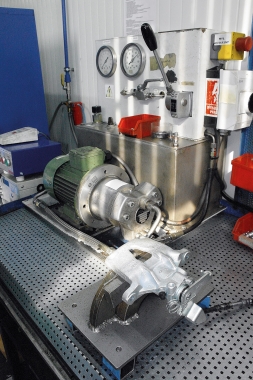
Status dostawcy na pierwszy montaż w branży motoryzacyjnej wymaga spełnienia wielu wymagań producentów samochodów, co wiąże się z reprezentowaniem przez przedsiębiorstwa rozwiniętej kultury organizacji w zakresie systemu zarządzania jakością. Gdy mowa o zaciskach hamulcowych, regeneracja jest bodaj najpiękniejszym przykładem działania wszystkich uczestników rynku.
Dlaczego piszemy akurat o tym elemencie układu hamulcowego? Otóż za wyraźną sugestią Ministerstwa Rozwoju SDCM tworzy podwaliny pod uproszczoną certyfikację części samochodowych. Prace trwają od marca tego roku, a ramowy projekt standardów branżowych powstaje przy współpracy z instytutami badawczymi. Krótko mówiąc – najpewniej czeka nas novum w dziedzinie minimalnych wymogów dla zacisków hamulcowych. Jakkolwiek dziś można tylko domniemywać, czy zacznie obowiązywać standard jakościowy ECE R90, to tym bardziej warto zdiagnozować sytuację panującą w warsztatach samochodowych.
Już rok temu w artykule traktującym o elementach składowych układu hamulcowego sygnalizowano, że branża aftermarket chce podniesienia standardów, by skuteczniej eliminować z rynku pośledniej jakości zaciski. Notabene, te co rusz stanowią propozycję firm z Azji (kazus: Alibaba.com). Krótka sonda wśród warsztatów celujących w naprawach zacisków hamulcowych nie pozostawia wątpliwości – propozycja wymiany uszkodzonego elementu na „przypadkowy produkt z pudełka” jest niezwykle kusząca, ale na szczęście tylko cenowo. Czy wobec tego panująca sytuacja faktycznie wymaga ingerencji instytucji odpowiedzialnych za dopuszczenie do obrotu tylko produktów certyfikowanych?
– W warunkach ostrej konkurencji rynkowej, tak charakterystycznej dla branży motoryzacyjnej, na rynku nie ma praktycznie miejsca dla produktów niskiej jakości – tłumaczy Jarosław Kaflak, area sales manager w dziale Global Aftermarket FTE automotive. – Żaden profesjonalny mechanik nie zdecyduje się na montaż zacisku hamulcowego, jeśli ma jakiekolwiek wątpliwości co do jego jakości i związanego z tym poziomu bezpieczeństwa klienta końcowego. Z punktu widzenia mechanika każda reklamacja to ryzyko utraty klienta, który rozczarowany nieoczekiwanym problemem może zmienić miejsce obsługi samochodu. Dlatego mechanik zrobi wszystko, by uniknąć takiego scenariusza: zainwestuje w szkolenia, by zminimalizować ryzyko błędów montażowych, i wybierze części tylko tego producenta, którego poziomowi jakości ufa. Nie inaczej jest z punktu widzenia producenta części działającego na aftermarkecie. Utrzymanie najwyższej jakości produktów jest dla nas warunkiem koniecznym dla rozwoju firmy. W tym przypadku interes społeczny, jakim jest bezpieczeństwo ruchu drogowego, jest zbieżny z czysto biznesowym, czyli zapewnieniem jak największych zysków naszym udziałowcom.
O ile standard ECE R90 to europejska wytyczna, w oparciu o którą wydaje się homologacje dla klocków i szczęk hamulcowych, to w przypadku zacisków obowiązują normy branżowe (osobne normy dotyczą np. produktu, który powstał w trakcie badań i walidacji wprowadzanego do produkcji nowego układu hamulcowego), a bardziej rygorystyczne dotyczą „tylko” zarządzania jakością (ISO/TS 16949, DIN ISO 9001) oraz zarządzania środowiskowego (DIN ISO 14001).
