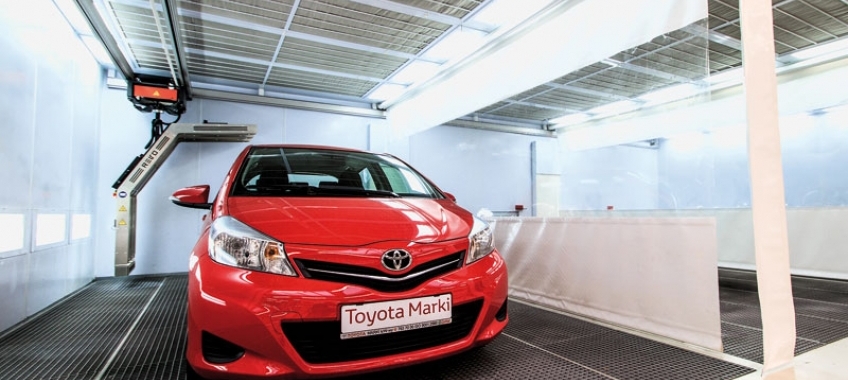
– BAT uzupełnione o BHP. Źródłem sukcesu ekonomicznego firmy jest wdrożenie do cyklu produkcyjnego najnowocześniejszych rozwiązań gwarantujących wysoką jakość przy możliwie niskich kosztach. Oczekuje się więc sytuacji, aby rosnące wymagania stawiane urządzeniom w zakresie nanoszenia powłok szły w parze z wdrożeniem inwestycji ukierunkowanych na ochronę zdrowia pracowników zaangażowanych w przygotowanie powierzchni.
O innowacyjności rozwiązań mówimy wtedy, gdy bardzo dobrym warunkom BHP towarzyszy eliminacja zagrożenia u źródła. W żadnej innej dziedzinie definicja jakości nie jest tak szeroka, jak przy obróbce powierzchni. Ostatecznie bowiem jakość zawsze oceniana jest z perspektywy użytkownika, zaś ocena ta zależy od tego, jakie zadanie postawiono do wykonania. Obojętne, czy powierzone zadanie polega na szybkim i intensywnym zdzieraniu starej powłoki, czy celem jest przygotowanie delikatnej powierzchni pod perfekcyjne wykończenie, czy też usunięcie wad lakierniczych w procesie polerowania – centralny odciąg pyłów stanowi gwarancję, że zagrożenia dla układu oddechowego pracowników eliminujemy u źródła, a środki ochrony osobistej (np. maski przeciwpyłowe) stanowią uzupełnienie kompleksowego podejścia do zagadnień zdrowia i ekologii.
Idea systemu usuwania zanieczyszczeń u źródła jest szczególnie mocno akcentowana w przypadku produktów Festool związanych ze szlifowaniem i polerowaniem. Przykładem może być tutaj zintegrowane odsysanie pyłów powstających w procesie szlifowania, a wzorcową instalacją tego typu może pochwalić się dziś serwis blacharsko-lakierniczy Toyota Marki w Warszawie. Dlaczego?
- Poczynione w roku ubiegłym inwestycje zostały potwierdzone pozytywną oceną w zakresie proekologicznych technologii – wyjaśnia Mariusz Dylewski, kierownik serwisu blacharsko-lakierniczego punktu ASO Toyota Marki. - W opinii Zespołu Rzeczoznawców Techniki Samochodowej i Ruchu Drogowego Automobilklubu Nowy Świat, akredytowanych przy DEKRA, nasze rozwiązania wykazują znamiona innowacyjności oraz spełniają normatywy BAT (ang. Best Available Techniques), czyli najlepszych dostępnych technologii, co też pozwoliło nam skutecznie ubiegać się o dofinansowanie w ramach Regionalnego Programu Operacyjnego Województwa Mazowieckiego.
Wdrożone rozwiązania konstrukcyjne zdecydowały o zmniejszeniu poboru energii elektrycznej, ograniczeniu generowania ścieków, podnoszeniu stopnia efektywności i jakości procesów produkcyjnych.
Pokusa wdrożenia najskuteczniejszych rozwiązań w strefie przygotowawczej pojawiła się wraz z decyzją o przebudowie architektonicznej obiektu i wdrożenia technologii lakierowania opartej na wodorozcieńczalnych produktach, mającej na celu ograniczenie emisji LZO do środowiska. Prace adaptacyjne były poważne. Zwiększenie przepustowości stanowisk osiągnięto, usuwając filary, które pierwotnie podtrzymywały konstrukcję dachu. W ich miejsce pojawiły się belki nośne, a lżejszej konstrukcji poszycie wzbogacono o świetliki, które są zamontowane nad głównym korytarzem komunikacyjnym – od bramy sąsiadującej ze strefą rozbrajania karoserii, po wjazd do kabin lakierniczych. Adaptujący obiekt wyburzyli ścianki działowe, które pierwotnie oddzielały strefę przygotowawczą („brudno-mokrą”) od strefy wstępnych prac lakierniczych i suszenia elementów. W sąsiedztwie dwóch kabin lakierniczych z rekuperatorami odzysku ciepła z wydalanego powietrza podczas faz malowania i suszenia, które oddziela od siebie pomieszczenie suszarni do wygrzewania uprzednio zdemontowanych elementów karoserii, powstało nowe pomieszczenie mieszalni i sąsiadująca z nią kabina półotwarta, architektonicznie wydzielona trzema ścianami stałymi i kurtyną.
