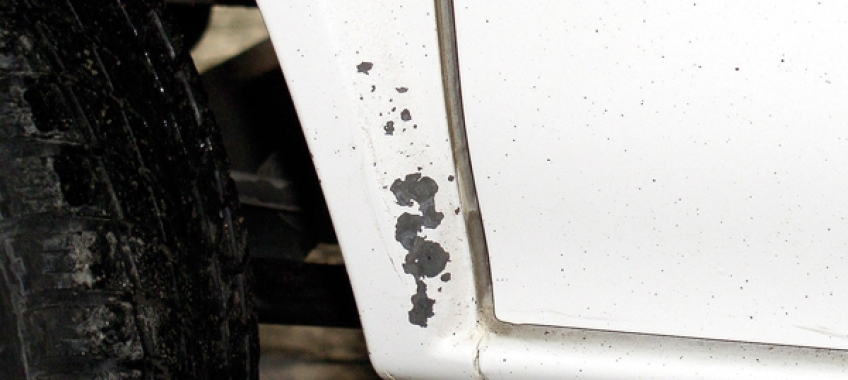
W praktyce uszkodzenia te, to odpryski lakieru, lakieru i podkładu lub całej powłoki ochronnej, łącznie z warstwą cynkową. Są to drobne odpryski, ale często występujące w bardzo dużej ilości. Charakterystyczne miejsca ich występowania to dolne elementy nadwozia, jak błotniki i progi, ale również pokrywa silnika w części przedniej i dach w pojazdach podwyższanych. Odpryski lakieru są zależne przede wszystkim od jakości dróg i ich czystości. Również od sposobu jazdy, szczególnie po drogach polnych, przez które często prowadzą objazdy, jak również przez budowane lub remontowane odcinki dróg. Można zatem powiedzieć, że tak naprawdę odprysków lakieru nie da się uniknąć. Konieczne jest jednak takie zabezpieczenie blach nadwozia, żeby odpryśnięty lakier, a właściwie cała powłoka lakierowa, nie odsłaniała czystej powierzchni stali. W takich punktach bardzo szybko pojawiają się ogniska korozji. Chodzi zatem o takie zabezpieczenie antykorozyjne nadwozia, czyli o taką warstwę ochronną pod lakierem, która nie odpryśnie lub nie ulegnie uszkodzeniu po uderzeniu drobnych kamieni czy piasku. Warstwa, która nie jest tak twarda jak lakier, ale na tyle miękka i sprężysta, żeby odbijać uderzenia tych drobnych zanieczyszczeń znajdujących się na drogach. Jeżeli pod lakierem nałożona jest taka warstwa, to zjawisko wypiaskowania warstwy ochronnej nie wystąpi. Może co najwyżej odprysnąć powłoka nawierzchniowa, odsłaniając warstwę odporną na uderzenia takich uszkodzeń (fot. 2). Ale nie nastąpi całkowite jej uszkodzenie i nie powstaną ogniska korozji. W związku z tym, że jest to warstwa gruba (do 1-2 mm), nie stosuje się jej na całym nadwoziu. Takie nadwozie nie wyglądałoby zbyt elegancko. Bierze się zatem pod uwagę tylko te obszary nadwozia, które są najczęściej i najbardziej narażone na mechaniczne działania zabrudzeń drogowych. Ochronę przed uderzeniami kamieni stosuje się na dolnych bocznych powierzchniach nadwozia: progach, dolnych częściach błotników i drzwi bocznych. Niektórzy producenci samochodów stosują także taką ochronę na przednich powierzchniach pokrywy silnika. Ze względu na estetykę nadwozia, jak również z praktycznej strony, stosowane są obecnie nakładki z tworzyw sztucznych na progi i dolne części błotników przednich oraz folie ochronne na krawędzie tylnych błotników od strony wnęki drzwi (fot. 3). Takie rozwiązania są skuteczne, ale trudno okleić samochód z każdej strony folią ochronną, która mimo swojej przezroczystości nie wygląda na większych powierzchniach zbyt estetycznie. Lepszym i skuteczniejszym rozwiązaniem jest natryśnięcie specjalnej masy (tzw. „baranka”) i pokrycie go lakierem nawierzchniowym. Sprawdzają się w tym przypadku masy strukturalne na bazie żywic syntetycznych, które z jednej strony są twarde i odporne na ścieranie, a z drugiej strony na tyle elastyczne, że nie odpryskują po uderzeniu kamienia. Oczywiście można by tu zastosować także zwykły, kauczukowy „baranek” do zabezpieczania podwozia przed korozją, ale nie można z niego uzyskać odpowiedniej i drobnej struktury, takiej jaka została nałożona podczas procesu produkcyjnego. W praktyce warsztatowej taki „baranek” nakładany jest różnymi materiałami i sposobami, które poza efektami wizualnymi nie mają nic wspólnego z ochroną przed uderzeniami kamieni. Często zdarza się, że wykonywany jest przy użyciu szpachlówki natryskowej. Podobno wygląda nieźle, ale na pewno nie spełnia swojego zadania.
