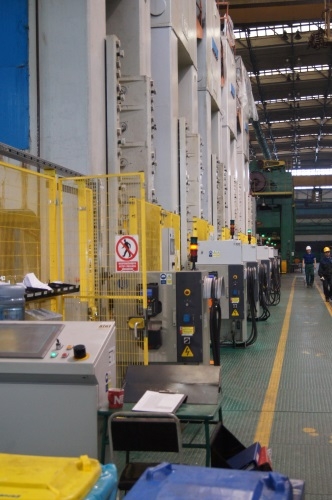
Stal jest wszędzie – porusza się po drogach, wkracza do naszych domów i wkomponowuje się w środowisko w postaci przedmiotów codziennego użytku. Dopiero kiedy o tym pomyślimy, uświadamiamy sobie, jak bardzo ważny dla ludzkości jest ten metal, a przemysł związany z jego produkcją – dla gospodarki światowej.
Jedną z najważniejszych grup przemysłowych w Europie produkujących wyroby ze stali jest CLN. Liczby mówią same za siebie: 1 rodzina, 3 pokolenia, ponad 60 lat ciągłego wzrostu, obecność na 4 kontynentach, w 18 krajach, 40 firm i zakładów produkcyjnych, zatrudniających ponad 9000 osób. Skonsolidowany obrót Grupy to 1,9 miliarda euro.
Struktura CLN podzielona jest na 3 sektory: CLN (półprodukty ze stali), MA (części karoseryjne, wytłoczki, części dla przemysłu ciężkiego) i MW (felgi stalowe). Skupmy się na tych ostatnich.
Felgi stalowe dla wszystkich
MW (dawniej Magneto Wheels) produkuje felgi stalowe do wszystkich pojazdów, dostarczając produkty (koła szprychowe) również do motocykli. Dysponuje firmami i fabrykami na całym niemal świecie, również w Polsce. Działająca od 2007 r. spółka-córka MW Poland Sp. z o.o. należy do coraz szerszej sieci dystrybucji felg na rynki wtórne. Powstała w oparciu o współpracę z Inbud-Faro, byłym wyłącznym przedstawicielem Gianetti Ruote w Polsce. W październiku 2006 podpisany został kontrakt, którego stronami były: Inbud-Faro S.A., Magnetto Wheels S.p.A. oraz MW Poland Sp. z o.o. Na mocy tej umowy MW Poland Sp. z o.o. w styczniu 2007 przejęła obowiązki dystrybutora felg stalowych od Inbu-Faro S.A. Podobne firmy, wyspecjalizowane w handlu na rynkach wtórnych, powstały w ramach grupy MW wcześniej w kilku krajach Europy.
Technologia produkcji MW
Technologia produkcji felg stalowych MW to zaawansowany proces, w którym szczególną uwagę przykłada się do jakości. Wszelkie wymagania dotyczące sztywności, wagi i zmęczenia materiału poparte są odpowiednimi analizami i obliczeniami. Mowa o tak zaawansowanych technologiach analitycznych, jak:
- obliczenia linearne/nielinearne,
- symulacja procesu produkcji: bicie, formowanie, scalanie,
- symulacja zachowań felgi: interakcja z tarczami, piastą, śrubami.
MW dysponuje też laboratoriami wyposażonymi w najlepszy sprzęt, taki jak:
- urządzenia do testów zmęczenia materiału (obrót z oponami i bez opon),
- urządzenie do testów otworów montażowych,
- urządzenie do testów odporności na wstrząsy,
- urządzenie do mierzenia sztywności,
- urządzenia do testów odporności na korozję i warunki klimatyczne.
MW korzysta również z zaawansowanego oprogramowania:
- systemu telemetrii do statycznej i dynamicznej analizy zewnętrznej,
- programów do modelowania i strukturalnej optymalizacji, takich jak: UG, CATIA, IDEAS, Think3,
- programów do analizy komponentów przy obciążeniu i zmęczeniu materiału: MARC, Optris, Pam-Stamp, Permas, Straus,
- programów do nielinearnej symulacji (kształtowanie metalu, analiza styczności itp.): MARC, Straus.
Sam proces produkcji felg stalowych można podzielić na cztery etapy:
- produkcja tarczy koła,
- produkcja obręczy,
- montaż koła,
- lakierowanie.
Wytwarzanie tarczy rozpoczyna się od prostowania materiału. Stal – dla każdej aplikacji stosuje się inne jej parametry (wytrzymałość, gęstość, twardość, grubość itd.) – do zakładu dociera w wielkich zwojach o wysokości dorosłego człowieka. Dlatego taką taśmę należy najpierw rozprostować, aby nadawała się do pocięcia na kawałki o pożądanej długości i wykrojenie z nich tzw. rozkroju, który jest w odpowiedni sposób tłoczony i wyginany. W uzyskanej w ten sposób tarczy, kształtem przypominającej czaszę, wstępnie wycinane są otwory mocujące, otwór centralny oraz otwory wentylujące. Otwór centralny jest na brzegach wywijany, a otwory mocujące „stożkowane”. Fazowane są z kolei otwory wietrzące.
Oczywiście tarcza musi być skalibrowana. Najwyższa precyzja wykonania tego elementu w największym stopniu decyduje o jakości produktu. Błędy rzędu dziesiątych części milimetra w wykonaniu otworów mających styczność z piastą mogą powodować znaczne wibracje w pojeździe lub zadecydować o całkowitej bezużyteczności koła.
Prostowaniem materiału rozpoczyna się również tworzenie obręczy. Mimo że później obręcz znowu jest zwijana, należy wcześniej stalową taśmę pociąć na odpowiedniej długości kawałki i oznakować. Następnie obręcz jest zgrzewana, okrawana, walcowana i roztłaczana. Profilowanie odbywa się aż w czterech etapach, jest to bowiem proces skomplikowany. Ostatni z tych etapów to kalibrowanie, polegające na rozciąganiu obręczy we wszystkich kierunkach tak, aby uzyskała ona swoje ostateczne parametry. Nowoczesne obręcze muszą doskonale współpracować z bezdętkowymi oponami o coraz bardziej zaawansowanych konstrukcjach. Z tego też powodu niezbędna jest dokładna kontrola wykonania obręczy, przeprowadza się też – już na tym etapie – kontrolę szczelności.
Po stworzeniu elementów składowych koła należy jeszcze złożyć w całość. Montaż felgi rozpoczyna się pozycjonowaniem tarczy, ponieważ jej usytuowanie względem otworu pod zawór do pompowania opony ma znaczenie dla wyważenia koła. Potem wykonuje się takie czynności, jak: wciskanie tarczy w obręcz, spawanie, czyszczenie spawów oraz znakowanie i sprawdzenie wyważenia kompletnego koła. Każde gotowe koło sprawdzane jest komputerowo pod kątem jakości, aby jeszcze przed malowaniem odrzucić ewentualne wadliwe sztuki.
Komentarze (0)