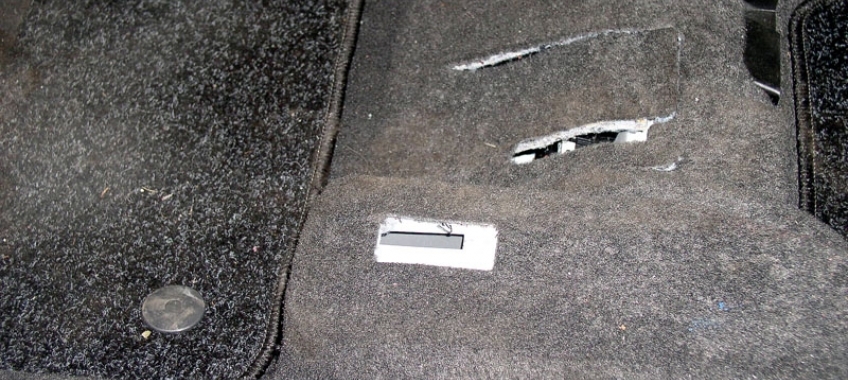
Nadwozie współczesnego samochodu można porównać do blaszanej puszki z wieloma zakamarkami i pustymi przestrzeniami, tzw. profilami zamkniętymi. Te zamknięte przestrzenie potęgują rozchodzenie się hałasu i dźwięków pochodzących z zewnątrz pojazdu, jak również dźwięków wygenerowanych wewnątrz po uderzeniach o podwozie różnego rodzaju zanieczyszczeń znajdujących się na drodze.
Jak to działa w rzeczywistości, można się przekonać po wykonaniu małego doświadczenia. Wystarczy do małej, metalowej puszki wrzucić monetę i potrząsać puszką. Powstały hałas jest nie do wytrzymania. I tak hałasowałoby nadwozie podczas jazdy, gdyby poszczególne blachy nadwozia nie zostały pokryte specjalnymi matami lub masami wyciszającymi i wygłuszającymi.
Mamy tu do czynienia z dwoma rodzajami powstawania hałasu.
- Pierwszy to przenoszenie się hałasu przez metalowe ścianki nadwozia z zewnątrz do wnętrza pojazdu. Takie hałasy potęgowane są przez pudła rezonansowe powstałe podczas produkcji nadwozia, czyli profile zamknięte. Takie ograniczanie hałasu nazywane jest wyciszaniem nadwozia.
- Drugi to generowanie dodatkowego hałasu w blachach poszycia zewnętrznego po wprowadzeniu w nie działania zewnętrznego, czyli uderzenia kamienia o podwozie czy drgania dużych powierzchni blach poszycia zewnętrznego drzwi, tylnego błotnika i dachu. Taki rodzaj ograniczania hałasu to wygłuszanie nadwozia.
Każdy z elementów nadwozia izolowany jest przed przedostawaniem się hałasu z jednej strony elementu na stronę drugą oraz ograniczeniem generowania dodatkowych fal akustycznych. O ograniczeniu wpływu na hałas w pojeździe pudeł rezonansowych pisałem już w poprzednich artykułach.
Do izolacji stosowane były do niedawna najczęściej maty, a obecnie wykorzystywane są coraz częściej specjalne masy natryskowe. Należy tu zaznaczyć, że także wykładziny dekoracyjne wnętrza pojazdu spełniają rolę wyciszającą. Są to dywaniki w kabinie pasażerskiej, wykładziny wewnętrzne drzwi, słupków, bagażnika oraz podsufitka (fot. 1). Również wkładki z gąbki montowane w dolnych częściach słupków B (fot. 2).
Rolę tłumiącą hałas spełniają także masy antykorozyjne nakładane na podwozie pojazdu, szczególnie w nadkolach oraz plastikowe nadkola.
Maty
Maty tłumiące i tłumiąco-wygłuszające stosowane są od dawna. Tłumiące drgania maty lub płyty przyklejane są na boczne, wewnętrzne elementy blach nadwoziowych, jak poszycie zewnętrzne drzwi (fot. 3), błotniki tylne, dach itp. Potocznie zwane są matami lub płytami Kellera.
Na elementy podłogi nadwozia w kabinie pasażerskiej i w bagażniku przyklejane są maty tłumiąco-głuszące (fot. 4). I tu uwaga – mata tłumiąca i mata tłumiąco-wygłuszająca spełniają swoje zadania tylko wtedy, kiedy przylegają do podłoża całą swoją powierzchnią. Jeżeli mata będzie przylegała tylko w kilku miejscach, to nie będzie efektu tłumienia czy głuszenia. Maty tłumiące drgania to samoprzylepne płyty na bazie mieszaniny produktów bitumicznych i tworzyw sztucznych. Po stronie zewnętrznej maty te pokryte są cienką folią aluminiową, dzięki czemu wykazują dużą stabilność i odporność na wysokie temperatury. Poza tym są to maty przyklejane często na powierzchnie widoczne lub łatwo dostępne i powłoka aluminiowa pozwala na ich polakierowanie lub nie pozwala na zabrudzenia produktami bitumicznymi. Relatywnie ciężki materiał bitumiczny jest skuteczny w tłumieniu dźwięku pochodzącego z materiału nadwozia, czyli z blachy oraz zmniejsza drgania elementów metalowych i z tworzyw sztucznych. Najczęściej stosowane są maty o wymiarach 500 x 300 mm i grubości 2 mm. Strona do mocowania wyposażona jest w samoprzylepne podłoże, niezawierające rozpuszczalników na bazie specjalnych akrylowych kopolimerów. Strona klejąca jest pokryta materiałem (folią polietylenową) chroniącym ją podczas transportu i przed wpływami magazynowania.