Masy do ochrony przed uderzeniami kamieni oferowane są na rynku polskim zarówno na bazie rozpuszczalników organicznych, jak i wodorozcieńczalne. Te na bazie „wodnej” mają kilkakrotnie większą odporność na ścieranie i wypiaskowanie. Różnica widoczna jest także w systemie nakładania. Masy rozpuszczalnikowe muszą wyschnąć, żeby mogły być polakierowane lakierem na bazie „wodnej”. I tu może powstać problem z przyczepnością lakieru bazowego wodorozcieńczalnego. Jeżeli masa rozpuszczalnikowa nie zostanie dokładnie wysuszona (przed upływem co najmniej 2 godzin), to z połączenia z lakierem wodnym może wyjść tzw. „kaszana”. Jeżeli masa zostanie przesuszona (powyżej 6 godzin), to baza „wodna” nie będzie miała przyczepności (fot. 4). W takich przypadkach konieczne jest zastosowanie podkładu na tworzywa sztuczne lub należy po prostu zmatować jej powierzchnię. Jeżeli zostanie zachowany odpowiedni czas suszenia (od 2-6 godzin), nie powinno być żadnego problemu z przyczepnością bazy do masy.
Masy rozpuszczalnikowe
Zaletą mas na bazie żywic syntetycznych jest to, że mogą być nakładane pistoletem lakierniczym (z dyszą 2,0-2,5 mm), mogą być lakierowane w systemie „mokre na mokre”, jak również mogą być barwione lakierem nawierzchniowym. Ta ostatnia właściwość jest bardzo ważna, ponieważ w przypadku odpryśnięcia lakieru pod wpływem uderzenia kamienia powstaje jasna lub ciemna plama masy odpornej na uderzenia kamieni. Jeżeli taką masę zabarwimy przed nałożeniem lakierem bazowym, to po odpryśnięciu lakieru będzie widoczna tylko trochę jaśniejsza od powłoki lakieru nawierzchniowego plamka – na tyle niezauważalna, że nawet uczulony na wszelkie uszkodzenia powłoki lakierowej właściciel danego samochodu nie będzie przyjeżdżał od razu do warsztatu i reklamował wykonanej wcześniej naprawy blacharsko-lakierniczej. Przy zastosowaniu masy rozpuszczalnikowej niemożliwe jest także barwienie jej lakierem bazowym wodorozcieńczalnym i w konsekwencji niewykorzystanie jednej z jej zalet, czyli nierzucania się w oczy po odpryśnięciu lakieru. Po wyschnięciu masa tworzy warstwę odporną na korozję, odporną na ścieranie i uderzenia kamieni oraz ma wysoką odporność na starzenie. Wyschnięty materiał ma dobrą przyczepność do zagruntowanej i polakierowanej blachy, jak również do tworzyw sztucznych, które pokryte zostały wcześniej podkładem lub wypełniaczem.
