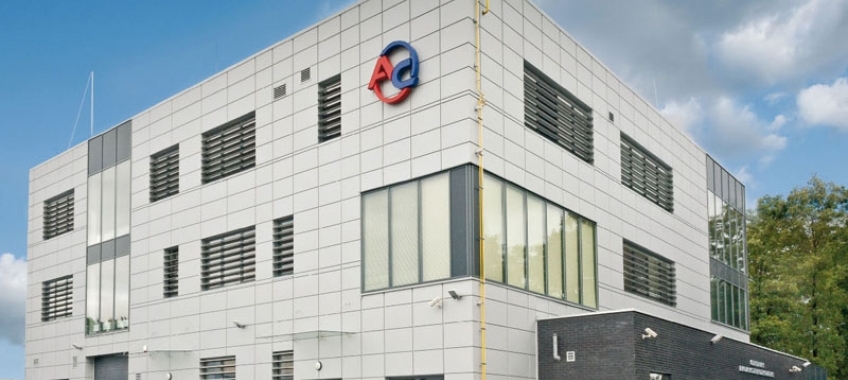
Zanim trafią do produkcji seryjnej, wszystkie produkty firmy AC SA poddawane są licznym testom. Symulacje środowiskowe, które przeprowadzane są na wytwarzanych w Białymstoku podzespołach, umożliwia aparatura oddanego w zeszłym roku do użytku Centrum Badawczo-Rozwojowego firmy. Również tam trwają prace nad prototypami nowych produktów.
Powstały w ramach projektu sfinansowanego z Programu Operacyjnego Innowacyjna Gospodarka 2007-2013 obiekt to ponad 2000 metrów kwadratowych powierzchni rozdysponowanej między laboratoria, hamownie, warsztaty i działy techniczne, w których nie ustają prace nad nowymi technologiami zasilania silników mechanicznych alternatywnymi źródłami energii. Całkowity koszt budowy Centrum wyniósł ponad 18 mln zł. Aby na własne oczy przekonać się o randze inwestycji, zobaczyć, jak duży wpływ na jakość ostatecznego produktu mają realizowane w jednostce prace, odwiedziliśmy firmę AC SA. Po Centrum oprowadził nas Tomasz Cybulko, jeden z pracowników jednostki. Zwiedzanie zaczynamy od...
laboratorium samochodowego
To właśnie tu testuje się prototypowe rozwiązania oraz ulepsza istniejące metody montażu instalacji gazowych. Dostępna aparatura umożliwia realizację badań nie tylko na samochodach osobowych i dostawczych, ale również na pojazdach wielkogabarytowych, np. ciągnikach (zarówno siodłowych, jak i rolniczych) i autobusach. Z laboratorium samochodowego przechodzimy do...
hamowni podwoziowej
Hamownia podwoziowa to przede wszystkim urządzenie diagnostyczne do symulacji obciążeń silnika, na które narażone są pojazdy w ruchu. Dokonywane tu pomiary umożliwiają określenie charakterystyki silnika – mocy i momentu obrotowego, a także mocy na kołach i mocy strat w zależności od prędkości obrotowej pojazdu. Przygotowywane tu są również auta przechodzące testy homologacyjne, testy spalania, testuje się tu nowe rozwiązania i algorytmy sterujące funkcjami programów. Jak wyjaśnił nam Tomasz Cybulko, hamownia w Centrum Badawczo-Rozwojowym AC SA przeznaczona jest do pracy ciągłej dla pojazdów o mocy do 1000 KM. Dodajmy, że w Polsce istnieją tylko dwie hamownie tego typu.
- Możliwość symulacji dowolnych warunków drogowych umożliwia dokładną obserwację sterowników STAG oraz komponentów mechanicznych AC SA nawet przy skrajnie wysokich prędkościach – mówi. - Mamy dzięki temu pewność, że produkty oferowane przez Spółkę skonstruowane są z naddatkiem mocy i nie zawiodą nawet przy ekstremalnych obciążeniach silnika.
Stanowisko wyposażone jest również w profesjonalny analizator spalin, który podczas testu na bieżąco rejestruje poziom emisji zanieczyszczeń.
- Chodzi o to, aby uzyskać jak największą moc, a zarazem jak najmniejszą emisję zanieczyszczeń – dodaje nasz przewodnik. - Takie rygorystyczne testy przechodzi każdy prototyp sterownika wyprodukowany w naszej firmie.
O firmie
AC SA jest producentem samochodowych systemów LPG/CNG marki STAG. Na polskim rynku motoryzacyjnym działa od ponad 27 lat, zatrudnia ponad 500 osób i jest obecnie największą firmą w segmencie instalacji gazowych w kraju. Jak wskazują szacunki spółki, AC SA posiada ponad 50-procentowy udział w rynku polskim. Firma oferuje ponad 200 produktów do autogazu, spośród których wiodącą rolę odgrywają sterowniki do instalacji LPG/CNG. Flagowym elementem oferty handlowej spółki jest seria produktów marki STAG.
