogumienia lub całkowicie się na niego nastawia. Jak w każdej branży, wielkość i charakter placówki tego typu zależy od możliwości finansowych inwestora. Ze względu na fakt sezonowości wymiany ogumienia, tego typu warsztat może być częściowo zlokalizowany na zewnątrz, poza obiektami zamkniętymi. Największe obłożenie pracami występuje wiosną i jesienią, a o tej porze roku z całą pewnością można śmiało pracować na zewnątrz obiektu zamkniętego. Dlatego jako zasadę przy tworzeniu tego typu placówki przyjmuje się wydzielenie kilku stanowisk na zewnątrz, a w związku z tym wystarczy tylko zadaszyć całe stanowisko robocze. Podstawą współczesnego warsztatu samochodowego zajmującego się obsługą ogumienia jest zapewnienie ciągłego dostarczania do pracujących w nim urządzeń sprężonego powietrza w odpowiedniej ilości i o właściwej jakości. Nowoczesna instalacja sprężonego powietrza montowana jest z elementów wykonanych z tworzyw sztucznych. Materiały te w odróżnieniu od stosowanych w przeszłości elementów metalowych są odporne na wahania temperatury, co zapewnia zachowanie szczelności połączeń oraz zabezpiecza instalację przed powstawaniem wody w przewodach. Instalacja sprężonego powietrza powinna być tak dobrana, aby jej wielkość i wydajność odpowiadały zapotrzebowaniu na sprężone powietrze wszystkich pracujących w warsztacie maszyn i urządzeń. Parametrami technicznymi niezbędnymi do rozpoczęcia jakichkolwiek prac projektowych instalacji są:
- ilość przewidywanych stanowisk odbiorczych,
- nominalne zużycie sprężonego powietrza na poszczególnych stanowiskach,
- wymagane ciśnienie robocze odbiorników (maszyn i urządzeń) na poszczególnych stanowiskach,
- długości poszczególnych odcinków przewodów (przewidywane usytuowanie stanowisk odbiorczych).
Podstawowym urządzeniem w całej instalacji jest sprężarka, która wytwarza sprężone powietrze. W przeszłości stosowano najczęściej sprężarki tłokowe. Obecnie zostają one wypierane przez sprężarki śrubowe. Charakteryzują się one sprężaniem powietrza w przestrzeniach pomiędzy dwoma wirującymi śrubami w ośrodku olejowym. Ich zaletą w stosunku od wcześniej stosowanych tłokowych jest znacznie niższy poziom wytwarzanego hałasu oraz znacznie wyższa trwałość dochodząca nawet do 30 tysięcy roboczogodzin. Kolejnym ważnym ogniwem systemu jest zbiornik ciśnieniowy. Najważniejszą funkcją zbiornika ciśnienia jest bilansowanie wydajności sprężarki z aktualnym zapotrzebowaniem powietrza w instalacji. Dzięki temu nie ma konieczności ciągłej pracy sprężarki, a jej włączaniem i wyłączaniem steruje wyłącznik ciśnieniowy w zależności od aktualnego ciśnienia sprężonego powietrza w zbiorniku. Dla wstępnego ustabilizowania ciśnienia w instalacji sprężonego powietrza na przewodach odpływowych zbiornika ciśnienia instaluje się nastawne reduktory z manometrami. Obecnie w większości warsztatowych instalacji sprężonego powietrza wykorzystuje się ciśnienie robocze od 6 do 10 bar. Powietrze przed doprowadzeniem go do jakiegokolwiek rodzaju odbiornika musi być najpierw odpowiednio, adekwatnie do konkretnego przypadku przygotowane i uzdatnione, poprzez:
- oczyszczenie z zanieczyszczeń: mechanicznych (pyłu, rdzy), wody oraz oleju;
- redukcję ciśnienia do wymaganej przez konkretny odbiornik wielkości;
- nasączanie olejem poprzez wprowadzenie kontrolowanej ilości czynnika smarnego w postaci mgły olejowej (dotyczy to punktów zasilania kluczy pneumatycznych).
W warsztacie zajmującym się serwisem ogumienia samochodowego niezbędne jest stworzenie optymalnego dla danej placówki rozwiązania problemu całkowitego lub częściowego unoszenia pojazdu w celu odkręcenia kół. Do demontażu jednego koła (np. w przypadku naprawy opony) stosuje się przejezdne podnośniki hydrauliczne podsuwane pod tą część samochodu, po której zachodzi konieczność jego uniesienia. W przypadku konieczności obsługi jednocześnie większej ilości kół w pojeździe, stosuje się podnośniki najazdowe (najczęściej dwukolumnowe). Kolejnym krokiem w serwisie ogumienia jest odkręcanie i ponowne dokręcanie kół (po wykonaniu następnych czynności obsługowych). W przeszłości stosowano tylko ręczny klucz krzyżowy. We współczesnych warsztatach jest to już niedopuszczalna praktyka. Profesjonalnie działające placówki tego typu stosują tylko klucze pneumatyczne. Ich stosowanie znacznie ułatwia pracę i zdecydowanie zwiększa jej wydajność. Do obsługi kół samochodów osobowych i dostawczych w zupełności wystarczy klucz pneumatyczny o momencie ok. 400 Nm. Ze względów bezpieczeństwa niezmiernie ważne jest dokręcanie śrub mocujących koło momentem zgodnym z zaleceniami producenta pojazdu. Dlatego idealnym rozwiązaniem jest stosowanie klucza pneumatycznego z przystawką dynamometryczną. Jednak ze względów ekonomicznych używa się zwykłego klucza pneumatycznego, a w ostatniej fazie dokręcania stosowanie ręcznego klucza dynamometrycznego.
Warunkiem koniecznym do dalszych czynności obsługowych w serwisie ogumienia jest umycie koła. Nie chodzi tu tylko o kulturę obsługi, dbałość o trwałość maszyn (montażownic i wyważarek) oraz zachowanie czystości podczas pracy. Niedokładnie umyte koło na skutek pozostania na oponie i obręczy zanieczyszczeń jest powodem fałszowania wyników wyrównoważenia. Do tego celu stosuje się najczęściej profesjonalne myjki wysokociśnieniowe (najlepiej na gorącą wodę). W pełni profesjonalnym rozwiązaniem jest stosowanie myjki do kompletnych kół w układzie zamkniętym. Najnowsze rozwiązania opierają się na zastosowaniu w niej zimnej wody i drobnych plastikowych kuleczek, które kierowane są z dużą prędkością na obracające się wewnątrz myjki koło. Są one w pełni bezpieczne dla powierzchni obręczy koła, a zarazem bardzo skuteczne w usuwaniu brudu i na trwałe przylegających zanieczyszczeń.
Czas mycia w takim urządzeniu może być regulowany w zakresie do 2 minut, lecz przeciętnie wystarcza w zupełności około 30 sekund. Po przeprowadzonym procesie mycia koło jest dodatkowo odmuchiwane sprężonym powietrzem w celu usunięcia pozostałości wody.
mgr Andrzej Kowalewski
Komentarze (0)