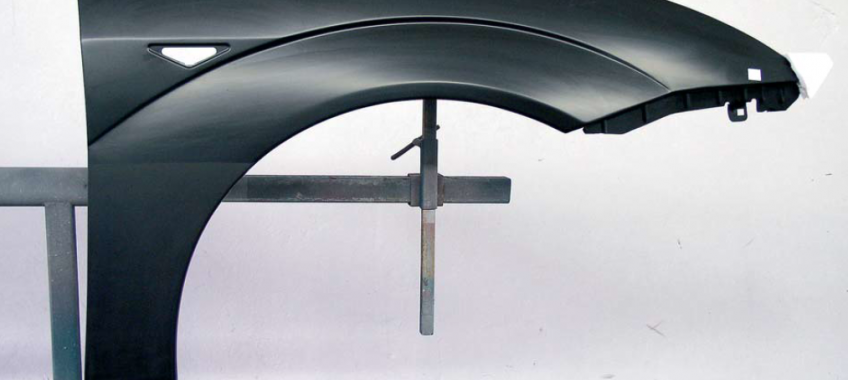
Nowe elementy nadwozia, wymieniane podczas naprawy blacharskiej, pokryte są podkładem kataforetycznym. Najczęściej jest to podkład w kolorze czarnym. Niestety, ale nie przewodzi on prądu i dlatego zarówno przed zgrzewaniem, jak i przed spawaniem lub lutospawaniem musi zostać usunięty (fot. 1).
Dla przypomnienia – podkład kataforetyczny to podkład nakładany techniką wykorzystującą zjawisko elektroforezy, czyli rozdzielania mieszaniny substancji chemicznych pod wpływem pola elektrycznego. Podkłady wykorzystywane do malowania elektroforetycznego są farbami wodorozcieńczalnymi. Proces ten ma podobny przebieg do procesu nakładania powłok galwanicznych. Przedmiot malowany podkładem zanurzany jest w roztworze podkładu i podłączany do odpowiedniej elektrody – dodatniej lub ujemnej, w zależności od składu stosowanej farby.
Przed przystąpieniem do malowania przedmiot musi zostać odpowiednio przygotowany. Przygotowanie polega na usunięciu śladów korozji oraz nadania mu odpowiedniej chropowatości w celu zapewnienia przyczepności powłoki. Następnie przedmiot poddaje się odtłuszczaniu. Odtłuszczenie przeprowadza się przez zanurzenie przedmiotu w rozpuszczalnikach organicznych lub odpowiednich kąpielach odtłuszczających zawierających roztwory alkaliczne. Celem tej operacji jest zapewnienie odpowiedniej zwilżalności pokrywanego przedmiotu.
W przemyśle samochodowym przed nałożeniem powłoki podkładowej metodą elektroforezy następuje zazwyczaj nałożenie powłoki fosforanowej. Fosforanowanie służy do przygotowywania powierzchni metali (stal, żeliwo szare, cynk i aluminium) przed lakierowaniem. Celem tego procesu jest polepszenie przyczepności lakieru oraz, w połączeniu z lakierowaniem, zwiększenie ochrony antykorozyjnej powierzchni metalu.
Przed zgrzewaniem lub spawaniem podkład kataforetyczny usuwany jest po obydwu stronach blachy, a w niektórych przypadkach usuwany jest także na całym obwodzie nowego elementu (fot. 2). Nie wszyscy wiedzą, w których miejscach będą punkty zgrzein lub spawania, dlatego usuwają podkład na powierzchni całego obwodu elementu.
Te oczyszczone z podkładu kataforetycznego miejsca powinny być jak najszybciej zabezpieczone antykorozyjnie – podkładem cynkowym lub cynkowo-aluminiowym, które przewodzą prąd. Mogą być także zastosowane specjalne pasty przeznaczone do połączeń spawanych lub masy uszczelniająco-klejące na bazie MS-ów (modyfikowanych silanów). Chodzi tu o zabezpieczanie antykorozyjne połączeń surowych blach przed ich zgrzewaniem. Dlaczego jest to tak ważne dla żywotności nadwozia, pomoże nam zrozumienie tzw. korozji szczelinowej.
