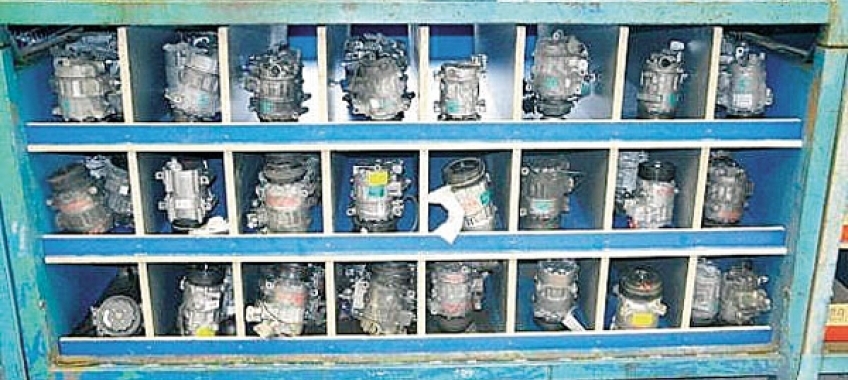
W dzisiejszych czasach trudno sobie wyobrazić jazdę autem bez sprawnej klimatyzacji. Sercem tego skomplikowanego wbrew pozorom układu jest kompresor (sprężarka klimatyzacji), który tłoczy czynnik chłodniczy w postaci gazowej w układzie i dzięki procesom termodynamicznym, jakie zachodzą w skraplaczu oraz parowniku, „odbiera” ciepło z wnętrza pojazdu.
Chemiczny czynnik chłodniczy paruje bądź skrapla się w ciśnieniu otoczenia w bardzo niskich temperaturach (1 bar ciśnienia powietrza = -26,5°C) i może przy tym odebrać bądź oddać bardzo dużo energii cieplnej. Poprzez zmiany ciśnienia w obiegu zmienia się temperatura wrzenia czynnika chłodniczego.
Sprężarka ze względu na warunki pracy podlega stałym przeciążeniom i narażona jest na liczne usterki powodowane jej przeciążeniem w wyniku możliwych usterek pozostałych elementów całego układu klimatyzacji – takich jak między innymi niesprawny zawór rozprężny (lub dysza dławiąca), osuszacz, niesprawne wentylatory, niesprawny skraplacz czy parownik. Dlatego podczas eksploatacji często dochodzi do awarii sprężarek. Ponieważ współczesne kompresory klimatyzacji stosowane w pojazdach są dość skomplikowane, ich naprawą powinni zajmować się specjaliści posiadający zarówno odpowiednią wiedzę, jak i należyte zaplecze techniczne oraz wyposażenie.
Regeneracja kompresora klimatyzacji zaczyna się od demontażu koła pasowego oraz zabezpieczenia przyłączy. Następnie rdzeń przechodzi etap śrutowania w urządzeniu, które z dużą siłą uderza o detal kulkami chromowo-niklowymi w celu wygładzenia oraz zmatowienia powierzchni. Po etapie śrutowania rdzeń swoim wyglądem zbliżony jest do produktu nowego.
W kolejnym etapie kompresor zostaje rozłożony na poszczególne podzespoły i trafia do kosza składowego. Na tym etapie ważne jest odpowiednie rozłożenie w przegrodach par pasownych, tj. tłoczków wraz z pestkami.
Kolejno podzespoły są myte w urządzeniach ultradźwiękowych oraz polerowane. Następnie elementy eksploatacyjne, znajdujące się wewnątrz sprężarki, przechodzą etap weryfikacji. Wymiana m.in. uszczelniaczy, uszczelek, płyt zaworowych i tych zweryfikowanych jako uszkodzone: tłoki, cylindry, łożyska, zawory ciśnienia i elementy sprzęgła. Następnie odbywa się precyzyjny i etapowy montaż na nowych podzespołach z wykorzystaniem skomplikowanych i certyfikowanych przyrządów technologicznych i pomiarowych. Końcowym etapem jest sprawdzenie poprawności działania zmontowanego podzespołu i jego wszystkich parametrów istotnych dla dalszego poprawnego funkcjonowania w układzie.