Ze wspomnianego pomieszczenia można wydzielić aż trzy strefy, które na czas szlifowania oddzielamy od sąsiadującej kurtyną „brudną”, a na czas wygrzewania elementów kurtyną „czystą”. Obojętnie, czy korzystamy z kurtyn, czy też nie, pracownicy obu stref mogą bez przeszkód korzystać z pneumatycznego modułu zasilania EAA DW TURBO/A-EU marki Festool. Moduł ten umieszczono bowiem w kasecie, która po zamknięciu rolety ochronnej licuje się ze ścianą, więc nie stanowi przeszkody dla opuszczania/podnoszenia którejkolwiek z kurtyn. Centralnie wbudowany moduł (pośrodku obu stref) gwarantuje, że mogą z nim współpracować narzędzia pneumatyczne w sąsiadujących ze sobą stanowiskach pracy. W trzeciej strefie znajdziemy system promienników podczerwieni. System Revo to skoncentrowana w jednym urządzeniu najnowsza technologia szybkiego suszenia i utwardzania za pomocą promiennika podczerwonego. Ramię urządzenia porusza się na szynie umocowanej do sufitu strefy i dzięki czujnikom odległości automatycznie dopasowuje się do suszonego elementu karoserii.
W tak zaprojektowanej kabinie półotwartej nie wyklucza się dokonywania procesów lakierniczych na małych powierzchniach. Lakierowania zaprawkowe, bez możliwości suszenia w podwyższonych temperaturach, są możliwe przy użyciu różnego rodzaju lamp lub promienników. Dla komfortu prac niezbędne okazało się wyposażenie takiej w urządzenie nawiewowe z górnym rozprowadzaniem powietrza na stanowiska robocze i układem odsysania zanieczyszczonego powietrza wraz z jego filtrowaniem w celu usunięcia pyłów powstających w procesie szlifowania. Od pozostałej części hali stanowiska te są oddzielone specjalnymi kotarami.
Po przeciwnej stronie kabiny półotwartej znajduje się strefa „brudno-mokra”. Stanowisko przygotowawcze umożliwia wykonanie wstępnych prac lakierniczych przed właściwym lakierowaniem elementów. Są to takie prace, jak np. szlifowanie podkładów i wypełniaczy podczas obróbki powierzchniowej. I tu zainstalowano kotary, więc strefa ta jest przystosowana do wykonywania wszelkich prac naprawczo-remontowych, powodujących zapylenie lub zanieczyszczenie stanowiska pracy na skutek m.in. szlifowania, polerowania, wygładzania, nanoszenia „wypełniaczy”, szpachlówek, podkładów lakierniczych i innych podobnych prac. W strefie tej znajdziemy centralny odzysk powietrza z nawiewem świeżego (powietrza) od dołu, a trzy wysięgniki odsysające ASA 5000 marki Festool wyprowadzono wprost ze ściany, co zapewniło większy zakres działania (zasięg podwójnych ramiom przegubowych wynosi 2 x 2,5 metra) niż w przypadku mocowania ich do filarów.
- Takie rozwiązanie gwarantuje też pełną koncentrację na realizacji powierzonego zadania, bo w każdej chwili potrzebne narzędzie jest natychmiast gotowe do użycia. Odsysanie rozpoczyna się z chwilą uruchomienia narzędzia i ustaje dopiero po jego wyłączeniu. Wszystkie procesy są sterowane centralnie za pomocą zawieszanego modułu zasilania/odsysania EAA w połączeniu z wysięgnikiem odsysającym ASA – wyjaśnia Konrad Marciniak, Dyrektor Sprzedaży BU Automotive, Festool Polska Sp. z o.o.
Lekkie profile aluminiowe wysięgników sprawiają, że operowanie nimi nie wymaga wysiłku, a umocowane moduły są zawsze w zasięgu ręki, dostarczając energię (sprężone powietrze) i zapewniając automatyczne odsysanie. Pneumatyczne narzędzia są połączone z modułem zasilania/odsysania EAA antystatycznymi wężami (3- lub 7-metrowymi IAS 3 light), zaprojektowanymi do współpracy z pneumatycznymi szlifierkami mimośrodowymi LEX 3.
Sercem instalacji jest właśnie turbina odsysająca TURBO II DC-14WP, zaprojektowana do obsługi nawet 14 stanowisk pracy, jakkolwiek w tym przypadku jest ich 10. Stale wysoka, a jednocześnie niezbędna moc ssania jest dynamicznie regulowana przez falownik na podstawie aktualnego zapotrzebowania (pobór mocy przy 50 Hz to 7500 W). Nad wydajnością układu czuwa system automatycznego oczyszczania filtra. Urządzenie gwarantuje odsysanie pyłów klasy M.
Rafał Dobrowolski
R. Dobrowolski i Toyota Marki
Komentarze (0)