Zdaniem przedstawiciela FTE automotive, obecna sytuacja, w której zaciski hamulcowe spełniają tylko rygorystyczne wymagania wewnętrzne producenta, jest akceptowalna. Konieczność dodatkowej certyfikacji wywołałaby tylko zamieszanie na rynku i mogłaby się nawet odbić niekorzystnie na dostępności produktu dla klienta. Dotyczy to zwłaszcza sytuacji, w których mówimy o systemie certyfikacji obejmującym tylko jedno państwo, a nie na przykład całą Unię Europejską. Niewykluczone, że Komisja Europejska potraktowałaby to jak wprowadzanie barier w obrocie wewnątrzunijnym, czego zabrania prawo UE.
– W sytuacji gdy wszystkie elementy łańcucha zaopatrzenia warsztatu niezależnego dbają o jakość zacisku hamulcowego, komplikowanie sytuacji prawnej wydaje się niewskazane – kontynuuje J. Kaflak. – Producent zacisku w jego wysokich parametrach szuka przewagi konkurencyjnej. Dystrybutor, który chce współpracować z jak największą liczbą warsztatów, nie może sobie pozwolić na sprzedaż części wątpliwej jakości. Z kolei warsztaty kupują tylko sprawdzone produkty u zaufanych dystrybutorów. Kluczem jest tu wzajemne zaufanie. Mechanizm certyfikacji wydaje się zbędny, tym bardziej że nie ma żadnych danych mówiących o tym, że niskiej jakości zaciski hamulcowe są przyczyną wypadków samochodowych w Polsce. Co więcej, certyfikacja nie rozwiąże problemu obrotu częściami używanymi i niewiadomego pochodzenia, dlatego chcąc realnie poprawić bezpieczeństwo ruchu drogowego, ustawodawca powinien właśnie tam skierować swoją uwagę. Obecne polskie przepisy, które zakazują powtórnego montażu „części mających wpływ na bezpieczeństwo jazdy”, nie są respektowane w stopniu wystarczającym, by zapobiec przypadkom montażu zacisków hamulcowych zdemontowanych „na szrotach”.
Zacisk hamulcowy to jedna z najważniejszych części w układzie hamulcowym każdego pojazdu. Tradycyjne rozwiązania bazują na konstrukcji tłoczka, który podczas hamowania wypycha klocki bezpośrednio do tarczy. W 1991 r. firma ZF TRW jako pierwsza wprowadziła na rynek tylny zacisk hamulcowy z hamulcem ręcznym, z zabudowanym rozpieraczem kulkowo-klinowym. Następnie został on przekształcony w pełny zestaw hamulcowy z zaciskami na przód i tył, przeznaczony do samochodów z segmentu C, zapewniając tym samym bezpieczniejsze użytkowanie pojazdów. Technologia ta nadal dominuje wśród producentów tylnych zacisków hamulcowych na całym świecie.
Starzejący się park samochodowy wymaga dostępności części na długo po zaprzestaniu produkcji poszczególnych typów pojazdów. Fabryczna regeneracja części zamiennych jest doskonałą alternatywą dla nowych części z punktu widzenia wszystkich zainteresowanych stron: producentów pojazdów i części, dystrybutorów, właścicieli warsztatów oraz użytkowników końcowych. Jedynym sposobem na zapewnienie części zamiennych do starszych pojazdów i utrzymanie ich na drogach jest regeneracja (przykładowo, pozyskiwanie zużytych elementów i ich regeneracja umożliwiają TRW zapewnianie klientom części przez maksymalnie 15 lat od zakończenia produkcji). Z kolei firma Lauber Sp. z o.o. jako jedna z pierwszych w Polsce i Europie Środkowo-Wschodniej rozpoczęła regenerację części samochodowych już w 1994 roku. Argumentów na rzecz zasobooszczędnej gospodarki jest wiele.
– Nieustanne wprowadzanie na rynek nowych modeli aut oraz zastosowanie nowoczesnych technologii układów hamulcowych powoduje rozszerzenie asortymentu zacisków hamulcowych – dowodzi Rafał Krupiński, menedżer ds. klientów kluczowych w firmie Lauber. – Wychodząc naprzeciw oczekiwaniom klientów dotyczącym powiększenia katalogu produktów regenerowanych, w ciągu ostatniego miesiąca firma Lauber wprowadziła do oferty handlowej regenerowane zaciski hamulcowe do aut osobowych i dostawczych wyprodukowanych po roku 2006. W niedługim czasie pojawi się również oferta dla aut po roku 2010. W związku z dużym zainteresowaniem i licznymi pytaniami wdrożyliśmy również program regeneracji elektrycznego zacisku hamulca postojowego z własnym silnikiem elektrycznym. Dotyczy to głównie systemu stosowanego w autach marek VW i Audi – tak pierwszych, jak i najnowszych modeli. W odróżnieniu od konwencjonalnego zacisku hamulcowego jest to produkt, którego regeneracja wymaga sporych nakładów pracy, materiałów oraz posiadania właściwej technologii oraz urządzeń diagnostycznych. Pomimo tego udało się nam zaoferować klientowi towar w interesującej cenie, będący alternatywą dla produktu nowego.