Laboratorium badań środowiskowych
Jak już wspomnieliśmy, wszystkie produkty AC SA, zanim trafią na rynek, poddawane są wielu testom. Podzespoły przechodzą m.in. szczegółowe badania środowiskowe, które odtwarzają i analizują ich zachowanie w warunkach odpowiadających rzeczywistym. Laboratoria firmy wyposażone są w wyspecjalizowaną aparaturę i sprzęt pomiarowy, m.in....
komorę klimatyczną
W laboratorium znajdują się dwa takie urządzenia. Pozwalają one na wytworzenie i utrzymanie pod kontrolą zmiennych warunków atmosferycznych – temperatury i wilgotności, czyli podstawowych parametrów panujących w komorze silnika i przedziale pasażerskim.
- W komorze klimatycznej obserwujemy zachowania naszych produktów w różnych warunkach klimatycznych, wykrywając w ten sposób ewentualne błędy projektowe i produkcyjne – wyjaśnia Tomasz Cybulko. - Temperaturę w komorze regulować można w przedziale od -40ºC do +180ºC. Od temperatury zależna jest wilgotność, która oscyluje od 10 do 98% w zakresie temperatur 5ºC do 95ºC.
Aby test był dokładny, czas jego trwania wynosi od kilku dni do... dwóch miesięcy.
Komora szoku temperaturowego
Jak sama nazwa wskazuje, urządzenie analizuje właściwości materiału oraz zachowanie sprzętu wystawionego na działanie gwałtownych zmian temperatury. Na czym polega test?
- Automatyczna winda przemieszcza się pomiędzy komorami o dwóch skrajnych temperaturach: wysokiej i niskiej – demonstruje działanie urządzenia pracownik Centrum. - Możliwy zakres regulacji temperatury komory cieplnej wynosi od +60ºC do +220ºC, zimnej: od -80ºC do +60ºC. Oprogramowanie komory umożliwia szeroki wybór cykli i szybkości przejścia z jednej temperatury do drugiej.
Tak wygląda tzw. test szokowy. W przypadku podzespołów samochodowych istotna jest również szczelność produktów, którą AC SA sprawdza w...
komorze deszczowej
Przeprowadzane w niej badania to kolejny z wielu testów, który egzaminuje produkty Spółki w trudnych, zbliżonych do naturalnych warunkach.
- Każdy nasz wyrób przechodzi egzamin stopnia ochrony, służący do określenia jego szczelności – podkreśla Tomasz Cybulko. - Strategicznie rozmieszczone w komorze dysze deszczowe sprawdzają wodoszczelność produktu w różnych warunkach: od delikatnej mżawki, po intensywną ulewę.
Zgodnie z normą test szczelności trwa 15 minut. Jeżeli po upływie tego czasu woda nie przedostaje się do wnętrza sterownika, obudowa spełnia stopień ochrony IPx4, wymagany przez regulamin R67 i R110.
Komora korozyjna
Badanie korozyjne w mgle solnej umożliwia określenie odporności na korozję takich materiałów, jak: farby, elementy metalowe czy powłoki ochronne. Celem testu jest określenie czasu, po jakim zachodzi korozja.
- Rozprowadzenie w komorze 5-procentowego roztworu soli umożliwia tzw. wieża dystrybucyjna, a używane do wytworzenia mgły solnej sprężone powietrze jest podgrzewane i nasycane wilgocią z nawilżaczy – tłumaczy Tomasz Cybulko. - Badanie kończy się po 7 dniach (170 godzin) i odpowiada 3-letniemu procesowi korozyjnemu. Istotnym elementem oceny gotowości prototypu do produkcji jest określenie jego odporności na wibracje. Służy do tego...
system wibracyjny
Na żywotność i niezawodność produktu, a co za tym idzie – komfort i bezpieczeństwo jego eksploatacji, wpływ mają nawet najmniejsze wibracje. Występujące w samochodzie drgania i przeciążenia symuluje system wibracyjny z ruchomą komorą klimatyczną. Umożliwia on zarówno przeprowadzanie badań regulaminowych, jak i opracowanie autorskich programów badawczych.
- W tym celu w pojeździe montowane są czujniki przyspieszenia, które rejestrują drgania występujące w samochodzie w różnych warunkach i cyklach jezdnych – mówi Tomasz Cybulko. - Drgania te przenoszone są następnie do systemu wibracyjnego i odtwarzane w warunkach środowiskowych. Opcja ta jest niezbędna, gdy obok testów przeprowadzanych zgodnie z wymaganiami norm występuje potrzeba odtworzenia rzeczywistych drgań zależnych od warunków drogowych czy modelu samochodu. Choć komora klimatyczna przystosowana jest do systemu wibracyjnego, może pracować również w trybie całkowicie niezależnym. Zakres temperatury pracy w komorze wynosi od -70ºC do +180ºC, wilgotności względnej od 10 do 98%, a prędkości zmian temperatury – 5K/min.
