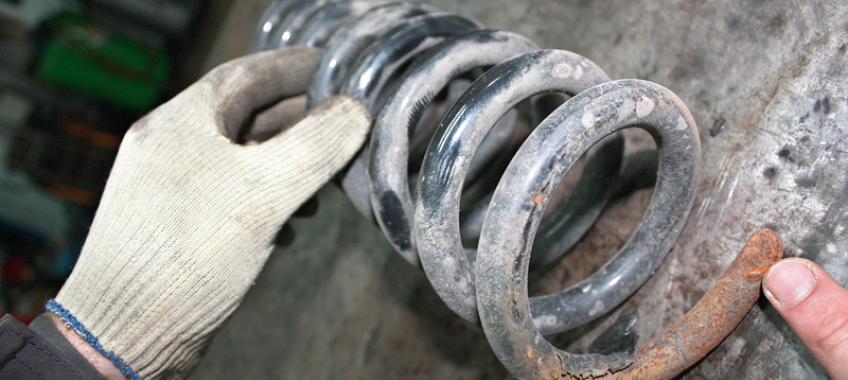
– typowe przypadki trapiące układ zawieszenia
Inżynierowie nieustannie pracują nad nowymi rozwiązaniami, a w dziedzinie elementów zawieszenia przyświecają im dziś głównie dwa cele: zwiększenie bezpieczeństwa oraz redukcja masy, zwłaszcza, gdy chodzi o tak zwaną masę nieresorowaną. Przewymiarowania komponentów zawieszenia unika się z dwóch powodów. Zysk kilku gramów wydawać się może niewielki, ale w produkcji masowej odchudzenie konstrukcji to ogromne oszczędności.
Do lamusa odchodzi żeliwo, a standardem staje się aluminium. Awansują już tworzywa, a nawet kompozyty, które coraz powszechniej bywają proponowane na tylnej osi w postaci nowej generacji resorów piórowych. Te i inne działania pozwalają na redukcję niebagatelnej masy własnej pojazdu.
Kilka lat temu Sogefi uruchomiło produkcję sprężyn z materiału kompozytowego GFP. Zwoje sprężyn kompozytowych ważą od 40% do 70% mniej od tradycyjnych, stalowych elementów zawieszenia i w związku z tym korzystnie wpłyną na obniżenie masy pojazdu. Innowacyjne połączenie materiałów – włókna szklanego i żywicy epoksydowej rewolucjonizuje branżę motoryzacyjną, jakkolwiek tego typu aplikacje zarezerwowane są póki co na pierwszy montaż. Najnowszym przykładem redukcji masy nieresorowanej są sprężyny do Audi A6 Avant. Takie rozwiązanie pozwala zaoszczędzić 4,4 kg masy całkowitej samochodu. W podobnym duchu anonsowano niedawno debiut szóstej generacji Fiata Ducato, którego tylne zawieszenie (resor piórowy) wykonano z materiałów kompozytowych, co pozwala wyraźnie, bo aż o 15 kg, zredukować masę własną pojazdu. Nie inaczej prezentują się osiągnięcia inżynierów ZF.
- Rozwój osi tylnej do samochodów osobowych z resorem piórowym wykonanym z tworzywa sztucznego wzmocnionego włóknem szklanym jest dowodem na kompetencje ZF, podobnie jak produkcja kompletnych systemów osi wykonanych z lekkich materiałów – dowodzi Thomas Wenzel z działu prasowego ZF. - Zmniejszenie wagi o 15% w porównaniu do konwencjonalnej osi o konstrukcji stalowej nie jest jedyną zaletą tej technologii. W przeciwieństwie do złożonej, wielowahaczowej konstrukcji, wykorzystuje ona jeden element resorujący – mianowicie pióro, które odpowiada zarówno za prowadzenie koła, jak i za tłumienie nierówności i kontakt z nawierzchnią. Poprzez zintegrowanie elementów w jeden zmniejsza się złożoność osi, co przekłada się na mniejsze koszty montażu i naprawy dla producentów samochodów, a także dodatkową oszczędność miejsca.