Masa rozpuszczalnikowa po całkowitym wyschnięciu może być pokrywana lakierami wszystkich systemów lakierniczych dostępnych w handlu. Możliwe jest bezproblemowe suszenie w piecu części polakierowanych, jak i nielakierowanych. Masa w kolorze jasnym może być barwiona na każdy kolor przez mieszanie z oryginalnym lakierem samochodowym (bazą lub akrylem), ale tylko w ilości do 30% lakieru (w proporcji objętościowej). Utwardzona warstwa masy daje się dobrze szlifować. A to oznacza, że masy odporne na uderzenia kamieni mogą być stosowane zamiast podkładów wypełniających. Można też zeszlifować zewnętrzną powierzchnię masy z nieudaną strukturą i nałożyć ponownie strukturę właściwą. Masy rozpuszczalnikowe (np. Terotex Super 3000) mogą być także nakładane na dolne części bocznych elementów nadwozia w celu zabezpieczenia ich przed uderzeniami kamieni, korozją spowodowaną solą i wilgocią, jako warstwa zewnętrzna, nielakierowana. Są bowiem odporne czasowo na działanie benzyn i różnego rodzaju zmywaczy (fot. 5). Powierzchnie zabezpieczane masą odporną na uderzenia kamieni należy dobrze oczyścić i usunąć z nich rdzę. Powierzchnie te muszą być suche, wolne od tłuszczu, brudu i kurzu. Elementy niepokrywane należy okleić papierem ochronnym. Przyczepność masy można zwiększyć przez przeszlifowanie pokrywanych powierzchni włókniną szlifierską. Jeżeli lakierowanie wykonywane jest dopiero po całkowitym utwardzeniu się masy, przygotowanie powierzchni wykonuje się jak przy lakierowaniu tworzyw sztucznych. W celu dobrej ochrony przed korozją i uzyskania dobrej przyczepności wskazane jest nakładanie masy na fosforanowane i zagruntowane powierzchnie blach nowych elementów nadwozia lub na powierzchnie pokryte podkładem wypełniającym. Najlepiej jak powierzchnię pod masę przygotuje się tak samo jak pod lakier nawierzchniowy. Ważne jest, aby warstwy podkładów gruntujących i wypełniających były suche, jeżeli będzie na nie nakładana masa. Masa oferowana jest najczęściej w wysokich, 1-litrowych puszkach przystosowanych do nakręcania na nie zwykłego pistoletu podciśnieniowego UBS. Potrzebne ciśnienie powietrza do nakładania masy wynosi 4-5 barów. Delikatną strukturę powierzchni można osiągnąć, używając pistoletu lakierniczego lub pistoletu ciśnieniowego dla puszek wysokich, jak również pistoletu podciśnieniowego z regulowaną dyszą natryskową (fot. 6). Przed nałożeniem właściwej struktury zaleca się wykonanie próbnych natrysków i odpowiedniego ustawienia dyszy pistoletu. Po nałożeniu masy rozpuszczalnikowej możliwe jest w krótkim czasie (7-20 minut) lakierowanie wszystkimi dostępnymi w handlu lakierami 2K, ale tylko rozpuszczalnikowymi. Takie lakierowanie w systemie „mokre na mokre” może być suszone w temperaturze ok. 60°C, bez obawy powstawania pęcherzy i rys na powierzchni lakieru. Masę należy lakierować zasadniczo do 6 godzin po nałożeniu, żeby lakier mógł się połączyć z zewnętrzną warstwą masy przed całkowitym jej utwardzeniem.