Korozja szczelinowa jest zjawiskiem ściśle związanym ze zgrzeinami. Pomiędzy dwoma ściśle przylegającymi blachami połączonymi zgrzeiną zachodzi specyficzne środowisko, w którym samoistnie powstaje ognisko korozji (fot. 3). Tuż w pobliżu zgrzeiny jest mała szczelina, w której jest mała ilość tlenu. Trochę dalej blachy nie przylegają już tak dokładnie do siebie i szczelina jest większa. W obszarze tym jest duża zawartość tlenu. Pomiędzy tymi obszarami powstaje różnica potencjałów, co przy odrobinie wilgoci prowadzi do powstania mikroogniwa elektrochemicznego.
Dla takiego ogniwa jest tylko kwestią czasu, kiedy powstanie w jego miejscu ognisko korozji. Nawet najlepsze zabezpieczenie antykorozyjne, ocynkowanie i kataforeza blach, nie są w stanie zapobiec temu zjawisku. Dlatego dodatkowo stosuje się zabezpieczenie w postaci mas woskowych.
Podczas prac blacharskich możemy mieć do czynienia z koniecznością tylko zabezpieczenia powierzchni blach, z zabezpieczeniem i jednoczesnym uszczelnieniem połączenia blach, jak również zabezpieczeniem z równoczesnym uszczelnieniem i sklejeniem łączonych blach.
Zabezpieczenie antykorozyjne
Podczas napraw blacharskich musimy zatroszczyć się o jak najlepsze zabezpieczenie antykorozyjne połączonych ze sobą blach. Tym bardziej, że przed zgrzewaniem blachy muszą być oczyszczone z podkładu kataforetycznego. Jeżeli nie zostanie usunięty, to blachy nie zostaną połączone. Jeżeli zeszlifujemy podkład i nie zabezpieczymy odsłoniętych powierzchni blachy, blacha bardzo szybko skoroduje. Dlatego konieczne jest zabezpieczenie tych powierzchni surowej blachy preparatami, które przewodzą prąd elektryczny lub masami, które nie przeszkadzają w wykonaniu prawidłowej zgrzeiny.
Jeżeli połączenie blach musi być tylko zabezpieczone antykorozyjne, miejsca oszlifowane pokrywamy cienką warstwą cynku z pojemnika spray, który umożliwia szybkie użycie i nałożenie cienkiej, równej warstwy. Jest to najczęściej spotykany przypadek, ponieważ dotyczy wszystkich prac wykonywanych przez blacharza. Cynk jest doskonałym materiałem zabezpieczającym antykorozyjnie, odpornym na działanie zewnętrznych czynników atmosferycznych i wysokich temperatur – do około 500oC. Ma także dobrą przewodność elektryczną, co przesądza o jego zastosowaniu do zabezpieczania połączeń zgrzewanych i spawanych (fot. 4).
Innym preparatem chętnie stosowanym przez blacharzy jest pasta cynkowa, która gwarantuje ochronę antykorozyjną dzięki wysokiej zawartości cynku, ok. 95%. Pasta cynkowa to doskonałe połączenie pigmentu z żywicami epoksydowymi. Jej właściwości chemiczno-fizyczne spełniają wszystkie wymagania:
- jest preparatem szybkoschnącym,
- trwale zabezpieczającym przed korozją,
- po wyschnięciu jest elastyczna i odporna na ścieranie,
- tworzy warstwę ochronną o wysokiej odporności na agresywne działanie środowiska,
- jest idealna do spawania i zgrzewania punktowego.
Także pasty na bazie bitumicznej do zabezpieczania powierzchni przed spawaniem lub zgrzewaniem mają bardzo duże uznanie wśród blacharzy (fot. 5).