Podczas IAA 2014 prezentowano kolejne rozwiązanie seryjne, tym razem pomyślano o redukcji masy pojazdów ciężarowych. Czteropunktowy wahacz wzmacniany włóknem szklanym (GRP) pozwala odchudzić konstrukcję pojazdu o 11 kg i przy okazji zredukować koszty produkcji. Jeszcze większe oszczędności anonsowano w dziedzinie zawieszenia pojazdów ciężarowych. IS 80 TS – tak nazwano nowej konstrukcji zawieszenie, które pozwala na oszczędność rzędu 40 kg, co z powodzeniem rekompensuje wagę elementów stanowiących niezbędniki wyposażenia pojazdów spełniających normę Euro 6.
Póki co najpoważniejszą barierą w anonsowaniu rozwiązań opartych na nowatorskich materiałach (kompozyty) pozostają wysokie koszty produkcji. Nie bez znaczenia jest też pewnego rodzaju ułomność tego typu nowinek. Otóż w przeciwieństwie do tradycyjnych materiałów symptomy zmęczenia takich konstrukcji objawiać się będę… nagle. Inaczej, bo zwykle w dłuższym interwale czasu przebiega utrata pierwotnych właściwości w materiałach tradycyjnych (stal, żeliwo, aluminium). Łatwość diagnozy, a raczej przewidywania spodziewanej konieczności wymiany zużytego komponentu „na nowy”, pozostaje niedocenionym walorem stosowanych dziś powszechnie materiałów.
Objawy niedomagania
Jednym z pierwszych objawów niesprawności układu zawieszenia jest niepokojące zachowanie samochodu, któremu towarzyszą zwykle metaliczne odgłosy (gdy uszkodzeniu uległa sprężyna lub miejsce jej mocowania). Wahacze to jeden z komponentów zawieszenia auta, który łączy piastę koła (zwrotnicę) z nadwoziem. Tłumienie drgań układu zawieszenia i utrzymywanie poszczególnych części ruchomych w stałej odległości od siebie zależy od silentblocków (elementów gumowo-metalowych). Niewielka część o dużym zastosowaniu wycisza pracę zawieszenia. Jazda na wyeksploatowanych tulejach może skutkować silnymi luzami i spadkiem trakcji pojazdu. Tuleje zużywają się jako pierwsza część zawieszenia. W niskiej temperaturze guma wszak staje się mniej elastyczna, przez co łatwiej powstają na niej mikropęknięcia, a sama mieszanka szybciej się starzeje. Nic więc dziwnego, że elementy zawieszenia najbardziej degradują się zimą. Woda, sól i piasek tworzą mieszankę, która jest wyjątkowo agresywnym ścierniwem. Gdy nie w porę zauważyć na pozór błahe objawy, te uruchamiają szereg destrukcyjnych i dużo kosztowniejszych procesów niszczących.
Kontrolę sworzni przeprowadzamy na stanowisku warsztatowym – oś przeznaczona do kontroli nie może być uniesiona. Warto wtedy oczyścić sworzeń. Nie należy jednak stosować agresywnych środków czyszczących, a szczególnie rozpuszczalników (do czyszczenia należy użyć specjalnych środków czyszczących neutralnych dla farb, lakierów, osłon gumowych czy czujników ABS). Stan techniczny amortyzatorów ma niebagatelne znaczenie dla bezpieczeństwa. Nowoczesna technika sprawia, że ABS przestaje działać, gdy te są wyrobione. Generalnie też im pojazd bardziej naszpikowany systemami poprawiającymi bezpieczeństwo, tym bardziej producent nie przewiduje żadnej tolerancji dla niesprawności mechanicznej elementów zawieszenia.
Organoleptyczna kontrola elementów odpowiedzialnych za tłumienie sprowadza się w zasadzie do dwóch czynności poprzedzających właściwe badanie. Po pierwsze należy dotknąć amortyzator suchymi palcami. Jeżeli palce są nadal suche, to amortyzator jest szczelny. W razie wątpliwości należy czynność powtórzyć, wycierając uprzednio do sucha część roboczą amortyzatora i ponawiając kontrolę po kilku dniach. Warstewka oleju na amortyzatorze jest zjawiskiem całkiem normalnym. Przy każdym skoku tłoczysko zabiera z komory roboczej mikroskopijną ilość oleju, która służy też smarowaniu uszczelki, więc na suchym i sprawnym amortyzatorze zawsze będzie widoczna cienka warstwa oleju. Gdy ślady oleju są znaczne – co powinno skutkować utratą oleju i spadkiem siły tłumienia, elementy należny poddać wnikliwej diagnozie.