Montaż odbywa się w specjalnie zaprojektowanym pomieszczeniu z 5-krotną wymianą powietrza na godzinę. Przed samym procesem montażu produkt jest ostatecznie myty w myjce w celu wyeliminowania kurzu oraz innych zanieczyszczeń. Testy kontrolne odbywają się na specjalistycznym, zautomatyzowanym urządzeniu Hartridge HA7-AC, wykonującym zadane, ściśle określone procedury.
Elementy standardowo wymieniane w kompresorze:
- zestaw uszczelnień,
- o-ringi,
- simmering,
- separator oleju,
- zatyczki wejściowe,
- gumy koła pasowego.
Połączenie wiedzy, nowoczesnej technologii oraz oryginalnych części zamiennych daje w efekcie finalnym produkt o parametrach fabrycznych i takiej samej trwałości oraz jakości. Nabywcy pozostaje cieszyć się ponownym komfortem użytkowania, a korzystna cena i wysoka jakość regenerowanych sprężarek zaspokoi oczekiwania nawet najbardziej wymagających klientów.
Dodatkowym atutem zakupu kompresorów regenerowanych jest możliwość zwrotu wymontowanego „starego”, niesprawnego podzespołu i finalnie obniżenia ceny zakupionej sprężarki.
Główne przyczyny uszkodzeń kompresorów
1. Nieprawidłowa naprawa. Poprzednia naprawa została wykonana nieprawidłowo, powodując jeden z poniższych problemów.
- System został nieprawidłowo oczyszczony. Zanieczyszczenia zostały przetransportowane do kompresora, powodując uszkodzenia cylindrów, tłoków oraz łożysk.
- Za dużo oleju. Przy wymianie kompresora do systemu zostało dodane zbyt dużo oleju, co skutkuje blokadą cieczy. Bieżnia prowadząca zostaje zniszczona.
- Komponenty systemu nie zostały dokładnie wysuszone po płukaniu układu. Pozostały środek do płukania powoduje rozrzedzenie oleju i złe smarowanie.
- Nabijanie układu przez port niskiego ciśnienia. Czynnik w postaci ciekłej dostaje się do kompresora i po uruchomieniu systemu następuje blokada cieczy pod tłokami kompresora.
- Nieprawidłowa procedura nowo zamontowanego kompresora. Podniesienie obrotów silnika podczas pierwszych 2 minut nowo zamontowanego kompresora. Czas potrzebny do wymieszania oleju z czynnikiem i jego powrotu do kompresora to około 2 minuty. Dla bezpieczeństwa należy pozostawić silnik na wolnych obrotach przez około 5 minut.
2. Za dużo lub niezgodny z SAE barwnik UV. Za duża ilość barwnika powoduje nieprawidłowe smarowanie kompresora i niską wydajność chłodniczą. Barwnik poza specyfikacją SAE może powodować złe smarowanie oraz rdzewienie części kompresora. W obu przypadkach prowadzi to do uszkodzenia kompresora.
3. Niewystarczająca ilość czynnika. Czynnik transportuje olej. Mało czynnika to mała ilość oleju w nim transportowana.
4. Nieprawidłowe smarowanie – za mało czynnika chłodniczego/oleju (czarny osad po stronie ssania).
5. Za mały napływ oleju – nadmiar oleju sprężarkowego:
- czarny osad i cząsteczki metalu po stronie tłoczenia,
- czarny osad po stronie ssania.
Przyczyna – klimatyzacja nie została poprawnie oczyszczona!
6. Niewystarczające smarowanie (za dużo barwnika UV – zmniejszenie lepkości i wydajności smarowania).
7. Blokada oleju – za dużo oleju w układzie:
- strona ssania i tłoczenia czysta, ale mokra od oleju,
- wszystkie cylindry wypełnione olejem.
Powody zerwania sprzęgła kompresora (fot. 1)
1. Wewnętrzne opory obrotu kompresora.
2. Nagła zmiana obrotów silnika.
3. Sprzęgło jednokierunkowe alternatora zablokowane.
4. Sprzęgło dwumasowe niesprawne.
5. Niesprawny automatyczny napinacz.
Wyraźnie oddzielone dwa różne typy olejów – jeden wciąż przeźroczysty, drugi nie (fot. 2)
- Opis problemu – brak zmiany wydajności. Blokada układu lub zatarcie sprężarki.