Zabezpieczenie antykorozyjne i uszczelnienie
Niektóre elementy poszycia zewnętrznego wymagają nie tylko zabezpieczenia antykorozyjnego, ale także idealnego uszczelnienia połączenia z konstrukcją karoserii. Najlepszym przykładem takiego elementu jest poszycie dachu, którego połączenie z karoserią musi być szczególnie szczelne. Samo uszczelnienie tego połączenia po zgrzewaniu lub spawaniu nie zawsze jest wystarczające. Dlatego uszczelnienie musi być wykonane przed zgrzewaniem. Do tego celu stosuje się różnego rodzaju pasty do zgrzewania. Ale najlepszym materiałem do uszczelniania połączeń zgrzewanych przed zgrzewaniem są uszczelniające masy na bazie modyfikowanych silanów, czyli MS-Polimery. Podczas zgrzewania nie wydzielają żadnych szkodliwych substancji. Nie palą się i nie wytwarzają dymu. Nie mają także ujemnego wpływu na prawidłowe połączenie blach.
Zabezpieczenie antykorozyjne, uszczelnienie i sklejenie
Do jednoczesnego sklejenia, zabezpieczenia antykorozyjnego i uszczelnienia stosuje się także masę MS, ale o podwyższonej wytrzymałości na rozrywanie i ścinanie. Stosując masę klejącą, można znacznie ograniczyć ilość punktów zgrzania. Oczywiście dotyczy to elementów poszycia zewnętrznego. Do takich elementów należą: dach, błotnik tylny, błotnik przedni, pas tylny, progi oraz poszycia zewnętrzne drzwi, pokrywy silnika i bagażnika (połączenia obrzeżne).
W nowoczesnych konstrukcjach nadwozi połączenie dachu z nadwoziem wykonywane jest spawaniem laserowym i nie wymaga uszczelniania. Ale w warsztacie technologią zastępczą połączeń laserowych jest klejenie klejami jednoskładnikowymi, wspomagane zgrzewaniem lub spawaniem otworowym albo klejenie klejami dwuskładnikowymi. Najlepszym materiałem do klejenia i jednoczesnego uszczelniania połączeń wspomaganych zgrzewaniem są masy na bazie modyfikowanych silanów, czyli MS-Polimery. Masy MS są masami bez zapachu, rozpuszczalników, izocyjanianów, silikonów i PCW. Po utwardzeniu się są obojętne dla środowiska. Podczas zgrzewania nie wydzielają żadnych szkodliwych substancji, w przeciwieństwie do powszechnie stosowanych mas poliuretanowych. Klejenie daje spoinę ciągłą z jednoczesnym uszczelnieniem i zabezpieczeniem antykorozyjnym. Typowym przykładem takiego zastosowania masy klejącej może być zamocowanie do karoserii poszycia zewnętrznego błotnika tylnego. Zamiast zgrzewania lub spawania może być przyklejony na całym obwodzie. Zgrzewanie można ograniczyć tylko do kilku miejsc w celu utrzymania elementu w odpowiednim położeniu do czasu utwardzenia się masy klejącej. Natomiast w miejscu mocowania błotnika z nadkolem wewnętrznym nie stosuje się ani spawania, ani zgrzewania i dlatego tam konieczne jest zastosowanie takiej masy klejącej (fot. 6).
Technologia klejenia nie wymaga usuwania podkładu kataforetycznego. Powierzchnia klejona wymaga tylko dokładnego oczyszczenia i odtłuszczenia. Zwiększenie przyczepności uzyskuje się przez lekkie przeszlifowanie powierzchni klejonej, czyli tzw. zmatowanie podkładu.
Czynności zabezpieczenia blach przed korozją podczas prac spawalniczych nie widać po naprawie blacharsko-lakierniczej. Ale bardzo szybko brak takiego zabezpieczenia „wychodzi” na zewnątrz, pokazując czerwonordzawym nalotem jakość wykonanej naprawy (fot. 7).
Wiesław Wielgołaski
Komentarze (2)