Do regeneracji zacisków w firmie Lauber wykorzystywane są podzespoły i części zamienne wiodących światowych producentów. Regeneracja przemysłowa przebiega z zachowaniem norm i technologii produkcji, maszyn i urządzeń służących do właściwej regeneracji. Dwuetapowy proces kontroli jakości zapewnia wysoką klasę produktów, skoro firma udziela na nie 25-miesięcznej gwarancji.
Również w przypadku zacisków hamulcowych regenerowanych przez FTE automotive kluczem do sukcesu okazał się rygorystyczny system kontroli jakości. Do specjalnego zakładu produkcyjnego trafiają zużyte zaciski hamulcowe skupowane przez lokalnych dystrybutorów FTE. Każdy z nich jest szczegółowo oglądany przed skierowaniem go do magazynu surowców, ponieważ do procesu regeneracji kwalifikowane są wyłącznie zaciski pochodzące z pierwszego montażu. Następnie są one demontowane i oczyszczane tak, by wykryć ich uszkodzenia. Procedury FTE Automotive są jednoznaczne: jakiekolwiek ubytki na korpusie zacisku są dyskwalifikujące, z tak uszkodzonego zacisku można odzyskać jedynie surowiec, ale nie zostanie on wykorzystany w całości. Pozostałe części są starannie kontrolowane, piaskowane na mokro, malowane, a w przypadku korpusów – także galwanizowane. Czym wyróżniają się produkty fabrycznej regeneracji FTE na tle konkurencji?
– Jedynym elementem odzyskanego zacisku hamulcowego, który nigdy nie zostaje powtórnie wykorzystany, jest tłoczek – podkreśla J. Kaflak. – Ten element ruchomy zacisku podlega największemu zużyciu w czasie eksploatacji, dlatego dla bezpieczeństwa użytkowników zawsze stosujemy nowe tłoczki, które gwarantują pełną szczelność układu hamulcowego.
Odzyskane elementy służą następnie do starannego montażu fabrycznie regenerowanych zacisków. Cały proces demontażu, a następnie ponownego montażu odbywa się ręcznie, ponieważ dzięki temu możliwe jest przeprowadzenie kontroli jakości na każdym z etapów procesu. Każdy gotowy zacisk przechodzi test szczelności, podczas którego zostaje napełniony płynem hamulcowym pod ciśnieniem 200 barów, a następnie pompa podająca płyn wprowadza pulsację, tak by zasymulować warunki ekstremalnego hamowania. Dodatkowo, od 5% do 10% zacisków z wyprodukowanej partii danej referencji jest rozbieranych, a ich korpusy rozcinane, by upewnić się, że w czasie regeneracji nie został popełniony żaden błąd, a zaciski są całkowicie sprawne.
– Tak ostry reżim kontroli jakości zaowocował niższym poziomem reklamacji w przypadku zacisków fabrycznie regenerowanych niż w przypadku nowych produktów – dodaje Jarosław Kaflak z FTE Automotive. – Dowód? Wszystkie zaciski hamulcowe FTE Automotive – zarówno nowe, jak i fabrycznie regenerowane – są objęte identyczną, 24-miesięczną gwarancją.
Zaledwie pięć lat temu firma wyprodukowała ok. 20 tys. sztuk zacisków regenerowanych fabrycznie. W 2016 roku skala produkcji wyniesie 1,2 mln szt. To chyba najlepszy dowód, że branża nie potrzebuje nowych regulacji. Niewidzialna ręka rynku skutecznie ignoruje „przypadkowy produkt z pudełka”, a uzasadnione zaufanie zyskuje produkt będący efektem regeneracji przemysłowej.
Rafał Dobrowolski
Fot. FTE, Lauber, TRW, Brembo
Komentarze (0)