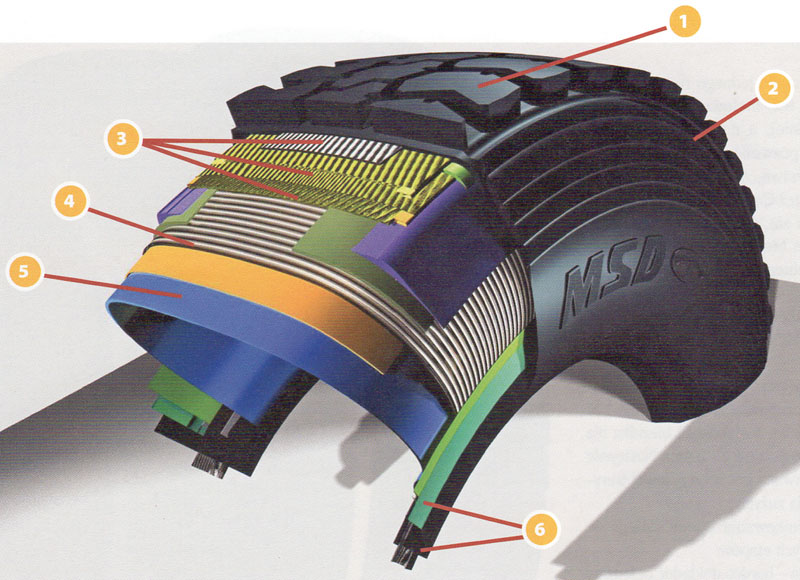
Mas strukturalnych nie powinno się nakładać w jednym cyklu roboczym. Dla uzyskania grubej warstwy (1-2 mm) prawidłowe jest nałożenie do 3-4 warstw, z czasem schnięcia poszczególnych warstw około 10-15 minut. Jeżeli masa rozpuszczalnikowa schnie dłużej niż 6 godz., wzmacnia się warstwa zewnętrzna i zachowuje się jak tworzywo sztuczne, tzn. przed lakierowaniem należy pokryć ją cienką warstwą podkładu na tworzywa sztuczne. Masy rozpuszczalnikowe zawierają mieszaninę bardzo lotnych rozpuszczalników, które rozpuszczają różne podłoża, np. warstwę cynku nałożoną z pojemnika spray, masy uszczelniające: poliuretanowe i polimerowe. Masy nie można nanosić także bezpośrednio na powierzchnie, które pokryte zostały wcześniej odrdzewiaczem do blach (np. Rostumwandler Emulsion czy Rost Killer), ponieważ wytworzona przez odrdzewiacz powłoka rozpuszcza się i proces odrdzewiania zostaje przerwany. Dlatego przed nałożeniem masy zaleca się wykonanie odpowiedniego gruntowania (natrysk podkładu 1K lub 2K ).
Masy wodorozcieńczalne
Dla warsztatów stosujących lakiery „wodne” polecam wykonywanie struktury „baranka” masami na bazie dyspersji wodnej. Przyspiesza to wydatnie proces lakierowania, ponieważ są to masy, które można lakierować w systemie „mokre na mokre”. Poza tym jak wspomniałem wcześniej, masę na bazie „wodnej” można barwić lakierem wodorozcieńczalnym (fot. 7). Najważniejszą właściwością mas wodorozcieńczalnych (np. Terotex Super 3000 Aqua) jest to, że są one prawie bezwonne. Podczas natrysku nie czuje się żadnych rozpuszczalników. Preparaty na bazie wodnej są przejrzyste, słabo kryjące. Suszenie wykonuje się w temperaturze pokojowej, ale może być przyspieszone, np. w kabinie, w temperaturze do 60°C. Masa „wodna” ma bardzo dobrą przyczepność do blach zagruntowanych podkładem kataforetycznym. Podobnie jak przy masach rozpuszczalnikowych także i masy „wodne” mogą być mieszane z lakierem wodorozcieńczalnym w ilości do 30%. Jeżeli konieczne jest nałożenie na naprawianą powierzchnię podkładu wypełniającego lub szpachlówki natryskowej, to należy nałożyć je przed natryśnięciem masy. Do natrysku stosuje się pistolety lakiernicze przystosowane do wyrobów wodorozcieńczalnych. Ciśnienie powietrza 2-5 barów (fot. 8). W celu zapobieżenia wtrąceniom w nakładanej, drobnej strukturze powierzchni masy oraz przypadkowym zabrudzeniom wymagane jest przelewanie gotowej masy do pistoletu przez sitko lakiernicze (fot. 9). Masy wodorozcieńczalne mogą być nakładane na wszystkie poliuretanowe i polimerowe masy uszczelniające, stosowane do uszczelniania połączeń blach nadwozia samochodu. Odwzorowanie oryginalnej struktury „baranka” nie jest łatwe. Wymaga dużej wiedzy i umiejętności. Zależy nie tylko od nakładanej masy i jej jakości. Duże znaczenie ma odpowiedni pistolet (czyli odpowiednia dysza) oraz ciśnienie powietrza natryskowego. Dlatego też konieczne jest stosowanie manometru i zaworu regulacyjnego zamontowanego przy pistolecie.
Wiesław Wielgołaski
Komentarze (0)