Idziemy dalej, do...
laboratorium kompatybilności elektromagnetycznej
Pole elektromagnetyczne jednego urządzenia może zakłócać pracę drugiego. Aby zbadać wpływ tych zakłóceń i zmierzyć ich wartość, niezbędna jest specjalistyczna aparatura. Dysponuje nią laboratorium kompatybilności elektromagnetycznej AC SA, które prowadzi pomiary emisji i odporności produktów na zakłócenia przewodzone liniami zasilającymi, sygnałowymi i te przenoszone w powietrzu. I tak np. odporność na częstotliwości radiowe sprawdzana jest na...
stanowisku do badania metodą BCI
Metoda „Bulk Current Injection” polega na testowaniu odporności produktów na wąskopasmowe zaburzenia elektromagnetyczne. Sygnał testowy „wstrzykiwany” jest za pomocą cęgów prądowych o częstotliwości od 20 do 400 MHz, umiejscowionych wokół wiązki przewodów badanego urządzenia. Testy opierają się na zmianie poziomu i częstotliwości wstrzykiwanego sygnału.
- Na wiązkę przewodów zakładana jest cewka generująca oraz cewka odbiorcza, która mierzy wstrzykiwany prąd – wyjaśnia Tomasz Cybulko. - Obserwacja zachowania testowanego układu umożliwia wystawienie diagnozy, przy których częstotliwościach następuje nieprawidłowa praca urządzenia. Dzięki tej informacji można przeprowadzić działania korygujące.
Stanowisko do pomiarów emisji przewodzonej
Do symulacji zaburzeń zasilania oraz ich wpływu na elektronikę instalacji gazowej służy stanowisko do pomiarów emisji przewodzonej. Umieszczone tam generatory symulują spadki lub zwyżki napięcia, za które w samochodzie odpowiadają m.in. takie czynniki jak: uruchomienie i wyłącznie wycieraczek czy też zakłócenia pochodzące z układu zapłonowego (i każdego innego układu elektronicznego).
- Rodzaje symulowanych zaburzeń regulowane są przez szereg norm – mówi nasz przewodnik. - Są one fabrycznie zaprogramowane w generatorach, co gwarantuje szybkie przeprowadzenie testów. Stanowisko, którym dysponuje AC SA, umożliwia również generowanie zakłóceń nieobjętych normami, ale które mogą wystąpić w pojeździe. Takie zakłócenia rejestrowane są w „warunkach polowych”, a następnie przenoszone i odtwarzane w generatorach.
Stanowisko do pomiaru odporności na ESD
Terminem ESD (Electrostatic Discharge) opisuje się chwilowe, niechciane prądy, tzw. wyładowania elektrostatyczne, które mogą spowodować uszkodzenie sprzętu elektronicznego. Ładunki elektrostatyczne powstają wtedy, kiedy oddziałują na siebie dwie powierzchnie, np. naelektryzowane ciało i urządzenie. Powstaje wówczas przeskok iskry pod napięciem rzędu kilku do kilkudziesięciu kV.
- Wyładowania elektrostatyczne mają duży wpływ na elementy elektroniczne – przyznaje Tomasz Cybulko. - Czułych na nie jest bardzo wiele urządzeń, np. układy scalone, dyski twarde itd.
Badania ESD obejmują testy przy napięciu od 8 do 15 kV.
Komora GTEM-1000
Ta imponująca z wyglądu aparatura (patrz zdjęcie) służy do oceny kompatybilności elektromagnetycznej urządzeń, tzn. ich zdolności do poprawnej pracy w określonym środowisku elektromagnetycznym.
- Aby zyskać pewność, że badane fale elektromagnetyczne pochodzą od właściwego urządzenia, testowany sterownik izolowany jest w komorze – pokazuje Tomasz Cybulko. - Komora wyposażona jest w antenę, która mierzy poziom generowanych fal elektromagnetycznych. Zmierzony poziom sygnału wyświetla analizator widma. Innymi słowy, stanowisko umożliwia zakłócanie pracy sterownika w warunkach kontrolowanych. W ten sposób testowana jest odporność elektroniki na działanie zakłóceń, które mogą występować podczas jazdy samochodem. Jest to o tyle istotne, że wszystkie urządzenia elektroniczne spełniać muszą pewne normy określające limity amplitud generowanych zakłóceń. O tym, czy normy te zostają spełnione, informuje nas wspomniany analizator widma.
Krzysztof Dulny
Fot. Krzysztof Dulny i AC SA
Komentarze (0)