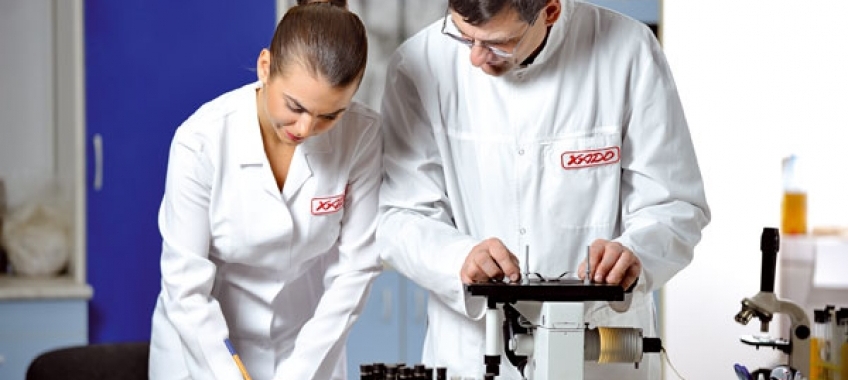
Jakościowe i efektywnie działające produkty zawierające rewitalizant znaleźć można na półkach sklepowych wielu krajów świata. Za ich pomocą można przywrócić i utrzymać kompresję, moc i ekonomikę silnika na wyższym poziomie, usunąć głośność pracujących zespołów napędowych i wspomagania kierownicy, efektywnie dotrzeć detale nowego auta i zabezpieczyć maksymalny resurs. Jak rzeczywiście działa rewitalizant?
Rewitalizacja – przywrócenie do życia, odmłodzenie, odnowienie, leczenie powierzchni metalowych z usunięciem występujących defektów. Nie jest to zwykły slogan, a realna praca.
Zróbmy eksperyment
Uzyskanie dobrego efektu to dla niektórych za mało. Jak i dzięki czemu osiąga się idealny efekt oraz jakie dokładnie procesy zachodzą na powierzchniach detali? Aby zobaczyć, jak usuwane są groźne defekty i na czym polega rewitalizacja, zwróciliśmy się do specjalistów laboratorium tribologicznego kompanii XADO. Celem sprawdzenia przedstawionego efektu użyto prawdziwego elementu, dokonano pomiarów i naniesiono uszkodzenie, które posmarowano „leczącym” smarem. Co z tego wynikło?
Przebieg eksperymentu
1. Na ścieżkę toczenia wybranego łożyska naniesiono rysę za pomocą rylca grawerskiego (fot. 1).
2. Wprowadzono smar „XADO Remontowy”, przeznaczony do węzłów o dużym zużyciu (do 80%). Jest to zwykły produkt seryjny, który można bezproblemowo zakupić w sieci handlowej.
3. Zaczęto leczyć łożysko ze smarem pod poważnym obciążeniem (nacisk rzędu 8000 N i 1000 obrotów na minutę) na specjalnym urządzeniu. Podczas pracy zachodzi rzeczywista rewitalizacja, a więc likwidacja uszkodzenia drogą budowy metalowo-ceramicznej warstwy osłonowej na powierzchni tarcia.
Zabudowa uszkodzenia
Proces zachodzi bardzo szybko i dlatego zatrzymujemy urządzenie po 15 minutach pracy, dopóki są widoczne zarysy uszkodzenia. Popatrzmy, co wydarzyło się z powierzchnią? Już gołym okiem widać, że defekt znacznie się pomniejszył, zaciągając się z obrzeży.
Fotografia z mikroskopu (fot. 2) pozwala dojrzeć szczegóły – drobne ślady po fabrycznym szlifowaniu zniknęły, na krawędziach wgłębienia powstały napływy przypominające nawisy śnieżne na obrzeżu wąwozu. Przyrost warstwy metalowo-ceramicznej zachodzi na krawędziach wgłębienia, stopniowo zapełniając defekt od krawędzi do środka. Schemat tego pokazano na rysunkach.