Trudne przypadki – mocowania śrubowe
Klucze – bez tych narzędzi właściwa obsługa połączeń śrubowych, które mocują elementy składowe układu zawieszenia, byłaby w zasadzie niemożliwa. Odkręcenie zapieczonej lub za mocno dokręconej nakrętki bywa prawdziwą udręką. Co zrobić, aby nie dopuścić do uszkodzenia gwintu lub zerwania łba śruby? Sposobów radzenia sobie z zapieczonymi połączeniami śrubowymi jest kilka. Na pewno warto na początek użyć środka penetrującego, by w kilka minut potem kilka razy z wyczuciem obstukać śrubę. Na podobnej zasadzie działa klucz udarowy, który zakładamy na łeb śruby lub nakrętkę i uderzamy młotkiem w ramię. W chwili uderzenia powstanie odpowiednio duży moment obrotowy, który powinien pomóc w poluzowaniu śruby. To narzędzie zostało tak skonstruowane, a jego składniki stopowe tak dobrane, aby móc przyjmować siłę uderzenia.
- Optymalna jest tu stal chromowo-molibdenowa (CrMo) – tłumaczy Emil Sieligowski, Brand Manager marki dedykowanych profesjonalistom narzędzi PROLINE. - Ponieważ jest twardsza i bardziej wytrzymała, stosuje się ją do produkcji narzędzi najwyższej jakości, często używanych do zadań specjalnych, np. nasadek udarowych czy specjalnych udarowych kluczy oczkowych, które mają wzmocnione główki przeznaczone do pobijania.
Zawsze, gdy mamy problem z odkręceniem śruby, warto wypróbować inny klucz lub nasadkę. Przy okazji zwróćmy uwagę, jak bardzo ważna okazuje się technologia wykonania klucza nasadowego, a szczególnie odpowiedni profil wewnętrzny nasadki. Otóż klucze renomowanych producentów mają specjalne profile, które nie tylko zapobiegają niszczeniu się łba śruby, ale przede wszystkim pozwalają na pracę z już spracowanymi łbami – nawet w 50%! Taki walor wynika z odpowiedniego rozkładu sił, które zamiast na krawędzie wywierają nacisk na środek ścian łba śruby.
Kluczami lepiej chroniącymi łeb śruby przed ścieraniem są klucze oczkowe. Pozwalają również na znacznie bezpieczniejszą pracę, zwłaszcza w miejscach trudno dostępnych, gdyż zmniejszają prawdopodobieństwo uślizgu klucza podczas wykonywania obrotu. Doskonale znane mechanikom i często przez nich używane są też klucze oczkowe półotwarte. W warsztacie przydadzą się również klucze oczkowe odsadzone. Mówiąc o kluczach w warsztacie mechanika, nie sposób nie wspomnieć o tzw. kluczach fajkowych dwustronnych. Doskonale sprawdzają się we wszelkich miejscach, gdzie śruby i nakrętki osadzone są na tyle głęboko w otworach, że nie da się wykorzystać klasycznych kluczy nasadowych. Pozwalają na zastosowanie dużej siły, można też zakładać na nie różnego rodzaju przedłużki, dzięki czemu możliwe jest wydłużenie ramienia zastosowanej do odkręcania lub dokręcania dźwigni.
Niewielkich rozmiarów podgrzewacz indukcyjny – tego typu wyposażenie świadczy o profesjonalnym podejściu warsztatu do usług serwisowych i na pewno przydaje się przy remontach zawieszeń czy ustawianiu geometrii kół. Punktowe nagrzanie zapobiega uszkodzeniom, jakie powstają przy użyciu otwartego płomienia. Nie trzeba nikogo przekonywać, że poluzowywanie zapieczonych elementów przy użyciu palnika gazowego jest ryzykowne i to nie tylko ze względu na możliwość pożaru czy poparzenia, ale również ze względu na możliwość uszkodzenia nagrzewanego materiału. Inaczej jest przy użyciu nagrzewnicy indukcyjnej, która pozwala na miejscowe, dokładne i bezpieczne rozgrzanie metalu – wystarczy nasadzić odpowiedni rozmiar końcówki, by dużo precyzyjniej i szybciej poradzić sobie z zapieczonymi śrubami, nakrętkami, sworzniami itp.
Rafał Dobrowolski
Fot. R. Dobrowolski i materiały firm:
ZF, Sogefi, AGENTOOLS
Komentarze (0)