Często spotykam się z wieloma uwagami blacharzy, że maty „nie trzymają”, że same odpadają. I tu trzeba powiedzieć, że o tym, czy mata będzie się trzymała, decyduje odpowiednie przygotowanie powierzchni oraz sposób jej przyklejenia do podłoża. Powierzchnie do klejenia muszą być czyste, odtłuszczone i suche. Do oczyszczenia należy użyć zmywacza benzynowego.
Na widocznej powierzchni maty można zaznaczyć nożem dowolny kształt o dowolnej, wymaganej wielkości. Po tej wyrytej linii można płytę złamać, ponieważ płyta w temperaturze pokojowej jest krucha. Elastyczna staje się dopiero po podgrzaniu. I to jest cała tajemnica prawidłowego nakładania mat. Po odtłuszczeniu powierzchni oraz przygotowaniu kształtu maty konieczne jest podgrzanie zarówno maty, jak i powierzchni blachy do temperatury 30-40ºC. Ze strony spodniej zdejmuje się polietylenową folię ochronną i powierzchnią z naniesionym klejem dociska do podłoża. Należy przy tym zwrócić uwagę na równomierny i mocny docisk. Jeżeli okaże się, że klej na macie nie trzyma odpowiednio mocno, można matę przykleić klejem kontaktowym na bazie kauczuku chloroprenowego. Maty tłumiąco-głuszące to także samoprzylepne maty, ale wykonane tylko z produktów bitumicznych ze specjalnym wypełniaczem. Przez dobrą giętkość już w temperaturze pokojowej mata dopasowuje się do wytłoczeń blach nadwoziowych. Przez podgrzanie maty do temperatury około 30-40ºC można dopasować ją do głębokich i ciasnych zagłębień. Przy głębokich wytłoczeniach jednocześnie z podgrzewaniem stosuje się dociskanie maty do podłoża przy pomocy np. trzonka pilnika. Główne zastosowanie maty to tłumienie drgań i hałasu pochodzących od podłogi pojazdu w kabinie pasażerskiej i w bagażniku. Najczęściej spotykane wymiary mat podłogowych to 500 x 500 lub 1000 x 500 mm. Grubość to około 3 mm.
Podobnie jak przy matach tłumiących powierzchnie do klejenia muszą być czyste, odtłuszczone i suche. Niektórzy producenci samochodów stosują zamiast mat bitumicznych maty filcowe, przyklejane bezpośrednio na wewnętrzne powierzchnie w kabinie pasażerskiej lub w bagażniku (fot. 5).
Masy
W warunkach fabrycznych nakładane są coraz częściej szerokie ściegi strukturalne (fot. 6), zarówno na powierzchniach podłogi, jak i na powierzchniach drzwi. Jeżeli w zakładzie produkcyjnym nałożenie takich strukturalnych powierzchni mas nie jest problemem, ponieważ wykonywane są one przez odpowiednio zaprogramowane roboty, to w warsztacie dostępnymi narzędziami takich ściegów już się nie nałoży.
Dlatego też firmy produkujące chemię warsztatową musiały podjąć wyzwanie opracowania odpowiedniego materiału i narzędzi do jego aplikacji. Odpowiedni materiał znany jest już od lat. Jest nim masa MS (modyfikowane silany).
Utwardzają się przez wilgoć zawartą w powietrzu do postaci elastyczno-gumowej. Tworzenie się „skórki” na powierzchni masy i czas wskrośnego utwardzania się zależą od wilgoci i temperatury powietrza oraz od grubości nałożonego ściegu. Przez podwyższenie temperatury i wilgotności można ten czas skrócić; niskie temperatury, a także mała wilgotność wpływają natomiast opóźniająco.
Masy MS charakteryzują się następującymi właściwościami:
- mogą być nakładane natryskowo, odwzorowując oryginalne struktur,
- nie zawierają rozpuszczalników, izocyjanianów, silikonów i PCW,
- mają bardzo dobrą przyczepność do metali, podkładów gruntujących i lakierów,
- mogą być lakierowane dostępnymi w handlu lakierami, także zawierającymi alkohol,
- utwardzają się reaktywnie,
- mają dobrą odporność na działanie promieni UV,
- mają bardzo dobre właściwości tłumiące drgania i hałas.
Powierzchnie uszczelniane i zabezpieczane muszą być suche i wolne od kurzu, tłuszczu i piasku, jak również od pozostałych elementów zmniejszających przyczepność. W celu poprawienia przyczepności masy wymagane jest przeszlifowanie powierzchni pokrywanej masą. Gdy powierzchnie uszczelniane lub zabezpieczane zostaną polakierowane dopiero po wyschnięciu masy, to przygotowawcze prace lakiernicze należy przeprowadzić tak samo jak przy lakierowaniu tworzyw sztucznych.
Do nakładania mas MS w celu odwzorowania fabrycznej struktury potrzebny jest specjalny pistolet o nazwie Power Liner II (fot. 7).
Te wszystkie maty i masy mają wpływ na komfort jazdy samochodem. Jeżeli podczas naprawy blacharsko-lakierniczej któryś z tych elementów zostanie wyrzucony i nie zostanie zamontowany nowy, to w najbliższym czasie klient pojawia się ponownie. I nie po to, żeby zlecić naprawę, tylko z uwagami, że ten samochód po naprawie jest bardzo głośny, że wszystko w nim słychać itp. A to oznacza tylko dodatkową pracę, niepotrzebne zdenerwowanie i stracony czas.
Wiesław Wielgołaski
Komentarze (0)