- Przyczyna awarii – olej PAO podany do obiegu chłodniczego. Nie można mieszać olejów PAO i PAG, ponieważ tworzą substancję parafinopodobną.
- Wynik – zatkanie zaworu regulacyjnego i/lub obiegu chłodniczego.
Wyraźnie oddzielone dwa różne typy olejów – w postaci kropel pływa w drugim (fot. 3)
- Opis problemu – nadmierny hałas
lub/i zatarcie sprężarki.
- Do obiegu chłodniczego dodano olej POE. Olej PAG i POE nie mieszają się ze sobą.
- Wynik – zbyt duża ilość oleju POE zmniejszy wydajność smarowania.
Port ssawny jest czysty i suchy (fot. 4)
- Opis problemu – zatarcie sprężarki.
- Przyczyna awarii – niewystarczające smarowanie spowodowane przez: a) zatkanie układu; b) brak procedury dotarcia.
- Wynik: a) brak powrotu oleju i smarowania wewnętrznych części sprężarki; b) zbyt wysokie obroty silnika podczas pierwszego uruchomienia sprężarki; za mało czasu na wymieszanie oleju z czynnikiem chłodniczym zasysanym do sprężarki.
Stwardniała lub żelopodobna substancja w porcie ssawnym (fot. 5)
- Opis problemu – brak zmiany wydajności, blokada układu lub zatarcie sprężarki.
- Przyczyna awarii – uszczelniacz lub dodatek uszlachetniający dodane do obiegu chłodniczego.
- Wynik – reakcja chemiczna uszczelniacza lub dodatku uszlachetniającego spowodowała zatkanie zaworu regulacyjnego sprężarki i/lub zaworu rozprężnego.
Cząstki kauczuku w portach ssawnym i tłocznym (fot. 6)
- Opis problemu – brak zmiany wydajności lub zatarcie sprężarki.
- Przyczyna awarii – pogorszenie stanu gumowego przewodu elastycznego z powodu starzenia się lub reakcji z dodatkami, preparatami konserwującymi lub czyszczącymi.
- Wynik – cząstki kauczuku znajdują się w obiegu chłodniczym, blokując i powodując awarię sprężarki.
Uszczelki są napuchnięte i nie pasują do pierwotnej pozycji (fot. 7)
- Opis problemu – brak zmiany wydajności, wycieki czynnika z układu.
- Przyczyna awarii: a) układ napełniony nieodpowiednim czynnikiem chłodniczym; b) dodatki lub nieodpowiednie preparaty czyszczące.
- Wynik – czynnik chłodniczy, olej, dodatek lub preparat czyszczący reagują z uszczelnieniem, powodując jego puchnięcie.
Port ssawny jest zabrudzony i czarny (fot. 8)
- Opis problemu – brak zmiany wydajności, zatarcie sprężarki.
- Przyczyna awarii – niewystarczające czyszczenie obiegu chłodniczego lub brak wymiany rekomendowanych części.
- Wynik – cząsteczki brudu znajdują się w układzie i wracają do sprężarki, powodując złe smarowanie lub zatkanie zaworu regulacyjnego.
Port tłoczny jest czarny i ma zmieniony kolor (fot. 9)
- Opis problemu – brak zmiany wydajności, zatarcie sprężarki.
- Przyczyna awarii – zbyt mała ilość czynnika chłodniczego lub częściowo zablokowany obieg chłodniczy.
- Wynik – niewystarczający obieg oleju powodujący złe smarowanie i przegrzanie sprężarki.
Popękane koło pasowe (fot. 10)
- Opis problemu – pas napędowy powoduje hałas lub spadł.
- Przyczyna awarii : a) niewłaściwe usunięcie lub instalacja pasa napędowego; b) uderzenie koła pasowego przed lub po instalacji.
- Wynik – nadmierna siła spowodowała popękanie koła pasowego.
Komentarze (0)