Złożona fizyka prostymi słowami
Widzieliśmy, jak rewitalizant zaczyna działać najpierw w przeciążonej strefie (strefie największego zużycia) i przyrost powierzchni podczas rewitalizacji zawsze zachodzi w strefie uszkodzenia. Dlaczego? Popatrzmy, jak powstaje defekt na rzeczywistych elementach silnika. Wystarczy zadrapanie, odprysk spowodowany twardym, obcym ciałem (pył, drobne opiłki, wiórki). Miejsca te są strefą anomalnej aktywności powierzchniowej. Atomy metali mają tu nieskompensowane wiązania i przy wzroście obciążenia łatwo je rozluźnić, oderwać od rdzenia. Defekt rośnie, powiększa się i zachodzi zużycie detali. Na marginesie, następstwa takiego zużycia silnika są przewidywalne i bardzo nieprzyjemne: spadek mocy, obniżenie i rozrzut kompresji, wzrost zużycia oleju oraz paliwa, wzrost zawartości szkodliwych związków w spalinach. Obniżenie kompresji o 20-25% (przykładowo z 14 do 10 jednostek) świadczy o 100-procentowym zużyciu silnika w odniesieniu do założeń technicznych producenta. Złym znakiem jest również rozrzut kompresji w cylindrach więcej niż 1,5 jednostki, zużycie oleju przekraczające 0,4-0,6% w relacji do paliwa (tj. 0,8 litra na 1000 km, przy zużyciu paliwa na poziomie 10 litrów na 100 km).
Aby zrozumieć zakres tego procesu, wystarczy powiedzieć, że w czterech litrach zużytego oleju znajduje się ok. 2 g metali. A przecież remont kapitalny silnika to zaledwie 60 g metalu dla silnika o pojemności 1800 cm3. Cóż to jest 60 g dla 100-kilogramowego silnika – kropla w morzu. Problem w tym, że ściera się szczególnie w kluczowych miejscach par tarcia (pierścień – cylinder, czop wału – panewka itd.), odpowiadających za prawidłową pracę silnika. Czy można walczyć z zużyciem i usunąć oraz zabudować defekt?
Można, a przedstawiony eksperyment jest tego świadectwem. Rewitalizant zaczyna działać głównie w strefie największego zużycia, dlatego że właśnie tu występuje nadwyżka energii inicjującej proces, a atomy metalu mają największą ilość swobodnych, nieskompensowanych wiązań. Wiązania te, jak magnesy, wychwytują i zatrzymują wprost w miejscach zużycia materiał budujący – rewitalizant. Kilka minut po inicjacji rewitalizacji w miejscu zadrapania pojawia się metalowo-ceramiczna łatka (fot. 2 i 3b). Strefa anomalnej aktywności zanika. Procesy energetyczne stabilizują się, przyrost metalowo-ceramicznego pokrycia gaśnie (fot. 3c). Defekt usunięty!
Wnioski podstawowe
Rewitalizant działa wszędzie tam, gdzie jest tarcie i obciążenie. Pozwala on usunąć luz w łożysku i podnieść klasę dokładności, zmniejszyć elipsoidalność cylindra, optymalizować ślady współpracy w zazębieniu kół zębatych i inne. Rewitalizant dobrze radzi sobie z poważnym brakiem fabrycznym, jaki dzisiaj nie jest rzadkością. Żelazo rzeczywiście można leczyć!
Co mówi ekspertyza techniczna?
Zwróciliśmy się do autorytatywnych ekspertów, aby raz na zawsze postawić kropkę nad i – organ certyfikacyjny Europy, TÜV (Związek Nadzoru Technicznego Niemiec), potwierdził, że po zastosowaniu rewitalizanta osiągnięto:
- wzrost kompresji w cylindrach od 11 do 14 Atm,
- wzrost mocy silnika o 2,7% (2,3 kW),
- spadek zużycia paliwa o 5,3%,
- obniżenie toksyczności spalin do 15%.
Obiekt demonstracji
Łożysko seryjne produkcji GPZ oznaczone 8202 (FŁT 51202), wykorzystywane w pompach wtryskowych silników wysokoprężnych.
Jako obiekt demonstracyjny wybrano zwykłe łożysko. Łatwo rozbieralne i składane, wytrzymuje duże obciążenia. Materiał łożyska – stal stopowa specjalna ŁH 15. Stal tę stosuje się do produkcji silnie obciążonych i ważnych części samochodowych, takich jak rolki popychaczy, elementy tłoczące pomp wtryskowych, przeguby równobieżne, łożyska wzdłużne wałów skrzyń biegów.
Komentarze (0)